New hardware combined with monitoring technologies can help optimize combustion now and in the carbon-conscious future
Combustion has long been a delicate balancing act. Chemical processors want their combustion systems to be fuel efficient and available for use, while at the same time, they must also be safe and meet emissions standards. Unfortunately, these requisites are often at odds with each other. Recently, the trend toward reducing carbon emissions is throwing yet another challenge at combustion management. However, thanks to new technologies and the inclusion of combustion monitoring, processors may find it easier to achieve harmonious balance, even in a carbon-conscious culture.
“The general issue with combustion is that as processors try to meet production goals, they are forced into a situation where minding emissions permits, efficiency and regulations nearly forces them to run in a state that is at odds with what would be the easiest and most efficient operation and would provide them with the most reliability and best asset lifetime,” says Neil Widmer, senior business development manager with Emerson (Shakopee, Minn.; www.emerson.com). “This forces them into a very narrow operating range.”
While oxides of nitrogen (NOx) emissions have been the major pollutant to fret over, the trend toward fuel efficiency and decarbonization threatens to make this delicate combustion balance even more precarious. “NOx emissions are now back on the table as an ongoing challenge because there are new rules in place that require NOx reductions for a large number of heaters and fired equipment,” notes Matthew Martin, chief R&D scientist with XRG Technologies (Tulsa, Okla.; www.xrgtechnologies.com). “CO2 is a new challenge due to the focus on decarbonization because unless you’re burning ammonia or hydrogen, any combustion process makes CO2.”
Chuck Baukal, director of the Koch Engineered Solutions Institute (Tulsa, Okla.; www.kochengineeredsolutions.com) agrees that this is a developing trend to watch: “Pollution emissions are always an issue for the chemical processing industry, but one of the newest challenges is a great deal of attention on CO2 emissions. So now folks are considering changing their fuels to something like hydrogen or ammonia, which don’t produce CO2 emissions.”
Mark Hannum, manager of Innovation and Research and Development with Fives North American Combustion (Cleveland, Ohio; www.fivesgroup.com), adds: “While there are currently not many regulations regarding CO2 emissions in the U.S., many processors are creating their own corporate goals and/or anticipating future regulations and trying to determine what they can do now to ‘future proof’ their businesses and processes in a new application or when installing new equipment. They want to do this without sacrificing any of their other needs regarding safety, reliability and efficiency.”
Achieving emission goals
Combustion-equipment providers are continually improving existing equipment to assist with reaching tighter emission regulations. For example, there are new burner technologies that produce lower NOx emissions and selective catalytic reduction (SCR) equipment can be added to further reduce the pollutant. “Additionally, any efficiency improvement you make to combustion equipment or fired heaters results in less carbon emissions, because burning more efficiently uses less fuel,” notes XRG’s Martin. “Improving efficiency is a quick win when the goal is reducing CO2.”
In addition, he says, many processors can see up to a 20% improvement on the top end in combustion and fuel efficiency by upgrading their fired heaters with technologies that pre-heat combustion air or by revamping the heat-recovery section in the heater. “These methods reduce fuel consumption while allowing more throughput. So, specific to CO2 production, the amount of the pollutant per unit of product goes down,” says Martin.
Although, returning to that delicate balance, using pre-heated combustion air will increase efficiency, therefore reducing CO2 emissions, but the use of pre-heated combustion air along with the use of carbon-based fuels tends to increase NOx emissions.
For this reason, some companies are developing technologies that help processors potentially reduce both NOx and CO2, while still increasing efficiency and allowing flexibility with fuels. “For medium- or low-temperature process heaters, we have equipment that will allow us to have low emissions of NOx and CO2, even when we preheat combustion air,” says Hannum. “Our EcoFornax line is amenable to having air preheat and still providing really low emissions” (Figure 1).
