Special considerations must be made for loading expensive solid catalyst materials into fixed-bed and tubular reactors
Most units in the chemical process industries (CPI) use complex and expensive heterogeneous catalysts aimed at improving reaction performance. Although sometimes overlooked, the solids-handling practices associated with loading and unloading solid catalyst materials into and out of reactors can have a significant impact on the ultimate performance of the catalyst, the operation of the process and the safety of the personnel involved. Even the most highly engineered solid catalysts can exhibit reduced performance and present safety hazards if they are not correctly handled and loaded.
Efficient catalyst loading significantly increases the process unit’s performance by improving the flow distribution inside the reactor and also preventing any settling of the bed, resulting in more reliable operation. This article discusses some of the potential issues that can arise from improper loading of solid catalysts and explores best practices and current technology for achieving proper loading.
Catalyst materials and usage
Catalysts, inlcuding homogeneous, heterogeneous and biological catalysts, are added to a chemical reaction to increase the reaction rate. They are manufactured globally by a number of specialized suppliers that design them to reduce environmental emissions and production costs.
Many solid hetergeneous catalyst substances have transition metals as active sites, and the desired reaction occurs on the surface of the solid. The electron structure of transition metals adsorbs reactant molecules strongly enough to allow the stabilization of a transition state for the reaction, but not so strongly as to prevent desorption of product molecules from the catalyst surface.
Cobalt is a key constituent of a number of catalyst systems used worldwide for hydrotreating and hydrodesulfurization, Fischer-Tropsch synthesis and gasoline mercaptan removal. Other catalytic applications of cobalt include production of the monomer for manufacturing polyethylene terephthalate (PET), a plastic often used for beverage containers. Precious metals, such as platinum, palladium, ruthenium and silver, are effective catalysts in many applications because of their extreme stability at high temperatures and pressures, and their inertness to chemical reactions.
The range of different ways catalysts are used is broad. In polymer production, the catalyst material is often injected into a reactor containing the monomer and hydrogen under pressure. The polymer particles are formed and removed from the reactor.
Fixed-bed reactors are the most common type of reactor for solid catalysts. These are typically cylindrical vessels filled with catalyst pellets. The gas or liquid reactants flow through the solid catalyst bed and are converted into products.
Tubular reactors/reformers consist of a series of tubes containing the catalyst (Figure 1). This type of reactor is normally used in cases where the process must be carried out at high temperatures, and where hot gases are present on the outside of the tubes. Tubular reactors are also used where the process is highly exothermic and coolant needs to be applied to the outside of the tube.
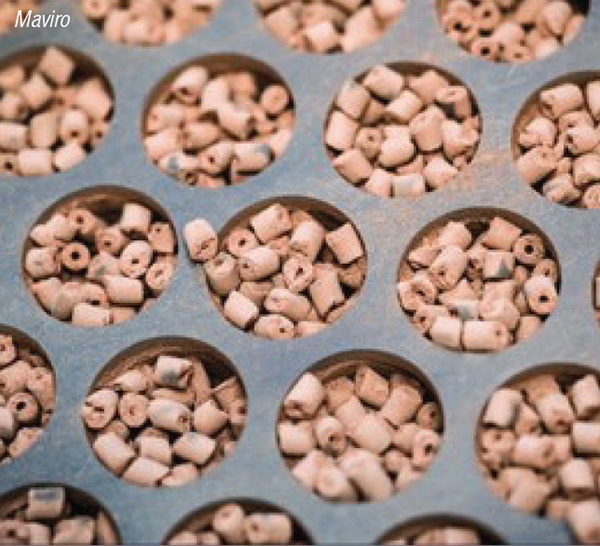
FIGURE 1. Tubular reactors contain a series of tubes that contain the solid catalyst material, as shown here
In both cases, the presence of multiple tubes makes it possible to reach and maintain the very high or low temperatures required. Achieving the temperatures needed would be difficult if a single bed was utilized.
Fluidized-bed reactors suspend small catalyst particles by the upward motion of the fluid to be reacted. The fluid is typically a gas with a flowrate high enough to mix the particles without carrying them out of the reactor. Fluidized-bed reactors are typically multiple-vessel units whereby under normal operation, the catalyst will migrate between vessels.
Catalyst handling
Catalyst handling applications involve full containment of catalysts and require very limited exposure to workers. Loading and unloading of catalyst materials is often best completed by specialist catalyst-handling companies that have the expertise and technology to perform this work (Figure 2).
