Water-treatment programs for cooling towers have evolved in recent years, favoring non-phosphorus programs today. This article reviews the impact on water chemistry and operating reliability
Cooling towers are a critical component of many industrial facilities. Cooling towers evaporate only pure water, forcing the minerals in the water to progressively concentrate, or “cycle up.” The enriched mineral content makes the water more corrosive and can lead to the deposition of sparingly soluble salts, such as calcium carbonate, on critical heat -transfer surfaces. The resulting design and operating challenges have become particularly acute following the gradual phase-out of chromate-based treatment programs (beginning in the 1970s) due to human health concerns. However, the most widely used replacement programs, whose core chemistry is based on the use of inorganic and organic phosphates, has proven to be less effective and much more difficult to control than the earlier chromate-based corrosion inhibitor programs.
Today, with phosphorus discharge to receiving bodies of water being restricted (or even banned in some places), ongoing effort is underway to find suitable alternatives, with movement toward treatment programs that do not contain phosphate or zinc. Like any major change, acceptance comes slowly until plant personnel understand the performance benefits of the new technology. This article examines the ongoing evolution in water treatment for cooling towers.
The ‘good old days’
Cooling systems typically have mixed metallurgy, with carbon steel being the common economic material choice for system piping, heat- exchanger shells and even tubes. Where greater corrosion resistance is required for heat-exchanger tubes, stainless steels are often the choice material used today. This includes the venerable Types 304 and 316, as well as the newer Duplex grades, UNS 2205 and UNS 2507.
Copper tubes are widely used for chillers, with both the inner diameter and outer diameter textured to improve heat transfer. Admiralty brass and copper-nickel alloys are still used for heat-exchanger tubing, due to their chloride resistance, although titanium and super-ferritic stainless steel are becoming more popular for applications that require high reliability in cooling waters that have a high chloride content.
Chromate was such a powerful corrosion inhibitor that it enabled cooling systems to be operated at a lower, more corrosive pH, typically in conjunction with sulfuric acid for pH control. This chemistry is quite straightforward. In most natural waters, and especially when progressive cycling causes water constituents to become concentrated inside a cooling tower, the primary water chemistry issue (apart from microbiological fouling) is calcium carbonate (CaCO 3) scale deposition, as shown in Equation (1):
The equation illustrates the inverse solubility of CaCO 3 as a function of temperature. As cooling water temperature rises inside heat exchangers, the exchanger tubes or plates become susceptible to CaCO 3 deposition. The historic acid-chromate program inhibited scaling by reacting sulfuric acid with bicarbonate ions (HCO 3 –) to convert the ions to CO 2, which then escape as gas. A typical pH control range was at or near 6.5.
The second compound in the formulation, sodium dichromate dihydrate (Na 2 Cr 2 O 7 •2H 2 O), provides hexavalent chromium ions that react with carbon steel to establish a protective pseudo-stainless-steel layer.
Acid-chromate programs performed extremely well in most applications. Chromate programs were not only effective on steel alloys, but were also effective corrosion inhibitors for copper alloys. Chromate also has the advantage of being non-fouling. This allowed the flexibility to always feed an effective chromate concentration, even in highly corrosive waters and brines.
Goodbye chromate
The phaseout of highly effective chromium due to environmental and health concerns necessitated that cooling programs be operated under less corrosive, higher pH conditions, as illustrated in Figure 1.
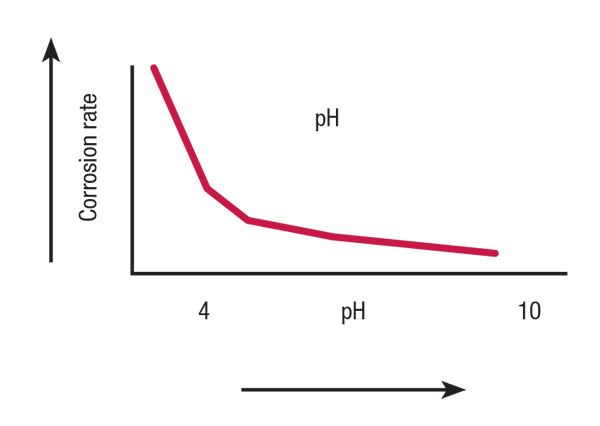
FIGURE 1. This graph shows the general influence of pH on the corrosion rate of iron and copper
A typical formulation would include inorganic ortho- and poly-phosphate, an organic phosphate (aka phosphonate), a high polymer dosage to hold the phosphate in solution, and perhaps a small concentration of zinc. Several factors in such formulations are important to optimize both scale and corrosion inhibition. A brief review of some fundamental aspects of corrosion is provided below.

