With an eye toward a circular economy, technology developers are advancing a host of new approaches to chemical recycling of post-use commodity plastics
Plastics are indispensable parts of almost every sector of the economy, with wide-ranging economic, environmental and convenience benefits in their use stage. But increasingly, the sheer volume of plastics produced (estimated at well over 300 million metric tons annually) presents environmental risks if the material is not captured, and represents a waste of resources if the material is disposed of in landfills. Currently, only a small fraction of commodity plastics are recycled globally (some estimates peg the number at 14%), while the majority end up in landfills, incinerators or in the environment, particularly the ocean.
The past two years have seen an acceleration and expansion of efforts aimed at addressing the issues associated with waste plastic. Stakeholders from several industries and from along the plastic value chain are involved in a host of plastic-waste initiatives (see below, “Coordinated Efforts in Plastics Recycling”). One aspect of the overall effort is to foster the idea that plastic waste can be a resource and that even single-use plastics have value after they are discarded.
Jeff Wooster, global sustainability director with Dow Packaging and Specialty Plastics (Midland, Mich.; www.dow.com), says “We are operating in a resource-constrained world, so we need to keep driving toward a circular economy. If plastics are landfilled, we lose their value. We put energy and resources into making those materials, and that is lost if we landfill the waste plastic. Recycling and energy recovery can retain the value of those materials for society.”
The majority of plastic-recycling processes today are mechanical, where waste thermoplastic material from end-use products are melted and used as a component of another manufactured product. While improvements continue to be made in this area (for example, in spectral identification and sorting of plastic items), it is clear that mechanical recycling processes alone are not sufficient to handle the volume of plastic recycling that is required to shift society toward a circular economy with regard to plastic.
“Making meaningful progress on the problems we are facing related to plastic waste will take a truly global effort — it needs to be ‘all hands on deck,’” says John Thayer, head of polyethylene business at NOVA Chemicals (Calgary, Canada, www.novachem.com).
The limitations of existing recycling processes and the push toward circular economy ideals has driven development of chemical recycling processes — those in which polymers are taken back to their monomers. This class of processes need to be developed and deployed at scale to complement existing mechanical recycling efforts. “Plastics are too valuable of a resource to end up as litter or trash,” NOVA’s Thayer comments. “One hundred percent of plastics should be reused, recycled or recovered and regenerated. We believe that chemical monomer recovery is the best long-term solution, where end-of-life plastics become feedstock that is chemically indistinguishable from fossil-fuel-sourced monomer.”
Presented here are several advancements in chemical recycling processes, including several technologies that have recently been, or are soon to be, scaled up.
Coordinated Efforts in Plastics Recycling
The following are short descriptions of some selected consortia, alliances and collaborations that are aimed at various pieces of the plastics recycling movement.
Alliance to End Plastic Waste (AEPW; www.endplasticwaste.org). Launched in January 2019, AEPW is an alliance of nearly 30 global member companies from across the plastics and consumer goods value chain. The alliance has committed over $1.0 billion, with the goal of investing $1.5 billion over the next five years to help end plastic waste in the environment. The Alliance will develop and bring to scale solutions that will minimize and manage plastic waste and promote solutions for used plastics by helping to enable a circular economy, according to AEPW. Member companies include BASF, Braskem, Chevron Phillips Chemicals, Clariant, Covestro, Dow Chemical, LyondellBasell, NOVA Chemicals, Sasol, Total, Veolia and others.
Materials Recovery for the Future (MRFF; www.materialsrecoveryforthefuture.com). MRFF was formed by the non-profit arm of the American Chemistry Council (ACC) to foster the addition of flexible plastic packaging to the recycling stream. MRFF is trying to install sorters that can separate flexible packaging from recycled streams, so that consumers can include flexible packaging into their regular recycling bins. Members include the Dow Chemical Co., PepsiCo, SC Johnson, Nestle, the Association of Plastics Recyclers, Target Stores and others.
CEFLEX (www.ceflex.eu) CEFLEX is the collaborative project of a European consortium of companies representing the entire value chain of flexible packaging and continues the work of Project REFLEX and Project FIACE.
