This article provides an overview of how computational fluid dynamics (CFD) works, and what benefits it can bring to the chemical process industries
Sustainability, waste reduction, energy efficiency and increased demand for engineered material are driving process engineers to continuously investigate new products and processes, and develop ways to improve process and equipment safety, efficiency and reliability.
To accomplish this, engineers can leverage advanced product-development modeling tools, such as computational fluid dynamics (CFD), to conduct simulations that replicate the near real-life operating conditions of a plant or mimic product performance requirements. This virtual testing requires just a fraction of the time and cost of laboratory-scale or pilot-plant testing. It also reduces the need for expensive prototypes, delivers improved product quality and helps speed products to market.
CFD defined
Process engineers are familiar with plant design software and general mathematical modeling tools for process optimization. CFD is a branch of engineering simulation that solves the physics of fluids with or without heat transfer, mass transfer and chemical reactions, and is used for the design and analysis of equipment and unit processes. The idea is to predict, and design around, transport-related problems using detailed numerical-solution methods prior to physical testing. Alternatively, CFD simulations can provide operational support for troubleshooting, throughput improvement, process scaleup (and scaledown), and improving product quality and plant yield. The simulation can be steady or dynamic – 2D or 3D – and subjected to initial, boundary and flow operating conditions.
The use cases for which CFD can be applied are unlimited, but examples of unit processes include separation (Figure 1), mixing (Figure 2), heat-transfer systems, flow measurement and control, and reactors of all types, including packed-bed and fluidized-bed reactors. The CFD simulation results can be used to optimize the product at concept development, product design inception or for equipment already deployed in the field. The key element of successfully applying CFD is the ability of CFD algorithms to allow the simulation of complex physical flow phenomena within complex machinery under realistic process conditions accurately and reliably.
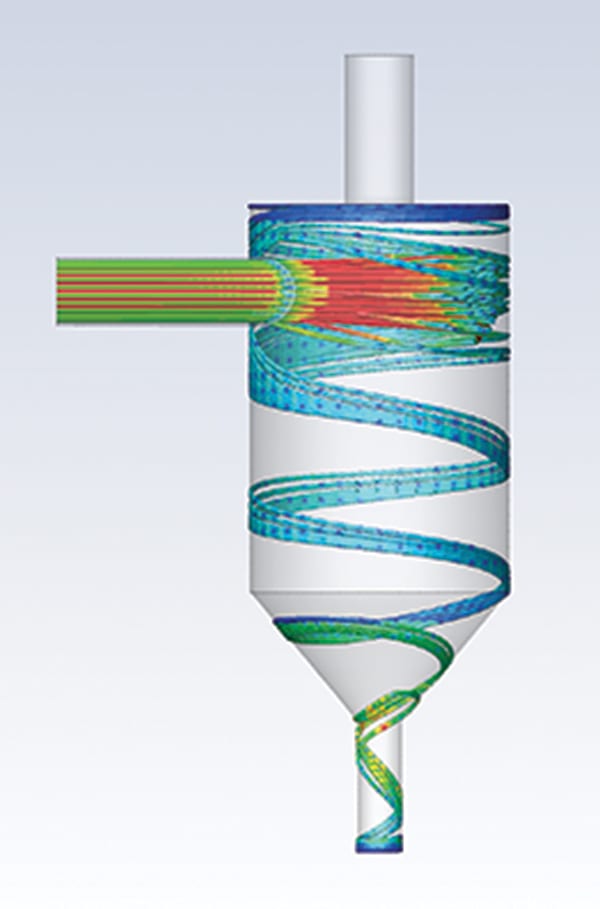
Figure 1. Particle pathways in the separation of solid particles from gas in a cyclone can be modeled by CFD Image: Ansys
CFD offers major advantages for the design and analysis process. Visualizing complicated flow features inside equipment can be quite complex. CFD enables engineers to create and explore “what if” simulated scenarios, providing them with detailed and comprehensive insights on flow fields, allowing them to virtually look inside their equipment. This enables the analysis, optimization and verification of design performance before building costly prototypes or undergoing time-consuming trial-and-error physical testing.
