Combining new and improved high-performance column internals and a whole-system view provides a comprehensive solution with more benefits
Today’s economic and environmental pressures have chemical processors looking into projects that will help them achieve more throughput from existing columns while also reducing energy use. New high-performance trays and packings can certainly help increase capacity and efficiency of the tower. However, it is a holistic approach to the system and all the internals that yields the greatest benefits.
“Processors are always trying to maximize utilization of their assets, meaning they want to get maximum throughput while maintaining or improving product quality and also being cognizant of their carbon footprint, making energy utilization of the column very important,” says Izak Nieuwoudt, chief technology advisor with Koch Engineered Solutions (Wichita, Kan.; www.kochind.com). “It may seem like looking for the Holy Grail, but it is possible to achieve.”
For this reason, continues Nieuwoudt, there is a constant drive to improve column internals, leading to some significant improvements in trays and packings, but also to other column internals, as well. “For instance, a high-performance packing might yield even better results if it is paired with improved liquid distributors,” he says.
Babak Rafienia, mass-transfer technology manager with Amacs (Houston; www.amacs.com) asserts: “Looking at a tray or packing alone isn’t the only way to find better throughput and efficiency. We have seen many applications that need higher throughput and, while replacing conventional trays and packings with high-performance components can help, better results are always achieved when you look at the complete system, Often, we find other considerations, like inlet piping or feed arrangement, can affect the performance of the tower, so it should be looked at as a system to provide a comprehensive solution with a holistic approach.”
High-performing trays/packings
If a tower is underperforming due to the use of conventional trays and packings or if a processor wants to improve capacity or efficiency of existing equipment, a move to high-performance trays and packings can indeed enhance performance.
“In the recent economy, we have seen a lot of projects put on hold due to capital, logistical and material issues, and processors are trying to get more capacity and higher efficiencies from existing columns,” says Moize Turkey, technology director with Amacs. “In these cases, high-performance internals can boost the performance.”
For instance, the most recent generation of Amacs’ Superblend ASB high performance random packing (Figure 1) provides superior performance when compared to previous packing generations in terms of both capacity and efficiency. Likewise, SEMV mini-valve trays are high-performance internals that can improve both capacity and efficiency by breaking vapor jets and providing better vapor-liquid contact, says Rafienia.
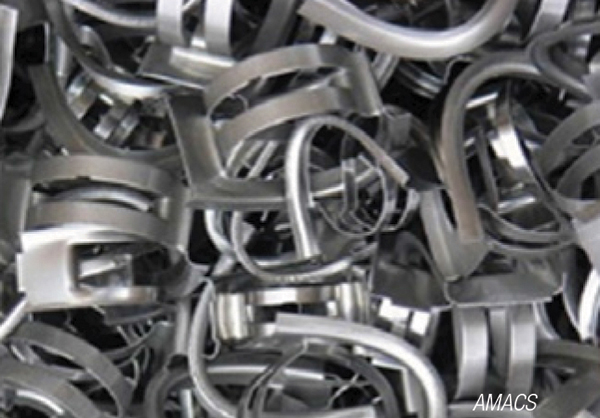
FIGURE 1. Amacs’ fourth-generation high-performance Superblend ABS packing is a combination of various packing sizes, which provides the efficiency of the smaller and the capacity of the larger packing to provide enhanced benefits
Koch’s Nieuwoudt adds that the drive to increase column performance has led to improvements in trays and packings that allow increases to both capacity and efficiency in existing columns. For example, the company’s new Flexipro valve trays offer improved capacity and efficiency, enhanced push and sweeping of the tray deck, which leads to improved fouling resistance and higher turndown ratio with no increase in pressure drop. This situation opens opportunities for revamps and new vessels. The valve trays extend the operating range of fixed valves to levels close to those of movable valves, while maintaining the performance and reliability of fixed valves.
Mark Pilling, manager of technology with Sulzer Chemtech USA (Tulsa, Okla.; www.sulzer.com), agrees that newer technologies can help achieve both capacity and efficiency improvements. “Our UFM valve trays offer a robust design that works over a variety of operating conditions and consistently provides high efficiency. They were designed using computational fluid dynamics (CFD) to ensure ideal mixing between the vapor and liquid on the tray deck to maximize efficiency while simultaneously increasing capacity,” he says (Figure 2).
