Blending and segregation are two opposite and competing processes in solids handling that ideally fit the expression “two sides of the same coin.” But, if you think about it, coins have three sides and sampling completes the idiomatic expression perfectly. Blending is a necessary and essential process operation widely employed in many industries and materials, from nano-scale powders to run-of-mine ores. Segregation is almost always an unwanted consequence of handling operations that reverses the blending process or creates a need for blending where it might not otherwise be necessary if it were not for the effects of segregation. Sampling is the vitally important tool for measuring and quantifying a blend, understanding the sources and effects of segregation and for troubleshooting problems.
Blending
Blending is the process of combining two or more materials to achieve a combined product. The mixture may be a combination of dissimilar materials such as cement, sand and aggregate to make concrete; or cereal flakes, raisins, nuts and marshmallows to make breakfast cereal. A blend may also be a combination of chemically similar particles blended to create a uniform mixture of particle sizes, or another property such as color, flavor, melt index and so on. Blending bulk solids can be achieved in many ways including batch and continuous methods and with a wide variety of equipment, covering the range from extremely low intensity blending with gravity recirculation or layering components onto a belt, to high intensity blending with high-speed, high specific-horsepower blenders.
All of the various equipment and processes for blending solids rely on three principal mechanisms for achieving a blend: convection, diffusion and shear.
Convection.Convection is the transfer of a collection of particles from one location to another. This can occur as a result of material cascading in a tumble blender, material moving against the blade of a ribbon or paddle blender or as a result of gas pressure pulses in a pneumatic blender.
Diffusion.Diffusion is the random redistribution of particles that occurs as a result of increased particle mobility. Increased mobility typically occurs when the bulk density of the material is decreased sufficiently to allow individual particles to move relative to one another. Fluidization in fluidized bed reactors or granulators results in diffusion. Mechanical blenders move collections of particles by convection, but when the speed of the agitator is sufficient to locally fluidize material, diffusion occurs. Tumble blenders, continuous screw blenders and agitated blenders also provide opportunities for diffusion where material is cascading or in free-fall.
Shear. The definition of shear as it applies to solids blending is sometimes misunderstood. Shear occurs in a flowing granular solid as a result of a velocity gradient, and can develop as either a discontinuous shear (for instance, a shear or slip plane) or as a continuous gradient of velocity. In either case there can be some overlap in what could be called shear and what might be characterized as convection. The important difference, at least as it applies to solids blending, is in the intensity. Shear planes that develop in gravity blending or in a tumble blender or screw blender will achieve blending predominantly by a convective process. Shear in a high-speed mixer will have a different end result in that it will be much more effective in breaking up agglomerates of fine powders and distributing small-particle-size material with high surface activity.
Figure 1 is a cross section view through a bin showing the displacement of material as it flows. The pattern shows how the faster velocity in the center displaces material relative to the slower material at the walls. This displacement pattern can be described as shear deformation, but the blending that occurs is caused by convection of collections of material from the central part of the bin that reach the outlet sooner than material near the wall. If material withdrawn from the bin is circulated back to the top, the discreet fill pattern that was placed into the bin will be smeared and homogenized, and some degree of blending will be achieved after several recirculations [ 1].
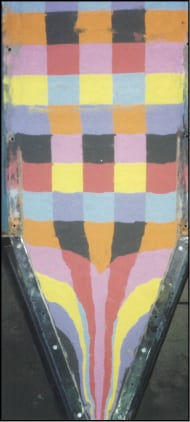
In a high-speed agitated blender, shear occurs with significantly higher intensity near the agitator but affects a relatively small volume of material. The high-intensity shear can break agglomerates, plate fine particles onto the surface of larger particles and redistribute particles with much higher intensity, causing better diffusion of small particles that may adhere to themselves or other particles. Ideally, the convective component of blending in this type of blender brings all of the material in the blender into the high shear zones.