Simple CFD problems can be solved on laptops (for more information on CFD models using laptops, see Portable CFD: Build Interpolation Models from CFD Results in this issue). More sophisticated problems — in terms of physics or problems size — may require high-performance computing (HPC) that offer large clusters with countless cores and terabytes of memory, delivering dramatically reduced turnaround times for complex simulations.
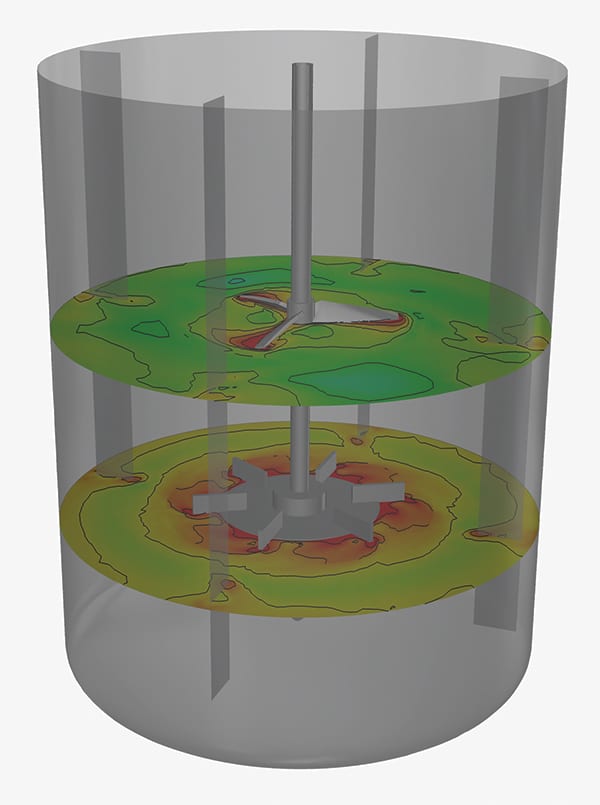
Figure 2. Shear rate variations in two planes passing through the impellers of a mixer can be shown with CFD Image: Ansys
Executing CFD simulations
Executing a successful CFD simulation that delivers meaningful end results requires considerable understanding of the problem being investigated. This typically involves the physics of fluid flow, mixing, chemical reaction and heat transfer. To achieve this, engineers must solve a set of mathematical equations that represent the problem of interest. CFD remains key for selecting and solving the physics-based equations “numerically,” since these equations are essentially impossible to solve analytically. CFD’s numerical or computational methods convert these equations into clear, linear algebraic equations and solves them numerically. Every CFD problem has the same general workflow, divided into four basic phases: model objective and domain extent, pre-processing, solving and post-processing.
Model objective and domain extent. Before initiating a CFD model, a clear description of the problem must be developed. What exactly needs to be modeled? What are the quantities of interest that should be obtained from the model (for example, pressure drop, flow distribution, concentration of various materials, and so on)? Then comes the question of what the domain extent for that CFD model should be (for instance, a mixing tank or a heat exchanger). The next step is to discern whether all the process (boundary) conditions are known (such as inlet conditions and heating/cooling controls). Another important ingredient in CFD modeling is the definition of material properties for the various ingredients. Finally, the CFD model must be made as efficient as possible by figuring out what simplifying assumptions can be made, in terms of physics, process conditions and even geometry.
Answering these questions in CFD modeling provides “rigor” to the engineering process, which by itself helps with the definition, documentation, repeatability and scalability of the process.
Pre-processing. During pre-processing, the first step is to prepare a geometrical computer-assisted design (CAD) model for CFD modeling purposes. The idea is to have a CAD representation that only contains the relevant geometrical features that will impact flow. Any unnecessary details or features should be omitted at this point.
