In this interview, experts from the Thermal Kinetics division of RCM Technologies discuss an engineering-first approach that helps address market gaps in the fuel-ethanol industry and unlocks capacity-expansion potential for manufacturers
Despite significant projected growth in the ethanol sector through 2030, fuel ethanol producers are still generally smaller organizations than petroleum refining and chemical manufacturing corporations. This means that ethanol plants may lack the same in-house engineering and infrastructure support of other large organizations. In light of this market gap, the Thermal Kinetics division of RCM Technologies, Inc. (Pennsauken Township, N.J.) has launched its New Ethanol eXpansion Technology (NEXT) program — a suite of engineering solutions designed to help ethanol plants increase their production capacity without major equipment replacements or process overhauls.
“Fuel ethanol plants, for the most part, run lean. There are no real centralized engineering offices, they have relatively small staffs, without a large number of operators, and often the employees are just trying to make sure things operate and are fixing day-to-day issues, so there’s not really an engineering staff that they could work with for guidance on operational improvement and expansions. We come in and tell them what their plant can actually do and how much more money they can make, as an extension of their engineering staff,” says Roy Viteri, business development manager at RCM Thermal Kinetics. “And since we know how to do hydraulics, equipment design, heat transfer, distillation, dehydration and evaporation, we can tie all of that together and provide expertise and support to the smaller ethanol players.”
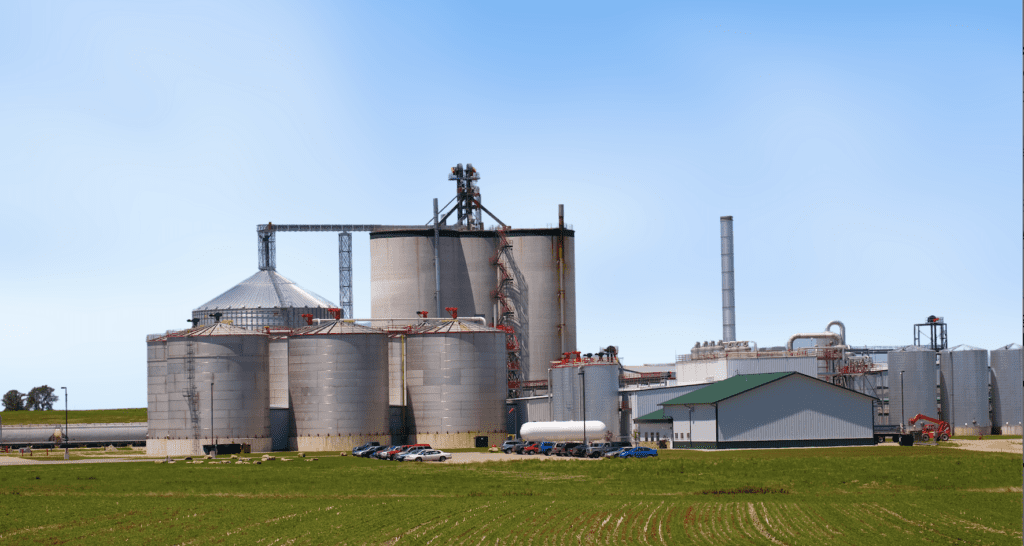
A small ethanol plant (Shutterstock)
NEXT was born out of a project Viteri worked on at an ethanol plant that was experiencing severe operating problems. Since Roy has the in-the-field skillset as well as an understanding of hydraulics, after being on site for only an hour and a half at this plant, it became immediately evident that it was needed to start replacing the column internals.. Then there is the hydraulic balance around the entire distillation, dehydration and evaporation units. At this particular site, someone installed a piping circuit with a control valve that was incorrectly sized and instrumentation that was incorrectly spanned. This was the gap in the market — having one company that knows how to identify the cause of operational issues, understands the unit operations and has the ability to balance system hydraulics around all of it” explains David Loschiavo, general manager – Thermal Kinetics at RCM Technologies. Often, when smaller plants want to tackle process issues or evaluate capacity expansions, they have to seek out contractors who are individually specialized in pumps, valves, control strategies and so on. The NEXT program offers comprehensive coverage of the full ethanol process. “Nobody else has this entire package in ‘one box,’ who can take on all of these responsibilities, and now that’s what we’re doing,” emphasizes Loschiavo.
The scope of NEXT’s first deployment includes installing new internals in two distillation columns, expanding heat exchangers and expanding pipe-spool sizes, as well as a list of around 18 other improvement items. The plant employs 25 people and produces around 86 million gal/yr of ethanol, which Loschiavo expects to increase to 105 million gal/yr after implementation of NEXT program improvements. The punch list of mechanical changes is accomplished over a 5-day plant turnaround with a crew of approximately 50 working 24/7.
“Customers are trying to find innovative ways of making more with without spending a lot more money. So we come in with the scalpel and figure out what minor modifications or, in some cases, major modifications, can be done within the time allotment to make it a profitable investment for the customer,” adds Viteri.
Another benefit of the NEXT program is the nimbleness gained from an engineering team working onsite with the physical equipment, versus remotely working with simulation and historical process data. “The basis of our design, which again, is lacking in the ethanol industry, is being able to go out into the field and actually get real operating data. What we like to say when we’re out in the field is that the equipment will always tell us the truth. It is useful to talk to operators, but in the end, the equipment will tell you what’s going on. There are no ‘tall tales’ or bad instrument measurements that that people have been believing for years on end. It’s actually what the equipment is doing. We’re going out into the field getting pump, suction and discharge pressures and inlet and outlet pressures around control valves and so on. With all that information, we can then start gathering how the system is really working and then figure out how far they can push the distillation towers,” says Viteri.
Notably, NEXT program initiatives can be implemented during short-duration plant turnarounds, with just a small onsite engineering team, enabling production schedules to remain uninterrupted while delivering an achievable expansion strategy.