Purity requirements and gas properties require different methods for the purification of industrial gases. Provided here are key considerations for selecting gas purification technology
Industrial gases are critical for a wide range of applications throughout the chemical process industries (CPI). In most cases, industrial gases are produced to a particular purity specification, which means they may contain only a limited quantity of contaminants. For many applications, the gases provided by suppliers may not meet process specifications for a given process, meaning that the gas would require purification to further reduce contaminants. An improved understanding of industrial gas generation, storage and separation can help with the selection of the gas purification technology that meets process needs. A number of key considerations can have an impact on the type of gas purifier selected. These include the following: the production method for the gas supply; the purity of the gas source; how the gas source is packaged; the species of impurity molecules to be removed and the expected purity; as well as media selection, media capacity, space velocity, package design and shipping requirements. This article discusses the production of industrial gases with respect to methods of purification, storage, safety and shipping.
Many methods of gas generation exist, but for this article, we will mostly consider the physical separation of components (such as nitrogen from air or hydrogen from natural gas), rather than generation of gases via chemical reactions. Reactions generate gases such as ammonia, using the Haber-Bosch process. Other reactions create gases such as NO, SiH4, PH3, and so on, which are commonly used in the electronics industry.
Physical gas separation
Physical gas separation relies on membrane, catalytic and adsorption processes, cryogenic distillation, and other technologies. A few common ones are discussed here.
Membrane separation. A common air-separation technology uses hollow fiber membranes to separate nitrogen from oxygen (Figure 1). Membrane technology is commonly used when purity requirements are not stringent. Within the membrane system, many thousand hollow fibers are placed in a housing and compressed air is supplied to one end. The fiber wall is permeable to gases, but the diffusion rate across the fiber wall varies by gas. For air, oxygen, carbon dioxide, argon, and other trace contaminants pass through the wall a faster rate than nitrogen, and are directed to vent. Nitrogen exits the membrane system at a typical purity of greater than 95%. The purity achieved by a membrane-based system can be varied by the user by adjusting the flow through the system. The advantage of a membrane-based system is there are no moving parts, but outlet purity may vary with flowrate.
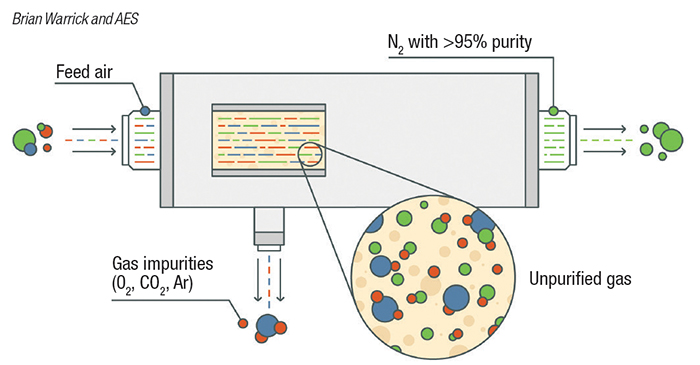
Figure 1. Membrane separation devices, used when purity requirements are not stringent, employ hollow-fiber membranes to separate nitrogen from oxygen
Pressure-swing adsorption. Pressure swing adsorption (PSA) and vacuum pressure swing adsorption (VPSA) are used where purity requirements are higher. When separation of impurities in the high parts-per-million (PPM) level is required, as opposed to separation of impurities at the percentage level, PSA is an option (Figure 2). PSA systems are typically used as pre-purification of gases entering a cryogenic process and for the purification of hydrogen. VPSA technology (Figure 3) is used for on-site float glass production and medical-grade oxygen.
