Solids-handling processes and downstream process steps can benefit greatly from carefully controlled particle characteristics. Presented here is guidance on how agitation agglomeration techniques can achieve desired particle properties
Throughout the diverse sectors of the chemical process industries (CPI), the ability to control the particle characteristics of bulk solids is crucial. Controlling particle characteristics allows producers to manage product performance, ensure shelf life, regulate downstream processes and more. One technique that is especially useful in controlling particle characteristics is agglomeration (particle size enlargement), which converts powders and fines into granules. There are several different forms of agglomeration — some that utilize extreme pressure to form agglomerates, others that use heat, and so on. Agitation agglomeration utilizes motion, typically along with a liquid binder, to form granules. This technique is also sometimes referred to as wet granulation, pelletizing, or tumble-growth agglomeration. The flexible nature of the agitation agglomeration approach allows producers to achieve a specific set of desired particle characteristics.
This article provides information on why controlling particle characteristics is so essential, which particle characteristics can be controlled through agglomeration, and how the various types of agitation agglomeration equipment provide the opportunity to reach the sought-after specifications.
Particle engineering benefits
Chemical producers can use particle characteristics both as a tool in the production line, as well as a way to manage the quality and performance of their finished (or intermediate) product (Figure 1). In each case, their ability to control these parameters is essential in meeting market demands and being able to do so efficiently.
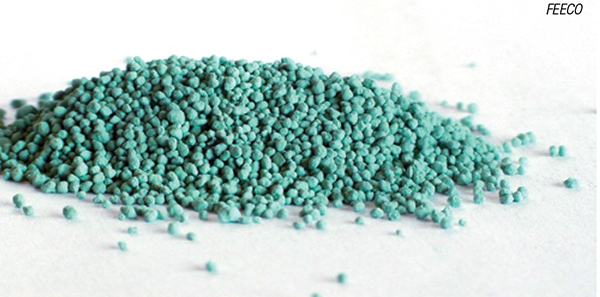
FIGURE 1. Paint pigment micropellets, such as the ones shown here, were produced in a pin mixer, and are an example of how particle characteristics can impact desired product qualities
Particle characteristics in the production line. From catalysts and fertilizers, to specialty chemicals, fillers and more, particle characteristics are often the foundation of every step in a production line. By controlling them, producers can improve flowability and precisely control metering and dosing of process components, allowing them to ensure that products meet a guaranteed analysis, or have the precise chemical composition needed to do their job. Further, particle characteristics can be used to make handling and transporting the material around a facility cleaner and less dusty, minimizing the amount of raw material or product lost to dust. The ability to control particle characteristics also goes beyond the initial production line by allowing producers to control how the solids perform in downstream processes, such as in the smelting process, where particle characteristics are used to promote enhanced gas-solid heat transfer.
Particle characteristics in the product. In an intermediate or finished product, particle parameters are used to reduce shipping costs, improve storage characteristics, and most importantly, meet the precise expectations of the end user. These expectations might include one or more of the following:
- Preventing segregation of the solid product during transport and storage
- Ensuring that products arrive to customers in the exact condition desired
- Mitigating the potential for caking during shipping, storage or on store shelves
- Optimizing the look, feel and performance of the product for its intended application
- Minimizing the amount of particle attrition a product experiences, thereby reducing the amount of product lost as dust and fines
- Ensuring that end products meet the demands of their intended application
In the hydraulic fracturing industry, for example, crude oil producers require solid proppant materials that meet certain specifications in composition, shape and compression strength to hold open rock fissures and allow for efficient hydrocarbon recovery. If producers of proppants were unable to control product parameters, hydraulic fracturing would be much less efficient.
Particle parameters
The particle characteristics that are important in any given setting vary based on the specific industry sector, the nature of the product, and the individual manufacturer. Even within a single plant, the same product is often manufactured in differing qualities and grades, making it essential for producers to be able to meet the different characteristics expected of each product line. Agitation agglomeration allows producers to target the specific set of parameters important to them. Typical parameters that are desirable to control include the following:
- Uniformity index (UI) and size guide number (SGN; the average particle diameter)
- Bulk density
- Particle size distribution (PSD)
- Crush strength
- Moisture content
- Green/wet strength
- Particle shape
- Surface quality
- Porosity
By controlling these parameters, producers are further able to manage solids qualities such as the following (Figure 2):
- Flowability
- Rheology
- Dissolution
- Solubility
- Surface-area-to-volume ratio
- Melting abilities
- Particle attrition
The agitation agglomeration process is also flexible in that it allows for various solid and liquid additives to be included, giving producers control over formulation as well.