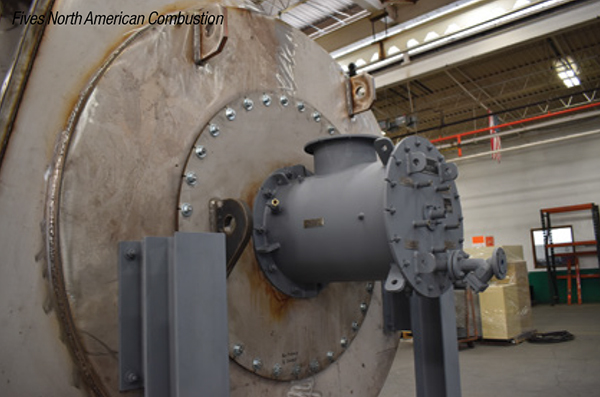
FIGURE 1. EcoFornax LE and LEX (shown here) burners both rely on lean premix. The LE also employs fuel staging and dilute combustion mixing technologies to accomplish emissions and efficiency goals
EcoFornax LE and LEX burners both rely on lean premix, while the LE also employs fuel staging and dilute combustion mixing technologies to accomplish emissions and efficiency goals. “We have put these on a number of process heaters, such as glycol heaters, crude oil heaters, titanium tetrachloride vaporizers and even some field-erected, high-pressure boilers,” says Hannum. “Additionally, they are flexible regarding fuel, so if a processor wanted to switch from natural gas to a fuel with less carbon, this line would have advantages for CO2 reduction, as well.”
XRG offers its Xceed system, which provides a modification to the combustion system for fired heaters, furnaces and boilers that changes the way in which combustion takes place to distributed combustion or disbursed combustion, allowing for increased efficiency, as well as NOx and CO2 reductions by changing the heat transfer inside the system (Figure 2).
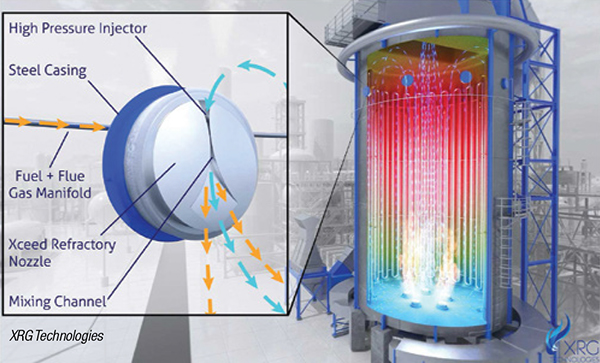
FIGURE 2. XRG’s Xceed system provides a modification to the combustion system for fired heaters, furnaces and boilers that changes the way in which combustion takes place to distributed combustion or disbursed combustion, allowing for NOx and CO2 reductions by changing the heat transfer inside the system
“This is a physical change you make to your existing system,” says Martin. “It involves specialized nozzles that work with the burners in the combustion system you already have. This means the existing burner stays in place, so start-up and shut-down routines remain the same. After the system has begun operation and has reached steady state, the device is turned on and it changes the nature of combustion. It is low temperature and very dilute, so it produces very little NOx and the heat-transfer uniformity of the process is greatly increased. This eliminates hot spots in the fired equipment, so it can operate to a higher capacity without exceeding temperature limits.”
The lower NOx emissions it enables mean that users can recover more heat and increase combustion pre-heat air. “These features make Xceed an enabling technology for CO2 reduction, but it does not itself reduce CO2,” explains Martin. “The system is capable of firing hydrogen or ammonia, so it could be used to replace part of your hydrocarbon fuels with hydrogen or ammonia firing in order to reduce CO2 emissions.”
Zeeco, Inc., (Broken Arrow, Okla.; www.zeeco.com) offers combustion equipment that features ultra-low NOx technologies with the ability to handle high-hydrogen and other fuels, says Rex Isaacs, chief technology officer with the company. “While we have been doing some high-hydrogen applications for 20 to 30 years, we’ve recently made some enhancements to those technologies to make them more maintainable and to make better use of internal fluegas inside of the furnace. The ability to inert the H2, which burns at a higher adiabatic flame than other fuels, delays combustion and also achieves lower NOx. At the same time, it reduces the local temperature inside the burner, which reduces the damage to the metallurgy, increasing reliability of the equipment” (Figure 3).