Recycle Across America (RAA; www.recycleacrossamerica.org). RAA created the world’s first and only society-wide standardized labeling system for recycling bins to make it easier for people to participate in recycling programs. The standardized labels are proven to help increase recycling levels and significantly decrease the costly garbage thrown in recycling bins, RAA says.
Project STOP (Stop Ocean Plastics; www.systemiq.earth) is a frontline initiative to prevent ocean plastic leakage in Southeast Asia. Its partners include Borealis, SYSTEMIQ, the Government of Norway, NOVA Chemicals, Borouge and Veolia and Nestlé.
PET upcycling
A sizeable amount of activity in the recycling field surrounds polyethylene terephthalate (PET), a widely used polyester that appears in many packaging and clothing applications, among others. Among the major commodity plastics, PET has the highest recycle rates (near 30%), although much of the PET waste that is recycled goes into lower-value materials.
“Some effective recycling processes exist for PET, but they require uniform streams of material, and generally result in products that are not likely to be recycled themselves,” says Gihan Hewage, Lux Research Inc. (Boston, Mass.; www.luxresearchinc.com) analyst and co-author of a forthcoming report on waste products, entitled “Waste Conversion Innovations to Enable a Circular Economy.” “There are now a number of companies developing technology for PET waste that allows a more circular path for PET, and that can result in products from recycled PET waste that are indistinguishable from petroleum-derived PET.”
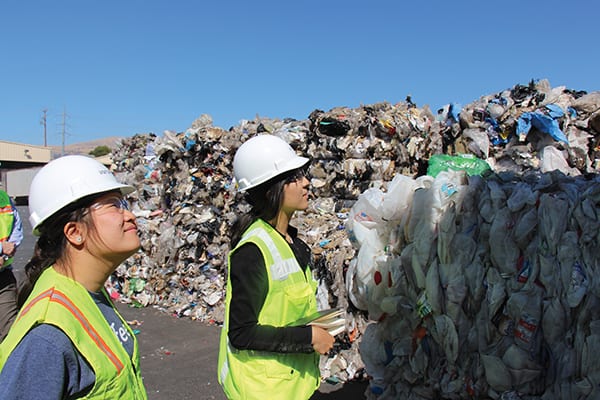
Figure 1. Several companies are developing chemical recycling approaches to handle low-value mixed plastics. Among them is BioCellection, whose founders are shown here inspecting mixed plastic waste that could be a feedstock for its process to make chemical intermediates from such plastic
Photo courtesy of BioCellection
Among this group of companies is Loop Industries (Montreal, Canada; www.loopindustries.com). Loop has developed a technology that uses a catalytic process to convert low- or no-value waste PET and polyester fiber (plastic bottles and packaging, carpet and polyester textile of any color, transparency or condition and even ocean plastics that have been degraded by the sun and salt) into virgin-quality monoethylene glycol (MEG) and dimethyl terephthalate (DMT) for the manufacture of virgin-grade Loop-branded PET resin and polyester fiber.
In Loop’s process, waste PET, which the company refers to as “feedstock,” is introduced into a vessel at ambient temperature and pressure along with Loop’s proprietary and patented catalyst and a carrier agent. The catalyst selects only the bonds between the polyester monomers, so it depolymerizes PET only, and leaves other plastics, such as polypropylene (PP) and high-density polyethylene (HDPE) intact, explains Nelson Switzer, Loop’s chief growth officer. This means that Loop’s technology can use low-value mixed streams of plastic and still yield virgin quality monomers. Because of this, the monomers can be separated easily from the process to produce food-grade quality Loop-branded PET. “Essentially, Loop’s monomers become a drop-in substitute for petroleum-derived monomers,” Switzer says.
Loop has established an industrial-scale pilot plant near Montreal, and is currently developing a full-scale commercial plant through a 50/50 joint venture with Indorama Ventures. Loop and Indorama are retrofitting an existing Indorama plant with the Loop technology to make Loop-branded PET resin. The commercial plant is expected to be operational in 2020. Loop also has an alliance with thyssenkrupp Indusrial Solutions to integrate the companies’ technologies.