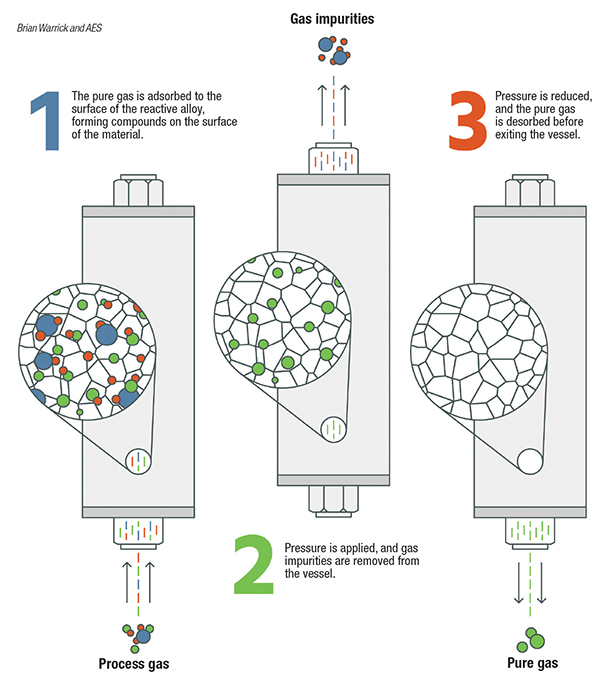
Figure 2. Gases can be purified using a range of different purification media, including zeolites, metal alloys and others
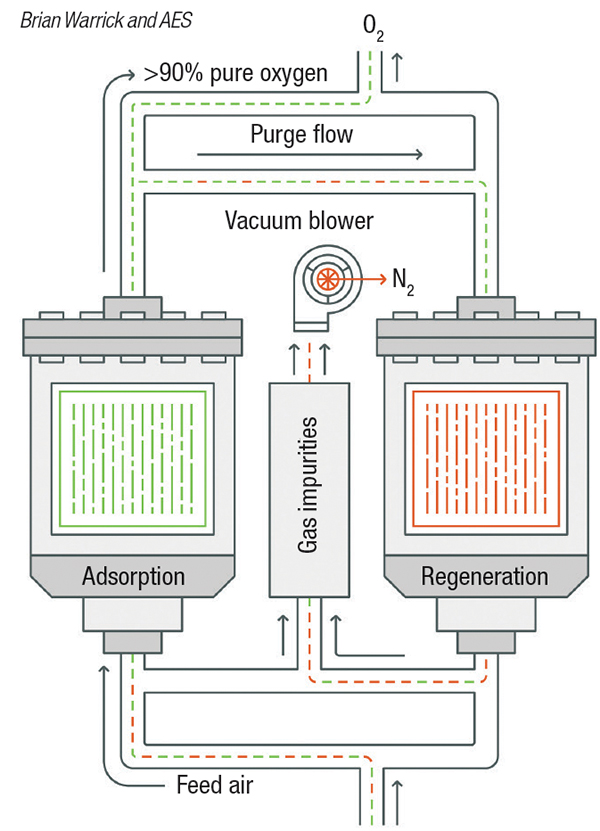
Figure 3. Vacuum pressure-swing adsorption is used when gas purity requirements are higher
PSA systems consist of pairs of vessels operating in parallel, or they can be designed in configurations with multiple vessels in series. Each vessel is packed with adsorption media, such as carbon molecular sieves, zeolites and charcoal. Feed gas to be purified passes through one or more vessels operating at pressures typically greater than 100 psig. Impurities within the feed gas stream are physically adsorbed (physisorption) onto the surface of the media by Van der Waals forces (weak bonds created by short-range electrostatic interactions among molecular dipoles). PSA systems work by taking advantage of differing adsorption behavior at different pressures and temperatures. Adsorption sites are occupied by impurity molecules, while the desired gas passes through the media. Capacity for each impurity varies based on the media selection, often determined by the pore size. As impurity molecules break through the PSA vessels, the media requires regeneration to remove the adsorbed impurities. Within a PSA system, the vessel is isolated and the gas is rapidly vented to atmospheric pressure, which releases the trapped impurities. The vessel is then repressurized and is ready for more feed gas. This regeneration may be completed at a cycle time of minutes to hours. For the separation of nitrogen or oxygen from air, the cycle is typically short.
