Modernized pumps and advanced controls improve accuracy and repeatability of liquid-dosing systems
Whether the application is dosing chemicals for process or water treatment, whether it’s batch or inline dosing and whether it’s continuous or intermittent flow, at its heart, successful liquid dosing is really based upon choosing the proper pump and controls. But, therein lies the real challenge — how do you select the right equipment and assemble it into a system that is compatible with the chemistry, while providing the accuracy and repeatability necessary for the process? Fortunately, several advances in pump and control technologies are making it possible to design the liquid-dosing system that best meets the needs of your process.
Chemical-compatible pumps
There are many challenges associated with the chemicals being dosed, such as corrosiveness, potential for off gassing, high temperatures and viscosity, and any issues must be addressed when designing a liquid dosing system in order to provide accuracy, repeatability and reliability.
“First and foremost, the processor needs to consider chemical compatibility,” says Brian Ellingwood, technical sales coordinator with IVEK (North Springfield, Vt.; www.ivek.com). “Often there are chemicals that are corrosive or other hazardous materials that may be used in process.”
One of the ways manufacturers of dosing system components are handling chemical compatibility is by using advanced materials. For example, IVEK offers positive displacement pumps and valves in its product line. “We use ceramic because it is chemically inert. It enables us to take on a wide scope of projects while maintaining the integrity of the fluid handling process,” says Ellingwood. Recently, the company expanded its ceramic capabilities.
“We make and custom machine our own ceramics. While our primary ceramic has always been aluminum oxide, which is very hard, durable and non porous, there are chemistries where it is not compatible. We’ve expanded our capabilities and now offer zirconia with different stabilizers for a variety of applications. We also offer silicon carbide, which is ideal for hydrofluoric acid, a damaging, dangerous and difficult material to work with.”
Another consideration is off-gassing, says Mark Girgenti, lead design engineer with Burt Process Systems (Hamden, Conn.; www.burtprocess.com). “Certain chemicals will release themselves into a gas, so when they are injected, particularly at low flow rates, the recessed cavities of certain pumping technologies can allow the gas to build up, causing system failure or causing the system to inject the wrong amount of chemistry.”
New pumping technologies allow for degassing of systems. “One of the newer metering pumps we use has built-in degassing, where it bumps the motor into stand-by mode in order to allow it to remove the gas from the system prior to injection.”
Similarly, if a metered fluid is very hot, toxic or highly viscous, this can be a problem, says Michael Birmelin, marketing editor, with ProMinent GmbH (Heidelberg, Germany; www.prominent.com). “In difficult dosing applications, it’s important to use hermetically sealed metering units with wear-free diaphragms, which offer the ability to optimize dosing precision, even under tough conditions.”
The physical properties of the chemical being dosed can also create challenges, notes Ken Sipes, director of engineering for process systems with EPIC Process Systems (St. Louis, Mo.; www.epicmodularprocess.com/systems/dosing-systems). “Many metering applications require low or very low flowrates. If you are pumping a slurry with suspended solids or abrasive materials, there’s a chance the fluid may erode or damage the equipment or valves. Without proper equipment and material selection, the system will have great difficulty in metering accurately and consistently. There are many ways this can be accommodated. It’s a best practice to understand the process, consider the challenges and find the right pumping and control solution.”
Smarter, for better accuracy
Accuracy is important in liquid dosing for two reasons, says IVEK’s Ellingwood. “First, achieving repeatable and consistent product each and every time is essential in the process industry. Second, the chemicals being dosed could be very expensive material that must be tightly controlled and not wasted,” he says.
“While it’s key to repeatable and consistent product, getting accurate flow data is one of the greater challenges when designing a liquid dosing system,” explains Burt Process’s Girgenti. One thing that is helping is the development of smarter pumps paired with advanced control systems, he says. “In these cases, we’ve been employing smart pump technologies that can measure the volume of the chamber and provide a realtime flow measurement, allowing users to move away from adjusting stroke length toward a computer-controlled system that allows them to monitor and measure the volume of what is being dosed.” Other options include higher-end controls that communicate with the plant to provide realtime data and control the pumps locally, he says. “We are starting to see modernization and a move toward smart dosing pumps and higher-end control systems in the chemical feed and liquid dosing industry.”
Combining the two, Burt Process’s ChemPlus chemical feed systems (Figure 1) are pre-engineered chemical injection systems that provide flexibility in metering pump options and controls to meet the chemical- and corrosion-resistance requirements, as well as control needs for each application.