Next, the discretization (mesh generation) of the flow domain plays a crucial role in the CFD workflow. While this used to be the most labor-intensive and time-consuming part of simulation, recent advances have streamlined this step tremendously. During discretization, CFD divides the CAD model into a finite number of discrete, small, individual regions called cells. This is analogous to a digital photograph where millions of pixels compose a single complex image, with each pixel possessing its own unique color. Analysts must strive for the optimal mesh that will capture flow features of interest, while keeping the overall model size in check.
To calculate the numerical solution in these individual cells, CFD computes all the flow variables (such as pressure and velocity) at the center (or node) of each cell, based on the values of velocity and pressure of its surrounding nodes. A large number of cells increases the solution’s accuracy, but also increases the number of equations that must be solved.
Solving. After discretization, the model can be set up for simulation. The set-up process involves the definition of the following:
- Boundary (or process) conditions, such as inlet flowrates, temperature and impeller speed (revolutions per minute)
- Physics, including laminar versus turbulent flow, steady versus unsteady, and so on
- Material properties, such as density, viscosity, thermal conductivity and specific heat
After the solver and physics model are established, the flow field can be solved. During the computing process, the solution must be monitored as modeling iterations are executed. This helps to understand the accuracy of the physical models, discretization and problem setup.
Post-processing. Post-processing is the last step in the CFD workflow. In this step, the obtained results are visualized, analyzed and interpreted. CFD provides both quantitative and qualitative insights. Examples of quantitative results include flow, concentration and temperature contours across the domain. On the other hand, examples of qualitative results include information like the average temperature exiting the system or the total pressure drop experienced. Based on the results, the appropriateness of the selected discretization resolution and the physical model is measured and revisited as necessary.
CFD for improving operations
CFD enables engineers to maximize throughput, innovate on new products, enhance process stability across the plant, drive sustainability and develop new processes more efficiently. The following are examples of how CFD can be applied to improve each of these.
Flow distribution. Most chemical companies do not design their own plant equipment; rather, they own assets and operate them. The key issue is throughput and finding new ways to push more material through production. Can they get more from their assets than they already have? How can they manage flow distribution to avoid erosion, corrosion and extra pressure drops? How will existing assets behave under different products or materials?
CFD delivers both a virtual visualization of the flow, as well as a quantitative description of how uniform or non-uniform the flow will behave across any section of the system (Figure 3). Empowered with this predictive modeling, engineers can best determine how to ensure flow uniformity throughout the entire system to better maximize throughput, yield and the operational efficiency of plant equipment.
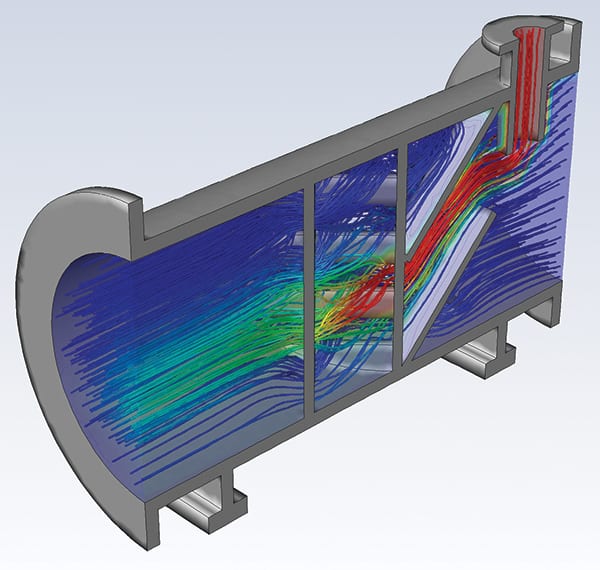
Figure 3. This diagram shows a visualization of the flow through a static mixer with hot and cold fluids Image: Ansys
Scaleup. CFD is also instrumental for supporting the scaleup process, especially in the chemical and pharmaceutical industries. During this process, engineers run experiments inside a laboratory on a much smaller piece of equipment to be tested. This bench- or laboratory-scale equipment is used to develop the product. Then, through the scaleup process, questions of how this product can be manufactured on the commercial scale are answered. CFD is used to estimate how the commercial-scale process will perform and the corresponding outcome on the product.