Blend quality
In casual conversation, terms such as “uniform blend”, “homogenous mixture”, and “well blended” are often used without quantifying what they mean. In the heavily scrutinized pharmaceutical industry, regulations and guidelines dictate specific and often rigorous methodology for quantifying the uniformity of a mixture. Food and other consumer products must also meet trade regulations for delivering the stated quantity of product and composition of ingredients. Quantifying the structure of a blend requires defining not only the composition (for instance, the proportion of each component and allowable variation) but also the quantity of material that is to be measured. The compositional requirement of a blend is usually well known because it is either the entire objective of the process to produce a particular mixture, such as a pharmaceutical tablet or box of cereal, or it is an intermediate mixture that has well defined requirements. Determining the amount of material to measure is sometimes less clear, and may be different depending on who is answering the question. In pharmaceutical applications the answer is clear in that it is almost always based on the unit dose of the blend that makes up the final tablet.
In other applications the sample size subjected to scrutiny is not as clear cut. Take, for example, a box of cereal. In one specific example a manufacturer produced a cereal with a cereal particle and a marshmallow candy particle. The packaging line filled boxes from a series of conveyors that fed a mixture of the two components into a gravimetric packaging machine that dispensed the required weight of the blend into each package. The two components of the mixture were of similar size and density and the only blending that occurred was in the handling system along several conveyors and in a surge hopper. Each component was metered onto the conveyor system at the correct ratio, but there was not a discreet blending process. The manufacturing plants fine tuned their systems to get an acceptable mixture into each box.
In this case, each box was always within weight tolerance for the stated package quantity, but there was no direct control of the ratio of the two components in any box. In an effort to improve quality, a new packaging line was installed that handled each component individually up to the packaging head where each component was weighed in a series of weigh hoppers, and then each box was filled from several hoppers of each component, selected by the packaging system controller, to control both the proportion of each component and the total weight in a box. This would seem an ideal solution since it would guarantee both accurate package weight and composition. From the producers point of view, they had improved quality by insuring that every package met their quality standard.
However, to everyone’s surprise, consumer complaints from packages produced at this plant went up. What the plant had gained in compositional accuracy they had sacrificed in uniformity. Consumers found that individual bowls of cereal poured from the new packages had much wider variations of the two components than boxes filled from the old filling line. The new filling line had given up control of blending, even though the blending in the old system was very “low tech”. The new system allowed only about one second from the time the ingredients were separate until they were combined in the package. There was very little opportunity to do any blending, and the result was that some boxes were well blended while others were segregated. From the manufacturers point of view, they had “improved quality” and were taking responsibility for what they could control to the highest degree of precision, but they were not controlling the sample size of interest to consumers.
Random blend. The simplified case of blending two different ingredients that do not have significant bonding or other interactions is often referred to as a random blend. In a random blend, all individual particles are free to move relative to each other, and particle bonding is very weak or does not occur. Particles that form random blends can be easy to blend, because the particles move easily relative to one another, but that also means that they can readily separate from each other and collect in zones of similar particles when forces such as gravity, airflow, or vibration act on the blend. This process is referred to as segregation. Random blends are never perfect, and even in the best-blended state there will be random variations in concentrations of components.
Ideal random blends are uncommon in most industrial applications, although the cereal example described above comes close. In most dry blending applications, particles have some tendency to interact with one another by way of chemical, molecular, physical, or other means such that individual particles can agglomerate, coat or bond to one another. When particle interaction occurs, the blend is referred to as an ordered, structured, or interactive blend. In an ideal world, this type of blending process could create new particles, each consisting of the combined individual ingredients. A perfect particle created in this blender would consist of the desired ratio of each ingredient. This concept of combining ingredients to create new, chemically homogeneous particles is one of the primary objectives of wet and dry granulation processes. In most industrial blending processes, the reality is somewhere between a random blend and an ordered blend. Some particles of the blend may have very little tendency to interact while other blend components may have significant interaction.
![]() |
![]() |
![]() |
![]() |
![]() |
Segregation
Segregation is the separation of particles that have identifiable differences. By definition, identical particles cannot segregate. Segregation can be driven by many forces including gravity, electrostatic forces, fluid drag forces and elastic forces.
