This column is based on “Bio-based Adipic Acid Production from Glucose – Cost Analysis,” a report published by Intratec. It can be found at: www.intratec.us/analysis/adipic-acid-production-cost.
Adipic acid is one of the most commercially important aliphatic dicarboxylic acids. It is produced on a large scale primarily to supply the nylon 6,6 production chain. Other applications include the manufacture of coatings, synthetic lubricants, fibers, plastics, plasticizers and polyurethane resins.
The process
In the process described in the following paragraphs, adipic acid is produced from glucose via a two-step catalytic process (Figure 1).
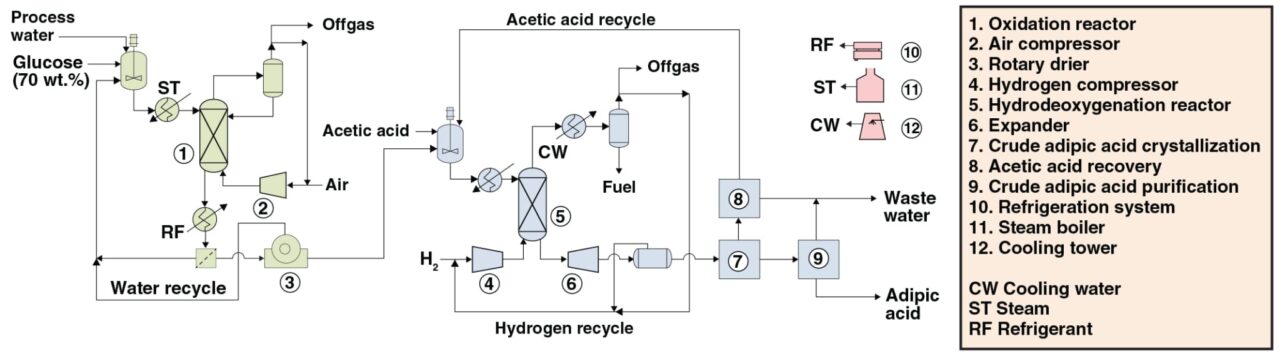
Figure 1. The production of bio-based adipic acid from glucose via a two-step catalytic process is shown here
Glucaric acid synthesis. A glucose solution is mixed with process water and heated before being fed to the oxidation reactor. Oxygen is supplied to the reaction by feeding compressed air to the bottom of the reactor. The overhead from the reactor is fed to a knock-out drum, a liquid stream is recycled to the reactor and most of the recovered gaseous material is recycled to the air compressor. The reactor’s bottoms product is cooled and filtered, and glucaric acid is recovered as a solid. It is then fed to rotary dryers to remove water. Dry glucaric acid is conveyed to the hydrodeoxygenation feed mixer.
Adipic acid synthesis. Glucaric acid is dissolved in acetic acid and heated before being fed to the hydrodeoxygenation reactor. Glucaric acid reacts with hydrogen at high pressure, yielding adipic acid and water. The reactor’s overhead stream, a hydrogen-rich stream, is partially condensed to remove light byproducts, which are burned as fuel. The gaseous stream is recycled to the hydrogen compressor. The reactor’s product stream is expanded in a turbo generator, producing electricity. Its low-pressure output is directed to a knock-out drum in which a hydrogen-rich gaseous phase is recovered and recycled to the hydrogen compressor and a liquid phase, composed mostly of acetic acid, water and adipic acid, is directed to a crystallizer. The output from this crude crystallizer is then filtered and fed to a rotary dryer to recover crude adipic acid. The mother liquor from the filter and the acetic acid evaporated from the dryer are mixed and fed to an extractive distillation system to remove the water content from the acetic acid so it can be recycled to the hydrodeoxygenation feed mixer. Crude adipic acid must still be dissolved in water and then subjected to further crystallization, filtering and drying to reach fiber-grade purity.
Adipic acid production pathways
Adipic acid production has been predominantly based on cyclohexane and, to a lesser extent, phenol. Shifts in the hydrocarbon market and growing environmental concerns have resulted in the development of alternative production routes for adipic acid from renewable resources, such as sugar and fatty acids (Figure 2).
Economic performance
Using data from Q3 2013, variable costs (raw materials and utilities) for manufacturing fiber-grade adipic acid from glucose in the U.S. are estimated to be around $1,100/ton of product, accounting for a significant portion of the production costs.
Edited by Scott Jenkins
Editor’s note: The content for this column is supplied by Intratec Solutions LLC (Houston; www.intratec.us) and edited by Chemical Engineering. The analyses and models presented are prepared on the basis of publicly available and non-confidential information. The content represents the opinions of Intratec only. More information about the methodology for preparing analysis can be found, along with terms of use, at www.intratec.us/che.