Use the strategies discussed here to maximize the yields of solid products from batch drying vessels
Successfully drying a wet solid in a drying vessel does not complete the operation — the dry solids must be removed from the vessel. This step often presents challenges, because it can be difficult to fully empty drying vessels when leftover solid material remains on the interior surfaces. For batch drying processes where the residues can be dissolved into the subsequent drying run, the problem of incomplete emptying may not be particularly acute. However, for processes where the solid residues must be rinsed out of the vessel’s interior prior to the next drying batch, and the rinse is lost, maximizing the yield of the dryer is of great importance. This article provides information on measures that improve and maximize the yield in batch drying processes for fine chemicals and active pharmaceutical ingredients (APIs).
Batch drying processes
In most liquid-solid-separation processes, thermal evaporation (in a vacuum contact dryer) is often the follow up step to mechanical dewatering, in order to achieve the best “dryness” result. During any drying process, all additives and solvents must be removed from the solid materials without changing the original chemical composition of the solid. In essence, there should be no changes to the molecular structure of the solids during the drying process, and no chemical derivatives should be formed due to the drying process.
A vacuum contact dryer is built to evaporate solvents from a solid by using temperature, vacuum and mechanical fluidization by agitation. The degree of residual moisture in the finished product is related to the enthalpy of the solvents, the effectiveness of the mixing and time. The degree of residual dry powders left after discharge of the vessel is strictly product related.
Almost all batch drying processes consist of the process steps mentioned in Figure 1. Whether the steps are performed in a non-agitated tray or in an agitated vessel, the concept of evaporation and re-condensing and collecting the solvents is quite the same. When it comes to maximum yield, it is important to focus on all aspects of the drying process, not only on discharge.
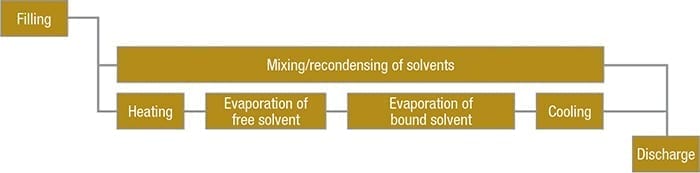
Figure 1. The schematic shows process steps common to many batch drying operations
Each process step has issues that require special attention. Discharge of solids is demanding — while fluids or suspensions drain well from a vertical vessel, draining a dry powder is a challenge. Residues left after draining are lost in most instances.
Maximum yield after discharge is important for the cost balance of the drying system. In a situation where a single product is processed in a vessel, leaving residues after discharge for the next drying campaign may be permissible. However, in a typical process for producing pharmaceuticals or fine chemicals, cross-contamination of different products is not allowed (Figure 2).
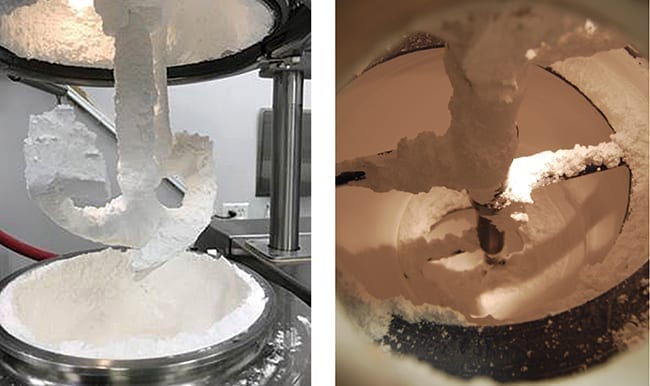
Figure 2. Residues of solid materials left on interior surfaces after drying processes can be significant
Vacuum dryer design
The majority of commercially available vacuum contact dryers are built with the same general features: a jacketed vessel — either horizontally or vertically oriented — with a wall-wiping agitator. Vertical (upright) solids dryers have the advantage of being aided by gravity in the natural, top-to-bottom flow of products. These dryrers have the following characteristics:
- Upright cylindrical vessel with a filling-height-to-diameter ratio designed for bulk mixing
- Cone-shaped bottom to support the outflow of solids
- Jacketed to suit the selected heating system (Figure 3)
- Top-entry agitator, designed for solids applications (re-starting in settled solids)
- Valves and safety applications to operate as a pressure vessel
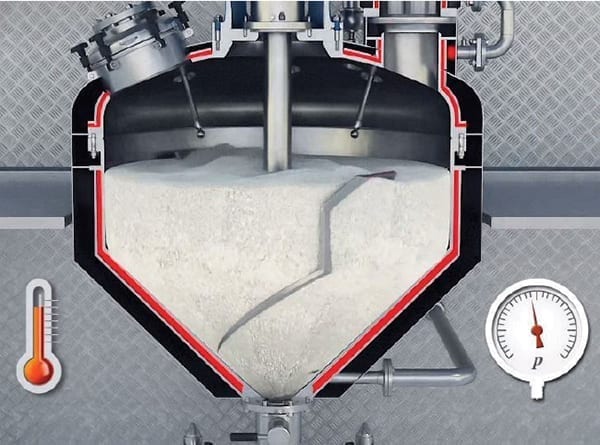
Figure 3. This cutaway shows surface heating
Whether the wet product is fed by gravity from the top of the vessel, or is transferred by powder transport systems, depends on the process. In both cases, the feed point/system has to be designed to avoid excessive splashing or dust formation when entering the vessel. Unguided filling might lead to accumulation of product on impeller arms or slow rotating shaft areas. Guiding vanes or funnels are recommended.
