Advancements in artificial intelligence (AI) and improved technologies for providing robots with positional awareness have driven an expansion of robotics use in a variety of application areas across the chemical process industries (CPI)
Robots have been fixtures on discrete-product manufacturing assembly lines for some time, but they have not seen the same level of penetration into chemical manufacturing. In part, this is because the nature of chemical manufacturing and the complexity and diversity of chemical processes have not lent themselves to the incorporation of robots to the same degree as discrete manufacturing. Now, however, recent developments in a range of different fields, such as artificial intelligence (AI), image analysis and others, have expanded the possible applications for which robots can be deployed. Several new robotics applications can have a significant impact on operations in the CPI.
Many of the emerging applications for robots at chemical process facilities involve functions known to be dangerous, difficult or time-consuming for humans to carry out. These include using robots for asset inspections, warehousing, plant security, chemical and materials R&D, picking and sorting operations, among others.
The expansion of robotics at CPI sites is part of a broader trend in automation, and is tied closely to the so-called digital transformation that seeks to incorporate digital tools to improve plant operations. In general, digitalization technologies are being inegrated with automation and robotics tools with the goal of increasing plant safety, reliability and profitability.
Technology convergence
While effective at repetitive movements, industrial robots have historically been limited in those applications that require data collection from the surroundings, autonomous movement and decision-making in direct collaboration with humans.
Xiao Zhong, a research analyst with Lux Research Inc. (Boston, Mass.; www.luxresearchinc.com), explains, “Robotics in the CPI has been driven by advancements in the ability of robots to better sense and respond to their environment and their position relative to other objects and humans.” In addition to improved machine-learning algorithms, these advancements include better camera systems, image analysis capabilities, light detection and ranging (LiDAR), sensors, grippers for delicate objects and others, adds Josh Kern, another Lux analyst.
And the improved technologies, along with growing AI know-how and improved automation tools, are coming together to increase the scope and impact of robots in the CPI.
“Integration is fundamental to maximizing outcomes when deploying robotics,” says Sergio Fernandes, chemical market leader at Yokogawa Corp. of America (Sugar Land, Tex.; www.yokogawa.com). “The data captured by robots become an additional and integral piece of the ‘data lake.’ Not only are we talking about process variables (temperature, pressure, flow, pH, composition), but also about non-numeric data, like images and speech. The expectation now is for AI algorithms to digest photos and dialogue, and to infer from their pattern what may turn into personnel safety concerns, environmental compliance risk, physical asset integrity and health, and, ultimately, operational profit sustainability,” explains Fernandes.
Yokogawa’s approach to creating a platform for integrating robotics and digitalization tools with domain expertise in the CPI depends on all of these. “Advancements in sensing and micro-electromechanical technologies make robots more functional, less expensive, smaller and lighter. Autonomous vehicle research and development has lowered costs of high-priced technology testbeds. The convergence of all these technologies turned robotics into one of the main beneficiaries,” says Yokogawa’s Fernandes.
Meanwhile, ongoing workforce challenges in the CPI and the current pandemic situation has further amplified the opportunities to explore robotics in various applications. “CPI companies are looking for ways to replace retiring workers, while navigating a complex and fast-changing network of end-use markets,” explains Duane Dickson, vice chair and leader of chemicals and oil and gas at Deloitte LLP (London, U.K.; www.deloitte.com). “This is creating imperatives to adopt new ways of operating, and companies are looking to technologies, such as robots and automation, to help them do so as they head into the future.”
In addition, the fallout from the COVID-19 pandemic has accelerated the rate of adoption for digital tools, including AI-enabled robots, by 5 to 10 years, Dickson estimates.
Chemical and materials R&D
The intersection of robotics and AI is playing out significantly in the area of research and development. According to Kebotix Inc. (Cambridge, Mass.; www.kebotix.com) CEO Jill Becker, the process of devising and synthesizing new molecules and materials has not changed fundamentally for a century or more, and a more modern approach is required to solve today’s challenges.
In pursuit of this, Kebotix has built a robotics- and AI-powered, self-driving laboratory for materials discovery. The company says its system can “accelerate the exploration, discovery, use and production of new molecules and materials to help solve the world’s most urgent problems.” Founded by Harvard University (Cambridge, Mass.; www.harvard.edu) researchers, Kebotix has developed “the world’s first and biggest AI brain for chemistry and materials,” which the company says can condense the research cycle for new molecules and materials from a decade to a period of months.
The Kebotix system, consisting of AI algorithms and robotics systems working in a reiterative closed loop, can rapidly and efficiently process enormous amounts of complex molecular data to discover new materials or generate new formulations of particular products with desired target properties, the company says.
In August 2020, Kebotix announced that it received $11.4 million in venture funding for its technology.
Another effort toward using AI and robotics in chemical discovery comes from IBM Corp. (Armonk, N.Y.; www.ibm.com). The company’s European research arm has developed RoboRXN, which IBM Research Europe scientist and manager Teodoro Laino says is an example of bringing technology to bear in order to effect a large change in how synthetic chemistry is done. “Two things that have driven AI recently are image processing and natural language processing — algorithms that are capable of understanding grammar and words,” says Laino. “There have been lots of recent improvements in this area.”
Laino’s team built a trained AI model that predicts chemical reactions and plans chemical syntheses by understanding hundreds of thousands of chemical reactions reported in the research literature. “By treating organic chemistry as a kind of language, we are able to provide an internet-connected, remote chemical laboratory driven by AI,” he says.
