An artificial intelligence (AI)-based search tool allowed workers to quickly mine historical data to improve operations and respond to emerging problems
At the Bayer Crop Science facility in Muttenz, Switzerland, managers and workers wanted to improve communication during shift handovers and enable more efficient knowledge transfer. The site had already digitized its shift handover notes, giving personnel a vast repository of historical data, but its next challenge was how to locate relevant information quickly on the shop floor. A smart search system powered by artificial intelligence (AI) has helped them mine these data to drive operational improvements and respond quickly to emerging issues.
Inefficient knowledge transfer
“Knowledge transfer is a big issue in shift operations,” says Matthias Hesskamp, head of site operations and excellence at Bayer Muttenz. “Shifts are producing and generating data 24/7, but the Day Operations staff, who are responsible for problem solving, are only onsite working 40 hours per week,” he explains. “That team faces the challenge of processing data that are generated constantly every day.”
To enable better communication across shifts and teams, Bayer Muttenz implemented a digital shift handover system, known as Shiftconnector by eschbach GmbH (Bad Säckingen, Germany; www.eschbach.com), about ten years ago. The software now acts as a centralized database and communication platform, capturing shift notes and other critical plant data in one location (Figure 1). This improves information flow and transparency, since employees know where to find updated information from recent shifts that they need to do their jobs. Over time, Shiftconnector has become a valuable repository of historical knowledge.
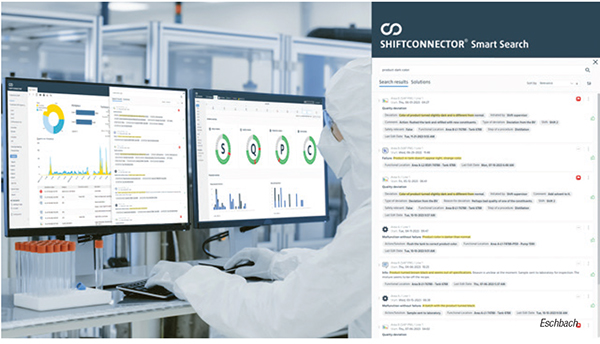
FIGURE 1. Natural language processing (NLP) allows employees to use plain language, rather than keywords, to query the data contained in the shift handover system
Bayer Crop Science process specialist Sven Kränkel explains, “Shiftconnector is mostly kept up to date by the shift teams working on site. They enter data on how the plant is operated, any disruptions or incidents, what ran well, and what optimizations were implemented. The Day Operations team needs exactly these pieces of information to assess whether the production went to plan. Did we have any disruptions? Were they recurring ones? This allows us to evaluate the production process and plan ahead for the coming days, weeks and months.”
However, finding the information at the time it was needed proved to be a challenge — especially if entries were incomplete or searchers did not know the exact correct search term needed to uncover the information. Using standard keyword-based search tools was inefficient and did not always return the most relevant results.
Shift collaboration system
Eschbach worked with Bayer Crop Science in Muttenz to develop a customized Smart Search tool with AI that could be used inside Shiftconnector. Natural language processing (NLP) allows employees to query the system in plain language, without worrying about exact keywords. An example query could be, “has this product output ever turned brown before?”. NLP allows the system to analyze unstructured data like manual shift notes to understand their contents and find relevant results, while machine learning (ML) enables it to look for patterns in vast amounts of data.
To make the system usable, the AI had to be trained on domain- and site-specific language, including technical terms and abbreviations. Eschbach worked with Bayer Crop Science and leading AI researchers at the University of Göttingen to adapt an off-the-shelf AI search tool for their needs. It took two years of development, prototyping and beta testing, which included user groups, workshops and onsite investigations to gather insights into users’ workflows and requirements as well as domain- and company-specific language. The result was a customized AI Smart Search solution that understands their language, workflows and user needs.
Results: impact on plant
AI-driven Smart Search has significantly reduced the amount of time that it takes workers to find relevant entries in their shift handover software. For example, if a problem develops (such as a blocked pipe), AI search allows them to quickly find all the previous times similar issues have arisen, look for patterns that might suggest a cause, and discover what remedies have been effective in the past. It is also faster and easier to find data requested during audits and locate information for operational decision making. Boyjan Guetlin, who works in operational excellence at Bayer Muttenz, says, “Our shift workers did not take long to realize the benefits of Smart Search. Search times were reduced, and information is available for longer. This saves resources and leads to much positive feedback from the shifts.”
Bayer Crop Science shift supervisor Martin Aregger especially appreciates the time saved during troubleshooting. He says, “Smart Search saves us a lot of time, often several hours. Before, I had to research myself how the problem was dealt with in the past. Now, it takes me only a few minutes to gather all the facts before I can tackle the problem and resolve it relatively quickly. Before, it took me hours just to work out an initial approach.”
Providing faster, easier access to historical data allows workers at all levels to do their jobs better and more efficiently. A centralized knowledge management system with Smart Search also preserves valuable information and knowledge for the future.
Process manufacturers are facing a knowledge exodus as experienced workers retire. At the same time, a shortage of skilled workers makes recruiting and retaining workers, and getting them up to speed quickly, essential. Aregger notes, “In principle, you can also store everything in the tool that is necessary for a good introduction. And they can call up the information themselves by entering search terms. This will give them a chance to make an active contribution and to quickly integrate with our company and feel at home here.”
The new tool has been well accepted by employees at all levels in the company. Smart Search is helping Bayer to streamline operations, improve efficiency and reduce the time it takes to identify, troubleshoot and respond to problems. Hesskamp says, “AI will lead to substantial gains in efficiency. As a supporting tool for our employees, it will help them to find data, generate knowledge and solve problems.”
Edited by Scott Jenkins
Author
Andreas Eschbach is the CEO of the global software company eschbach GmbH (Steinbrückstraße 10, 79713 Bad Säckingen, Baden-Württemberg, Germany; Phone: +49 (0) 7761 559 59-0; Website: www.eschbach.com) and inventor of the award-winning plant process management (PPM) platform, Shiftconnector (www.shiftconnector.com). The software is designed to help production teams streamline shift-to-shift communications and enable a safer and smarter environment through better data sharing and workforce collaboration. Holding a degree in computer science, Eschbach draws his practical experience from leading a variety of international software initiatives for major process manufacturing companies, especially in chemical and pharmaceutical industries. He holds a seat on the Forbes Technology Council and recently was named as one of the top 25 industry leaders to transform smart manufacturing by the professional association SME, both of which are committed to advancing manufacturing and developing a skilled and collaborative workforce.