Switzer points out that there are many advantages of Loop’s technology compared to conventional and mechanically recycled PET processes: notably the vast number of sources of PET and polyester fiber waste from up and down the PET value chain that can be used to produce Loop-branded PET. “We can use no-value or low-value PET waste that no one else wants,” he says. While the company won’t comment on costs, it says customers have agreed to its pricing.
Meanwhile, Carbios (Clermont-Limagne, France; www.carbios.fr) is taking a biological approach to depolymerizing PET. The company has developed a “biorecycling,” process, where waste PET bottles and fibers are crushed and ground to powder, then placed in a bioreactor and heated to 65˚C at atmospheric pressure. Specially bioengineered enzymes are added to de-polymerize, in less than 16 hours, the PET into monomers, MEG and PTA (purified terephthalic acid). Carbios has developed a proprietary filtration and purification process to generate high-purity monomers that can be re-polymerized by PET producers into high-quality PET with 100% recycled material.
The enzymes are extracted from naturally occurring bacteria that can break down PET, explains Carbios engineer Benjamin Audebert. “The enzymes have been engineered and optimized by our teams to be highly selective for PET, so only the PET is digested. In this way, the process can handle mixed-plastic streams,” he says. Because PET is broken down selectively, other polymers are alone and can be separated. “The enzyme does the sorting for you,” Audebert comments, “so you can use low-value mixed plastics materials as feedstock.”
The enzyme’s active sites cleave the ester bonds of PET. Carbios generated detailed models of the enzyme and its interaction with the polymer chains. The company will launch construction of a demonstration plant for this biorecycling technology in June 2019. It will be operational by the Q4 2020, Audebert says. Carbios will then license its technology for a commercial-scale facility to be fully operational by 2023. They are enlisting the help of the German division of Technip FMC, which has expertise in PET plants. Infinite recycling of PET is possible, Audebert comments. Carbios is working on enzymes for breaking down other polymers, and is also involved with technology for embedding specialized enzymes into single-use films of bio-based polylactic acid, so the plastic breaks down in an ecofriendly manner just after use.
In Switzerland, Gr3n Recycling (Lugano, Switzerland; www.gr3n-recycling.com) is also taking aim at PET, but instead of biological aids, they are using microwave technology to assist the depolymerization reactions of PET plastic into its constituent monomers. Gr3n’s process uses a saponification reaction with sodium hydroxide in water to break down the polymer. The key innovation is the application of microwaves to the reaction to speed it up. “The microwaves act like a catalyst,” says Mauricio Crippa, CEO of Gr3n. “The microwaves reduce the reaction times from multiple hours down to several minutes. Although the mechanistic details of how the microwaves catalyze the reaction at the molecular level are not clear, the process works on densified polyester fibers and on PET plastic.
The recycled waste is ground up and fed into a flow-through reactor, where the microwaves, generated by a standard magnetron, penetrate the mixture to aid the reaction and formation of MEG and PTA products. The company has built a demonstration-scale reactor and is currently building a demonstration plant in Italy that will process 1,000 ton/yr of PET feedstock. The demonstration plant will be completed at the end of 2019 or early 2020. The company’s vision is to build plants close to cities to reduce the need to transport waste PET feedstock. It is going to partner with a mechanical recycler to handle the waste PET that is not used.
In yet another approach, Ioniqa Technologies (Eindhoven, the Netherlands; www.ioniqa.com) is using an iron-based ionic liquid in a proprietary technology that is able to convert any PET waste, including colored packaging, back into transparent virgin grade material. The technology has successfully passed its pilot stage and is now moving towards testing at an industrial scale.