FIGURE 2. In an aerated-water corrosion cell, iron dissolution and metal loss occur at the anode while oxygen reduction occurs at the cathode
Corrosion is an electrochemical process, although erosion-corrosion also involves mechanical factors. A typical corrosion cell is shown in Figure 2, with the anodic reaction Equation (2) and cathodic reaction (Equation (3) shown below.
As is true for all electrochemical reactions, a circuit must be established for the reaction to proceed, and the anodic reaction and cathodic reaction must proceed at the same rate. In this example, each iron atom gives up two electrons at the anode and the iron ions at the surface dissolve into the solution, as shown in Equation (2):
The electrons flow through the metal substrate to the cathode, where they reduce common species in the water. In typical cooling-system waters, the primary reductant is oxygen, as shown in Equation (3):
The ions formed at the anode and cathode migrate toward each other, completing the circuit. The overall corrosion reaction is shown in Equation (4):
This reaction can cause intense pitting in carbon steel. Also, ferrous hydroxide [Fe(OH) 2 ] will further oxidize to ferric hydroxide [Fe(OH) 3 ] and eventually become rust (Fe 2 O 3 •xH 2 O) that can form heavy deposits and even close off small diameter pipes (Figure 3).
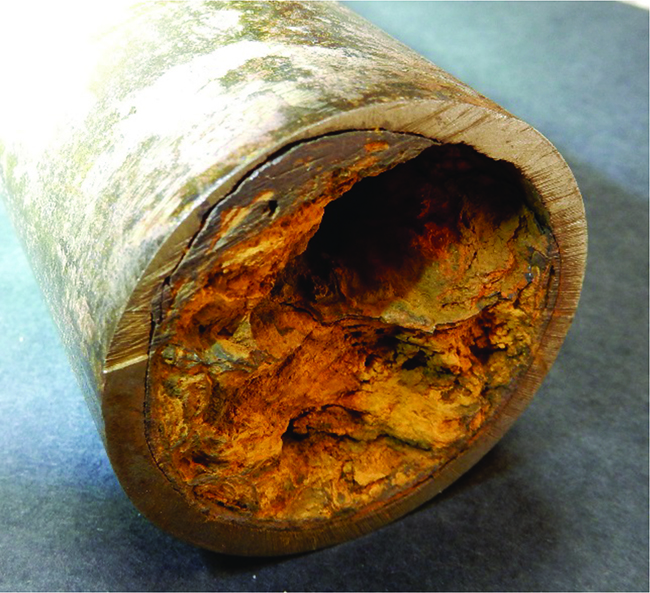
FIGURE 3. Shown here is a section of pipe that has become nearly closed off by iron oxide
deposition
Water-treatment corrosion inhibitors are designed to slow down either the anodic or cathodic reactions, or both. While the old chromate treatment option was technically an anodic inhibitor, correct application would allow the chemistry in the system to establish the formation of a continuous, pseudo-stainless-steel layer on carbon steel.
Now, consider the more complex chemistry of the phosphate/phosphonate-based replacement programs. The list that follows outlines, in general, the function of the main compounds within a typical formulation:
- Ortho-phosphate (anodic/cathodic corrosion inhibitor)
- Poly-phosphate (cathodic corrosion inhibitor)
- Organic phosphates (calcium carbonate scale inhibitor and cathodic corrosion inhibitor)
- Polymer (calcium phosphate scale inhibitor)
- Zinc (cathodic corrosion inhibitor)
- Azole (corrosion inhibitor for copper alloys)
One early treatment method was based on a feed of phosphates, either ortho-phosphate (PO 4), or phosphate compounds that would revert to ortho-phosphate, to precipitate calcium as [Ca 3 (PO 4) 2 ]. These programs also provided corrosion protection, as phosphate will react with ferrous ions (Fe +2) produced at anodic sites to form a rate-limiting deposit, while [Ca 3 (PO 4) 2 ] precipitates in the local alkaline environment at cathodic sites to inhibit electron transfer.