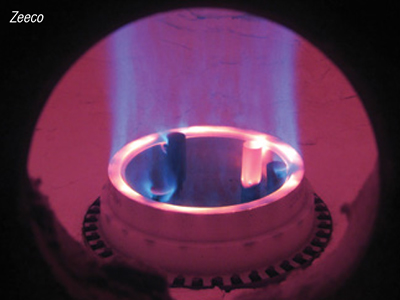
FIGURE 3. Zeeco’s ultra-low NOx technologies can handle high-hydrogen and other fuels. Recent enhancements to the technologies make them more maintainable and make better use of internal fluegas inside of the furnace
Koch Engineered Solutions also offers a wall burner for ethylene applications that enables 100% H2 firing, with lower NOx performance compared to traditional ethylene wall burner technology. This also eliminates flashback, which can be an operational concern and cause maintenance issues for customers, says KES’s Baukal.
“We’ve also engineered the Solex Burner, which can achieve single-digit NOx emissions regardless of the fuel composition and independent of furnace temperature,” explains Ryan Morgan, vice president of OnPoint, a Koch Engineered Solutions company. “The burner is designed with two significant combustion zones to achieve these emissions levels from start up to full capacity with minimal CO emissions. In addition, the burner’s compact flame lengths solve many issues ultra-low NOx burner technologies face in today’s market.”
Preparing for CO2 reduction
While it may not yet be feasible to switch to carbon-free fuels due to the capital expense of replacing or retrofitting an existing combustion system for unknown emissions goals, combustion experts say there are steps you can take to figure out where you currently are and what you need to do to reach corporate decarbonization goals and future government regulations. Fortunately, these same steps also help optimize the current combustion process.
“We are having a very ‘wild, wild west’ moment regarding CO2 emissions,” says Dale Smith, global growth leader, Connected Combustion Services, with Honeywell Thermal Solutions (Houston; www.honeywell.com). “Many companies are voluntarily making sustainability part of their corporate goals. We also know some regulations are coming and that California has already pushed some very aggressive emissions targets out there.
“What I suggest is taking a deep breath and collecting data on where you currently stand,” Smith continues. “Figure out your baselines: what are your burners doing, what you are emitting, how much fuel are you using, how are you actually performing? Once you have your baselines, you can determine where you have gaps and where you can improve and from there you can create a roadmap for the future and whether that requires investments or not.”
Todd Ellerton, director, Global Product Marketing, with Honeywell Thermal Solutions, agrees. “We have hardware and control devices that are capable of low NOx emissions and helping to improve efficiency, so if you are already taking advantage of these low-emission burners and they are performing well, adding something like Thermal IQ or remote monitoring software that is recording, archiving and analyzing your system can provide real-time visibility into the thermal performance of your combustion and actionable intelligence. It becomes an enabler for reliability, safety and emissions control and provides early warnings for predictive actions. If you can predict, you can be more efficient and effective now and see where you need to go in the future. That’s the power of data. It optimizes not only how we use our thermal equipment, but how we use our money and our energy and provides a roadmap for the path we will need to take in the future” (Figure 4).
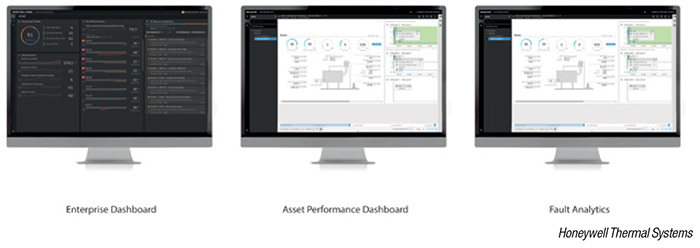
FIGURE 4. Thermal IQ remote monitoring software records, archives and analyzes thermal systems to provide real-time visibility into the thermal performance of combustion and actionable intelligence
Optimizing combustion systems
The bonus of monitoring combustion to find a path toward the future is that it also helps processors optimize their current combustion process, which aids in achieving that elusive balance of efficiency, reliability and emissions control, say the experts.
“Today we strive to operate at better efficiency. However, with different staging techniques for low-NOx burners and because today’s combustion tends to run leaner in excess air, which limits both NOx and CO2 emissions, but raises potential for CO emissions or unsafe fuel-rich conditions, it’s very important to make sure combustion systems are running properly maintenance- and safety-wise, but also to ensure the proper air-to-fuel ratio,” explains Emerson’s Widmer.