Once the solids temperature during a drying process is equal to the heating temperature, this indicates energy is no longer being used for the evaporation of solvents, so the product is effectively dry. Safety considerations might not allow the discharge of a hot solid, so cooling the product prior to discharge is mandatory. This can be achieved by changing the heating system to cooling mode.
Scaleup
Scaling up a drying process requires both small-scale testing capabilities and scaleup experience. Once a product is successfully dried at a 25-, 50- or 100-L scale, scaleup rules are in effect to predict the following parameters:
- Drying time
- Solvent load, energy demand
- Residues after discharge
- Particle size changes due to shear on the product
- Wear of the agitator parts due to exposure to the product
Scaleup works best when the trials have been carried out under physical parameters (including pressure and temperature) that are identical to the full-scale process. If this is not possible, correction factors have to be applied to the scaleup formula. From a small-scale test, engineers can predict the formation of residues in the full-scale vessel can be predicted.
Tools to improve yields
When they are supposed to leave the vessel, solids often do not behave in ways that make it easy for process operators to fully empty the chamber, as the examples show (Figure 2). However, certain tools and strategies are available to help improve the discharge effect from vertical vessels and increase the yield.
Vessel geometry. The vessel geometry is generally designed and manufactured at the vendors’ discretion. With respect to the mixing behavior, a filling-height-to-diameter ratio of 0.8 to 1.0 works best. For maximizing yields, minimizing the wetted surfaces is an important strategy. Table 1 shows sample data for drying vessels of three different geometries.
A flat-bottom vessel represents the design with the least wetted surface for a specific volume. Due to the almost perfect shape with respect to mixing, the mixing of the solids is based on dynamic operation with a minimum blade surface. Vessels with a filling-height-to-diameter ratios above 1.8 (for example, a helix-type agitator) naturally have more wetted surface inside the vessel, but its slim cone bottom design improves outflow. Finally, typical “spherical shape dryers” combine both the short shape and the cone bottom design for best results in yield.
Using the vessel as a contact dryer, it is mandatory to reduce cold spots during the drying process. Unheated surfaces will result in condensate formation during the drying step. Agitator shafts are made of solid bar. In low-temperature drying processes, this shaft will stay cooler relative to the vessel and product temperature, leading to condensation. Condensate on these surfaces will attract dust to form a cake. This will happen in the non-agitated section of the vessel (for example, the shaft, top dome, nozzles and filter bay). In order to improve the yield, maximum surface and shaft heating is advised.
Impeller clearances. Solids dryers require an impeller system that both moves the bulk and “wipes” the walls. Since scraper designs have an extremely limited lifetime in solids applications, they cannot be applied, so tiny impeller-to-wall clearances are needed. The impeller must be designed with a small wall clearance to prevent the buildup of layers on the wall, and to improve heat transfer (if required) and yield. Table 2 shows typical impeller-to-wall clearances for various types of solid products.
Wetted surfaces quality. Even free-flowing solids, such as crystalline sugar, change to “sticky” when wetted. Therefore, the surface roughness selection should not be based on the final appearance of the solids, but should consider the overall process. For milling and processing tasks of coarse products (such as coffee beans, cocoa nibs, almonds, nuts, pistachios), where residues are accepted, the mill-finish wetted surfaces are qualified. How much material creates a cross-contamination hazard? For example, does only one bean or nut left create a cross-contamination hazard? In food-grade and pharmaceutical applications, polish is advised to reduce leftovers.
Agitator impeller design. Designing for maximum yield is a balance between wide blades for effective (low-shear) mixing and product buildup on the wide blade surfaces. Even solid granules with excellent flow properties will accumulate on a horizontal blade even when the shaft is spinning. A pitch angle of about 45 deg (retrieved anchor) or tilted blades (helix) are designed to reduce solid-layer buildup on the blade top (Figure 4). Always pay attention to the lower side of the blades. Static electricity or sticky products “hide” on the lower side and “ignore” the presence of gravity. Special spacer designs are available to fill in “dead zones” where solids may accumulate.