Cryogenic distillation. When low-parts-per-million-level gas purity is required, cryogenic distillation is typically used. Cryogenic processes are based on the physical separation of gases relative to boiling point. Many gases may be cryogenically separated, but air separation is described here (Figure 4). Compressed air is chilled and then passes through a molecular sieve bed to remove moisture, hydrocarbons and carbon dioxide before entering the distillation column. Gas entering the column is cooled to cryogenic temperatures against outflowing gases. To maintain the balance of refrigeration needed to sustain the process an expansion turbine is often used. The air travels up the column through a series of trays against reflux liquid that is cascading down the column. Separation of the gases occurs because of different boiling temperatures. Nitrogen at 99.999% pure or greater may be supplied directly as vapor, or liquified for cryogenic delivery. Impurities within the nitrogen typically include carbon monoxide and hydrogen, which have a similar or lower boiling point.
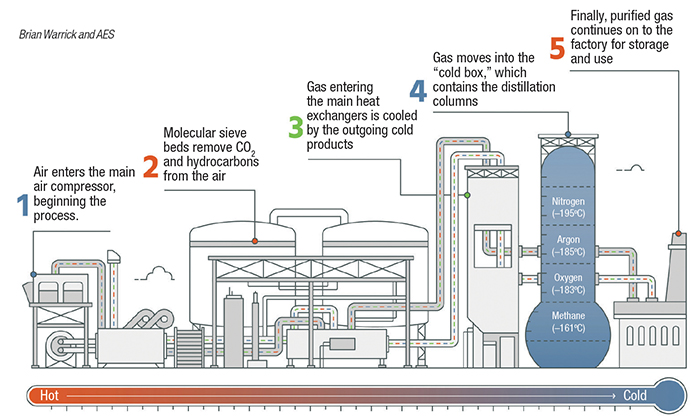
Figure 4. Air-separation units, like the one shown here, separate gases according to differing boiling points, using cryogenic distillation
H2 and He generation
Some gases are generated from stored reserves, such as natural gas. Helium is recovered from select gas fields, throughout the southwestern U.S. and other select areas of the world. Recovered helium may be liquefied for use in magnetic resonance imaging (MRI; the largest consumer of helium), as well as device cooling within the electronics industry, for flotation devices and others.
Hydrogen is produced from natural gas using a steam methane reformer (SMR) and is the source of more than 90% of all hydrogen. With a SMR, steam and methane from natural gas react over a catalytic material at elevated temperature to create hydrogen and carbon monoxide according to the following reaction:
CH4 + H2O —> 3H2 + CO
The H2 – and CO-rich stream further reacts with another catalyst to generate hydrogen and carbon dioxide. This hydrogen then enters a PSA system, in which carbon dioxide is separated, while trace levels of contaminants are trapped at elevated temperature and then released during the depressurization step. Hydrogen may be liquified for delivery into a cryogenic storage tank or supplied as a vapor via tube trailers, cylinders or pipeline. Cryogenic hydrogen will typically meet a purity level of 99.99999% without further purification.
Gas storage
Once generated, industrial gases are typically stored for delivery in cylinders, tube trailers, liquid containers, or connected to a pipeline after on-site generation (Figure 5). Storage cylinders range in size from small volume, and sub-atmospheric delivery pressure to greater than 200°C at pressures exceeding 3,000 psi. Tube trailers contain multiple horizontal tanks operating at high pressure and capable of storing thousands of cubic feet of gas. Hydrogen and helium are commonly stored in tube trailers. Atmospheric products, such as nitrogen, argon and oxygen, as well as specialty products, such as ammonia, are stored in dewars as a liquid or cryogenic product. Dewars are typically on wheeled bases, which allow for easy transport. During use, liquid is vaporized at a typical pressure greater than 100 psi. Dewars are commonly used for orbital welding, where a gas purge is required to protect the weld from contamination.