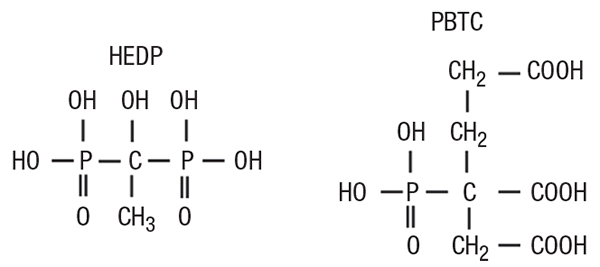
FIGURE 4. This figure shows two common phosphonates, 1-hydroxyethylidene-1,1-diphosphonic acid (HEDP) on the left, and 2-phosphono-butane-1,2,4-tricarboxylic acid (PBTC) on the right. Sometimes other compounds known as phosphinates may be effective
However, even small upsets in phosphate programs can cause severe calcium phosphate fouling, and in fact, Ca 3 (PO 4) 2 deposition can become almost as great a problem as calcium carbonate scaling. Accordingly, treatment methods have continued to evolve to more-forgiving methodologies, where in many cases the backbone of these programs are the organic phosphates (phosphonates; Figure 4) with a supplemental polymer to sequester and modify the crystal structure of scale-forming ions and compounds. Phosphonates attach to deposits as they are forming and disrupt crystal growth and lattice strength.
A common treatment program might include one or perhaps two of the phosphonate compounds in low-mg/L dosages for primary scale control, with 5–15 mg/L or so of ortho-phosphate for additional scale control and corrosion protection, and perhaps 0.5 to 2.5 mg/L of zinc added, as well. Zinc reacts with hydroxyl ions generated at cathodes to form a precipitate [Zn(OH) 2 ], which provides additional cathodic protection. Also typically included in this formulation is 5–10 mg/L of organic polymer for control of calcium phosphate deposition.
It should be noted here that although chromate has disappeared as a treatment option, sulfuric acid feed to reduce alkalinity has remained quite viable, and continues to be utilized in many applications. Reduction of the calcium carbonate scaling potential by acid feed helps to reduce the load on the scale inhibitor and allow higher cycles of concentration and better water utilization efficiency.
Careful monitoring and control of phosphonate-based programs is necessary, because overfeed of phosphonates can lead to calcium-phosphonate deposition. Additionally, phosphonates exhibit varying degrees of susceptibility to breakdown to ortho-phosphate from thermal and chemical stresses, particularly from oxidizing compounds. Degradation of the original phosphonates to ortho-phosphate will, of course, reduce the effectiveness of the phosphonates, and will also increase the ortho-phosphate concentration and potential for Ca 3 (PO 4) 2 deposition.
Non-phosphorus options
Increasing concern with respect to the impact of phosphorus on the environment — in particular, its role in promoting harmful algae blooms in natural bodies of water — has driven demand for non-phosphorus (non-P) chemistry options for treating cooling-water systems. Also factoring into this evolution is the desire to reduce the discharge of zinc, due to its toxicity to aquatic organisms. The best of these non-phosphorous and non-zinc programs now offer important performance advantages, including reduced fouling tendency and better corrosion inhibiting performance in challenging waters.
The original polymers developed for scale control contained only carboxylate functional groups (COO –), where the negatively charged oxygen atoms bind with calcium to modify crystal growth. More advanced compounds such as co- and ter-polymers have structures that may include carboxylate, amide (R-CO-NH 2), sulfonic acid (SO 3 H) and nonionic groups for improved performance and resistance to degradation. These enhanced polymers have been formulated to help control other deposition, including calcium phosphate, calcium sulfate, iron hydroxide, magnesium and calcium silicates, manganese, and calcium fluoride, to name some of the most prominent.
