Area electrical classification is a powerful tool for process safety. It is not, however, the only viable approach to a safe process
Electrically classifying an area is a long-standing safety measure in the petrochemical and related industries. It is also an area that is not taught in schools and most practitioners pick up as part of their on-the-job training. As a result, it is also an area prone to many misconceptions. While its application is always challenging, its application in a research environment is even more difficult. The need for constant process and equipment changes, the desire to modify and rearrange operations and equipment, the need to strike out in totally different areas all make flexibility a major requirement (Figure 1). And an electrically classified area is relatively restrictive in what can and can’t be done. So, unfailingly, research organizations look for alternative mitigative measures.
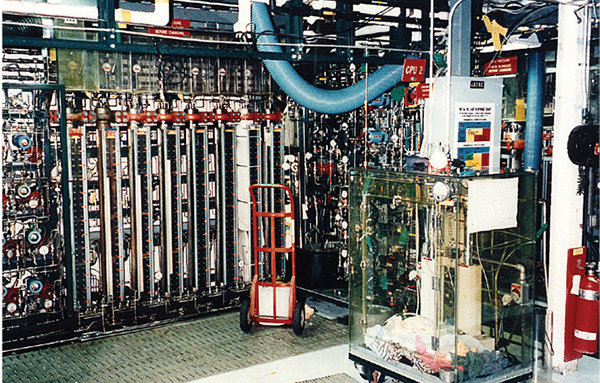
Figure 1. An electrically classified area, such as Class 1, Div. 2 for this pilot plant, can be relatively restrictive, especially when there are frequent process and equipment changes
Requirements
Do research operations involving flammable and combustible materials always require the organization to electrically classify the area?
NFPA [National Fire Protection Assn.] 70 The National Electric Code in 500.5(A) requires that “ Locations shall be classified depending on the properties of the flammable gas, flammable liquid–produced vapor, combustible liquid–produced vapors, combustible dusts, or fibers/flyings that could be present, and the likelihood that a flammable or combustible concentration or quantity is present.”
The U.S. Occupational Safety and Health Admin. (OSHA) in 1910.307(a)(1) uses similar language. OSHA 1910.119 considers electrical classification as a vital piece of process safety information that should be readily available but does not make it a mandatory requirement.
Many other NFPA codes require some specific areas to be electrically classified. NFPA 30 The Flammable and Combustible Liquids Code in Table 7.3.3 gives some specific guidance as to how some areas, like tank farms and vents, should be classified. However, 7.3.1 states that electrical equipment shall not “ constitute a source of ignition for any ignitible vapor that might be present under normal operation or because of a spill. Compliance with 7.3.2 through 7.3.7.1 shall be deemed as meeting the requirements of this section.” The word “deemed” is important here because it implies that if you follow the code guidance, you can assume you comply with ensuring that electrical equipment will not “ constitute a source of ignition for any ignitible vapor that might be present under normal operation or because of a spill” without much further analysis.
But what if you are willing to do that further hazard analysis and risk assessment? Can you use other mitigative measures? The answer is a resounding maybe.
NFPA 497 Recommended Practice for the Classification of Flammable Liquids, Gases, or Vapors and of Hazardous (Classified) Locations for Electrical Installations in Chemical Process Areas states three conditions are necessary for ignition of a flammable or combustible material in 4.3:
(1) A combustible material must be present.
(2) It must be mixed with air in the proportions required to produce an ignitible mixture.
(3) There must be a release of sufficient energy to ignite the mixture.