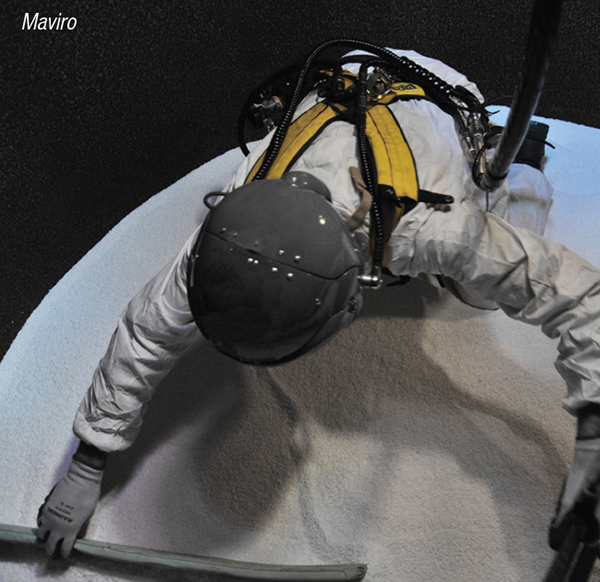
FIGURE 2. Loading of solid catalysts is often best accomplished by specialist companies with specific experience and equipment to carry out the operation
Loading and unloading encompasses a wide range of operations. Pre-bagging is basically transferring the catalyst material from its original packaging to intermediate hoppers. Screening and sieving normally involves removing the catalyst from a reactor, sieving the different-sized particles and removing the undersized solids, dust and fines from the catalyst. The screening step may be required due to a blockage at the top of the reactor, which can cause pressure-drop and flow problems. Sieving is also used to remove other materials, such as ceramic balls that can be used as an inert support in catalyst beds. In the majority of instances, the loading method is dictated by the manufacturer.
Fixed-bed reactor catalysts are usually dumped out of the reactor via a reactor catalyst dump chute, or vacuumed out from the top manway of the reactor via a catalyst vacuum truck. The materials are unloaded into drums, supersacks, flow-bins or roll-off boxes. The methods used here are generally determined by the user.
Loading methods
The following sections discuss various methods for loading solid catalyst materials.
Vacuum loading. This consists of pneumatically conveying the catalyst directly from approved packaging types into the reactor via a vacuum system. The vacuum system creates a negative vacuum on the reactor containing the catalyst material, which is then conveyed into the reactor. This method minimizes operator exposure and environmental impact, as well as eliminating the requirement for crane support.
Direct loading. The catalysts are placed in bags and the bags are lifted with cranes. They are made to pass through a dust containment system before being loaded into the reactor. There are two types of catalyst loading methods for fixed bed reactors, namely, dense loading or sock loading. Sock loading would be the least expensive loading method.
Dense loading. In dense loading, a device is used to spread the catalyst evenly in the reactor, in order to reduce void space, reduce channelling and to achieve a greater catalyst density gain. Dense loading technologies differ in their approach, with some using rotating equipment and others relying on air as a propellant to spread the catalyst. Nitrogen can be used in place of air for self-heating catalysts. Dense loading methods require constant operator attention to regulate the feed rate and avoid surges. It would normally require an operator inside the reactor to follow loading. Periodic checking of the level and evenness is required during loading.
The dense loader is set-up to load catalyst through the top manway on the reactor, if the reactor is a multi-bed reactor. The loader is set up at the inner bed tray section, loading into the lower bed.
Sock loading. Sock loading is a method in which the catalyst is transferred from a loading hopper at the top of the reactor into the catalyst bed via a flexible sleeve or sock. It typically consists of a rigid pipe attached to the discharge nozzle of the hopper at the top, and a flexible sock at the bottom. This equipment allows the catalyst-loading technician to keep the loading sock full of catalyst and prevent the catalyst from free-falling a maximum of three feet from the discharge area while loading the catalyst bed to the correct level. The sock is shortened as the loading operation continues and as the solid level increases toward the desired level of the catalyst bed. The same technique is also used to load multi-bed reactors.
Tubular reactor/reformer loading. Loading a tubular reactor requires directly filling the catalyst into each individual tube. In the past, this has been a highly labor-intensive operation, so numerous multi-tube-loading devices have been developed and are available.
Loading tubular reactors has historically presented many challenges for contractors to address. During the infancy of efforts to address the unique challenges of emptying thousands of tubes ranging in size from 0.5 to 1.5 in. in diameter, a significant portion of those efforts were focused on reductions in manpower, and reducing exposure to dust and injury, as well as lessening the physical labor the work involved.