Process stability. CFD also helps drive process stability. Chemical engineers must manage problematic issues, such as rust buildup in pipelines and fouling, erosion, hotspots, dead spots and cold spots in chemical plants. Through CFD modeling, engineers can predict and identify these issues before they materialize in the plant and deal with them to deliver an enhanced level of efficiency, reduce downtime and help ensure safety. Also, the stability of the process against process or material variability can be simulated using CFD.
Process intensification. While engineers want production to run cheaper, better and more reliably, they also are focused on process intensification that allows greater energy efficiency and the creation of more sustainable products through reuse or product redesigns.
Enhanced efficiency. Companies that employ CFD have better insights into their processes. This enables them to operate their equipment at lower cost, potentially reduce emissions and delay unwanted maintenance. Using the additional insight from CFD, plant operators can reduce material waste tremendously.
Within the chemical industry, engineers focus on reducing the time and effort required to develop new processes or redesign or retrofit existing equipment. Achieving this while the plant is in production can be prohibitively expensive and disrupt plant operations. However, this can be accomplished offline virtually with CFD.
High-performance computing
As with other aspects of engineering, CFD offers varying levels of fidelity. As the complexity of the problem increases, engineers may use more computational points or look at transient aspects of a given problem. Advanced CFD tools provide different modeling capabilities that can run on anything from a standard laptop to a high-performance computing (HPC) system. Leveraging highly scalable HPC unlocks virtually unlimited compute capacity. This enables engineers to rapidly run complex, large model, high-fidelity CFD simulations, perform parametric studies and remove any restrictions that could compromise a design, cutting months off development cycles and expediting the launch of new products. According to an internal study, computing power limitations cause 90% of businesses that run simulations to make modeling concessions by limiting the size of their meshes or making physics models less complicated so they can be completed quickly to meet tight schedules.
HPC computing eliminates those constraints, allowing engineers to generate and analyze computationally difficult simulations using hundreds of compute cores to gain additional insight into their design’s performance. Utilizing affordable distributed hardware instead of costly workstations to create their simulations, engineers can view their results in a couple of hours instead of traditionally needing to wait a full day. Additionally, through parametric optimization, engineers can quickly review numerous design variations to select an optimum design.
The HPC hardware itself may be physical (on premise), in the cloud or a combination of both, depending on the local engineering workload and the site’s information technology (IT) infrastructure.
Advanced CFD software
Tasked with accomplishing more in less time, engineers are turning to leading software providers for enhanced CFD solutions. Equipped with built-in automation of a task-based workflow, cutting-edge CFD software can boost user productivity by reducing the learning curve, decreasing probability of human error and reducing human input. Complicated models that formerly required days or weeks to mesh now require only hours, and still deliver high simulation accuracy. Additionally, engineers can obtain answers to their design questions sooner, while also exploring a larger variety of design options in the same timeframe as before.
CFD continues to slash design cycles, reduce costs and drive unprecedented innovation. Disrupting the status quo of product development, CFD enables engineers with next-generation capabilities to create highly accurate designs that increase production flows, improve stability, promote sustainability and significantly improve processes. As engineers continue to harness the powerful capabilities of HPC and new CFD software, complex models are solved faster than ever, enabling companies to deliver new products to market with unmatched speed.
Edited by Scott Jenkins
Author
Hossam Metwally is a principal application engineer at Ansys Inc. (2600 Ansys Drive, Canonsburg, PA 15317; Phone: 844.462.6797; Email: [email protected]). In his current role, Metwally leads a group of engineers focusing on business development for the chemicals, power, pharmaceuticals and consumer products industries. Metwally is involved in technical and sales support, training, technical marketing, testing, documentation revisions and business development for chemicals, rubber, glass and polymer processing companies. He obtained a Ph.D. in mechanical engineering from the University of Cincinnati in 2002. Metwally joined the consulting group in Fluent, Inc. (now part of Ansys Inc.) in 2001.