Sifting. The most prevalent type of segregation is sifting, which results in separation by particle size. Sifting segregation occurs to some degree in virtually every industry that handles bulk solids. Sifting will occur in mixtures of different size particles when particles are sufficiently large so that surface forces are weak relative to gravity (usually larger than 100 microns), when particles have mobility relative to one another (in other words, they do not adhere to each other) and when there is some mechanism to allow particles to move relative to one another. Collections of different size particles will not spontaneously segregate when at rest, but will often readily segregate when allowed to move in many common, industrial handling processes.
Figure 2 shows an example of sifting segregation that occurs when a mixture containing a range of particle sizes is allowed to form a pile. Smaller particles sift between larger particles as each layer of material slides along the pile surface. As the pile builds up, the finer fraction deposits preferentially near the center and coarser fraction near the edges.
A blend of perfect structured particles of identical size will not segregate after discharge from the blender. However, if there are size differences between the particles, then segregation by size may occur. Even if all the particles are chemically homogeneous, this segregation may cause problems because it may affect other blend properties, such as solubility or bulk density. There are many examples where this type of segregation is important, such as with spray-dried laundry detergent and food products, and other natural materials such as clay cat litter, coal and other mineral materials. In these examples the particles vary in size, but are virtually identical from a chemical standpoint.
In many other industrial-blending applications, particles not only differ in size, but also in chemical composition. And in most cases, particles of different size also have different chemical composition, so sifting segregation not only results in physical property differences associated with size distribution, such as bulk density and fluidization behavior, but also differences in chemical composition.
Fluidization segregation and particle entrainment. Other common mechanisms of segregation that act primarily on particle size are fluidization segregation and particle entrainment or dusting segregation. Fluidization segregation occurs where gas movement through a bed of solids causes finer, lighter particles to rise to the top surface of a fluidized blend of powder, while the larger, heavier particles concentrate at the bottom of the bed. Particle entrainment or dusting segregation occurs when fine particles in a blend are carried by air currents (such as during transfer of a blend into a container) and then settle preferentially at the container walls.
Sampling
Sampling is essential in determining the state of the blend in a blender, in downstream equipment or in the final delivered product. Samples are analyzed to measure the variables of interest to the application, such as particle size, chemical composition, pH, dissolution rate, color and so on. The overall average of the sample results represents the average composition of the blend. Variations between samples provide a measure of blend uniformity. Variability can be expressed by statistical measures, such as standard deviation, coefficient of variation, or relative standard deviation, as well as other measures [ 2].
The single most important rule of sampling is to collect a sample that accurately represents the state of the blend at the point where it is sampled. In many industrial processes this is a significant challenge due to either the difficulty of getting a sample at the desired location or because of the potential for sampling error that is introduced by the sampling method. The two “golden rules” of sampling are to always collect a full stream sample, and always collect a sample while it is moving [ 3].
In the case of the cereal example given above, sampling is easy because the sample is either a whole box of cereal or individual servings poured from the box. In either case the sample is easy to get and it is possible to analyze the entire sample. For other processes, significant challenges can prevent the use of good sampling techniques. In an example involving limestone at a circulating fluidized-bed boiler, the size distribution of the limestone used for fluegas desulfurization came into question. This became a critically important question because the plant could not meet emission regulations above about 50% output, and the blame was falling on the size distribution of the limestone produced by the onsite preparation plant. The plant produced about 50 ton/h of limestone, and to get a meaningful sample was not a trivial task. To satisfy all parties involved, the plant had to modify its chute systems to put in large diverter gates and position several operators to coordinate the collection of simultaneous full-stream samples in 55-gal drum quantities.
Samples of this size pose another challenge in analysis. Usually it is not practical or convenient to analyze such large sample quantities, so samples must be reduced or split. Simply grabbing a small sample from a large sample container can introduce significant sampling error, especially if sifting segregation can occur. The preferred method of splitting samples is to use a spin riffler, which can divide a sample into a number of smaller splits, usually from 6 to 16 divisions. Spin rifflers are capable of providing a high degree of uniformity between the individual sub-samples.
