Environmental imperatives drive the development of technologies for the chemical recycling of plastic waste, but significant hurdles – including economic viability, collection logistics and feedstock complexity – need to be addressed for chemical recycling to have a larger impact
Plastic waste continues to be a major global environmental issue. While mechanical recycling, where plastic waste is ground up and remelted, remains the most prominent form of plastics recycling, its limitations (material degradation, contamination and performance) prevent it from enabling real plastics circularity. The field of chemical recycling of plastics, which aims to break down polymers into starting materials that are chemically equivalent to petroleum-derived feedstock, is a fast-evolving area that is critical for achieving true plastics circularity.
It is generally envisioned that chemical recycling will not replace mechanical recycling, but rather, will complement it (Figure 1). In cases where mechanical recycling can be effective, it will be used preferentially, since its costs are lower. However, because mechanical recycling cannot be used indefinitely, and is only effective with uncontaminated, single-component waste streams, chemical recycling technologies will continue to have wide-ranging opportunities.
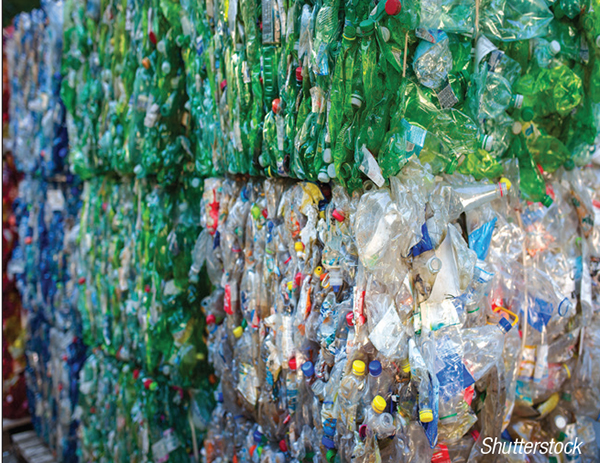
FIGURE 1. Mechanical and chemical recycling approaches are expected to be used complementarily for waste plastics
“We anticipate strong growth in the chemical recycling industry over the next decade, despite a host of challenges that have led to slower-than-envisioned progress on plant development and some project failures,” says James Kennedy, an analyst with market research firm IDTechEx (Cambridge, U.K.; www.idtechex.com). “It’s definitely a mixed picture within chemical recycling, with a variety of ups and downs, and different stories playing out among the different technologies,” he comments.
Economic viability
The field of chemical recycling can be divided into four general technology categories: pyrolysis, solvolysis, thermochemical processing and dissolution. Because of three factors — the size and complexity of the plastic waste issue, the diversity of polymer types and formulations, and the growing demand for recycled plastics — it is likely that most or all chemical recycling approaches will have opportunities in certain situations. And chemical recycling will exist as part of a mosaic of potential solutions for addressing plastic waste, including other external efforts, such as reducing plastic usage, designing for recyclability and incorporating alternative bio-based materials.
Within each chemical recycling technology category, there are significant efforts to reach technoeconomic viability. “The main concern right now overall is the cost of the technology,” says Marcian Lee, an analyst with Lux Research (Boston, Mass.; www.luxresearchinc.com). “It has to make good financial sense for companies to invest in [chemical recycling] technologies,” he says.
“Consumers will often say they would pay a ‘green premium’ for purchasing products made from recycled materials, but at the time of actual purchases, the follow-through action often fails to back up the sentiment,” Lee says.
Current price premiums for chemically recycled polyethylene terephthalate (PET) are estimated at two to three times the costs for petroleum-derived virgin plastics, Lee says. “For mechanically recycled plastics, I commonly hear a 30% premium is the ballpark maximum that most companies will pay for.”
“If left strictly to a free market, achieving plastics circularity through recycling is an extremely daunting prospect right now,” Lee says. “Regulatory mandates for utilizing recycled material are likely needed to spur the industry forward.” Chemical manufacturers are looking for government regulatory agencies to take a clear legislative stance and provide regulatory guidance. The details of these policies will have a large impact on how the chemical recycling industry will develop, Lee explains. (For more, see box below).
Pyrolysis prospects
In terms of announced capacity, the largest share of advanced recycling falls under the umbrella of pyrolysis, a recycling approach in which waste plastics are exposed to high heat in an inert (oxygen-free) environment to break down polymer chains into naphtha substitute that can serve as feedstock for other products or fuels. This technology class has received significant investment from many large companies in the oil-and-gas sector, because the pyrolysis oil resulting from processing plastic waste in this way can be integrated into existing petroleum refining and petrochemical assets. TotalEnergies, Shell, ExxonMobil, BP, Chevron Phillips Chemical and others are among the oil-and-gas majors investing in pyrolysis technology.