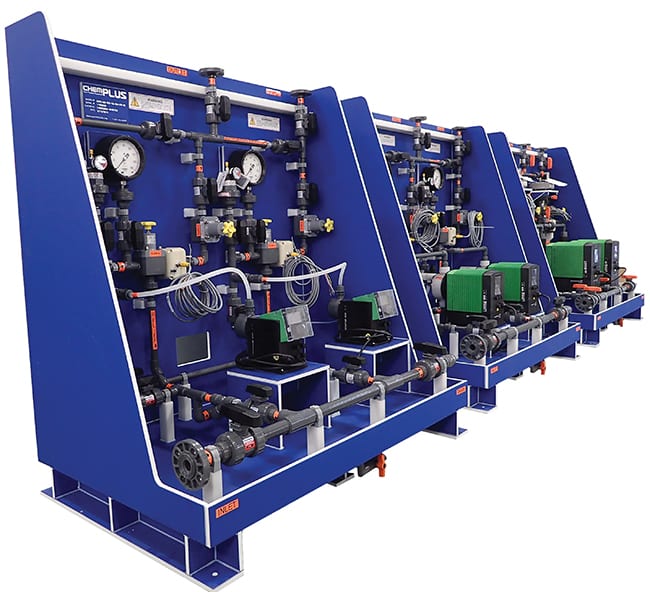
Figure 1. Burt Process’s ChemPlus chemical feed systems are pre-engineered chemical injection systems that provide flexibility in metering pump options and controls to meet the chemical and corrosion resistance requirements, as well as control needs for each application
Burt Process Systems
ProMinent’s Birmelin agrees that advanced pumps and controls are the latest development: “The amount of data generated by sensors and pumps will increase significantly in the future. A wide range of information needs to be recorded, provided and efficiently used in process control. Therefore, processors need data-based operating models, which require a high degree of mobility and transparency. So we are moving towards digital solutions that allow users to gather the relevant data and make them available where it is needed. These internal data are linked with external data and used to optimize operating processes.”
Considerations When Selecting a Liquid-Dosing System
While pumps and controls are becoming more modern, employing the latest technology won’t provide the necessary accuracy and repeatability if it is not the correct equipment for your application. EPIC Process System’s Ken Sipes provides some helpful information on making sure the system you end up with is properly designed and engineered for your process.
The first thing a system designer needs to know is the chemistry, or formula card, for the application. “This usually entails a number of different raw materials that are purchased in bulk from other chemical manufacturers and blended together to make the end product,” says Sipes. “Once we know what all the different ingredients are, we need to know how much of each goes into the process and, typically, there is an aspect of what level of accuracy is needed in dosing. The third component is the order of addition of the raw materials.”
When considering inline blending, knowing the necessary level of accuracy and order of addition is as important as understanding the characteristics of the raw materials. “Some chemistries are reactive as opposed to being a simple mixture. In those cases, accuracy is important because you are trying to force a reaction, control the reaction or to keep the reaction at a certain spot,” he says. “Order of addition is important because Chemical A and Chemical B may react poorly together, but if you first mix Chemical A and Chemical C, then add Chemical B, the reaction may be what you’re looking for.”
From there, it is important to consider the difference between batch and inline dosing. “Batch can be more economic from the initial investment standpoint, as it often requires less equipment and instrumentation and offers flexibility for formula changes that may occur down the road,” Sipes explains. “However, inline dosing and blending offers some advantages over batch related to space requirements and production productivity because there’s less equipment volume to clean during product changeovers.”
For example, manufacturers of detergent often make a “base” or “neutral” batch over and over again in large blend tanks and then pump it to fillers; however, before it goes to filling, the processor may dose the colors and fragrance near the filler, inline, so the amount of equipment and piping that has to be cleaned is minimized versus making the same finished product in large blend tanks. “A lot of processors are considering moving to inline operations for this reason, but they aren’t sure their formula can be done inline.”
To help, EPIC offers a small, demonstration inline blending skid (Figure 5). “If the chemicals aren’t hazardous or proprietary, we can run a trial in our facility or, if they are hazardous or proprietary, we can ship the skid to their site and they can run the test.” If the inline process passes QC tests and the processor elects to go to an inline system, we can then build one to their capacity. “Many customers are unsure about inline blending because they don’t want to risk investing in equipment and find that it won’t work in their application. The demo-scale skid we offer gives them the confidence to move to a production-scale system if that is appropriate.
