At the YNOW2024 Conference in Houston (photo), the move toward autonomous operations — including artificial intelligence, robotics and beyond — was a front-of-mind topic for all in attendance. In an exclusive interview from the event, Mitsuhiro Yamamoto, a Yokogawa vice president and head of the Systems Business Div., Digital Solutions HQ, discussed the technological developments helping to move operations from industrial automation to industrial autonomy (IA2IA), and how these solutions will spur the efficiency and workforce resiliency needed to foster the energy transition. “Yokogawa is definitely advocating for the IA2IA transition, especially in chemical plants, where the number of veteran operators is decreasing and the number of younger staff is increasing. We want to make it possible for all plant personnel to devote more of their time to value-added tasks, which requires increased autonomy from the automation systems,” said Yamamoto.
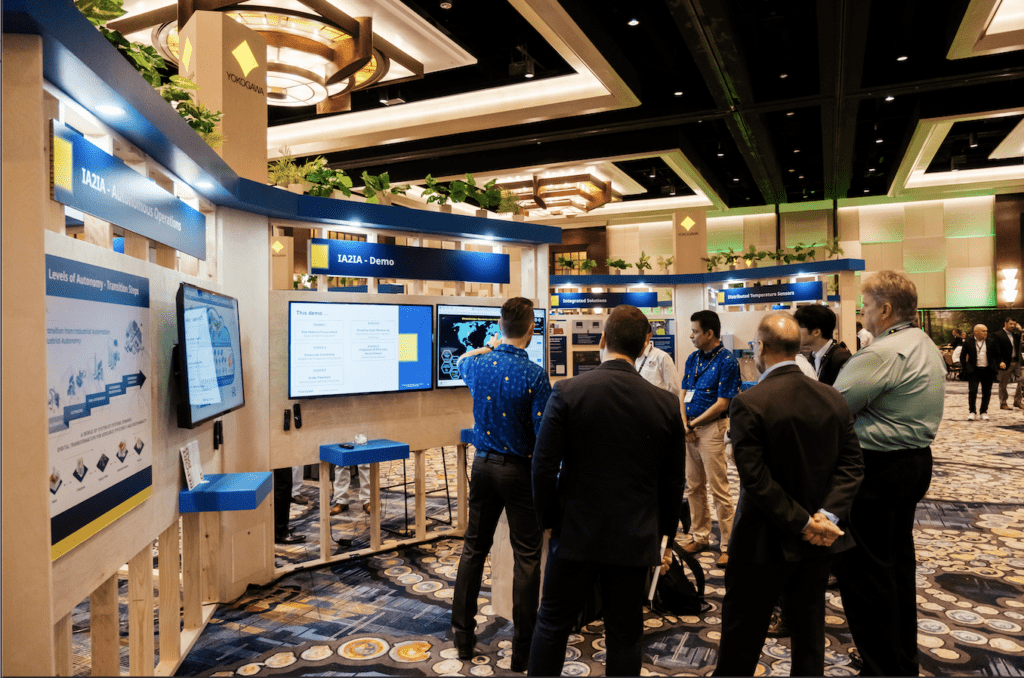
Attendees at the YNOW Conference (Source: Yokogawa)
In the YNOW2024 keynote addresses, Kevin McMillen, president and CEO of Yokogawa Corp. of America, and Peter Kwaspen, facilities and equipment technology lead at Shell, also shared their ideas on autonomy and the future of smart manufacturing. “Digital transformation is becoming part of our lives. It’s changing the way we manage industry, the way we work. You’ve got artificial intelligence that obviously is impacting every part of our businesses and of our lives, and we can either be run over by it, or we can understand it and utilize it to make that change more acceptable,” said McMillen.
Further defining the value of autonomy, Kwaspen added: “What is industrial autonomy? To me, it’s maximum uptime, independent operations and no human intervention. So when I translate that into technical requirements, I think of things like optimal mean time to repair and optimal mean time between failures. There are no surprises, no unplanned downtime, the most efficient maintenance processes and the shortest turnaround times.”
A number of technology platforms are enabling autonomous transformation in the chemicals industry, even in complex chemical operations that may require manual steps or specific variances between batches or product runs. “There are still many manual processes in the chemical industry. Digital technologies enable integrated or remote operation, optimizing talent usage and enhancing maintenance activities through advanced analytics, artificial intelligence and robotics,” explained Yamamoto, also highlighting collaborative servers, as well as digital twins and open process automation (OPA), as key technologies to leverage in these areas.
“Many transformational improvements are needed in production plants, such as for increased overall equipment effectiveness (OEE), product yields and throughput. Additionally, recipe management, energy efficiency, batch campaign management and quality stabilization are all areas in which Yokogawa can help with an initial assessment and roadmap development,” he noted. In 2023, Yokogawa announced a milestone in autonomous plant operation, in which a reinforcement-learning algorithm was officially adopted by ENEOS Materials Corp. for direct control of a distillation column within a chemical plant.
