Bioreactor development
To facilitate the configuration of bioreactors, GEA Group (Düsseldorf, Germany; www.gea.com) has developed a digital twin for virtual testing prior to construction. The aim is to create an optimum growth environment for cultured cells, which behave differently in mass production volumes than at laboratory scale.
“A digital twin simulates the environment inside bioreactors in a wide variety of scenarios. This lets us precisely match the tank design and the mechanical configuration for fine-tuning parameters, such as shear stress, temperature, nutrient and oxygen distribution, to what the cells need,” explains Daniel Grenov, product manager Bioreactor Technologies at GEA.
The virtual bioreactor testing is based on computational fluid dynamics (CFD), which models the growth behavior of cells, as well as the oxygen and nutrient delivery radii inside the reactor. “Experts estimate that, when scaling up bioreactors, uneven distribution of oxygen and nutrients inside the tank often leads to performance losses of up to 30%,” Grenov says.
By using CFD simulation and calculating kinetic models, combined with physical test rigs to measure bubble sizes and equipment behavior, the performance of large-scale bioreactors can be optimized before they are fabricated.
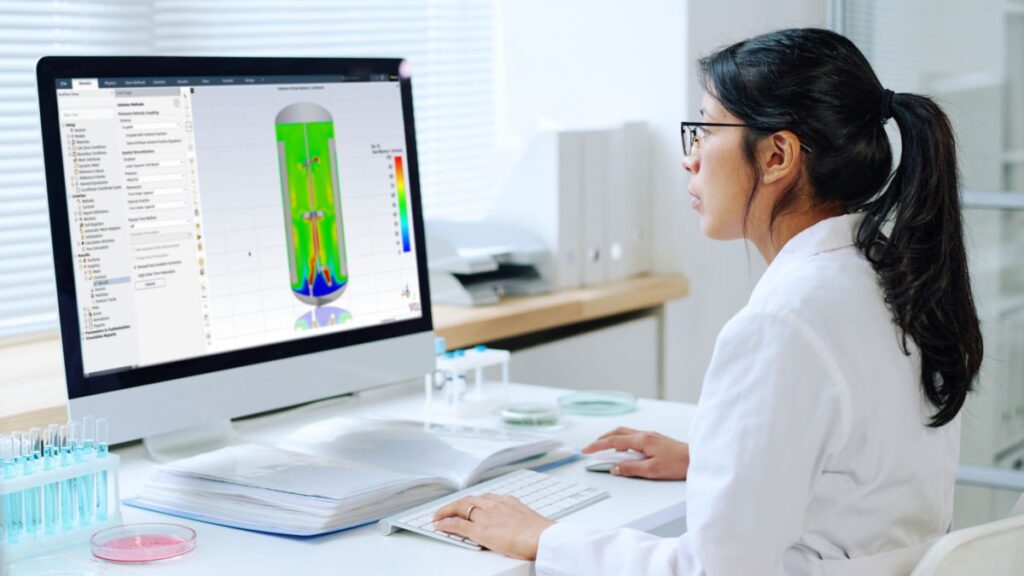
Source: GEA