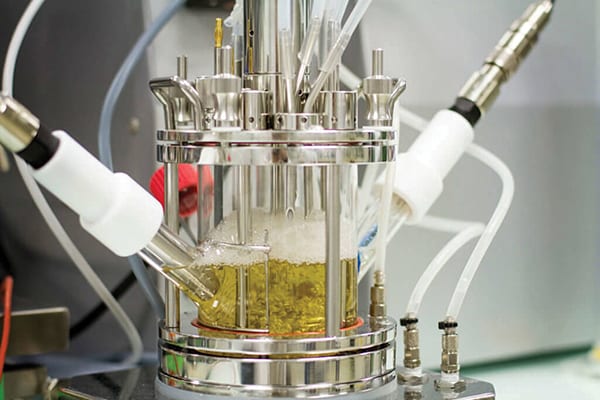
Figure 2. Carbios is developing an enzyme-based process to selectively de-polymerize PET from streams of mixed plastic waste in an effort to obtain high-purity monomers for new PET
Photo courtesy of Carbios
Ioniqa, a spin-off business from the Eindhoven University of Technology, has formed a partnership with Unilever, and the largest global producer of PET resin, Indorama Ventures, to develop the new technology which converts PET waste back into virgin-grade material for use in food packaging. Ioniqa’s Magnetic Smart Process is based on its proprietary Magnetic Fluid Catalyst (an iron-based ionic liquid). The platform technology is also being used in other applications beyond recycling.
In a process that was previously reported in this magazine (Chem. Eng., November 2016, and August 2018,), the BCD Group (Cincinnati, Ohio; www.bcdinternational.com) developed a modified base-catalyzed decomposition process for removing dyes from PET fabrics, and separating cotton from cotton-polyester blend textiles and fabrics is now being applied to bottles made from PET.
Making mixed streams work
One of the most difficult problems in plastics recycling is multi-component plastic packaging films. The use of these layered materials is widespread, and confers desirable functionality to the films in use. Examples are PE/PA, PE/PP, PE/PET. But the layering makes recycling the films after use problematic. A recently commercialized technology from APK AG (Merseburg, Germany; www.apk-ag.de) is aimed directly at this problem. The company’s NewCycling technology allows the recycling of multi-layer flexible films in packaging applications.
“In commonly used mechanical recycling processes, multi-layer films end-up in many cases in incineration or are recycled to re-granulates with a quality just suitable for low-value applications, such as grass pavers or pallets,” says Florian Riedl, director of business development at APK.
APK developed NewCycling as a way to separate the polymers in multilayer films so they can be used in applications normally for virgin-grade polymers. In NewCycling, the polymers are dissolved selectively by specially designed polymer-specific solvents. One component of the multi-layer film is dissolved while the other is left as a solid. Then the two components (solid of one species and liquid of another) are separated using a rotating system. The result of the process are sorted re-granulates (for example, PE and PA) with very high purity. The re-granulates are suitable to use them again in demanding applications, such as flexible packaging, Riedl says, so “we are offering an active contribution to the circular economy and help to achieve the growing recycling targets set by the industry and legislation.”
The APK solvents are removed from the plastic polymer to levels below 1,000 parts per million, Riedl says, and the pure stream of polymer is then sent to an extruder, where it is pelletized for sale to makers of plastic films for packaging. The solvents are recovered for re-use in the process. One initial application will be for non-food-contact plastic pouches for laundry detergent, Riedl notes.
After developing the process at pilot scale for the past three years, APK has built its first commercial-scale production line for making plastic pellets from recycled multilayer films. The plant, located in Merseburg, Germany, began production of pellets last month. The plant is capable of producing 8,000 ton/yr of pellets from post-industrial waste (off-specification film material). APK is planning to build a second commercial plant to produce plastics from post-consumer waste in the form of mixed films fractions from recycling sorting centers.
In another approach aimed at recycling waste plastic that is not currently recycled, BioCellection Inc. (Menlo Park, Calif.; www.biocellection.com) has developed a novel catalytic process that can break down PE into dicarboxylic acids, which can then be used as intermediates to synthesize other chemicals. The proprietary process is designed to work on PE films that are generally not being recycled currently, explains Erik Freer, BioCellection chief technology officer.