For production facilities requiring large quantities of gas, bulk liquid storage or on-site generation is common. On-site storage of cryogenic nitrogen, oxygen and argon (commonly referred to as bulk atmospheric gases; BAG), as well as hydrogen, ammonia, and others, allows for uninterrupted flow and stable delivery pressure. BAG and hydrogen products are stored in insulated horizontal or vertical tanks ranging from 1,500-gal to over 50,000-gal cryogenic capacity. These tanks are refilled with cryogenic product delivered via a tanker truck. Ammonia and other specialty gases are stored in bulk liquid sources commonly referred to as a tonner or ISO-container. These containers are typically replaced instead of being refilled. For high-volume end-user facilities, on-site gas generation of BAG and hydrogen is common.
Gas purification media
Common purification technologies are selected based on the class of gas, such as: inert, rare, fluorinated, corrosive, toxic, hydride and so on. Further, the technology choice is refined by the impurity removal required. It is important to avoid using a purifier with a gas or class of gases other than the one for which it was built. Many types of media used for purification are significantly more reactive than media used in front-end gas separation. For example, charcoal may be used in front-end air separation, but activated nickel can only be used for subsequent purification. While charcoal may be safe for air, if a percent-level amount of oxygen is passed through activated nickel, an exothermic reaction may result, generating heat in excess of 1,000˚C. Even as inert a material as a molecular sieve will generate significant heat if exposed to saturated moisture.
For most industrial-gas applications, the most common request is for the removal of moisture. This can be achieved using zeolites as purification media, but care must be taken to ensure selection of the proper zeolite for this purpose. As noted, saturated moisture may generate heat, improper pore size may impact efficiency and capacity, and some zeolite media are not compatible with corrosive and other gas classes.
Zeolite use in gas purification is not limited to moisture removal. Zeolites may be used in cryogenic applications to trap a variety of impurities, but the most common use for them is at ambient temperature. Moisture removal is a result of physisorption, as described above. A key difference in the use of zeolites for purification is that activation is completed by flowing gas through the media at an elevated temperature. This method optimizes purification, which can be sized for one year or longer life time.
In applications where removal of oxygen, carbon monoxide, hydrogen, and others is required, metal catalysts are typically used. Metal catalyst may be operated at ambient or elevated temperature. Common metals include nickel, copper and palladium, but a wide range of metal catalysts are available based on the feed gas. Many metals used in purification are not in pure elemental form, but rather, are used as a high-surface-area powder residing on a zeolite support. The quantity of metal may be as small as 0.5 wt.% for some media. Ambient-temperature metal catalysts operate on the principle of chemical adsorption or chemisorption (Figure 4). In the case of nickel, when contacted by carbon monoxide, nickel carbonyl is formed. Similarly, oxygen within the gas stream forms nickel oxide. These media require the addition of heat and hydrogen for activation. Hydrogen reacts with the catalyst at elevated temperature to reduce the carbon and oxygen bonds, leaving a pure nickel surface.
When removal of methane and nitrogen is required, a rare-earth metal alloy is used. These alloys are commonly Zr-based and are highly reactive with impurities. Operating at temperatures in excess of 300˚C, impurity molecules are adsorbed onto the surface and become a permanent part of the alloy, similar to a pill being absorbed in the body. Such media may be used only once, and in contact with impurity levels above 100 ppm, may generate an exothermic reaction stronger than that with nickel and generate heat in excess of 2,000˚C.
A wide variety of additional purification technologies, including highly selective membranes, cryogens, oxides, and so on, also exist, and are available for specialized applications.
Capacity and efficiency
Once the gas source, the purity of the incoming product and the impurities required for removal are understood and the purifier media is selected, the flowrate and pressure need to be determined. Not every medium has the same capacity for each impurity. Metal alloys have a high capacity for removing oxygen, but very limited capacity for nitrogen. Further, capacity is impacted by the quality of the media used. If the goal is to remove moisture from the feed gas stream and a 5A molecular sieve is used, then the removal capacity will be different than using a 13X molecular sieve. Therefore, after a medium is selected, the capacity for each impurity needs to be understood.