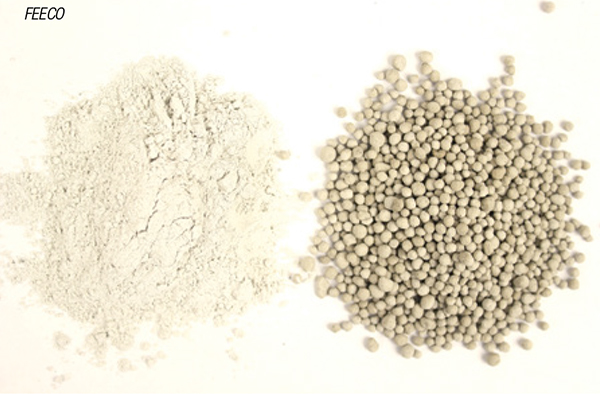
FIGURE 2. Limestone powder (left) can be agglomerated into limestone pellets (right), thereby affecting solids qualities such as flowability, dissolution, particle attrition and more
Equipment
Agitation agglomeration can be carried out using different types of equipment. Depending on the specific goals of an application, the different types of equipment may be used alone, or in combination, to produce the desired results. Typically, the combinations consist of one mixer and either a disc pelletizer or rotary drum. Each type of equipment, and each combination, has the ability to manipulate a unique set of process variables in reaching the desired product characteristics. An overview of the most common types of agitation agglomeration equipment, along with the unique adjustable variables for each, is given below.
Pin mixer. The pin mixer (Figure 3) is a horizontal mixer consisting of a single shaft in a trough. The shaft is fitted with an arrangement of rods or “pins” that, upon rotation, create an intense spinning action inside the trough. This thoroughly mixes solid and liquid feed components into a homogeneous mixture.
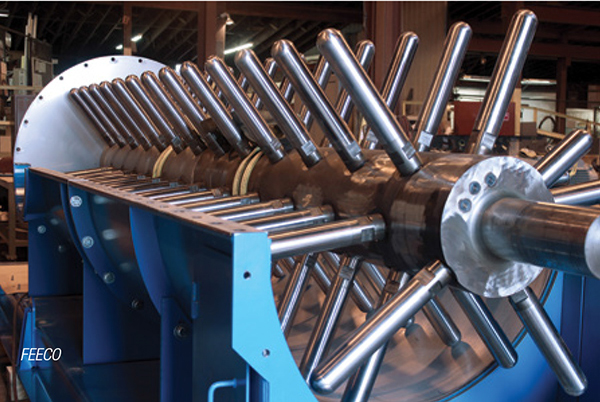
FIGURE 3. Pin mixers, like the one shown here, have a shaft fitted with rods that rotates within a trough
As the material moves along the length of the mixer, this spinning creates a rolling action among particles that facilitates the formation of small, dense seed pellets, or “nuclei,” which may meet the desired granule specifications, or may move on to another piece of equipment for further growth and refinement. Because this process produces small agglomerates, it is often referred to as “micro pelletizing.”
The following variables are adjustable on the pin mixer and can be manipulated to control the particle characteristics of the material exiting the mixer.
Retention time (the amount of time the material is processed in the unit): In the pin mixer, a longer retention time generally equates to more dense agglomerates.
Binder spray location(s): In all equipment, binder spray placement is used to encourage more or less wetting of fines, granule formation, and growth.
Binder and feed rates: For all types of equipment, the rates at which binder and feedstock are continuously fed to the unit generally follow capacity requirements, but in some cases, may require some adjustment to reach the desired characteristics.
Spray-nozzle type: Spray nozzles are available in a variety of designs, producing everything from drips and streams, to atomized sprays. In all types of equipment, the nozzle type is chosen in combination with the number and location of binder sprays to control the wetting of fines, as well as granule formation and growth
RPMs/speed of shaft: In the pin mixer, shaft rotational speed can be used to encourage additional densification without the use of additional binder
Pin arrangement: Pin arrangement refers to the number and placement pattern of pins around the shaft. For example, pins can be positioned in a helical pattern to help move material through the mixer, or they can be arranged for full- or half-sweep, among other patterns
Pugmill mixer. The pugmill mixer, also known as a paddle mixer or pug mill (Figure 4), is also a horizontal mixer. Instead of a single shaft, as in the pin mixer, the pugmill mixer has two shafts that rotate counter-currently to each other in a U-shaped trough. Each shaft is fitted with several paddles. This type of mixer also produces a homogeneous mixture of solid and liquid feed components, but instead of a spinning action, it uses motion comparable to kneading and folding. This produces some agglomerates of varying size, and is often referred to as “conditioning” for its role in de-dusting material fines via wetting and mixing.