The overall process designed by the company effectively recovers and recycles the catalyst, using mild temperatures and pressures to keep costs low. “The raw-materials costs for our process are much lower than existing processes for making dicarboxylic acids,” Freer says, so it is a good way to create a high-value chemical intermediate from waste plastic.
After a bench-scale demonstration, the company built a pre-pilot unit that is an order of magnitude larger than the bench-scale system to validate the effectiveness of the catalyst. They are now designing a commercial pilot plant that integrates all the components of the process and aims to validate the complete process, Freer says. In 2018, the company won a $100,000 award from UCLA and the Anthony and Jeanne Pritzker Foundation for emerging environmental projects.
Products from pyrolysis oil
One approach to addressing the problems associated with recycling mixed-stream plastics is to break down the plastics via thermochemical means, such as pyrolysis (thermal decomposition in the absence of oxygen), then separate them into fractions, similar to the refining of crude oil. The wax/oil mix from plastic can then be fed to steam crackers to be made into olefins for plastic production. A number of companies are operating in this area, including Recycling Technologies Inc. (U.K.), Plastic Energy Ltd. (U.K.) and Recenso GmbH (Germany). The outlets for this material are expanding as the companies are partnering with others who can use the products from the pyrolyzed plastic.
One example of this is BASF SE’s (Ludwigshafen, Germany; www.basf.com) ChemCycling project. In late 2018, BASF announced the first pilot products made from oils derived from the thermochemical decomposition of recycled plastic waste for which no recycling solutions currently exist. Using oils from plastic waste generated by partner Recenso, BASF put the material into its steam cracker at Ludwigshafen to make ethylene and propylene. From these olefins, BASF made plastic packaging for mozzarella cheese, for example.
Another similar arrangement was recently established by Plastic Energy Ltd. (London, U.K.; www.plasticenergy.com), which has developed a process for making a raw material feedstock from mixed plastics known as TACOIL. TACOIL results from the recycling of low-quality, mixed plastic waste otherwise destined for incineration or landfill. The upgraded pyrolysis oil will yield a cracker feedstock with similar characteristics and quality as the fossil-based naphtha feedstock, the company says. The naphtha cracking process yields the same monomers, such as ethylene and propylene, that are used to manufacture low-density polyethylene (LDPE), high-density polyethylene (HDPE) and polypropylene (PP).
A partnership between Plastic Energy and SABIC (Riyadh, Saudi Arabia; www.sabic.com) was recently announced where Plastic Energy is building a facility in Geleen, the Netherlands to make TACOIL from recycled plastics, and SABIC will use the TACOIL to manufacture plastic granulates. At the recent World Economic Forum in Davos, Switzerland, SABIC announced that a line of certified circular polymers made from TACOIL will be used by key SABIC customers Unilever, Vinventions and Walki Group for packaging solutions for a variety of consumer packaging in the food, beverage, personal- and home-care markets. Those products will be introduced into the market this year. The plant in Geleen is anticipated to enter commercial production in 2021.
Supply chain changes
While the processing side continues to advance, others are thinking about how the processes fit into the broader picture. “There are technical solutions available to the problems associated with plastic waste, but in order for them to make a difference, they have to be integrated with innovative supply-chain models,” says Jack Buffington, professor at the University of Denver (Colo.) School of management.
Today’s recycling business models largely aren’t profit-making. “Technologies to process and use recyclate exist, but they need to be further developed against goals around economies of scale and environmental footprint,” says NOVA’s Thayer.
Building new infrastructure for waste handling and chemical processing is needed, and supply-chain changes, including those surrounding waste collection, transport logistics, sorting and development of new markets for recyclate, can help close the gap. “The science needs to connect to the supply-chain side,” says Thayer.
Denver’s Buffington says, “Our central idea is to set up a community-based model in which smaller, regional chemical recycling plants are integrated with local collection systems, such that the recycling facility is not a centralized point, and the plastic waste does not have to be shipped” (shipping wastes some of the value intrinsic to the plastic waste). “The value of the plastic stays in the community and the economic force that it generates stays in the community,” he remarks.
Recycling hurdles
Many research groups, companies and partnerships around the world are active in many aspects of recycling, including improving recyclability of plastic products through upfront design, improving collection programs, developing new applications for plastic recyclates and others.