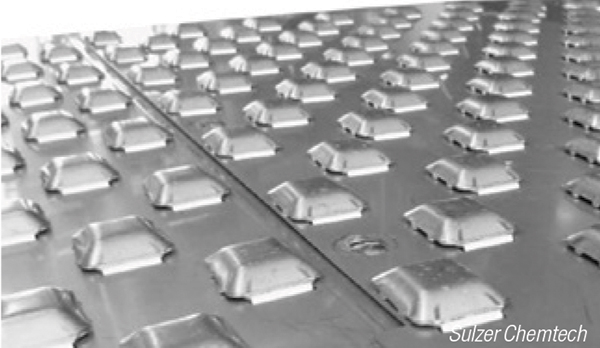
FIGURE 2. Sulzer’s UFM valve trays were designed using computational fluid dynamics to ensure mixing between the vapor and liquid on the tray deck in order to maximize efficiency while simultaneously increasing capacity
Taking a holistic approach
Often, the problem with underperforming columns is that existing towers are being pushed too far, which may necessitate a revamp of more than just trays and packings, says Andreas Danninger, head of sales engineering with Raschig GmbH (Ludwigshafen, Germany; www.raschig.com). “If the tower was designed and built for certain operating conditions that have since been gradually changed, the tower may not perform well, because the internals are not suitable for the current operating conditions,” he says.
“The problems can be manifold,” he continues. “From liquid distributors not being able to handle increased liquid loads to the gas distribution setup not being suitable for changed gas-feed flows, to random and structured packings operating close to flooding conditions to mass transfer trays not being able to handle current operating conditions. Addressing these issues not only requires modern high-performance equipment, but also a sophisticated engineering approach.”
Danninger says the first option that comes to mind is replacing conventional packing types with a modern, high-performance random packing, such as the Raschig Super-Ring PLUS, which provides increased throughput capacity, efficiency, pressure drop and fouling resistance (Figure 3). “But it is not only the packing that affects column performance. If internals like gas and liquid distributors are not suitable for the actual operating conditions, then the packing can’t reach its full potential,” he says. “A redesign of the internals, optimized for the actual process conditions, can significantly enhance packing performance.”
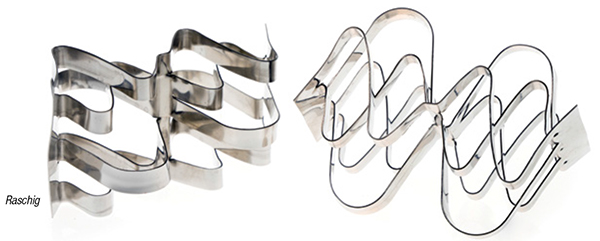
FIGURE 3. The Raschig Super-Ring PLUS provides increased throughput capacity, efficiency, pressure drop and fouling resistance
The same, he says, applies to trays where replacement with a high-capacity tray can enhance throughput capacity. For example, the Raschig R-MV provides higher capacity and lower pressure drop per theoretical stage compared to conventional valve trays due to the unique crowned head of the valve, which promotes improved lateral vapor release, reducing froth height and entrainment and increases hydraulic capacity. “However, a careful redesign of the existing trays with optimizations to the downcomer sections of the active panes for the actual operating conditions can further enhance performance and operability of the tower.”
Similarly, Christian Geipel, managing director with RVT Process Equipment GmbH (RVT; Steinwiesen, Germany; www.rvtpe.com), says that there is a growing need for tailor-made solutions in revamps of existing plants that need modifications to fulfill new demands or achieve longer, more predictable run times in fouling applications, higher capacities and lower pressure drop, wider operating ranges for more flexibility or better energy efficiencies. These can be achieved by combining high-performance trays or packings with other modern internals.
“In terms of energy efficiency, which for mass-transfer equipment mainly corresponds to pressure drop, a revamp from trays or random packings to structured packings is often a solution,” says Geipel. RVT has developed a novel high-capacity structured packing, the SP-Line, which offers modified channel geometry to provide low pressure drops and higher capacity (Figure 4). “However, especially for very low liquid loads, these packings can be combined with other internals such as modern liquid distributors. An improved spray nozzle distributor that combines spray nozzles with splash plates was developed and has been successfully used in refinery vacuum columns where it reduces entrainment and fouling in the packing sections above the distributor without sacrificing liquid distribution quality to the packing section below.”