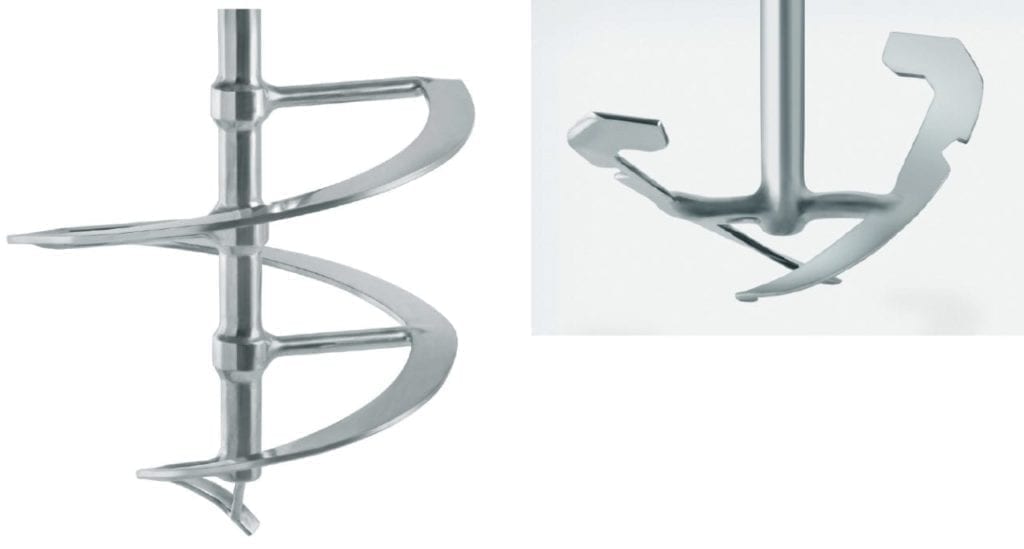
Figure 4. The photos show helix-type impeller (left) versus a retrieved-anchor type (above)
Agitator speeds and direction of rotation. Agitation in a solids bed is a low-speed, low-shear business. Shaft speeds are designed to gently move the bulk solids without excessive wear and particle size reduction. At the time of discharge, the bridge-breaking effect of the impeller is mandatory. The main pumping action of the solids impellers is “up”. This upward motion is counterproductive when the vessel is close to empty. At this point — under consideration of torque limitations — reversing the direction of the impeller is mandatory to have a full discharge of the solids.
Speeding up the agitators to elevated speeds (higher rpm) will improve product discharge. Influenced by the centrifugal forces, solid layers on the blades are thrown outward. The more coarse the product, the more effective the elevated speed will be. Drive-speed restrictions, however, do limit this measure. For scaleup from smaller to higher volumes, the shaft´s rotational speed should be constant (not the tip speed).
Process. Time is money for batch drying processes, and fast mixing or drying is the goal. If the fast process results in excessive crust formation and contamination of difficult-to-reach areas, a process change in favor of slower drying, but less contamination (less yield), is advised.
A clever vacuum or lower temperature regime can help to reduce flash evaporation and dust formation. Filter port sizes should be designed for low gas-flow speeds.
Even with a perfectly designed vessel and process, 100% discharge of the dried solids might be out of reach. In this case, a wet cleaning/rinsing process has to be added. The liquid rinsing system will have the capability of removing solids from a vessel without residues.
Jet pulse injection. Removing solids layers via jet pulse lances has shown effectiveness in very small-scale vessels (25 to 50 L). Larger vessel trials did show that a typical 3 bars pressure lance will have a limited effect. High-pressure gas jets, however, increase dust explosion hazards due to their dense local energy input.
Testing and scaleup. There is good news about efforts to maximize yield and process scaleup. Generally, observations made at small scale will translate directly at large scale (Table 3). Effects seen at small scales (25- to 100-L test) can be directly applied to the full commercial scale. A product layer of 0.25 in. on the blade surface and on the vessel dome at small scale will be 0.25 in. at the full scale. Where such an example layer results in a yield of 80% in the small scale, it will convert to 95% at the full scale — considering the wetted-surface-to-filling ratio of the small scale compared to the full scale.
Concluding remarks
Products change when processed and show highly individual properties, so this article cannot elaborate on flow behaviors. This must be done in individual trials. Process equipment should offer flexibility to maximize yield. Small-scale testing is mandatory to predict discharge effects, and sometimes even reverse operation will force a paste out of the reactor without damage. Solid residues are often lost, and are sometimes a hazard. Process owners and equipment vendors should combine their product knowledge to improve yields in batch-drying process vessels.
Edited by Scott Jenkins
Author
Eberhard Tritschler is product manager for sales at Ekato Systems GmbH (Käppelemattweg 2, 79650 Schopfheim, Germany; Phone: +49-7622-6907-808; Email: [email protected]; Website: www.ekato.com). Tritschler has served in sales and application engineering at Ekato since 2005. Prior to that, he worked in several other Ekato divisions. Tritschler holds a bachelor’s degree in mechanical engineering from the Technical School of Engineering in Lörrach, Germany, and a degree in business administration from the HWK School in Schopfheim, Germany. Aside from business duties at Ekato, Tritschler also speaks at customer seminars, tradeshows and business schools. He has special expertise in the mechanical aspects of vacuum contact drying, as well as extractions and all-in-one reactions in batch-type mixing vessels.