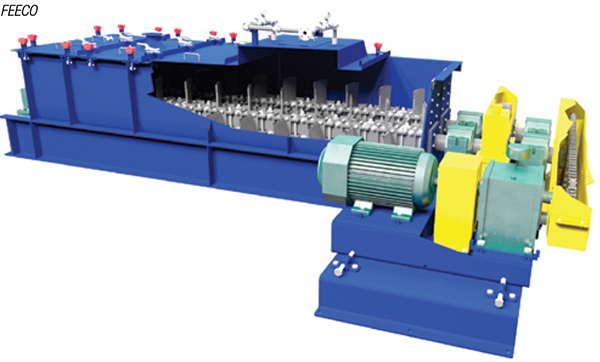
FIGURE 4. Pugmill mixers, like the one shown here, have two shafts rotating counter-currently relative to each other
The following variables are adjustable on the pugmill mixer, and can be manipulated to controlthe outcome of the material exiting the mixer:
• Retention time: Inside a pugmill mixer, a longer retention time typically leads to more agglomerates
• Binder spray location(s)
• Binder and feed rates
• Spray nozzle type
• RPMs (rotational speed of shafts): The shaft rotation speed in a pugmill mixer can be used to encourage more vigorous mixing, as well as more agglomeration
• Paddle arrangement: Paddle arrangement, along with shaft speed, can be adjusted to intensify mixing action, as well as to modify retention time
Disc pelletizer (pan granulator). The disc pelletizer, or pan granulator (Figure 5), consists of a rotating disc mounted onto a stationary base. Binder and feedstock are continuously fed onto the disc. Fines (or seed pellets if a pin mixer precedes the disc) are carried up the side of the disc and cascaded down through the feed stream. Combined with the moisture from the binder, this causes the fines to become tacky and pick up additional fines. The rolling motion forms the aggregated fines into pellets.
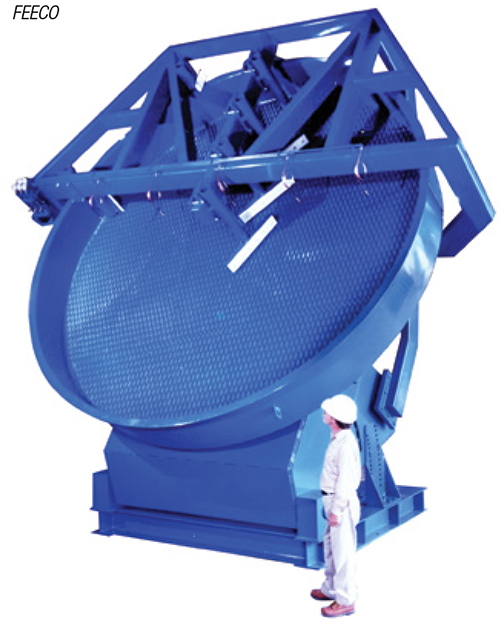
FIGURE 5. This photo depicts a disc pelletizer, showing the rotating disc mounted onto a stationary base
Pellets continue to pick up moisture and fines as they move around the disc, growing in a layering effect known as coalescence. Once pellets reach the desired size, they are discharged from the disc via centrifugal force.
The following variables are adjustable for disc pelletizers and can be manipulated to control the outcome of the material exiting the disc:
- Retention time: In a disc pelletizer, longer retention times typically lead to larger agglomerates.
- Binder spray location(s)
- Binder and feed rates
- Spray nozzle type
Placement of feed location: Feed placement, in collaboration with binder spray locations, can encourage increased or decreased granule formation.
Disc speed and angle: Because the disc pelletizer relies on centrifugal force to carry granules around the disc, disc speed and angle are often adjusted in collaboration to create the desired amount of centrifugal force and are therefore closely related.
Rotary drum (granulation drum). The rotary drum, also known as an agglomeration or granulation drum, is a large, rotating cylinder set on a slight angle, which helps to convey material through the unit (Figure 6). Material may be fed into one end of the unit, or at multiple locations throughout the drum, and binder is sprayed onto the material bed. The rotation imparts a rolling and tumbling motion that causes coalescence. Tumbling flights can be used to assist in agitating the material bed.
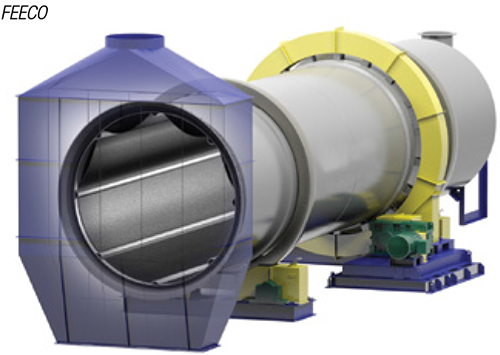
FIGURE 6. Rotary drums are angled to help convey material through the equipment as it rotates
The following variables are adjustable on the rotary drum and can be manipulated to control the outcome of the material exiting the drum:
Retention time: In a rotary drum, a longer retention time typically leads to more polished agglomerates, due to the continued tumbling action.
