Optimizing electrical conductivity in next-generation batteries depends on carefully controlling process variables, such as mixing, particle-size distribution and temperature. Presented here is a discussion of how these process variables affect battery performance
In the evolving landscape of energy storage technologies, solid-state batteries (SSBs) have emerged as promising alternatives to traditional lithium-ion (Li-ion) batteries. By employing solid electrolyte materials, SSBs have several potential advantages over traditional Li-ion batteries, which use electrolytes made of liquid solutions. SSBs are capable of higher energy densities than traditional Li-ion batteries, and are not susceptible to the formation of lithium dendrites, which can pose safety risks. In addition to energy density and safety advantages, the substitution of a solid electrolyte material also removes some restrictions in the battery-cell architecture that are present with traditional Li-ion batteries.
In the manufacturing process for electrode materials for both SSBs and traditional Li-ion batteries, slurries of active materials, conductive agents, binders and solvents must be precisely formulated and processed to achieve optimal electrode properties. The electrical conductivity of the battery slurries plays a vital role in dictating the performance of these batteries. Moreover, the batteries’ performance and longevity are intrinsically linked to the structure and properties of their electrodes, which are primarily determined during the manufacturing process.
In order to achieve optimal battery performance, processors need to know how various process variables affect the electrical conductivity of battery slurries. Among the various stages of electrode fabrication, the slurry mixing process is particularly critical. This article discusses the process variables related to the mixing process, and how they can affect the particle size and distribution of the electrode components.
Mixing time
The duration of the mixing process significantly affects slurry homogeneity. Insufficient mixing time can lead to particle agglomeration, resulting in uneven distribution of active materials and conductive agents. This unevenness can hinder both ionic and electronic conductivity. On the other hand, excessive mixing can introduce thermal degradation of sensitive components and can lead to the degradation of the conductive network, increasing the composite volume resistivity and reducing the battery’s performance (Figure 1). Utilizing a continuous mixing system, such as a twin-screw extruder, allows for precise control over mixing time, ensuring uniform dispersion without damaging the materials.
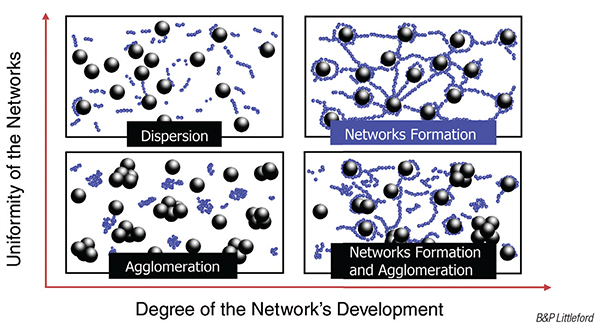
FIGURE 1. Mixing plays an important role in determining ultimate electrode properties. Insufficient mixing can result in uneven distribution of active materials, but overly intense mixing risks degradation of sensitive materials
Mixing speed
The speed of the mixer is crucial in applying appropriate shear forces. Higher speeds can enhance dispersion and break down agglomerates, promoting better conductivity. However, if the shear is too high, it can cause degradation of the binder or other sensitive materials. Conversely, lower speeds may lead to inadequate mixing, negatively impacting slurry viscosity and conductivity. Advanced mixing systems can be configured to provide tailored shear profiles, optimizing conductivity while maintaining material integrity.
Temperature
Temperature influences the viscosity and flow characteristics of the slurry. Optimizing temperature during mixing can enhance the solubility of binders and improve the dispersion of conductive additives. Higher temperatures can reduce viscosity, facilitating better flow and dispersion of materials. This improvement enhances contact between active particles and the electrical pathways within the slurry, ultimately boosting conductivity. Use of jacketed mixing vessels can provide effective temperature management throughout the process.
Particle size distribution
The size and distribution of active materials and conductive agents in the slurry are key determinants of the battery electrode’s ultimate performance. Smaller particles have increased surface area and ionic conductivity, but can also raise viscosity, complicating the mixing process.
Mixing technique
The choice between dry and wet mixing methods significantly affects material integration. Wet mixing, which involves the use of solvents or liquids to facilitate the mixing of active materials, conductive agents and electrolytes, often provides superior dispersion. Included in this category are ball milling, high-shear mixing and ultrasonic mixing. Dry mixing, on the other hand, involves blending solid powders without any liquid medium. It can lead to higher energy density by minimizing solvent content. Examples of this technique are tumbling mixers, ribbon blenders and planetary mixers (Figure 2).
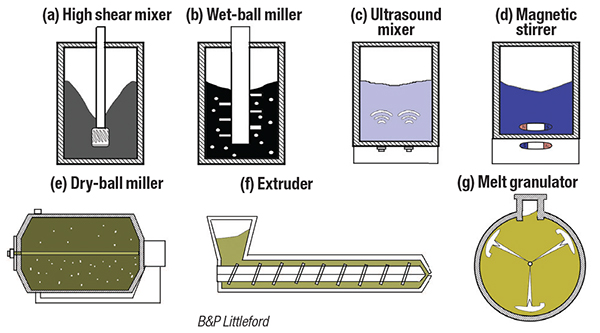
FIGURE 2. Several types of mixing equipment are available, categorized ac-cording to whether or not solvents or liquids are used to facilitate the mixing
The choice of mixing equipment, whether it is a planetary mixer, high-shear mixer, or dissolver, determines the intensity and type of forces applied to the slurry (Figure 3). Equipment that provides uniform shear forces is ideal for creating a well-dispersed slurry, leading to a more uniform electrode structure with lower resistivity and better performance.