Lee, from Lux Research, says that the period between 2024 and 2025 is a key inflection point for pyrolysis, “where we may see 1 million tons/yr of completed global pyrolysis capacity — a sign of the technology’s commercial maturity.” However, Lee has also observed that only half of the announced pyrolysis capacity has been realized thus far. For example, the Brightmark recycling plant in Ashley, Ind., which runs a pyrolysis process, has faced significant delays in reaching full capacity. And in July, Shell plc, which had been among the companies expressing optimism about pyrolysis, announced that it is scaling back its goals for pyrolysis recycling.
And scrutiny of pyrolysis processes is ongoing, partly because the pyrolysis products can be used to make fuels, rather than new plastic, raising the question of what actually counts as recycling. In September, California attorney general Rob Bonta filed a lawsuit against ExxonMobil after a two-year investigation, charging that the company has been “deceiving the public” about the potential of plastics recycling. Pyrolysis processes are at the center of the lawsuit, which alleges a wide gap between the amount of recycled content the company says it incorporates into its products, and what is actually contained.
A critical regulatory question for pyrolysis projects is whether plastics derived from pyrolysis oil will count as recycled content. If governments don’t allow it, there is little or no incentive to use pyrolysis oil over traditional crude oil.
Stepping up the pyrolysis game
“Pyrolysis is a viable technology for chemical recycling of polyolefins and mixed plastic streams, but its problem is that it is very imprecise,” explains Marcian Lee from Lux Research. “It’s difficult to get high yields of propylene from waste polypropylene, for example, and instead, many pyrolysis processes generate a wide range of hydrocarbons of random lengths when breaking the polymer.” Products range from CH4 to C35+ waxes. At large scales, achieving precise breakage is a significant challenge, but would be a distinct advantage, he says.
“Some thermochemical recycling methods can be thought of as ‘next-generation pyrolysis,’ where polymer chains are broken down in a more precise and targeted way,” Lee says.
Strategies including the use of catalysts to narrow the range of products, are being developed. These projects, mostly in the pilot stage now, “require precise control of temperature, because if that parameter varies, you start to get side reactions and more undesired species,” says Lee. While catalysts may improve product specificity, they also add complexity and cost.
In a recent example involving catalysis, LyondellBasell (Rotterdam, the Netherlands; www.lyondellbasell.com) started construction in September on its first advanced recycling plant at its Wesseling, Germany site (Figure 2). The project focuses on LyondellBasell’s proprietary MoReTec technology, a catalytic pyrolysis process developed with the Karlsruhe Institute of Technology (KIT; Karlsruhe, Germany; www.kit.edu) that converts pre-treated, mixed-waste plastic into raw materials to produce new plastic polymers. The incorporation of catalysis into the process allows lower operating temperatures than conventional pyrolysis, and allows a greater degree of selectivity of the chemical reactions. Rather than a range of mixed hydrocarbons, MoReTec produces virgin-quality polymer feedstocks that can be directly reintegrated into new plastic production, the company says. Anticipated startup for the new unit is in 2026, and other facilities are planned, according to the company.
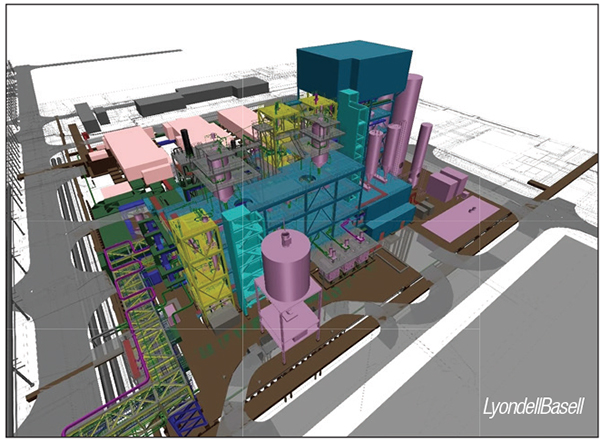
FIGURE 2. LyondellBasell started construction in September on a catalytic pyrolysis unit at its site in Wesseling, Germany
Another example of a “next-gen” thermal separation process comes from Carbon Rivers (Knoxville, Tenn.; www.carbonrivers.com), a company that has developed a mechanical and thermal process for downsizing and separating polymer composite materials, such as glass- or carbon-fiber-reinforced polymers. Carbon Rivers chief strategy officer David Morgan says the advanced materials engineering innovation firm makes various specialty materials, but is also advancing a process to efficiently separate polymers from glass fibers in composite materials used for wind turbine blades, marine vessels, aerospace, building materials and automobiles.
