On the heels of several technology breakthroughs in 2024, Phil Garcia, vice president of commercialization at synthetic biology specialist Cemvita (Houston), discusses what’s next for the company. Cemvita operates an integrated laboratory and pilot facility in Houston converting carbon waste into sustainable oils via its proprietary, microbial waste-to-oil process.
“In the last six to eight months, we really started hitting some strides that take this beyond the conceptual and really have the opportunity for real commercial scale in the hundreds, if not thousands, of barrels per day (bbl/d) production at that facility,” notes Garcia. This greatly accelerates the company’s initial projections for capacity of 500 bbl/d by 2029. Garcia adds that Cemvita is currently using 4,000-L bioreactor systems, but is poised to scale up to a 10,000-L reactor system based on some novel process improvements.
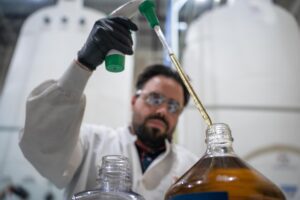
Cemvita has announced a series of milestones in the scaleup of its microbial waste-to-oil process (source: Cemvita)
The first of these breakthroughs, announced in May, supports production of large volumes of sustainable aviation fuel (SAF) via a solvent-free bio-extraction process. And in July, the company announced that technological improvements in lipid productivity and reactor optimization efforts have allowed for a quadrupling of production output and an increase in oil-extraction efficiency of 330%.
Cemvita’s process results in an oil that is similar to traditional palm oil. “It’s full of palmitic and oleic acids, with saturations that are exactly what you would see from a palm-oil alternative, without any of the land and water requirements of palm oil. And it happens to be produced from waste, resulting in something like palm oil without any of the sustainability issues,” emphasizes Garcia.
SAF production is indeed one of the company’s most attractive use cases for its oil, but it also could be a potential feedstock for food-grade products, cosmetics, animal feed and more. Garcia sums up the company’s priorities: “At Cemvita, we’re focused on large- scale industrial decarbonization, so for us, that means taking big swings at industries that really move the needle. While we were happy to help and use the products in various ways, we want to apply this technology for its highest impact in reducing carbon intensity and emissions profiles where they matter the most, so things like SAF are a great fit.”
When asked what is meant by “waste” with regards to Cemvita’s desired feedstocks, Garcia says that the company has a framework of ten different waste sources for feedstocks that have undergone lifecycle analysis and can “be treated under the right lens for carbon intensity.” This grouping of “waste” materials includes lignocellulosic sugars, as well as wastewater from food and beverage processing, which are desirable due to the organic content that can be fed to Cemvita’s microbes. “Lignocellulosic sugars are a viable input to our process that have not historically been very well utilized. Crude glycerin (a byproduct from biodiesel) is another promising avenue,” notes Garcia. The variety of feedstocks that can be handled by the process enable a more localized and flexible approach to production.
With the recent improvements to microbial effectiveness, Cemvita has achieved the ability to utilize these wastes with higher-than-anticipated carbon efficiency and conversion ratios. “By carbon efficiency, we mean grams of product per grams of carbon you put in, so whether that’s an element of food-and-beverage wastewater or if it’s from crude glycerin, the conversion of that waste to sustainable oil is where we’ve really made significant strides,” says Garcia.
The next pieces of the puzzle involve improvements to the bioprocess itself and the extraction of the oil product from the microbe. “As our yeast grows, it stores energy as fat, just like we do. And they don’t tend to move around a lot, so they don’t burn it off. So what we’ve done is maximize the oil content inside of those through specific proprietary technology that we’ve developed to make that oil content incredibly high,” comments Garcia.
For extraction, the major breakthrough was the development of a solvent-free process to efficiently extract the oil inside of the microbe at a very high production rate and throughput. Not only did this method help to improve efficiency, but it also opens the door to potential product streams other than fuels.
Beyond Cemvita’s main facility in Houston, engineering work is underway for the first commercial-scale production train, to be located on the U.S. Gulf Coast. Startup is currently expected in the second quarter of 2026, with anticipated production capacity at the scale of hundreds of barrels per day of sustainable oil. ♦