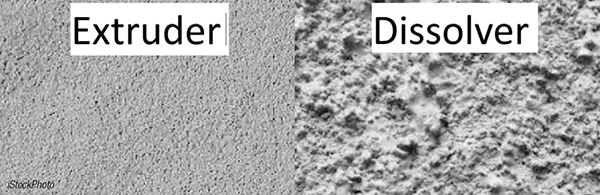
FIGURE 3. The representative image illustrates the degree of dispersion in the electrode slurry. At left, the dispersion achieved with an extruder is higher than with a wet-mixing method
The configuration of the mixing equipment is instrumental in determining mixing efficiency. Some systems utilize advanced geometries to enhance material interaction and ensure uniform dispersion of conductive additives. The ability to create a turbulent flow within the mixer helps break down agglomerates and promotes better conductivity throughout the slurry.
Also, the sequence in which the components are mixed affects the formation of conductive networks. For example, mixing the conductive agent with the solvent first, as opposed to simultaneously mixing all components, can result in a more stable and well-distributed conductive network. This method helps in preventing the collapse of the network structure during subsequent mixing stages, thereby improving the electrode’s electronic properties.
Shear rate and viscosity
The intensity of shear forces during mixing influences particle distribution and orientation. Optimizing shear rates enhances mixing efficiency and slurry uniformity — critical factors for achieving consistent conductivity across the electrode.
The shear rate applied during mixing and the viscosity of the slurry are interconnected variables that influence the particle distribution and network formation within the slurry. These variables are closely related to shear stress, which plays a critical role in the mixing process.
The shear stress, τ, during mixing is defined by Equation (1):
τ = 2.5 ∙γ∙η (1)
Where γ is the shear rate and η is the dynamic viscosity. A higher shear rate can improve the dispersion of particles within the slurry by breaking up agglomerates and promoting a uniform mixture. However, excessive shear can also lead to over-dispersion, where the conductive network becomes too fragmented, leading to higher resistivity. Viscosity affects how easily particles move and interact during mixing. A balance between shear rate and viscosity is essential to ensure optimal particle distribution without damaging the conductive network.
The shear number (SN), often a product of shear rate and time, quantifies the cumulative mechanical stress imparted to the slurry. It is expressed in Equation (2):
SN = (γ ∙ t) / (4∙π) (2)
where γ is the angular velocity and t is the mixing time. A high shear number can indicate extensive particle interaction and mixing, but excessive values can lead to over-dispersion and degradation of the electrode’s structure.
The viscosity of the slurry must be carefully controlled to ensure effective mixing and pumping. High viscosity can lead to poor flow characteristics, which may result in uneven mixing and inconsistent conductivity. Utilizing specialized mixing equipment designed to handle varying viscosities can enhance material interaction and ensure a uniform slurry. Monitoring viscosity in real-time allows for adjustments during processing to maintain optimal flow.
Composition and materials
The electrical conductivity of the battery slurry is significantly influenced by the characteristics of its components. Active materials, such as lithium cobalt oxide or lithium iron phosphate, must be optimally blended with conductive additives like carbon black or graphene. The choice and quality of these materials determine the intrinsic conductivity of the slurry. For example, the surface area of carbon black directly correlates with its conductivity; thus, using high-performance conductive additives can enhance the overall conductivity of the battery slurry.
The slurry composition, including the proportions of active material, conductive agents, binders and solvents, plays a crucial role in determining the final properties of the electrode and in controlling the conductivity. A balanced composition of these components enhances electron transport and ensures sufficient conductivity without compromising the mechanical properties of the slurry. Excessive concentrations can negatively impact the mechanical properties and conductivity. This is due to increased particle-particle interactions, leading to agglomeration. On the other hand, too little of the active material and conductive agents may not provide the desired conductivity. Process optimization based on empirical data can help identify the best ratios for specific slurry formulations.
The distribution of the active material (for example, graphite for the anodes) and the conductive agents (such as carbon black) within the slurry is critical. Uniform dispersion ensures effective electrical conductivity throughout the electrode. Poor dispersion can lead to the formation of agglomerates, which increase electrical resistivity and reduce the battery’s overall performance. Moreover, the order in which these components are mixed significantly affects the dispersion of the conductive materials within the slurry.
The solvent-to-solids ratio in wet mixing also affects the slurry’s viscosity and particle mobility. Achieving an optimal liquid-to-solid ratio in the slurry is vital for ensuring sufficient dispersion without excessively diluting active materials.
Edited by Scott Jenkins
Authors
Janina Lazo-Cruz is a versatile article writer, covering a wide range of topics while actively pursuing a career as a process engineer at a leading Japanese multinational company in electronic manufacturing. A chemical engineer and materials scientist by training, she graduated from the University of the Philippines and has a keen interest in data analytics, lean manufacturing, R&D and product development, and polymer chemistry. She can be reached at the following Email address: [email protected].
Daniel Shafer is responsible for field application engineering on industrial scale chemical process equipment on behalf of B&P Littleford (1000 Hess Ave., Saginaw, MI 48601; Email: [email protected]; Website: www.bplittleford.com). Shafer serves as global sales manager in the Battery Materials Division and is western U.S. sales manager for the entire line of B&P Littleford equipment. Shafer serves as co-director of Nikua Training Center, a multinational non-profit company promoting energy security in the South Pacific. Shafer holds a degree in chemical engineering from Oregon State University.