The company has developed an unconventional modified pyrolysis process to separate organic polymer resins from the glass fibers without degrading the glass. “We have a low-temperature thermolysis step that cracks the polymers, and a circular scheme that recovers the glass fibers intact, so they can be reused in other composites,” says Morgan.
To make the process work, Carbon Rivers had to find ways to minimize glass degradation during the process and identify the correct temperature to crack the polymers to allow for the separation. Then they apply a sizing chemistry in order to use the recycled glass fiber (rGF).
The company is currently in the engineering design stages for a commercial-scale facility in Texas for processing post-industrial and post-consumer composites and developing a novel continuous recycled-glass-fiber filament. Construction will begin in Q2 2025, Morgan says.
The Carbon Rivers process is suitable for epoxy, polyurethane, polyester, vinyl ester and Elium, and could be used to recycle wind turbine blades and marine hulls.
PET solvolysis ups and downs
The most technologically mature chemical recycling technique may be the use of solvolysis for depolymerization of PET, a common polyester used for beverage bottles and many other products. Solvolysis, a recycling approach in which ethylene glycol (glycolysis), methanol (methanolysis) or other chemicals are used to cleave polymer linkages in waste plastic, works for condensation polymers (including polyesters, polycarbonate, polyamides), but not for mixed plastic streams containing polyolefins.
Earlier this year, Eastman Chemical Co. (Kingsport, Tenn.; www.eastman.com) started the world’s largest molecular recycling facility at its Kingsport site using a methanolysis process (Figure 3), and announced further investments in other methanolysis facilities in Longview, Tex. and Normandy, France. In October, Eastman said work on the Texas project remains on track. The project features deployment of thermal heat batteries and onsite solar power, along with the recycling technology. Combined, the facility can achieve up to 70% reduced carbon emissions for recycling PET. “We can take polyester waste that mechanical recyclers cannot handle today, such as colored and opaque PET, clamshells, polyester carpet and textile fibers and more,” an Eastman spokesperson said.
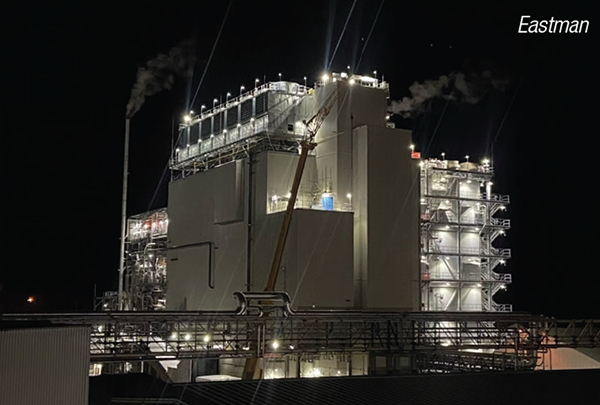
FIGURE 3. The chemical recycling facility at Eastman’s Kingsport, Tenn. site began producing recycled material from PET waste earlier this year
For the project in France, the priorities remain “securing customer offtake contracts and value engineering,” Eastman says. “We remain confident in the need for this and other plants, but continue to evaluate the optimal timing of the project.”
Some solvolysis recycling approaches use ethylene glycol (EG) as the reagent. SABIC (Riyadh, Saudi Arabia; www.sabic.com) is using a glycolysis process to depolymerize PET waste (mostly single-use water bottles) into monomers and oligomers. These are then dissolved and combined with 1,4-butanediol to upcycle the material into polybutylene terephthalate (PBT). PBT resins containing recycled PET have a smaller environmental footprint, in terms of cumulative energy demand and global warming potential, than virgin PET resin, SABIC says. PBT is used for products requiring enhanced properties and more durability, like electronic wire coatings.
Another solvolysis project, however, recently ran into trouble. The company Ioniqa (Eindhoven, the Netherlands; ioniqa.com) is developing a solvolysis process using EG and a proprietary catalyst to make virgin-quality materials from PET waste. Ioniqa had established a demonstration plant in Geleen, the Netherlands, but in October, the company announced it is seeking bankruptcy protection, citing higher costs than petroleum-derived plastics and an underdeveloped supply chain for plastic recycling. “The advanced recycling sector is challenged by the low cost of virgin plastics derived from fossil oil and a plastic recycling supply chain still in development. Furthermore, the implementation of regulated mandatory standards for meaningful recycling levels are too far out into the future,” Ioniqa says. Combined, these factors render large-scale deployment of Ioniqa’s technology “economically unfeasible,” the company says.
Dissolution
Plastics recycling processes based on dissolution technology aim to address a major recycling challenge: many plastic products contain multiple materials, such as packaging films with layers of polyethylene (PE) and the oxygen barrier ethylene vinyl alcohol (EVOH), which complicates any efforts to recycle them. Dissolution approaches are based on selective dissolution of one layer with a solvent mix that does not dissolve the other layers. The undissolved portion is filtered out and the dissolved polymer is precipitated with low temperatures or antisolvents.