API 500 Recommended Practice for Classification of Locations for Electrical Installations at Petroleum Facilities Classified as Class I, Division 1 and Division 2 expands on these conditions in 4.1:
a) A flammable gas or vapor must be present. In classifying a particular location, the likelihood of the presence of a flammable gas or vapor is a significant factor in determining the division classification. The decision is based principally on whether the flammable mixture may be present (1) under normal conditions, or (2) only under abnormal conditions (including equipment breakdown).
b) The gas or vapor must be mixed with air or oxygen in the proportions and quantities required to produce a flammable or ignitable mixture. This condition is important in determining the limit or extent of the classified location. The quantity of the substance that might be liberated, its physical characteristics, the operating pressure, and the natural tendency of gases and vapors to disperse in the atmosphere should be considered.
c) The mixture must be ignited. When classifying locations, the potential source of ignition is understood to be an electrical installation or device operating at energy levels or at temperatures sufficient to cause ignition.
Neither API 500 and NFPA 497 are suggesting that area electrical classification is the only way to prevent a fire or explosion. Rather they say that if you follow their guidelines then, historically, you are usually safe from fires and explosions. They are recommending one way to stay safe, not the only way. If you can provide adequate mitigative measures to prevent one or more of the above three conditions from being present, then area electrical classification is not the only possible approach.
NFPA 497 is clear in 5.2 saying “ The decision to classify an area as hazardous is based on the possibility that an ignitible mixture could occur.” API 500 in section 6.1 echoes this guidance. “ The decision to classify a location is based on the probability that flammable gases or vapors may be present…. It is noted that the occurrence of flammable material liberation from some of the above apparatus is so infrequent and at such a small rate, that it is not necessary to consider it as a source or to classify adequately ventilated nonenclosed areas containing such apparatus.” If you provide mitigative measures to reduce the possibility that an ignitable mixture could occur to less than a credible possibility, then the area does not need to be electrically classified.
Realistic mitigation measures
The key to this is what mitigative measures can realistically be applied.
Limit the amounts. The first approach might be to limit the amount of flammable and combustible materials to a de minimisamount. While 44 mL of flammable liquid is enough to catch fire, the realistic amount of damage one shot glass of liquid can produce has not suggested that we electrically classify bars. Yet a bar involves open transfers, open containers, frangible containers, and a very high probability for spills and human error. Despite this, we know — from experience — that bars do not catch fire due to flammable and combustible liquid handling with any degree of frequency. While no code addresses how much flammable or combustible material is enough to be of concern, consider that pint, quart, and even gallon containers of flammable or combustible materials are sold, handled, and used in homes, businesses and stores with incredible frequency with relatively low consequences. Hence, I suggest that quantities of 1 gallon (~4 L) or less are probably small enough to be considered de minimis. Note, however, that when one talks about the quantity of flammable or combustible material present, one must include all the flammable or combustible material in the given area; not just an individual container. So, while I would not worry about a single 1-gal container of hexane in a laboratory, I would be more concerned if it were one of a dozen.
This limiting approach may be feasible for some research applications but, in most cases — particularly those handling flammable gases or utilities — it may not be very practical nor useful.
Ventilation. A second approach might be to provide so much ventilation that the flammable or combustible material is captured at the source and the extent of any ignitable area is negligible (Figure 2). Note that I carefully avoided the term “adequate ventilation”, which is used extensively in all the codes.