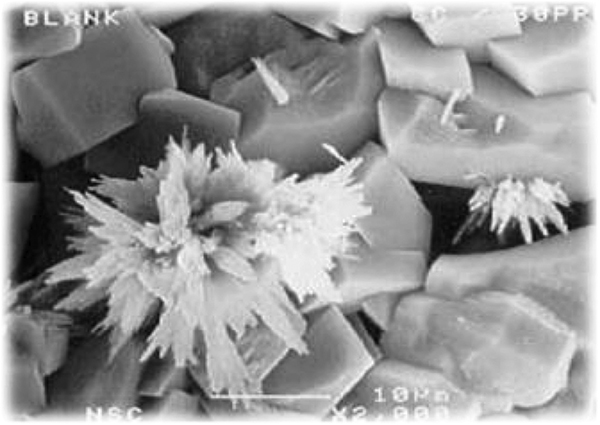
FIGURE 5. The deposition of crystalline mineral deposits on equipment systems can wreak havoc in an untreated cooling-water system
In the absence of any treatment, most minerals will deposit as well-ordered crystals on the surfaces of heat exchangers and other cooling system components, hindering efficient heat transfer (Figure 5).
Such crystals, whether they are calcium carbonate, calcium phosphate, a silicate, or some other species, usually form very tight and tenacious layers on the metal surface, impeding heat transfer efficiency and creating other operating issues.
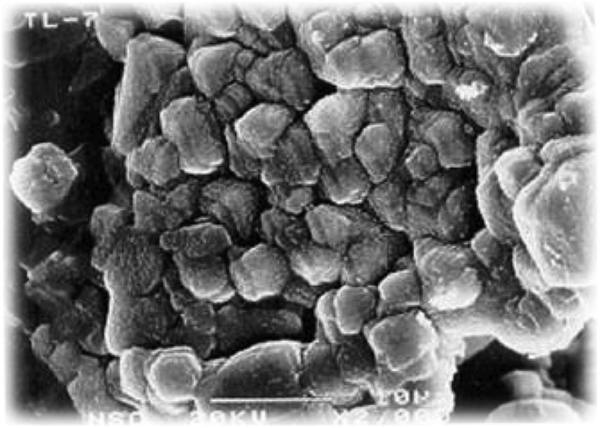
FIGURE 6. When treatment polymers are used, crystals are smaller, irregular, and remain non-adherent, allowing them to be washed away more easily
In large measure, treatment polymers function by interrupting crystal formation; specifically the chemicals distort and interrupt the regular, orderly crystal building block process, producing deposits that remain non-adherent (Figure 6).
These loose materials are more easily washed away. Some polymers also act as sequestering agents, where negatively charged functional groups will bind with cations to prevent them from forming scale. An advantage of polymer chemistry is that each polymer chain can contain many functional groups. Thus, a common range for polymer concentration in the cooling water is 2 to 10 parts-per-million (ppm). To use an old saying: “A little bit goes a long way.”
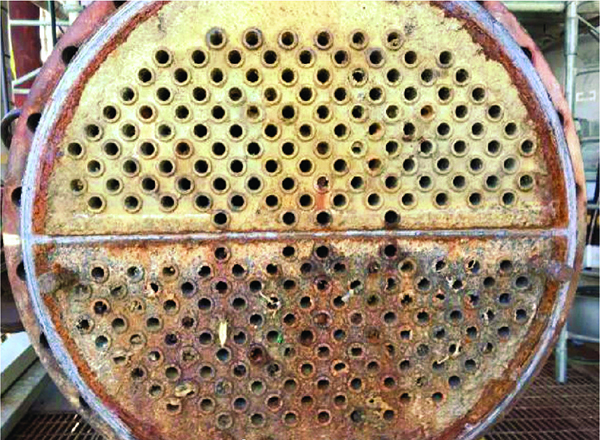
FIGURE 7. This two-pass heat exchanger that is using a zinc-phosphate program shows corrosion on the colder inlet pass, and fouling on the hot outlet pass
But another important question remains: How effective is a non-P program for corrosion inhibition? In the first place, non-P treatments, like phosphate/phosphonate programs, have been designed to operate at an alkaline pH range (7–9), which tends to minimize general corrosion of metals. Even so, corrosion cells can still develop in an alkaline environment (Figure 7).
