BMW Group has announced plans for a new pilot plant that will produce lithium-ion battery (LIB) cells. With this plant, the company is taking the next logical step in penetrating all aspects of the battery cell value chain: from selection of materials, to battery cell composition and design, all the way to near-standard production and recycling. This will lay the foundation to create battery cells that take into account every aspect of sustainability. They will be used in vehicles beginning in 2025. Northvolt will produce the battery cells at its own gigafactory currently under construction in Skellefteå in northern Sweden from 2024 on. One Partner, Northvolt will obtain the energy needed to produce the battery cells exclusively from wind and hydroelectric power generated regionally in northern Sweden. The other partner, Umicore N.V. (Brussels, Belgium), will contribute to development of a sustainable battery cell in Europe. Recyclable cell design is a consistent focus from the very beginning of battery cell development. Faced with rapidly growing demand for battery cells, recycling of battery components at the end of their lifecycle and extensive reuse of raw materials will be key to closing the materials loop in the best way possible.
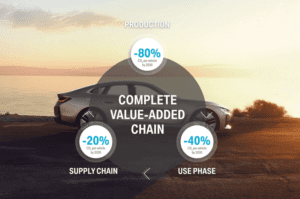
BMW has outlined some of its sustainability goals, with a special focus on raw materials and recycling (Source: BMW)
The circular economy plays a particularly crucial role when it comes to high-voltage batteries for electrified vehicles, which use a number of critical raw materials. Although the European Union currently requires a recycling rate of only 50 percent for high-voltage batteries, the BMW Group has partnered with German recycling specialist Duesenfeld to develop a method that can achieve a recycling rate of up to 96 percent – including graphite and electrolytes. The BMW Group already takes back all used BMW high-voltage batteries worldwide – even though there is no legal requirement to do so. Before recycling comes second-life usage at battery storage farms like the one at BMW Group Plant Leipzig.
The BMW Group is also piloting digital tools all the way to blockchain technology to track and verify global flows of goods. The PartChain project, for instance, enables tamper-proof and consistently verifiable collection of data in the supply chain. Going forward, critical raw materials, in particular, could be tracked all the way from mine to smelter.
The underlying flow of resources needs to change to improve overall sustainability. By making the recycling chain more transparent, the BMW Group aims to create high-quality secondary material and enable itself to track actual further use of raw materials in the cycle. the BMW Group plans to increase the share of secondary material in its vehicles significantly by 2030 – and is also exploring very far-reaching scenarios. Secondary material reduces CO2 emissions substantially compared to primary materials: by roughly factor 4-6 for aluminum and factor 2-3 for cobalt, nickel and lithium. Minimizing the amount of new extraction needed is also essential to conserve resources and reduce the potential for conflict – especially for critical raw materials.