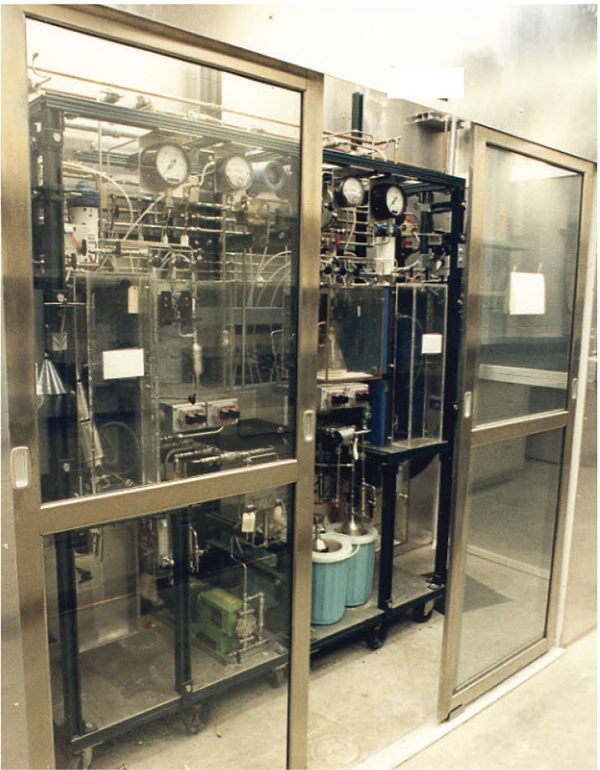
Figure 2. Ventilation is an important mitigation measure. This pilot plant is skid mounted, and can be easily moved into a hood
Adequate ventilation is defined in NFPA 30 section 17.1.1 as “a rate sufficient to maintain the concentration of vapors within the area at or below 25 percent of the lower flammable limit (LFL).” NFPA 497 in 3.3.1 defines it as:
A ventilation rate that affords six air changes per hour, 1 cfm per square foot of floor area (0.3 m3/min/m2), or other similar criterion that prevents the accumulation of significant quantities of vapor-air concentrations from exceeding 25 percent of the lower flammable limit (LFL).
API 500 in section 3.1.38 uses similar language:
Ventilation (natural or artificial) that is sufficient to prevent the accumulation of vapor-air or gas-air mixtures in concentrations above 25% of their lower flammable (explosive) limit, LFL (LEL).
API 500 expands upon this definition in section 6.3.2 where it gives practical guidance in this area. However, API 500 limits the use of ventilation, allowing ventilation to lower the electrical classification of a location from Division 1 to Division 2 but not be used to lower the electrical classification of a location from classified to unclassified.
Some organizations feel this guidance prohibits ventilation as a mitigative measure. I disagree. API 500 tacitly assumes that there is always a credible possibility of the presence of a flammable or combustible material in ignitable quantities in most areas of a petrochemical facility, a not unreasonable assumption. Hence using ventilation as a mitigative measure is not realistic since, in most cases, the adjacent areas could still be a source of flammable or combustible material. Ventilating an area in this case would simply keep drawing in other ignitable mixtures rather than capturing a local release so designing a failsafe ventilation system in these circumstances is probably not feasible.
However, most research applications — not all but most — usually are small enough in size and area and limited enough in the quantity of flammable or combustible materials that providing ventilation designed to capture any releases at the local source and keeping the ignitable area to a negligible extent is feasible. Hence, API 500 does not prohibit using ventilation as a mitigative measure in many research applications. It, for example, specifically excludes laboratories in 6.3.1.2.3 due to the nature of their operations and their high ventilation rates.
NFPA 497 is clearer on this point, noting in 5.5.1 that:
Experience has shown that the release of ignitible mixtures from some operations and apparatus is so infrequent that area classification is not necessary. For example, it is not usually necessary to classify the following locations where combustible materials are processed, stored, or handled:
(1) Locations that have adequate ventilation, where combustible materials are contained within suitable, well maintained, closed piping systems
(2) Locations that lack adequate ventilation, but where piping systems are without valves, fittings, flanges and similar accessories that may be prone to leaks
(3) Locations where combustible materials are stored in suitable containers
(4) Locations where the use of combustible liquids, or flammable liquids or gases, will not produce gas or vapor sufficient to reach 25 percent of the lower flammable limit (LFL) of that combustible material
A very important concept if one chooses to use ventilation as a mitigative measure is keeping the ignitable area to a negligible extent. ISA 12.24.01 Recommended Practice for Classification of Locations for Electrical Installations Classified as Class I, Zone 0, Zone 1, or Zone 2 gave excellent guidance in this regard in 5.3:
The most important factor is that the degree or amount of ventilation is directly related to the types of sources of release and their corresponding release rates. This is irrespective of the type of ventilation, whether it be wind speed or the number of air changes per time unit. Thus, optimal ventilation conditions in the hazardous area can be achieved, and the higher the amount of ventilation in respect of the possible release rates, the smaller will be the extent of the zones (hazardous areas), in some cases reducing them to a negligible extent (nonhazardous area).