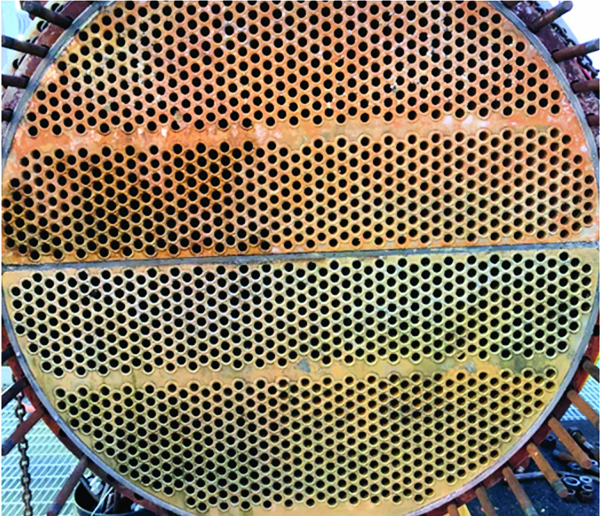
FIGURE 8. This four-pass heat exchanger that is using the RPSI corrosion inhibitor program shows no corrosion or fouling
The key is a reactive polyhydroxy starch corrosion inhibitor (RPSI) that binds directly to the metal surface, unlike phosphate chemistries that must react with calcium to form a protective layer. The RPSI complex is independent of calcium, pH, or other water chemistry constituents [ 1]. This makes the program more forgiving than phosphate and zinc programs, which require precise control of system chemistry to prevent fouling on heat transfer surfaces. The non-fouling nature of the RPSI complex allows it to be dosed to provide the required level of corrosion protection (Figure 8).
Full-scale application of this new chemistry option has proven to be very effective. In one application, at a large industrial complex in the southeastern U.S., RPSI replaced previous polyphosphate and then zinc chemistry (Figures 9 and 10). Carbon steel corrosion rates have been reduced from 0.2–0.25 mm/yr to 0.0025–0.0075 mm/yr.
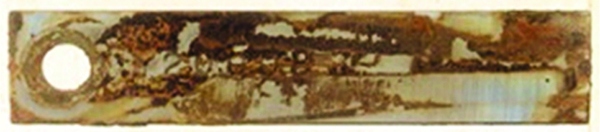
FIGURE 9. Shown here is a carbon steel corrosion test specimen using a polyphosphate water-treatment program
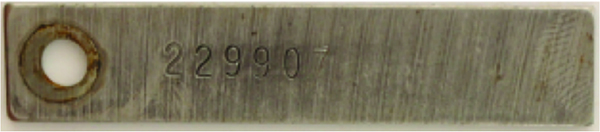
FIGURE 10. This carbon steel corrosion test specimen after converstion to RPSI inhibitor
On a secondary note, the change from zinc and then to RPSI was in part influenced by problems with severe algae formation in a clarifier and recycle pond at the plant. The removal of phosphate from the water effectively addressed that challenge, allowing a 70% reduction in sodium hypochlorite (bleach) usage for microbiological control.
In another example, also at a large chemical plant, traditional phosphate chemistry proved satisfactory for corrosion control, but calcium phosphate deposits caused fouling in some of the plant’s plate-and-frame heat exchangers. Such exchangers are notorious for low-flow locations and deposit accumulation. Conversion to RPSI chemistry maintained excellent corrosion protection and eliminated phosphate deposition (Figure 11).
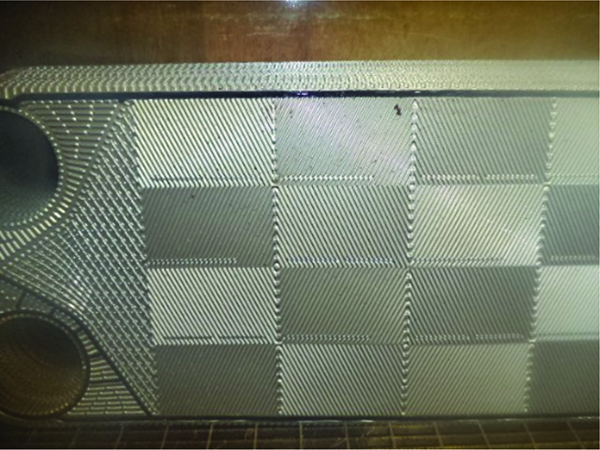
FIGURE 11. After the fouling was removed from this plate-and-frame heat exchanger, it remained clean using subsequent water treatment with non-P chemistry
One of the industries for which this newer chemistry option can be quite effective is power generation, where most plants are no longer base-loaded but instead operate in a cyclical (on and off) manner as part of normal operation. It is critical that a protective barrier be maintained on all cooling system metals in such applications, otherwise severe localized corrosion may result.
