In the quest to transform sugar and carbon dioxide into fumaric acid, an important intermediate for chemical production, in this case, using the bacterium Basfia succiniciproducens, BASF SE (Ludwigshafen, Germany) is collaborating with Saarland University, University of Marburg and the University of Kaiserslautern-Landau in a joint research project entitled FUMBIO (FUMarsäure BIObasiert). The bacterium, which was isolated in 2008 from the rumen of a Holstein cow, will be genetically modified by researchers so that it produces large quantities of bio-based fumaric acid, also known as fumarate, during fermentation. With this intermediate, BASF can make a wide range of products with a low carbon footprint, including additives for food and animal feed, starting materials for medication, or building blocks for polymers and detergents and formulators.
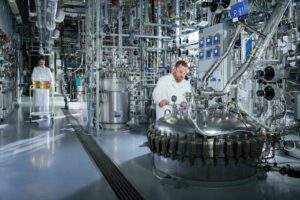
With the bacterium Basfia succiniciproducens, BASF would like to transform sugar and carbon dioxide into fumaric acid Fermenters, as seen see on this photo, will be used (Source: BASF)
“Together with our cooperation partners, we are taking a closer look at the fermentation process. We want to optimize it in such a way that the bacteria use renewable raw materials, such as sugar, and carbon dioxide to produce as much fumarate as possible,” says Dr. Barbara Navé, head of the FUMBIO project and responsible for the evaluation and coordination of new white biotechnology projects at BASF. The research project also focuses on the subsequent refinement of fumarate by enzymes – also known as bio-catalysis – into biodegradable industrial products.
Fumaric acid is very common in nature and is an intermediate product in many metabolic processes in humans, animals and plants. In the chemical industry, it has traditionally been produced primarily from fossil-based raw materials, such as crude oil. The FUMBIO research project will measure the CO2 footprint of fumarate made with biotechnology methods and compare this to petrochemical-based production. The cooperation partners expect the carbon footprint will be significantly lower – or even negative, thanks to the use of CO2 as a raw material.
The CO2 that the bacteria will use as a source of carbon, in addition to sugar, in the fermentation process will come from exhaust gas streams at chemical production plants. “Carbon dioxide is an important raw material for us in the chemical industry,” Navé explains. “If we recycle CO2 from industrial off-gas, this will help us to reduce emissions of this greenhouse gas and achieve our climate targets by 2050.”
Biotechnology processes, such as fermentation, in which microorganisms such as bacteria or fungi use CO2 as a building block for metabolic products, will also become increasingly important for the chemical industry in the future. “White biotechnology is an important tool that will enable us to offer our customers a wider range of bio-based products with a low carbon footprint.”
The FUMBIO project receives financial support from Germany’s Federal Ministry for Education and Research. In total, the Ministry is providing around €2.6 million to the project partners.