Marcian Lee says: “Dissolution has a big role to play in engineered plastics, because it is tolerant of contaminants. While it is hard to get to food-contact-grade material with dissolution technologies, it is not hindered by contaminants as long as they don’t dissolve in the solvent, which are generally trade secrets.”
One company working on scaling up a dissolution process is APK AG (Merseberg, Germany; www.apk.group). The company’s NewCycling process produces low-density PE granules from mixed plastic packaging waste by selectively dissolving PE and separating it from other polymers, additives and contaminants in the waste stream. APK says its recycling process lowers CO2 production by 66% compared to new plastic. The company has plans to isolate other polymers as well. In October, LyondellBasell completed its acquisition of APK.
Another example of a dissolution process is the solvent-targeted recovery and precipitation (STRAP) process, developed by scientists at the University of Wisconsin-Madison (www.wisc.edu) led by George Huber. Construction of a pilot plant for a continuous STRAP process was begun last year at the Michigan Technical University (www.mtu.edu), in a collaboration led by MTU professor Ezra Bar-Ziv.
Enzymatic depolymerization
Another approach to depolymerization utilizes enzymes to cleave the polymer bonds in plastic waste. This technology, sometimes included under the solvolysis umbrella, is somewhat less mature than some other chemical recycling technologies, but it is attractive because it requires less energy than many other approaches. Thus far, enzymatic depolymerization has been developed with a focus on PET, but theoretically, it could be used for other polymers. A leader in this area is Carbios (St. Beauzire, France; www.carbios.fr). In May 2024, Carbios broke ground on the world’s first PET biorecycling plant based on enzymatic depolymerization in Longlaville, France. The plant will have a processing capacity of 50,000 tons/yr of prepared waste when operating at full capacity, the company says, and products are expected to be delivered in 2026. It will handle multilayered, colored and opaque polyester packaging waste and polyester textile waste.
Thermochemical approaches
Because many waste streams consist of mixed plastics with contaminants and additives, there is keen interest in recycling processes that can accommodate a broader range of feedstocks. One approach is using supercritical water to break down plastic waste. Mura Technology (London, U.K.; www.muratechnology.com) developed Hydro-PRT, a process that uses water above its critical point to produce fossil-equivalent oils from mixed, multi-layered flexible and rigid plastic waste for the petrochemicals industry to create virgin-grade plastics.
The company says its first commercial-scale Hydro-PRT plant, in Teesside, U.K., will become the world’s largest advanced recycling plant when it commences operations later this year. Two further plants being built under license with partners in South Korea and Japan, are expected to come online next year.
The application of microwaves to as a method of energy transfer has emerged as an alternative approach to processing plastic waste streams. Startups such as Pyrowave Inc. (Montreal, Que.; www.pyrowave.com) and Microwave Solutions (Riehen, Switzerland; www.microwavesolutions.ch) are among those pursuing the use of electrically powered microwaves to replace thermal methods for plastics recycling.
Microwave Chemical Co. Ltd. (MWCC; Osaka, Japan; www.mwcc.jp) is also pursuing this, and has partnered with Asahi Kasei (Tokyo; www.asahi-kasei.com) to scale up its technology, known as the PlaWave platform. MWCC and Asahi Kasei plan to begin constructing a pilot plant using microwaves to depolymerize polyamide-66 (nylon) in 2025. The partnership envisions expanding the approach to other plastic types also.
MWCC’s Yuri Katoda says “Microwaves serve as a method of energy transfer, rather than initiating a specific chemical reaction… Each material has its own unique microwave absorption capability. And by leveraging these characteristics, we are engineering optimal depolymerization conditions based on microwave heat transfer principles.”
In the case of PA-66 recycling, the microwave process directly generates the monomers hexamethylenediamine (HMD) and adipic acid (ADA) at high yield with low energy consumption, Katoda says. Advantages of microwaves include precise temperature control, smaller facility footprint and decarbonization (use of renewable energy possible).
“Our chemical recycling technology is based on the microwave absorption capabilities of different plastics,” Katoda explains, “so we are basically prepared to adapt our technology to any type of plastic.” MWCC aims to build a commercial plant within the next several years, Katoda says.
Another recycling company employing microwaves is GR3N S.A. (Lugano, Switzerland; blog.gr3n-recycling.com). GR3N has developed microwave-assisted depolymerization (MADE) to break down PET into its monomers and create new PET pellets with quality comparable to virgin plastic. The technology combines microwaves with alkaline hydrolysis in a way that tolerates higher levels of impurities than existing methods, the company says. The company is building a facility in Spain to produce 40,000 tons/yr of “virgin-like PET.”