As such, ProMinent offers metering pumps with predictive intelligence, such as the Gamma L and Gamma XL, which can be combined with the DULCOnneX platform to allow efficient and fault-free system operation, which the operator can access from anywhere (Figure 2). Devices can be fully integrated and accessed both locally and remotely. Processors benefit from direct access to the information about installed devices and systems. Calibration data, parameter sets or error messages create a comprehensive overview of process conditions, such as operating time, dosed volumes and pressure conditions, which can be called up to the current status or retrospectively.
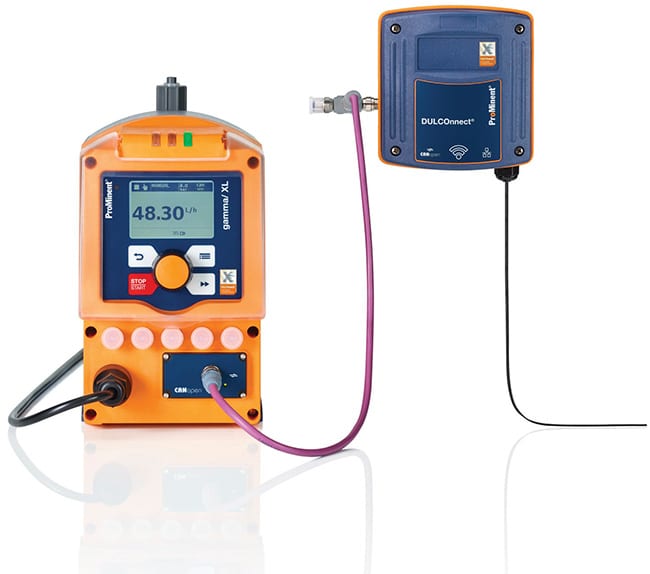
Figure 2. ProMinent offers metering pumps with predictive intelligence such as the Gamma L and Gamma XL, which can be combined with the DULCOnneX platform to allow efficient and fault-free system operation, which the operator can access from anywhere
ProMinent
Other components are also gaining intelligence as liquid dosing moves toward modernization, say the experts. For example, IVEK offers its Digispense 4000 programmable liquid dispensing system (Figure 3). The unit enables precise and repeatable fluid dispensing volumes at rates of 2 nL/s to 300 mL/s, as well as various production dispensing and metering modes that optimize the fluidic requirements. The control package also offers improved integration to programmable logic controller (PLC) systems. This is facilitated by Ethernet fieldbus communication options and web browser services. This communication allows processors to remotely monitor and control pumps through their computer network.
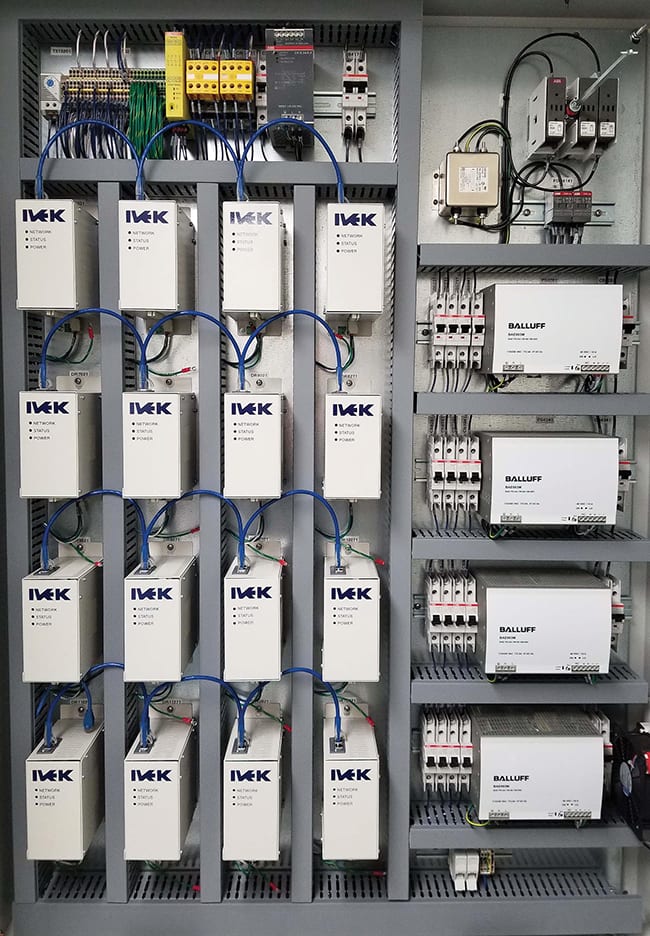
Figure 3. IVEK’s Digispense 4000 programmable liquid dispensing system enables precise and repeatable fluid dispensing volumes at rates of 2 nL/s to 300 mL/s
IVEK
Likewise, AW-Lake Company (Oak Creek, Wis.; www.aw-lake.com) offers smart batch controllers, such as the MX 9000, that can “learn” the process in order to get the most accurate volume possible (Figure 4). “The controllers gage how long it takes for the valves to open and close and adjust accordingly,” says Mark Iverson, general manager with AW-Lake. “For example, if the processor is doing a 50-gallon batch, our batch counter will count up to 49 gallons and will close the high-flow valve and switch to the low-flow valve from 49 to 50 gallons and then close the low-flow valve. If the controller sees that the dose was over by 0.1 gallons, it will recognize this and adjust until it reaches the precise volume. This intelligence helps achieve accuracy and repeatability in the process.”