- Binder spray location(s)
- Binder and feed rates
- Spray nozzle type
- Drum speed: The drum speed can be used to increase the rolling action imparted on the fines.
Drum speed, in combination with feed rate and binder spray locations, can be used to encourage more vigorous tumbling of the bed to better distribute the binder.
Evaluating equipment
The different possible combinations of equipment and process variables, as well as the variation in the starting feedstock, can make it difficult to predict the combination of parameters that will produce the desired results. This often requires a thorough testing program to determine the right combination of variables (Figure 7).
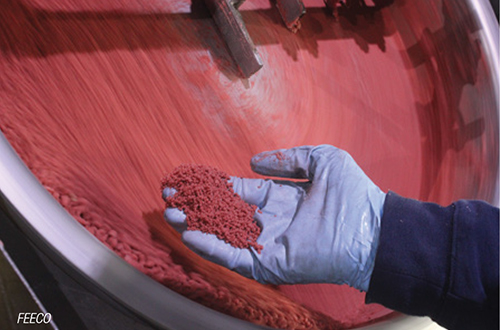
FIGURE 7. Testing is often required to determine the combination of equipment and process variables that will result in the desired solids properties
An understanding of agitation agglomeration fundamentals and the nuances behind each type of equipment helps to expedite this process, as the various physical and chemical parameters of the starting feedstock, along with the desired end product characteristics, can help to inform on the most appropriate equipment configuration. For example, the desire for highly refined granules often favors the pin mixer-disc pelletizer combination, in which the pin mixer yields a thorough mixture of material and begins forming seed pellets that can then further be grown on the disc pelletizer.
In contrast, if the priority is wetting and the formation of only rough agglomerates, a pugmill mixer may best serve the purpose. If the operation requires slightly more refined granules, but will be operating at a higher capacity, a rotary drum may be added after the pugmill mixer to achieve the desired results.
Because each material responds uniquely to agitation agglomeration, testing programs such as those sometimes offered by equipment vendors are often a critical part of developing a successful operation.
Adjustments during production
While process variables must be defined in a new process, in an already existing process, it is sometimes necessary to make adjustments in order to maintain product quality.
When process or feedstock conditions fluctuate, the agitation agglomeration process allows operators to respond as needed, modifying the variables mentioned above to re-stabilize the process (Figure 8).
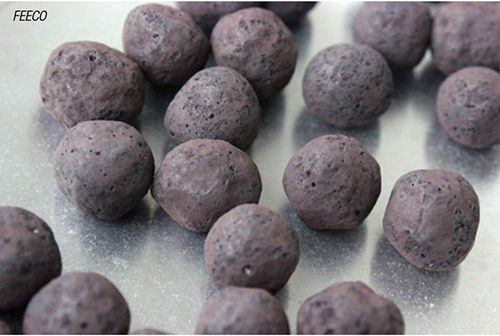
FIGURE 8. When feedstock varies, processors can modify the agitation agglomeration process to maintain product quality
For example, if the feedstock coming in suddenly has a lower moisture content, operators may need to adjust the binder spray rate to maintain the liquid-to-solid ratio. Or, if a pin mixer is in use, the operator may choose to increase retention time in the mixer to maintain the same density of the granules exiting the mixer. Making these types of adjustments can be challenging, as the adjustment of one variable often influences other variables.
For this reason, training operators on the key principles behind an operation is essential to maintaining product quality, minimizing downtime and product loss, and meeting production schedules.
Concluding remarks
For chemical producers, control over particle characteristics is vital to the ability to meet product specifications, streamline processing operations, and operate efficiently. Agitation agglomeration technology can be a powerful tool in helping producers to make granular products according to exacting specifications. However, with the many different types and combinations of equipment, process development testing and operator training are critical to reaching a product with the desired results. Further, consulting a pelletizing or agitation agglomeration expert can also provide the necessary guidance.
Edited by Scott Jenkins
Authors
Carrie Carlson is a technical writer at FEECO International (3913 Algoma Rd., Green Bay, WI 54311; Phone: 1-920-468-1000; Email: [email protected]). She works with engineers to distill complex topics into digestible content. She has been at FEECO for more than a decade.
Chris Kozicki is a process sales engineer at FEECO International (same address as above; Phone: 920-468-1000; Email: [email protected]), where he specializes in tumble-growth agglomeration. Kozicki has been with FEECO for over 35 years. Kozicki is an active member of the agglomeration community and former president of the Institute for Briquetting and Agglomeration (IBA).