If you can design and install a ventilation system so that it will capture all the flammable or combustible material effectively at the source, then you should not need to classify an area.
Consider an open drum full of flammable material. For some distance above the drum, an ignitable mixture of flammable vapor and air (that is, a mixture over the LEL) is present. Classifying this area in lieu of other preventive measures is only prudent. Alternately, if one were to install a properly designed ventilation system that drew off these vapors immediately at the surface of the drum then the extent of this ignitable area would be very small; in the code language a “negligible extent”. Suppose the design is effective in capturing all the vapors within one inch off the top of the drum. Does classifying the area several feet above the top of the drum and off to the side make any sense? At worst one might consider this one inch area above the drum as Class I Division 1 but then classify the rest of the area as unclassified. (And prudently don’t put any electrical devices or wiring in that one inch.)
Ventilation as a mitigative measure requires careful design, proper installation and testing to confirm it is effective, regular maintenance to keep it working properly, and appropriate failsafe alarms and safeguards to warn of its failure and take the proper actions to keep the area safe. All these are required. They also cost and require routine attention.
Simply doing a calculation that indicates that the ventilation rate will dilute the flammable or combustible material below its LEL is not enough for many reasons. First, the larger the area within the explosive range, the higher the change of encountering an ignition source before dispersion. So, there is a real need to design a system to keep this extent small, approaching negligible.
Second, theoretical gas dispersions doe not approach real world conditions. American Conference of Governmental Industrial Hygienists’ (ACGIH) “Industrial Ventilation, A Manual of Recommended Practice for Design” suggests a mixing factor to account for imperfect mixing that ranges from 1 to 10. Other sources suggest a similar safety factor of 2 to 5. Regardless of what value is used, the key point to recognize is that theoretical calculations rarely approach real-world conditions. Even computational fluid dynamics (CFD) simulations will invariably prove to be less accurate than expected.
Third, pressurized leak sources travel significantly longer distances. API 500 in Table 1 suggests an adjustment factor of 1.5 for pressures above 741 psig and 2.5 for pressures above 1,440 psig. Gas leaks will stay concentrated for significant distances before slowing and beginning to disperse. Finally, all ventilation calculations require you to assume a maximum leak rate. This is an area fraught with risk as too many things affect the size of a leak. Hence it can often be much larger or in a different place than expected.
The only truly safe approach is to either enclose the potential source of the release and ventilate it above the maximum possible leak rate one can credibly determine or provide a large enough system, properly designed, to capture the leak effectively at the source. In both cases, by moving the ventilation close to the source, one keeps the area of concern negligible. Prohibiting electrical equipment and wiring in this limited area is usually very feasible.
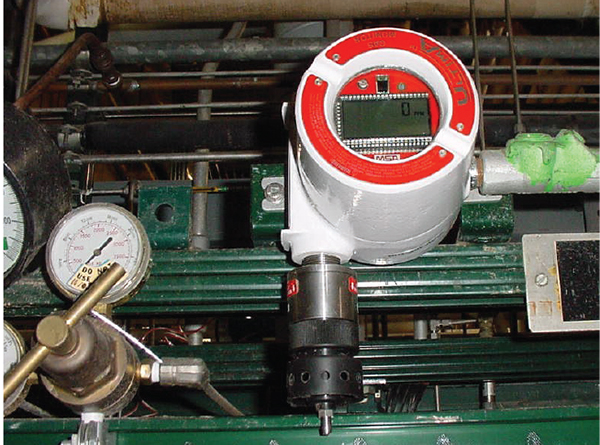
Figure 3. Fixed gas detectors can be an important mitigation measure
Gas monitoring. A third potential mitigative measure is continuous fixed gas detection (Figure 3). NFPA 70 in 500.7 states “ A combustible gas detection system shall be permitted as a means of protection in industrial establishments with restricted public access and where the conditions of maintenance and supervision ensure that only qualified persons service the installation.” However, it limits use of a gas detection system to three specific cases:
A location that would be Class I Division 2 based on a hazard analysis and risk assessment except for inadequate ventilation can, with a fixed gas detection system, be considered Division 2.