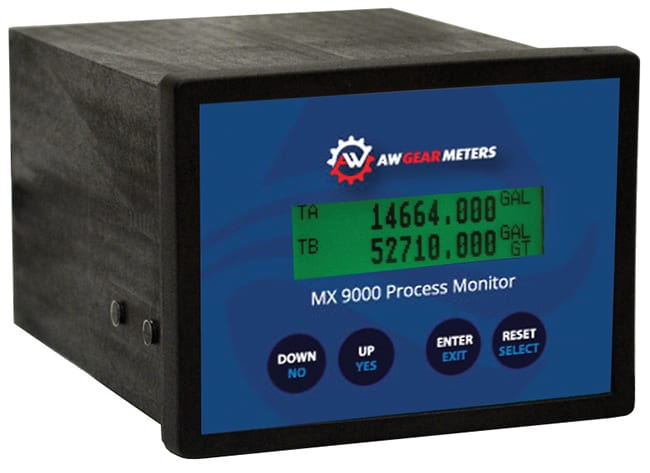
Figure 4. AW-Lake provides smart batch controllers, such as the MX 9000, that can “learn” the process in order to get the most accurate volume possible
AW-Lake
EPIC’s Sipes says these smarter, more automated pieces of equipment are coming together to improve the accuracy, repeatability and reliability of liquid dosing. “Better control can help minimize waste and create repeatability and consistency by taking error out of the equation,” he says. “The industrial internet of things (IIoT) and real-time data and diagnostics are starting to be deployed in liquid dosing applications, where, with the right sensors, instrumentation and equipment, the control system can watch a system perform and run. It can use artificial intelligence to learn what are normal operating conditions and what are not. Processors can collect those data and realize when preventive maintenance is needed base on operational history. Not only does this optimize the liquid-dosing application, but overall it improves uptime and profitability of the plant.”
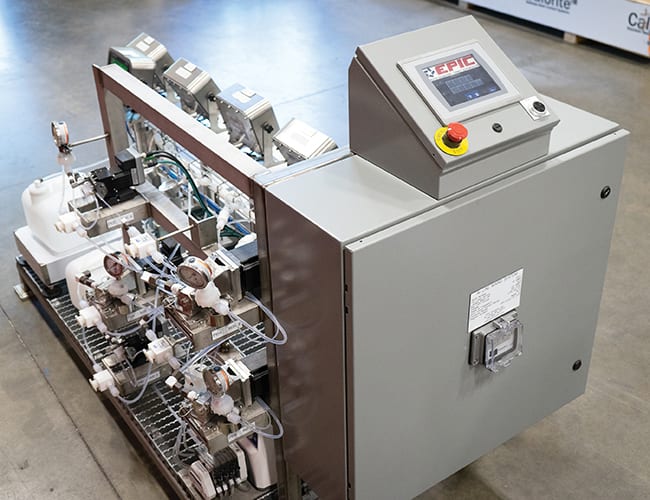
Figure 5. Many processors are unsure about inline blending because they don’t want to risk investing in equipment and find that it won’t work in their application. The demo-scale skid offered by EPIC gives them the confidence to move to a production-scale system if that is appropriate
EPIC
Note: For more technical information about metering pumps, see, “A Primer on Reciprocation Metering Pump Technologies,” Chem. Eng. 2019, pp. 43–49; www.chemengonline.com/primer-reciprocating-metering-pump-technologies.