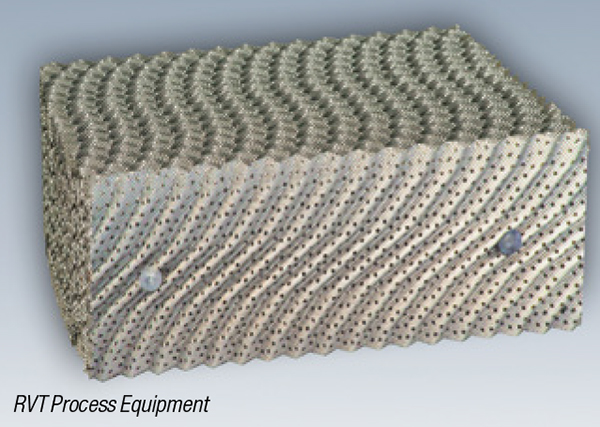
FIGURE 4. RVT has developed a novel highcapacity structured packing, the SP-Line, which offers modified channel geometry to provide low pressure drops and higher capacity
Brad Fleming, manager of Sulzer GTC’s proprietary equipment technology group (Houston; www.gtctech.com), says looking at the system holistically can provide benefits outside the column, as well. “High-performance internals can be tailored to achieve many process objectives,” he says. “For instance, in some processes, reducing pressure drop through the column can have benefits on downstream units. If the overhead gas leaving a main fractionator is going to a compression stage, by reducing pressure drop of the fractionator, you can increase the suction pressure to the compressor and that reduces the power requirement of the compressors or increases its throughput capacity. You can use the characteristics of the column to yield collateral benefits to other pieces of equipment.”
Fleming continues: “Most processors realize that you can replace standard valve trays and get a 20 to 30% increase in throughput, but if you really understand the process, you can use the benefits to optimize further. This means you can use the same number of trays in a column and achieve better product purity, while at the same time, those improvements in efficiency can be translated into energy reductions because you don’t have to drive the column as hard, so the real benefits come from how you use the improvements in equipment technology to drive a desired, optimized result throughout the process.”
Rainald Pabst, sales product manager for columns and internals with DeDietrich Process Systems GmbH (Mainz, Germany; www.dedietrich.com), agrees that overall optimization comes from considering the process as a whole. “No two columns are alike. In each individual case it is important to analyze the situation precisely to determine the optimum solution for the separation process and the column.”
He points to a revamp of a nitric acid concentration column using modern DeDietrich internals. “The column was originally equipped with cast iron internals, which caused many problems during operation of the plant, including limited load range, permanent blocking of the distributor holes due to breakage of the random packing and risk of fracture due to thermal stress. As a result, the required throughput of the column could not be achieved so the plant produced about 20% less than originally planned and the column required intensive maintenance,” he says.
DeDietrich remedied the situation by installing new equipment. In addition to its Durapack structured mass transfer packing (Figure 5), which offers a higher number of separation stages, better wettability and mechanical stability and glass grids with a larger free cross-area, Coretray distribution trays and SiC-channel distributors were installed. “The Coretray distributor trays combine the functions of collection, distribution and support in a single component,” he says. “The possible load range is designed individually and is enormous. Thus, lower loads can be handled without loss of distribution quality. Hydraulic overloads up to 280% can be handled without any problem, which is helpful for heavily polluting or foaming media. Further, the SiC-channel distributor is characterized by very good distribution quality.
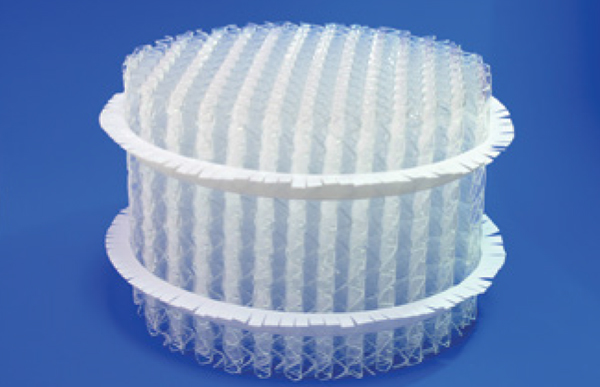
FIGURE 5. DeDietrich’s Durapack structured masstransfer packing offers a higher number of separation stages, better wettability and mechanical stability and glass grids with a larger free cross-area
“These improvements allowed the processor to increase performance up to 120% of the original required capacity,” he says.
To enable examining systems as a whole, Koch recently launched a software package, TowerView, that performs real-time calculations of the performance and health of equipment inside distillation or absorption towers. “The software takes advantage of the ability to digitalize separation equipment and provides real-time feedback on the values that cannot be measured,” says Nieuwoudt. “Often processors run a distillation column and measure pressure drop, temperature and composition of streams using probes in the column, but these values can’t provide information about issues such as whether certain parts of the trays are close to flooding.”
“Our calculation methodology provides users with a real-time view of what things look like inside the column to give a proactive view of where the tower is relative to its limitations,” he says.
The software can be used online in real time to provide alerts when there are potential problems, or offline to run what-if scenarios that can be used to enhance performance of the column before making physical changes.
According to the experts, looking at problems or enhancing performance of the column should change from focusing on a single point or component and move toward looking at it as a whole package. Often tweaking and finding small optimizations within the entire system can help operators improve the throughput or performance, which isn’t always specific to just one internal. A solution-driven strategy that examines the entire picture should be the focus of optimization projects.