Power plants generally directly discharge their cooling water, and consequently face significant restrictions on the use of phosphorous and zinc corrosion inhibitors.
Modern control methods
As with the other technologies, chemical feed and control capabilities have been vastly improved [ 2]. Automation of chemical feed and chemistry monitoring systems can do the following:
- Reduce chemical costs
- Reduce water usage
- Improve safety
- Improve performance and materials protection
- Improved utilization of plant staff
- Improve diagnostics and troubleshooting
- Achieve peace of mind
One aspect in this regard, which is valuable for any program, has been the development of traced chemistry programs, which allow solid state sensors to accurately measure chemical concentrations in the circulating cooling water without the need for reagents, or even a laboratory. Also, the instrumentation that is available for monitoring standard operating parameters has improved greatly in recent years, allowing for accurate, continuous, online readings of critical data, including the following:
- pH
- Specific conductivity
- Oxidation-reduction potential (ORP) for controlling oxidizing biocides
- Corrosion rate
- Scaling potential
- Biofouling potential
- Chemical feed tank levels
The unit shown in Figure 12 contains the instruments needed to accurately monitor and control important aspects of cooling water chemistry. It includes corrosion coupons, sensors, flow regulators and other related hardware. The analytical data can be distributed both internally and remotely to assist both plant personnel and external experts with evaluation of system conditions. Many new plants nowadays, at least in the power industry, are minimally staffed, with few, if any, personnel who are rigorously trained in cooling system chemistry.
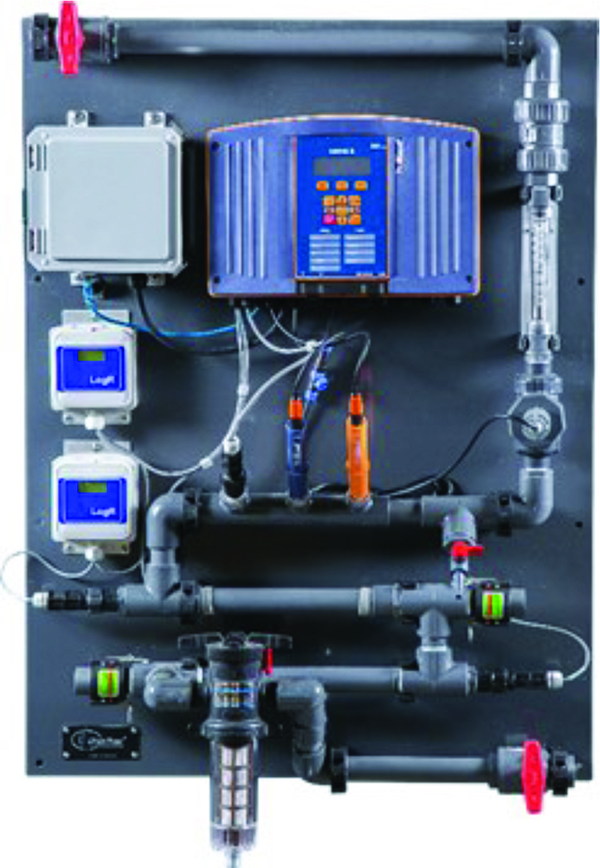
FIGURE 12. This compact cooling-water monitoring unit contains all of the sensors required to monitor, calculate, control, and communicate the key aspects of the cooling-water chemistry, ensuring proper operation
Against this backdrop, a digital data feed that allows outside consultants to monitor system conditions can be quite valuable for maintaining system reliability. Further, ever since Langelier produced his pivotal calcium carbonate scale calculations in the 1930s [ 3], increasingly accurate and comprehensive computer models have been developed to evaluate the scale and corrosion potential for untreated water, and to calculate the proper chemistry, strength and cost of products needed to control scale and corrosion issues. Modeling programs are available for purchase from independent software companies and are also offered by water-treatment service providers, often included with the water treatment chemistry. The best programs are capable of selecting and evaluating the most appropriate and cost-effective treatment programs that meet the plant’s environmental and operating constraints, such as water quality, alternate water sources, and costs for chemicals, water and sewer.