Next, the expected lifetime of the purification system needs to be considered. Specifically, the question is how long the purifier needs to last between regeneration or placement. For ambient temperature, zeolite and metal catalyst media, the general rule of thumb is a one-year lifetime, based on the “typical” impurity content within the feed gas stream. As discussed above, the typical impurities can be determined in many gases by simply knowing the method of gas production.
The final consideration surrounds packaging the purifier media. Here, space velocity is important to ensure the gas makes proper contact with the media. Insufficient contact means that flowrate changes, and outlet gas purity will also change. A goal of properly selecting a purifier is to ensure consistent purity with varying flowrates. In many applications, the end users’ processes are as dependent — or more dependent — upon consistency, than upon purity concentrations.
To optimize the final shape of the gas purification system, the aspect ratio, cross-section area, packing density and required pressure loss across the bed need to be considered, as well as whether the purifier will fit into the end-user’s space constraints. Optimization of the final product is possibly the most critical step in purification. Beyond a laboratory-scale purifier, consistency must be considered to ensure the purifier aligns with existing and potential future equipment design.
The final packaged purifier then needs to be shipped to the end user. Many zeolites and oxides can be sent via standard shipping methods, but many metal catalysts and alloys may require hazardous shipping. The International Air Transport Association (IATA) defines regulations for shipment of all hazardous materials sent via aircraft. Depending upon the hazardous material class and package group, limits on shipping quantities may apply. In these cases, a special permit may be required. Determination of hazardous material and special provision requirements are determined by IATA regulations.
Impurity concentrations
Not all 99.999%-pure gases have the same impurity loading and not all 99.999%-pure gases contain exactly 10 parts per million (ppm) of impurities. When selecting a purifier, a common question is “what is the impurity concentration?” This is the most important aspect of purifier selection and has significant impact on cost and lifetime of the purification system. Nitrogen generated in cryogenic form provides a good example. As nitrogen passes through the distillation process, trace amounts of carbon dioxide, moisture, and all hydrocarbons, as well as components with boiling points higher than that of nitrogen, liquify into a waste stream. Nitrogen exits the column containing hydrogen and carbon monoxide, which are not liquified, because of their higher boiling points. Further, if the nitrogen is liquified for cryogenic storage, hydrogen typically flashes from the liquid due to its boiling point. Therefore, nitrogen from a cryogenic source is typically closer to a 99.9999%-pure product. While some specialized distillation processes exist, nitrogen generated from a distillation column is typically the same across grades. What may vary is how the nitrogen is processed following distillation. For higher purity grades, enhanced transport and analytical testing is used to ensure the delivered product is of the highest purity. The gas may have a certificate of conformity. Other gases follow similar behavior, specifically that the impurity content within the gas may be predicted by how the product was generated.
A common element of the separation methods referenced above is the use of an adsorbent or catalyst to remove or separate components. Purification is simply an extension of these gas-generation technologies. With the exception of liquid hydrogen, the purity of each technology is 99.999% or greater (Figure 6). For many applications within the electronics industry, purity on the order of 99.9999999% is required. Therefore, enhanced technologies are required to further drive purity to these levels. A plot (Figure 7) demonstrates oxygen, moisture and carbon dioxide impurities removed to less than 50 ppt, When discussing the purity of a gas, a common terminology is to refer to the number of nines used to express the purity level. For example, a gas of 99.999% purity is referred to as a “5 nines” (5N) gas and may contain up to 10 ppm of total contaminants. For industrial gas purification, purity of 7 nines (7N; less than 100 ppb of impurities) to 9 nines (9N; less than 1 ppb of impurities) is common.
7N or higher purification technology exists for most industrial gases, but not all impurities can be removed from each gas. An example is oxygen, which contains high-ppm levels of inert gases. Standard purification technologies do not offer a means of removing inert gases from oxygen. Therefore, purified oxygen may be only a 5N gas, even though methane, moisture, hydrogen, carbon monoxide and carbon dioxide are removed to low-ppb levels.