A building that would not be classified but is, wholly or partially, inside a Division 2 area can, with a fixed gas detection system, be considered unclassified.
The interior of a control cabinet inside a Class 1 Division 1 area can, can, with a fixed gas detection system, be considered Division 2.
API 500 in section 8.2.8.2.4 goes further after allowing these same three cases and says:
All buildings and rooms that are determined to be adequately ventilated as per the requirements of 6.3 by mechanical means with a minimum of six (6) air changes per hour, and provided with gas detection meeting all of the requirements of 6.5 may be unclassified.
The logic is that the provision of two mitigative measures — adequate ventilation (Figure 4) and a fixed gas detection system — are adequate for safety, and area electrical classification is not required.
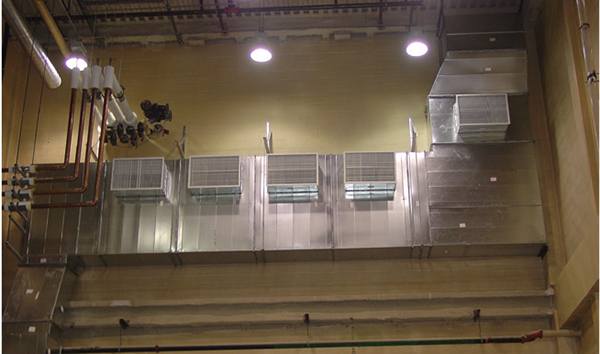
Figure 4. Adequate ventilation is important. Shown here is high-point exhaust in a pilot plant area
Again, these systems need to be properly designed, selected, and installed in a failsafe manner. They require both initial and ongoing routine calibration. They must be designed to work with all the gases that may be present and all the other compounds in the area that may inhibit proper sensing (poisons). Finally, an adequate number of sensors, properly placed to detect any release in a timely manner is required. These factors, particularly determining the last properly, make use of a gas detection system more challenging and, in many installations, highly problematic. Leaks can occur in locations not envisioned and far away from any sensor. Gas dispersion patterns may be very different from what is expected due to pressure, ventilation, open doors, obstacles, and many other factors. Hence selecting and placing the required number of sensors is always more uncertain. For research applications that are smaller and more limited in potential leak locations providing a larger number of sensors and placing them properly is still often possible.
In summary, area electrical classification is a powerful tool for process safety. Research applications should always evaluate its effectiveness, appropriateness, and mitigation. It is not, however, the only viable approach to a safe process.
Edited by Gerald Ondrey
Author
Richard P. Palluzi, P.E., CSP, of Richard P Palluzi LLC is a consultant to the pilot plant and laboratory research community on safety, design and research project management. He retired as a Distinguished Engineering Associate after 40 years at ExxonMobil Research and Engineering, where he was involved in the design, construction, and support of pilot plants and laboratories for ExxonMobil affiliates worldwide. Palluzi is the author of two books, over 100 articles and 40 presentations. He was chair of the AIChE Pilot Plant Committee, ExxonMobil’s Pilot Plant and Laboratory Safety Standards Committee, and ExxonMobil’s Safe Operation Team for their Clinton Facility. He is on the National Fire Protection Association NFPA-45 (Fire Protection for Laboratories Using Chemicals) and NFPA-55 (Industrial and Medical Gases) committees. Palluzi also teaches 15 courses for the University of Wisconsin’s Department of Engineering Professional Development as well as providing customized training to the research community. He has a BE(ChE) and an ME(ChE) from Stevens Institute of Technology in Hoboken, N.J. and holds a PE license as well as CSP (Certified Safety Professional). Palluzi now works full time providing consulting on all aspects of safety and design for pilot plants, laboratories, research facilities and operations.