He says in-situ oxygen probes, such as the zirconium-based Rosemount 6888 In-Situ Oxygen Transmitter provide a continuous, accurate measurement of the oxygen remaining in fluegases coming from any combustion process (Figure 5). Accurate measurements of furnace exhaust excess oxygen are directly related to and critical for maintaining proper air-to-fuel ratio, resulting in reduced energy costs, increased safety and lower emissions.
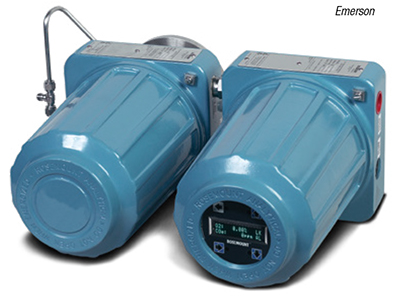
FIGURE 5. Emerson’s OCX8800 Combustion Fluegas Transmitter provides a continuous, accurate measurement of O2 and combustibles remaining in fluegases to permit a higher level of optimization
Additionally, the OCX8800 Combustion Fluegas Transmitter provides a continuous, accurate measurement of oxygen and combustibles remaining in fluegases. This close-coupled extractive analyzer permits a higher level of optimization. “It’s important to measure and monitor both oxygen and combustibles and to do so in a way that allows you to make changes in the controls so that you have some wiggle room in the setpoint of the oxygen,” Widmer says.
This is helpful, he continues, because most trim controllers are very good at maintaining the oxygen level, but not at optimizing it. “Some days you might have very good fuel sources or combustion conditions so you could run oxygen at 1% without any combustibles or CO emissions breakthrough, but other days, conditions might not be as optimal. This type of monitoring with the ability to manually make changes allows you to optimize for the combustion conditions that day,” says Widmer.
Additionally, combustion providers may offer advanced analytics to produce solutions that can help processors drive increased throughput, improved efficiency and reduced emissions. KES’s Morgan says OnPoint offers one such solution called EMBER that uses data from the plant to help optimize process heating operations (Figure 6). EMBER uses data from existing instrumentation and links those data to proprietary calculations, which are hosted in the cloud. That information is used to provide operators with recommendations on how to adjust their combustion equipment to be more efficient, increase throughput and reduce emissions.
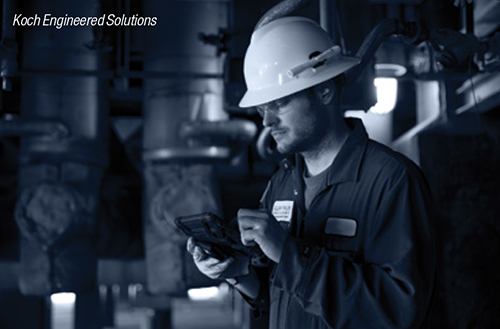
FIGURE 6. OnPoint’s EMBER solution uses data from existing instrumentation and links those data to proprietary calculations to provide operators with recommendations on how to adjust their combustion equipment to be more efficient, increase throughput and reduce emissions
“Depending on the company’s priorities, EMBER can help them manage those goals while continually benchmarking against the KPIs [key performance indicators] they monitor across the process unit,” explains Morgan. “For example, you can track energy intensity while also keeping track of the amount of emissions when trying to maximize throughput. Our solution will produce the recommendations to align those objectives and help operators meet those with the changing operating conditions they face every day.”
And, finally, a burner management system (BMS) is essential to providing optimized and safe performance, notes Joe Medeski, Technical Sales Engineer with Profire Energy (Lindon, Utah; www.profireenergy.com). “The ability to have deeper visibility into the combustion operation and receive actionable insights and make informed decisions is essential to optimizing the balance between safety, efficiency and emissions,” he says. “You want a BMS, such as the Profire 3100 burner management system, that sends an alert when you are close to setpoints so you can take these alarms and notifications into consideration and make any changes needed to keep things from going astray. And, having pre-determined setpoints is also helpful to ensure that optimized operating conditions are repeatable in the same exact manner over a long period of time.”
–Joy Le Pree