Selecting footwear for plant personnel is not a “one size fits all” situation — various factors must be considered to ensure the best shoe for a specific application
Chemical manufacturing plants generally have questions about their overall safety protection program, of which footwear is a foundation (Figure 1). Employers and workers want to avoid injuries while on the job, but standing for long periods of time can lead to tired, accident-prone feet. So which product features, especially when working with chemicals, should plants take into consideration when it comes to shoes?
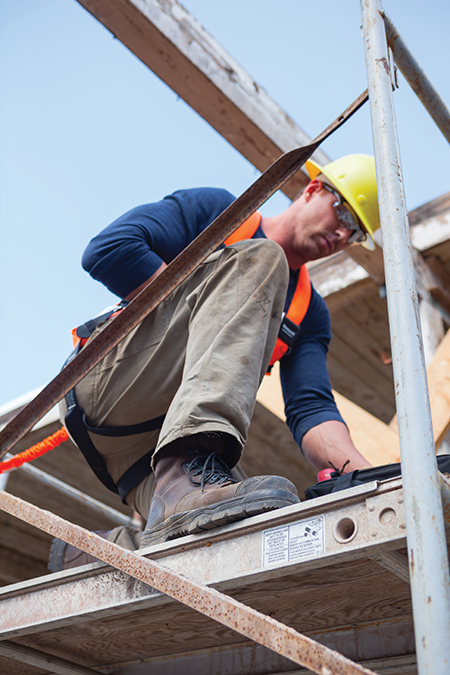
FIGURE 1. A variety of product features are available when selecting industrial footwear, and special consideration must be taken to choose the best shoe for a specific chemical-handling job
Chemical compatibility
The chemical compounds used in footwear have basic affinities or lack of affinities for certain chemicals, based on how they are made. Chemicals similar to the compound from which the footwear is constructed make that compound break down faster. For example, rubber, a common material used in footwear, is petroleum-based. Therefore, any substance that has oily content, such as gasoline or cutting oils, is going to break down the rubber faster than other compounds. Simply put, rubber is typically made from petroleum, so oily materials will more quickly break down the rubber compound. This is important to take into consideration for workers in the food-processing industry where oils (in the form of vegetable or animal fat) are prevalent. Workers in food-processing facilities should look for a polyvinylchloride (PVC) boot, since PVC will withstand those chemicals in their work environment much better.
Conversely, industries that work with materials such as alcohol and ammonia should choose a rubber boot, because these chemicals break down PVC comparatively quickly. Acids and bases are so varied in their impact on boot materials that there can be no single rule, as organic and mineral acids have wide-ranging effects. These chemicals need to be evaluated on a case-by-case basis to determine which footwear material is the proper choice.
Features to consider holistically
When looking to purchase footwear for the job, you cannot simply look at the upper material. It is important to look at the overall boot and make evaluations based on the specific job at hand. Managers must look at physical durability, chemical durability, slip resistance and comfort.
Finding the right shoe involves the right fit and protection for specific personnel duties, and is not based solely on the wearer’s occupation. Someone who is on their feet walking all day will require shoes that offer comfort and protection features related to being on one’s feet for long periods of time. Others may need more slip resistance. Therefore, it is important to evaluate the overall need and determine what is most important. Weighing durability against the chemical wear and tear based on your job is one part of the decision around which type of footwear is best. It is important to think of the different work environments that personnel will encounter and determine which features are most important.
Slip resistance is key
Slip resistance or traction is a feature that is very important to consider. Selecting appropriate slip-resistant footwear can be challenging, because there is a lot of industry frustration and confusion around slip ratings and what is best. Many products will say they are slip-resistant or call out their slip resistance as “fair,” “good,” or use another subjective term. If plants are looking for footwear to be compliant with a Slip Hazard Assessment Plan, it is important to be able to review the manufacturer’s actual slip scores in the standardized tests. The current standard for slip-resistant testing has been developed by SATRA Technology (Kettering, U.K.; www.satra.com), which is a whole-shoe test. Older tests were designed to test the floor, not the shoe, and are now considered obsolete.