For any material to be recycled, first it must be collected. Next a process must benefact the material to useable status. And then there must be a market for the material at a price necessary to pay for the first and second step, explains Dave Cornell, technical consultant for the Association of Plastics Recyclers.
Collection of enough consistent material is usually the first and foremost hurdle. There must be a critical mass of material to allow for the economic activity to be self-sustaining, Cornell continues. “For the over 600 different resins used, there are only a limited number for which the critical mass allows for the other steps to be attempted,” he says.
Regarding current barriers to plastics recycling, NOVA’s Thayer says, “Key issues include the lack of curbside collection in the U.S., and the fact that many plastic films are multi-material, effectively rendering them non-recyclable. Also, there is a need to identify more valuable, high-volume end markets for the recyclate. As with all issues related to end-of-life plastics, it will take all of us working together to address these issues, and a range of solutions that best fit for a given geography, population and so on.”
Mechanical recycling approaches are suitable for some applications, including using recycled bottles made from polyethylene terephthalate (PET) to make polyester fibers, but the plastics streams need to be highly uniform because contamination by other types of plastic or by other materials reduces the quality of the resulting recycled plastic. This limits the number of outlets for recycled plastics to lower-value items.
“Recycled plastics produced by mechanical recycling generally do not achieve the same level of quality and purity as virgin plastics, because the properties of the plastics are changed during the use-phase and during re-processing” says BASF.
“The available plastic waste streams differ in quality to such an extent that both mechanical and chemical recycling will have roles to play: mechanical recycling will be used for higher-quality plastic waste streams and chemical recycling will be used for lower-quality plastic waste streams,” says Sabic. The two approaches will complement each other.
Cost-effective chemical recycling approaches would allow the end products to achieve the same quality as virgin-grade plastic material, and would allow the processing of more varied materials, such as mixed streams and multicomponent plastic films, neither of which can be recycled using mechanical approaches.
Projects for flexible plastic packaging (FPP)
To increase plastics recycling, there is a need to improve the collection system for plastics that cannot currently be recycled through mechanical recycling programs. One major category is FPP — films, wraps, bags and pouches — which are not widely recycled today. As it becomes a larger part of the packaging waste stream, the need for scalable recycling collection strategies is critical to its sustainability.
One initiative in this area has been undertaken by Dow and Reynolds. The companies started the Hefty EnergyBag program, a recovery program for consumers to collect their flexible packaging materials like chip bags, candy bar wrappers, plastic straws and utensils, and other hard-to-recycle plastics. Through the program, which complements mechanical recycling programs and uses existing recycling infrastructure, those materials are diverted from landfills and used to make diesel fuel, but we are looking at ways to use those materials in a chemical recycling process to create new packaging.
Local programs exist in Omaha, Nebraska, Boise, Idaho, and Cobb County, Georgia. A new local Hefty EnergyBag program will launch in Lincoln, Neb., later this year.
A related pilot program for FPP comes from Dow Chemical, as a member of MRFF. Dow announced a pilot program for recycling FPP in Berks County, Pa. in mid-2018. The pilot is expected to generate data to help inform municipalities and the recycling industry on the most efficient and economical ways to recycle FPP. This will turn used FPP materials, typically destined for disposal, into a bale that can be sold to a variety of end markets.
Braskem (Sao Paulo, Brazil; www.braskem.com.br) also recently announced new partnerships for the development of chemical recycling, with a focus on transforming post-consumer plastics, such as grocery bags and packaging films for snacks and cookies, into chemical products that can be used by various different value chains. The partnerships will further research technologies that can transform plastics that are more difficult to be recycled mechanically into new chemical products. The research is being conducted in partnership with the Polymer Engineering Laboratory (EngePol) at the Alberto Luiz Coimbra Institute of Graduate Studies and Research in Engineering of the Federal University of Rio de Janeiro, the SENAI Institute for Innovation in Biosynthetics (SENAI CETIQT) and Cetrel, an environmental service company.