In fighting the spread of COVID-19, many organizations are opening themselves to new collaborative efforts and shifting their production capabilities. Many are looking toward additive manufacturing (AM) technologies to rapidly prototype and manufacture critical medical and protective supplies. Design that Matters recently launched the world’s first NIH-recommended 3D-printed face shields, and Siemens has opened its Additive Manufacturing Network for the medial sector to more quickly access necessary supplies.
In this same vein, Royal DSM N.V. (Heerlen, the Netherlands; www.dsm.com) has launched a collaborative platform focused on additive manufacturing, sharing know-how and relevant resources for 3D printing supplies essential for fighting the pandemic, including: Hands-free door openers; Plastic face shields; face masks; Venturi valves for Venturi Oxygen Mask; Safety goggles; Touch pods for fingers; and more. DSM’s additive manufacturing hub will be updated daily and aims to alleviate supply-chain concerns for critical materials during the pandemic while also facilitating collaborative 3D-printing design.
DSM has also converted a manufacturing facility to produce disinfectant at scale, which is being donated to nearby hospitals, joining Dow and numerous other chemical companies in their production of hand sanitizers and disinfectants. Following its announcement to quickly construct hand-sanitizer plants in Germany and the U.K., INEOS will build a similar factory in France to produce 1 million bottles per month of sanitizer.
Also sharing crucial expertise during the pandemic is Praj Industries Ltd. (Pune, India; www.praj.net), which has enabled open access to its process technology for producing hand sanitizer, with the hopes that sharing crucial know-how in this area will enable more manufacturers to produce larger volumes of critical hand-sanitizing and disinfectant products. Praj’s process design package for hand sanitizer production is available via email.
Other companies are rapidly adjusting their production slates to expand the supply of materials for personal protective equipment. Eastman Chemical Co. (Kingsport, Tenn.; www.eastman.com) worked with the Tennessee Higher Education Commission (THEC) and Austin Peay State University to donate enough rolls of Polyethylene Terepthalate Glycol (PETG) film, a copolyester commonly used for rigid medical packaging and medical devices, to produce 10,000 face shields. Eastman teams worked over the weekend to ensure that in four days, THEC had the materials needed to continue with the project.
Face shields have become an essential tool for protecting personnel in medical fields and others on the front lines of battling the epidemic. The shields protect people from droplets produced by coughing and sneezing and can help prevent workers from touching their faces.
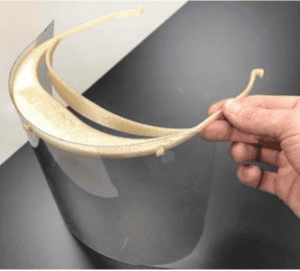
Prototype face shield made from transparent film and AM filament (Source: Solvay)
Additionally, Solvay S.A. (Brussels, Belgium; www.solvay.com) is supplying high-performance, medical-grade transparent film to Boeing for its production of face shields. Manufactured by Solvay’s Ajedium Films business, the thermoplastic film will be used by Boeing in the production of thousands of face shields. The film will be manufactured using Solvay’s medical-grade Radel PPSU or Udel PSU, two transparent specialty polymers widely used for medical devices because of their ability to be sterilized and withstand aggressive disinfectants. In addition to materials for face shields, Solvay is also offering support for the expanded production of other essential medical-grade materials, including ventilator components, nonwoven materials for surgical and N95 masks, 3D printing filaments and lubricants for oxygen-supply system components.