For robotics specifically, while many applications in the chemical industry are still in the proof-of-concept phase, Yamamoto sees a future where facilities may be managing several different types of robots for varying applications: “For example, some robots may need to be certified for use in hazardous areas, while others may not. Some robots may need to climb stairs, and some sites may be employing drones for certain tasks. A unified user interface and unified robot management will be very important.” Earlier this year, Yokogawa released its OpreX Robot Management Core platform, which provides a single user interface to control an entire fleet of robots, regardless of the supplier, and also connects into a plant’s distributed control system (DCS). “We envision a future where the DCS and robots work together. For example, an alarm triggered by the DCS can be used to direct the robot to inspect the site and address the problem. Also, data collected by the robot — including photos, video and audio — during its rounds of inspection can be reflected in DCS operations in real-time,” he added.
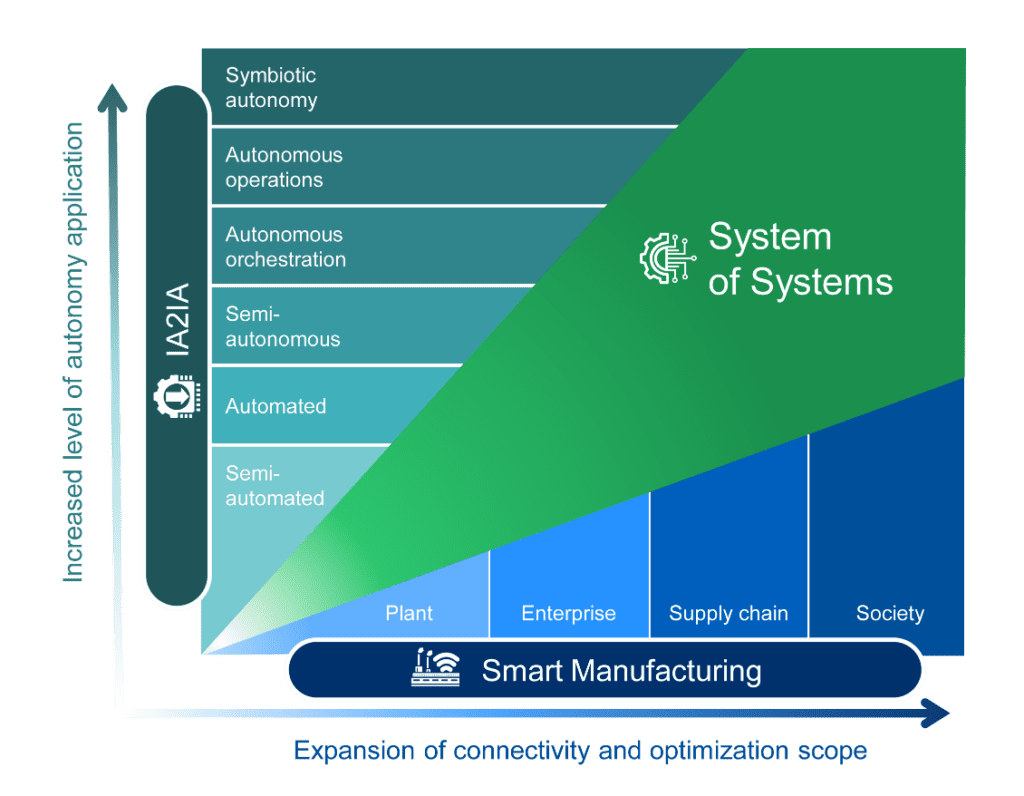
This diagram illustrates the systems of systems approach whereby automation systems can gain complexity to eventually reach autonomous operations (Source: Yokogawa)
Alongside the commitment to the IA2IA transformation are parallel efforts to advance the global energy transition. Yokogawa is deploying its Collaborative Information (CI) Server to a number of energy-transition projects, including Shell’s Holland Hydrogen I Project, the Yuri Green Hydrogen Project in Australia, CrossWind and the Ishikari Bay New Port Offshore Wind Farm. “The strength of the CI Server in all of these projects is its ability to integrate other companies’ products as well as ours. The world has entered an age in which things are interconnected in ever greater and more complex ways. Yokogawa aims to provide value through smart manufacturing and the System of Systems (SoS) concept,” said Yamamoto. The SoS concept (diagram) involves a collection of independently operated and managed systems, merging into an overarching system to deliver value. This approach, combined with IA2IA and other smart manufacturing concepts, changes the level of autonomy and broadens the scope of overall optimization, which is especially crucial in emerging renewable-energy projects.