Onsite recycling proved cost-effective for an aerospace supplier. With real-time feedback and control, a new automation upgrade takes process efficiency to the next level
Throughout the chemical process industries (CPI), efficient and affordable approaches to wastewater treatment are of paramount importance. In particular, onsite water recycling can support the bottom line while furthering sustainability goals. Ion-exchange systems offer a proven, economically viable technology for recycling industrial wastewater with high levels of recovery. While the initial equipment costs of this approach can be significant, they are more than outweighed by the long-term economic and environmental benefits. At the same time, system designers are always seeking even greater cost-effectiveness. As Ethernet-enabled components become ever more sophisticated, automation can provide this crucial edge.
Building on success
In 2017, a manufacturer in the aerospace sector worked with Water Innovations, Inc. (San Diego, Calif.; www.waterinnovations.net) to develop an onsite system for closed-loop recycling of its plating rinsewater. For more on this project, read Cutting Cost and Waste with Rinsewater Recycling, Chem. Eng., May 2023, pp. 45–46. The company’s operations require a high volume of deionized water (DI) to rinse metal parts as they are cleaned, etched and electrolytically plated with specialized metal finishes. To address both their supply and treatment needs, Water Innovations designed and installed three different resin-based ion exchange systems as well as a bentonite reactant treatment system for the oiliest waste. GF Piping Systems (GF; Irvine, Calif.; www.gfps.com), a longtime project partner for Water Innovations, provided crucial components and expertise.
Overall, the manufacturer’s total wastewater management costs dropped by 80%, with a 60% reduction in treated effluent going to the sewer. The onsite recycling system furthermore yielded an abundant supply of DI water, with cost per gallon reduced by 70%. After only two years of operation, the company achieved return on its Water Innovations investment. Then, in 2023, Water Innovations saw the potential to build even further on this success.
For more than twenty years, Water Innovations systems have utilized “feed-forward” grain counting to trigger countercurrent regeneration just before the resin beds became exhausted — instead of just after. Countercurrent (or reverse-flow) regeneration provides efficiency advantages in and of itself, on the order of 50–60% versus co-current methods. This is because the regenerant solution comes into contact with the less-exhausted resin layers first, so that a lower quantity of solution is ultimately needed. In recent years, Water Innovations has assessed contaminant loading in rinsewater by measuring its conductivity, using sensors provided by GF. This additional sophistication (as opposed to simple assessment via pH) already cuts the amount of wastewater sent to treatment by as much as 20%. But now, the advent of an Ethernet-enabled actuator (Figure 1) from GF offered a chance to streamline the regeneration process with even greater efficacy.
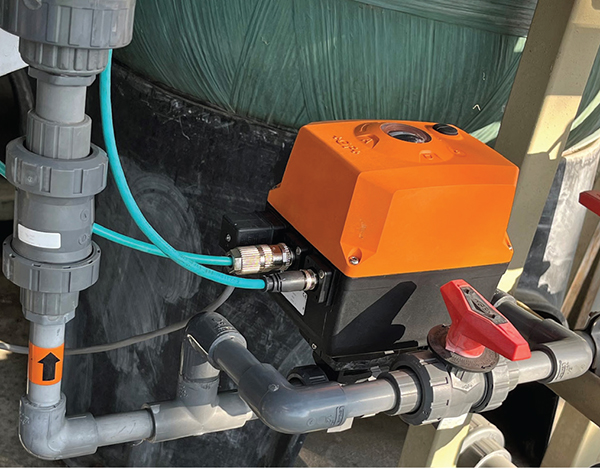
FIGURE 1. An automation upgrade using the EtherNet-equipped EA-25 electric actuator interface allowed an aerospace manufacturer to achieve greater efficiency for its onsite recycling process
As originally designed, the aerospace manufacturer’s Water Innovations system relied on GF Type 523 Metering Ball Valves, which have a 180-deg rotation V-notch design for greater resolution and linearity, to adjust the dosing of the regenerant solution. Operators would calculate the required chemical concentration and then manually adjust the valves to deliver the desired dose. Water Innovations designed an upgrade for the system, known as Optimized Regeneration Control (WI-ORC), in which the dosing would be monitored and adjusted automatically in real time. With automatic adjustments based on constant feedback, the time and materials required for regeneration could be minimized.
Real-rime precision cuts costs
As part of this upgrade, GF provided its newest electric actuator, the Type EA25-250, equipped with Ethernet/IP communications via M12 field connections. Other key components included GF’s 3-2823 conductivity sensors and 9950 dual-channel controller, providing an expanded conductivity range up to 800 mS/cm for measuring the individual chemical concentrations of the regenerant chemicals hydrochloric acid (HCl) and sodium hydroxide (NaOH).
In the upgraded system, automation serves to optimize the results. GF conductivity sensors monitor the concentrations of HCl and NaOH. The dual-channel transmitter sends the conductivity values to the WI-ORC system, where an algorithm calculates proportional-integral-derivative (PID) setpoints that can be transmitted to the electric actuator through its Ethernet/IP capability. The actuator and metering valve are thus continuously positioned to maintain an optimal chemical dose throughout the resin regeneration process. The Water Innovations control system is capable of continuously monitoring the actuator’s performance, including such parameters as valve position (%), cycle time, motor torque, total cycles and internal temperature, as well as providing detailed error flags. With the deployment of the web server, managers can externally configure the electric actuator’s open/closed end points, or select the desired color scheme for open and closed status (either red for closed and green for open or vice versa). The actuator can also receive firmware updates.
With the real-time precision of automation, the time required for resin regeneration has been cut by 10%. The amount of regeneration chemicals needed and the amount of regeneration wastewater sent to the municipal waste-treatment system have each been reduced by 10% as well. Factoring in the reduced outlay for chemicals and discharge fees, the upgrade is expected to achieve return on investment in just 15 months. Beyond the cost savings, the automated system’s performance is also more consistent, continuously providing high-quality water without dependence on the operator.
“We’re always looking for ways to fine-tune systems we’ve already built, even highly efficient ones. In this case, the Ethernet capability of GF’s new actuator let us take that next step,” said Steven Ward, managing partner at Water Innovations. With continual measurement and adjustment in real-time, the potential of automation to optimize process costs and outcomes has only just begun to be realized. ■
Edited by Mary Page Bailey
Photo courtesy of GF Piping Systems
Author
Rick Hines is the director of automation for GF Piping Systems’ U.S. Center of Excellence (9271 Jeronimo Rd., Irvine, CA 92618; Email: [email protected]). With over four decades of experience in the field of fluid handling, Hines is active in the effort to provide safe, clean and reliable water supplies to communities throughout the world.