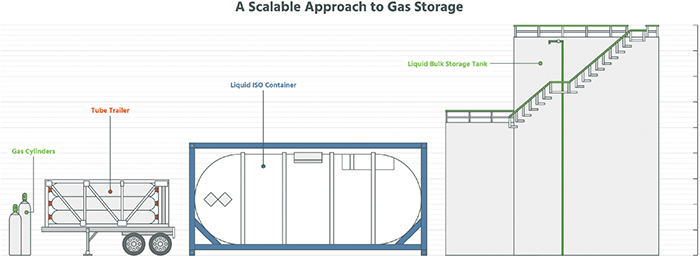
Figure 5. Several gas-storage options are shown here
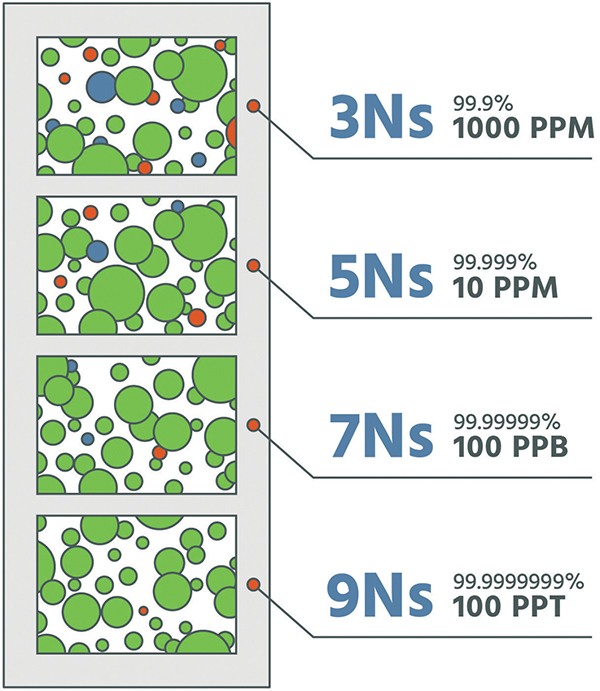
Figure 6. The number of “Ns” represent the level of purity of the gas
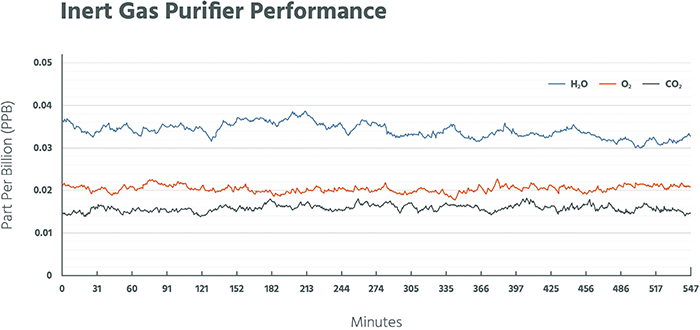
Figure 7. The plot shows the reduction of impurities to the parts-per-trillion level
Edited by Scott Jenkins
Authors
Brian Warrick is director of purification technology for Applied Energy Systems Inc., (180 Quaker Lane, Malvern, PA 19355; Email: [email protected]; Phone: 610-647-8744) ARM Purification division, a position he has held since 2013. Warrick has over 20 years of professional experience within the industrial gases and equipment industries, and has demonstrated expertise in research and development, product line development, sales, manufacturing, proposals and contracts. Prior to joining AES/ARM, Warrick worked in various capacities for Praxair Inc. He is author or coauthor of six U.S. patents. Warrick holds a master’s degree in physics from the University of Colorado and is a Six Sigma Green Belt.
Dan Spohn is the director of purification business development Applied Energy Systems (same address as above; Email: [email protected]; Phone: 610-647-8744). Prior to joining AES/ARM, Spohn held technical sales and marketing positions for several companies and was an engineering manager and mechanical engineer. Spohn is a veteran of the U.S. Navy and was educated at the U.S. Naval Nuclear Power School.
Editor’s note: To view additional graphics associated with this article, visit the online version of this article at www.chemengonline.com