These challenges were compounded by the need to maintain a clean, climate-controlled work environment, and the need to recover precious metals from catalysts. Also, the fines generated during catalyst-handling activities can present health hazards.
The objective of the loading operation is to consistently load fresh catalyst into the tubes while meeting the requirements for exact outages and narrow ∆P tolerances across the tube-sheet (typically 3 to 5%), without bridging the varied sizes and shapes of the catalyst particles.
In more recent years, catalyst-handling contractors have invested significantly in the development of new technologies, equipment and methods for the removal and replacement of these expensive catalysts (Figure 3).
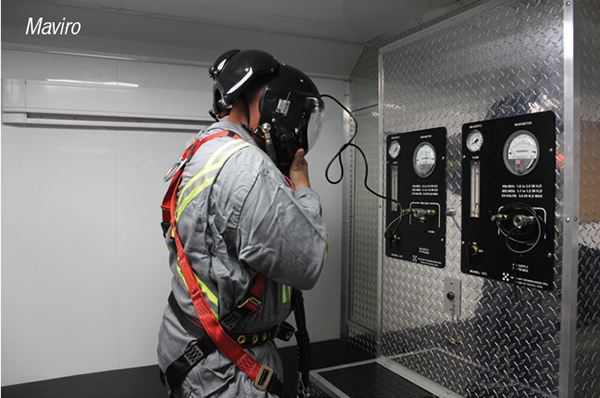
FIGURE 3. Modern catalyst loading requires equipment like the breathing mask shown here being tested for use inside a reactor
Among the innovations resulting from the push to improve the loading of tubular reactors are multi-tube fish-tape and recovery troughs, as well as electronic differential pressure (DP) measuring devices, air-lance unloading equipment and vibratory loaders. The term “fish tape” refers to catalyst guide tubes used to unload catalysts with maximum dust containment and catalyst recovery.
By employing the newer tools, reactor contractors that once used simple templates with openings matching the pitch and inner diameter of tubes observed reductions in the time required to perform catalyst changes. They also saw improvements in spent catalyst and precious metals recovery, product yields, catalyst life and the quality of the overall run cycle.
Current technology
The predominant technology employed in the U.S. tubular market today involves loading systems that drop bulk catalyst charges from a hopper by tube volume into cartridges loaded onto ten-tube vibratory loaders. Tracking of progress and status of each tube as it is loaded is essential to avoid mistakes when so many tubes are involved.
In order to accurately track loading progress, color-coded caps cover each tube. The availability of four or five different cap colors is typically required, so if a reactor contains 10,000 tubes, up to 50,000 or 60,000 tube caps are required per reactor. The installation, removal and re-installation of these caps can be a very time-consuming, but necessary, step in the loading process. The requirement for accurate tube counts between shifts and other times is also very time consuming. For each loader inside the vessel and on the tube-sheet, a dedicated operator is required, along with a runner who delivers the filled cartridges to the loader operator.
This system also requires two or three additional personnel at the charging hopper in addition to hole watchers, ground and other support personnel. With most reactor inner diameters at 20 in. or less, the space accommodates anywhere from four to six ten-tube loaders, requiring a crew of 12 to 16 people.
Once installed, the wheeled, individual loaders are moved relatively easily via a system of tracks. These systems are electrically driven with built-in dust collection that is fairly adequate. Load results are typically good, with an average of 50 tubes at a time filled.
Next-generation loaders capable of loading 120 tubes at once, and tube-sheet cover plates that replace the need for individual tube caps, have recently become available. They include a de-dusting hopper and two stages of built-in dust collection. The pneumatically driven units have several features to prevent double loading of tubes. Tube-sheet cover plates can be custom made for each reactor, based upon reactor and tube-sheet inner diameter, tube inner diameter and pitch.
Every catalyst manufacturer will likely have recommended best practices on how to load their product into a reactor. Reputable catalyst handling companies can contribute valuable experience and special equipment to accomplish the loading safely and correctly.
Edited by Scott Jenkins
Author
John Deajon is the vice president of catalysts for the U.S. at Maviro Inc. (1102 Howard Drive, Deer Park, TX 77536; Phone: +1-833-462-8476; Email: [email protected]). Deajon has worked in the catalyst business since 1995, and his career has touched on all aspects of the industry. Deajon was a field employee, an equipment manager, a corporate life support manager, an operations manager and a general manager before becoming vice president of Maviro’s U.S. catalyst operations in 2020. He is based on the U.S. Gulf Coast.