Slip-resistance certifications are typically divided into three categories (Table 1): SRA, SRB and SRC. It is recommended to select a shoe with SRA qualification for most wearing occasions, and an SRC slip-rated outsole when looking for best-in-class slip performance. If an outsole has a passing score on the Slip Resistance A test — soapy water on quarry tile — it can be labeled SRA. If an outsole has a passing score on the Slip Resistance B test — glycerol on stainless steel — it can be labeled SRB. If it passes both tests, it can be labeled as SRC.
Environmental testing
It is critical to test boots in the environment that they are intended to be worn (Figure 2). Sometimes it is not the first contaminant that is the problem. The contaminant itself could be relatively easy to work with but the cleaning material for the environment could pose problems. Bleach is often used as a cleaning agent, and bleach can be damaging to rubber, so a suggestion would be a dipped-neoprene or PVC product in that case. That is why it is always best to make sure products are tested on site to monitor potential cross-contamination. A good example of this is workers at hydraulic fracturing (fracking) sites. Fracking fluids are often proprietary, so footwear providers do not know exactly what chemical compounds are contained within them. Fracking fluids are highly volatile, and counteracting solutions in such sites need to be tested with the footwear to ensure safety.
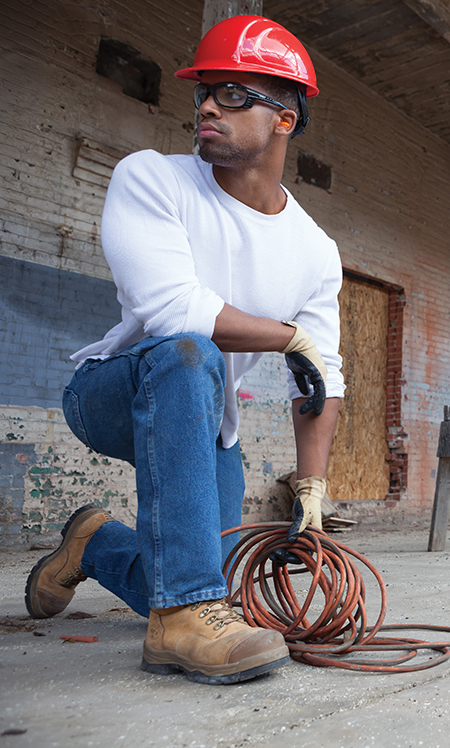
FIGURE 2. A best practice in footwear selection is to test the boot in the specific environment where it will be used
Inspection and cleaning
Do you have an inspection or safety survey in place to examine the boots to make sure they are being replaced at the right rate for the wear and tear based on the job? This is really important to ensure the safety of workers. The last and best thing to do with any boot is to make sure to wash them with clean, clear water after any working cycle. Any chemical that sits on the boot for some time will wear it down. The best cleaning agent is simply water.
New innovations on the horizon
As footwear design evolves, there are some innovations quickly coming down the pike that will greatly increase comfort and durability. The first is climate control. What we are seeing is that workers are becoming more sophisticated in their understanding of how to protect themselves from the cold. In the past, people have looked for temperature ratings, thinking that more protection is always best. Instead, the industry is seeing a trend to look for climate control in the boots rather than simple insulation. High insulation values that cause one to perspire create a worse condition than the cold itself, as perspiration condenses, drawing even more heat out of the body, especially when the person goes from an active to inactive state.
The second innovation is ergonomic design. Footwear design and production often err on the side of simplifying production, as the boots are mass-produced versus custom-made. The goal of the near future of boot making will be to deliver a product that has a customized fit with no break-in time.
As worker health and comfort become a greater focus for maintaining productivity, footwear needs to be a main part of the solution. Remember to look first at the overall job and working environment to determine what features (physical durability, chemical durability, slip resistance and comfort) are most important. Next, make sure that there is a system in place to properly test footwear, as well as inspect when the boots need to be replaced. Lastly, cleaning boots on a regular basis with clean, clear water will extend their lifespan and durability against exposure to chemicals.
Edited by Mary Page Bailey
Author
Xavier Kawula currently serves as the liaison for innovation at Honeywell Industrial Footwear (Westwood, Ma.; Website: safety.honeywell.com; Phone: (800) 430-5490), as well as product manager for Honeywell’s Work and Hunt offerings. He has more than 20 years of footwear experience. Prior to working at Honeywell, he was a product manager at Timberland Boot Company and Timberland PRO.