A key aspect with any program is the input of accurate historical chemical analyses of the raw water feed to the system. Both authors have seen over and over again project specifications that have only partial raw-water data — often sampling that is based on just a snapshot in time. Many owners and owner’s engineers do not understand that comprehensive water-quality data are essential, not only for selecting proper chemical-treatment methods, but to ensure the proper selection and sizing of water-treatment components such as clarifiers, filters, reverse osmosis units and other equipment.
Closing thoughts
Chemical-treatment programs for cooling towers have undergone significant evolution over the last several decades. New chemistry formulations and improved instrumentation and control options are making these programs even more effective. A key challenge is microbiological control (which is beyond the scope of this article). The benefits of well-applied scale/corrosion control programs can be quickly undermined if microorganisms are allowed to settle and develop colonies within cooling systems. Microbes thrive in warm and wet environments, and even slight lapses in treatment efficiency may result in big problems.
Edited by Suzanne Shelley
References
1. Tribble, R., Kalakodimi, P., Post, R., Lamm, J. and J.L. Nelson, Advances in Cooling System Passivation and Layup, presented at the EPRI Cooling Tower Technology Conference, August 6, 2015, Louisville, Ky.
2. Post, R., Buecker, B., and Shulder, S., Power Plant Cooling Water Fundamentals, Pre-conference seminar to the 37th Annual Electric Utility Chemistry Workshop, June 6–8, 2017, Champaign, Ill.
3. Langelier, W.F., The Analytical Control of Anti-Corrosion Water Treatment, J.AWWA, Vol. 28 (10), 1936.
Authors
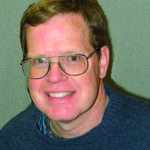
Brad Buecker
Brad Buecker is a senior technical publicist with ChemTreat (5640 Cox Rd., Glen Allen, VA 23060; Mobile: 785-213-2699; Email: [email protected]). He has 36 years of experience in or affiliated with the power industry, with nearly two decades in steam-generation chemistry, water treatment, air-quality control, and related engineering positions at City Water, Light & Power (Springfield, Illinois) and Kansas City Power & Light at the company’s La Cygne, Kansas, station. His experience also includes 11 years at two engineering firms. Buecker spent two years away from the power industry as acting water/wastewater supervisor at a chemical plant. He has authored many articles and three books on power plant water and steam chemistry and air-pollution-control topics. He is a graduate of Iowa State University, with additional course work in fluid mechanics, material and energy balances, and advanced inorganic chemistry. He is a member of the American Chemical Society, American Institute of Chemical Engineers, American Society of Mechanical Engineers, Cooling Technology Institute (corporately), and the National Association of Corrosion Engineers. Buecker is on the planning committees for the annual Electric Utility Chemistry Workshop and Power-Gen International, and he serves on the Advisory Council for the annual International Water Conference.
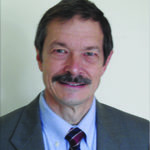
Raymond M. Post, P.E.
Raymond M. Post, P.E., is the director of cooling water technology with ChemTreat (5640 Cox Rd., Glen Allen, VA 23060; Mobile: 804-627-2369; Email: [email protected]). He has more than 40 years of industrial water-treatment experience, specializing in the development, application and evaluation of treatment programs for cooling water. Post is a licensed professional engineer and a member of the American Society of Mechanical Engineers (ASME), the National Assn. of Corrosion Engineers (NACE), the Cooling Technology Institute, the National Society of Professional Engineers. He has served as an advisor to EPRI’s Technology Innovation Water Conservation Program. He earned his B.S.Ch.E. from Princeton University, holds three U.S. patents, and has authored more than 50 technical papers on industrial water treatment.