Another challenging task is sampling from a static bed in a blender. Clearly these samples cannot be collected while the material is moving, so some means of getting a meaningful sample must be used. Simply scooping material from the top surface is insufficient for many reasons, including particle segregation, which could make the top surface significantly different from material deeper in the bed. A sampling thief is often used to collect samples from a stationary bed.
A sampling thief is a probe that can be inserted into a bed of material to collect a sample from below the surface. Many designs exist, but in their basic form, they consist of a rod, frequently with a pointed tip. The rod has cavities cut into it along its length which are covered by a tube that fits closely over the rod and has openings that correspond to the cavities in the rod. The tube can be rotated to cover the cavities or open them. When the rod is inserted into the bed of material, and the tube rotated to exposed the cavities, blended material will fill the cavities, which can then be covered again and withdrawn. Thief sampling has been used extensively and studied thoroughly. While it remains the only practical way to collect samples from all positions in a static bed, it has been shown to have biases and limitations that can cause sampling error. These can come from properties of the blend and from operator technique. Some typical sources of error include local segregation as material fills the cavities, smearing as the thief is inserted into the bed, and preferential adhesion or repulsion of some components of the blend.
Sampling will always introduce some degree of error, which can affect the sampling results in three ways. Perhaps the most common effect is that sampling increases the variability of samples, which produces data showing that the uniformity of the blend is worse than it actually is. In some cases, this presumed “fact” is used to suggest that a blend is actually better than what the sampling data shows.
Sampling error can also produce bias, or an overall shift in the results, indicating that the measured average from the collected samples is higher or lower than the known blend composition. This type of error can be confounding because people often jump to the conclusion that there is “missing” or “extra” material, somehow. It is more likely that one component adheres to, or is repelled by, the thief, or preferential flow of one component into the thief shifts the sample composition. Another possibility is that a sample is collected from an inappropriate location, such as a known dead zone in the blender that may be holding the “missing” material. When this type of error is observed it usually requires additional detective work to determine the cause of the bias.
Sampling devices can also produce samples that show lower variability than are actually present due to smearing of the sample. This type of error is often referred to as “counterfeiting.” Counterfeiting is hard to detect because it may produce results that show blending is good.
The purpose of sampling is to accurately quantify the state of a blend or uncover blend quality issues, not to mask or overlook suspected problems. Samples should be intentionally collected from suspected regions where the blend may be less uniform, not just from the middle of the blender, or during the “best” part of a production run. Fringe regions may include the surface of the material, regions where the material may have been stagnant during blending and at the beginning and end of discharge from a batch bin.
Edited by Rebekkah Marshall
References
1. Carson, J.W., and Royal, T.A., Techniques of in-bin blending, IMechE, C418/056, 1991.
2. Fan, L.T., Chen, S.J., and Watson, C.A. Solids mixing. Industrial Eng. Chem. 62, 53–69, July 1970.
3. Allan, T. “Particle Size Measurement”, 2nd Ed., Chapman & Hall Ltd., London, 1975.
Author

Thomas G. Troxel is a vice president at Jenike & Johanson, Inc. (3485 Empresa Dr., San Luis Obispo, CA 93401; Phone: 805-541-0901; Email: tgtroxel@jenike.com). He holds a B.S. in Engineering Science (ES) from California Polytechnic State University (Cal Poly) in San Luis Obispo. After graduating as the Outstanding Senior in the ES program in 1981, he worked at General Dynamics Co. He then helped to open Jenike & Johanson’s San Luis Obispo, California facility in 1982. Troxel has been intimately involved in many aspects of the firm’s consulting and research activities on a wide range of projects including flow properties testing, modeling, blending, pneumatic conveying and fluidization. He has been a major force behind the firm’s expansion in mechanical design engineering and custom-built equipment.