Cement manufacturing is a major source of greenhouse gas emissions due to two factors: carbon dioxide is released when calcium carbonate calcines to lime (CaO) in the cement manufacturing process; and cement kilns are operated at temperatures of 1,500°C, which requires significant fuel consumption. Cement is the agent that binds sand and crushed rock together to form concrete.
Solidia Technologies (Piscataway, N.J.; www.solidiatech.com) has developed technology that can reduce CO2 emissions in final concrete products by up to 70%, compared to conventional concrete, by using CO2 as a reactant in the concrete curing process, and by employing cement chemistry that allows lower kiln temperatures (~1,200°C).
Ordinary Portland cement depends on the binding of calcium oxide (from limestone) to silica (from clay) to form di- and tricalcium silicates. These compounds become hydrates when water is added, and the concrete hardens. In Solidia concrete, a patented process called reactive hydrothermal liquid-phase densification (rHLPD) promotes binding between monocalcium silicate (CaSiO3) and CO2 to cure the material, rather than relying on hydrate formation. To harden Solidia concrete, CO2 is introduced to a water-containing concrete slurry, where the gas dissolves and begins leaching calcium from the monocalcium silicate. This process forms CaCO3, which precipitates out of solution to lock particles in place (diagram), effectively sequestering CO2 within the concrete.
Based on the research of Rik Riman at Rutgers University (New Brunswick, N.J.; www.rutgers.edu), the Solidia concrete process has a number of significant advantages over conventional concrete. Aside from its substantially lower carbon footprint, Solidia concrete has higher compressive strength and better abrasion resistance than conventional concrete. “The carbonate is thermodynamically more stable than the hydrates,” says Solidia chief technology officer Nick DeCristofaro. Also, curing times are reduced from three weeks to eight hours. Further, “Our process uses the same raw materials and capital equipment as conventional Portland cement, and does not require any changes to the existing concrete supply chain,” adds Tom Schuler, Solidia CEO.
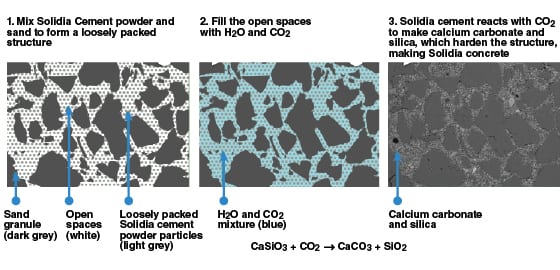
Solidia has signed an exclusive licensing agreement with Rutgers for the technology, and is commercializing the technology initially for pre-cast concrete, which constitutes pre-molded shapes including blocks, pavers, railroad ties and building components (as opposed to cast-in-place concrete, which is molded onsite).