Clariant AG (Muttenz, Switzerland) announced that it has renewed its successful partnership with Midrex Technologies, Inc. and will intensify collaboration in direct reduced iron (DRI) technology for steel production. A low-carbon alternative to conventional coal-based ironmaking, natural gas-based DRI converts natural gas with recycled CO2 and H2O to generate reducing gas for the production process. The technology combines Midrex Reformers with Clariant-manufactured REFORMEX Catalysts, which offer superior activity and stability to increase productivity, reduce energy consumption, and minimize carbon emissions. Midrex DRI technology avoids around one ton of CO2 per ton of crude steel.
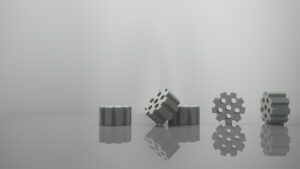
Clariant-manufactured REFORMEX Catalysts are combined with Midrex stoichiometric reformers to enhance DRI (Source: Clariant)
Georg Anfang, Vice President Syngas & Fuels at Clariant Catalysts, commented, “Together with Midrex, we have agreed to intensify our focus on natural gas-based DRI, as it is a critical bridge technology that will greatly support the transition of the steel industry toward net-zero production. While we collaborate on expanding and enhancing our current solution, we are also preparing and innovating for the future.”
Sean Boyle, VP-Commercial at Midrex, stated, “The Midrex Process is one of the most widely used technologies for producing all forms of DRI products, and it is well-known for its reliability and continuous operation. Clariant’s catalysts are tailor-made for our process to offer optimized and consistent performance. Our joint solution ensures the lowest CO2 emissions of any steelmaking route today.”
Based in Charlotte, North Carolina, USA, Midrex is one of the world leaders in direct reduction ironmaking technology and aftermarket solutions. Midrex has designed, built, and serviced direct reduced iron (DRI) plants for 50-plus years. Plants based on Midrex Process technology produce a substantial part of the world’s low CO2 DRI. Midrex Plants can be configured to operate on natural gas with hydrogen addition (Midrex Flex), and 100% hydrogen (Midrex H2™) and can process a wide range of iron oxide pellets and lump ores.
Clariant manufactured REFORMEX Catalysts, which have been used successfully for the Midrex Process since the 1980s, demonstrating their exceptional performance and longevity. Due to the catalysts’ outstanding activity and superior heat transfer properties, they enable highly productive and cost-efficient syngas production. Furthermore, their extreme mechanical stability and excellent coking resistance ensure a long production lifetime. REFORMEX Catalysts are successfully operated at around 50 major commercial steel production plants around the globe.