To do that, the AI model translates chemical structures into textual representations, and transforms written descriptions of experimental procedures into protocols that can be executed by a laboratory robotic system (Figure 1). It can also predict reagents and solvents, as well as actions, such as add, stir, filter, extract, concentrate, and so on, so that a robot can carry out the synthesis of a given target. The RoboRXN system also can react to feedback from analytical instruments, such as high-performance liquid chromatography (HPLC), mass spectrometry (MS) and nuclear magnetic resonance (NMR), that can characterize reaction products.
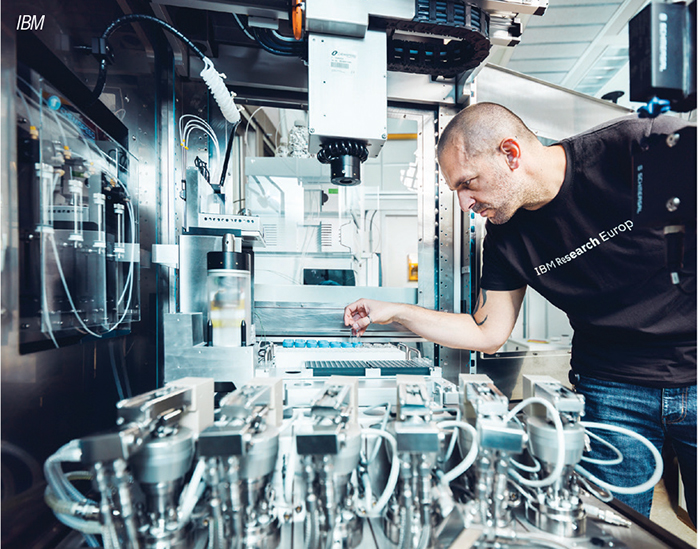
Figure 1. Combining artificial intelligence and robotics, IBM developed a system to accelerate the discovery of new materials
The IBM project took an open approach with the chemistry community. Publicly released in 2018, IBM RXN for Chemistry is currently used by a community of 17,500 researchers who used the IBM AI predictive models more than 2.25 million times to predict reaction routes and perform reactions on the robotic system remotely, Laino says.
“The impact of the system will be felt in accelerating the discovery of new compounds and materials,” Laino says, “as well as retaining knowledge from retiring chemists, and opening up new business for ‘chemistry on demand.’” The IBM scientists are working to improve the AI’s prediction of instructions, which is now 73% accuracy per step.
Laino and the IBM team envision the system as an accelerator for industrial chemistry, cutting the time for discovery of new industrially relevant chemicals, and shortening required development time.
Confined space inspections
Away from the R&D laboratory, robots are also gaining traction at plant sites. An attractive application area for the CPI is robotic inspections in areas that present safety hazards to humans, such as tanks, vessels, reactors and other confined spaces. Remote-operated robots for confined-space inspections is the objective of Invert Robotics Group Ltd. (Eindhoven, the Netherlands; www.invertrobotics.com), a company that has developed climbing robots capable of scanning the walls of tanks, vessels and reactors with a 30X optical zoom camera (Figure 2).
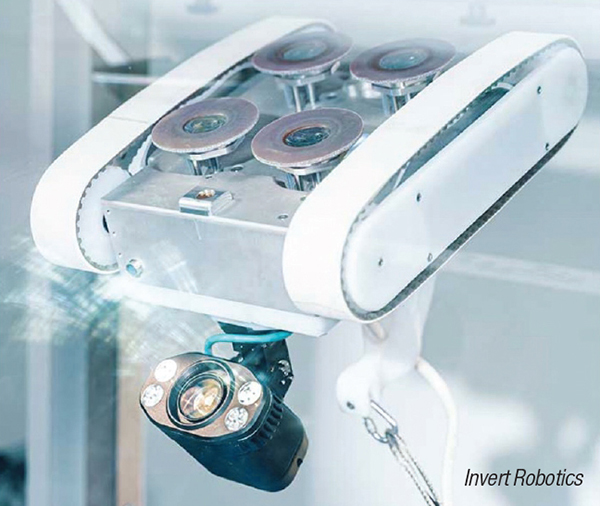
Figure 2. The remote-operated climbing robots from Invert Robotics can climb the walls of tanks, vessels and reactors for visual inspection
“The robots are platforms for a range of non-destructive testing (NDT) instruments,” says Invert’s U.S. sales manager Brent Bonner, such as ultrasonic testing for corrosion.
Two robot models use different mechanisms — vacuum suction and magnets — to hold onto vertical or inverted surfaces. One model features active sliding suction for smooth surfaces, such as stainless steel, aluminum and composites, while another model adds rare-earth-element permanent magnets that keep the robots on the surface of lined or coated surfaces for which suction is not effective. The robots have been used to inspect storage tanks, reactors, spray dryers and others, Bonner reports.
Hazardous environments
Robots are becoming the go-to technology for hazardous areas. ExRobotics B.V. (Delft, the Netherlands; www.exrobotics.global) has developed remote-controlled robots specifically for hazardous environments (Figure 3). ExRobotics has partnered with Yokogawa to offer the world’s first robot with IECEx Zone 1 certification for commercial use. Known as ExR-1, this robot can be used to assess an incident at a CPI site before taking action, and to perform preventative maintenance by regular inspection rounds. Because data can be gathered more systematically, the need to have a human operator in the field is minimal, the company says.
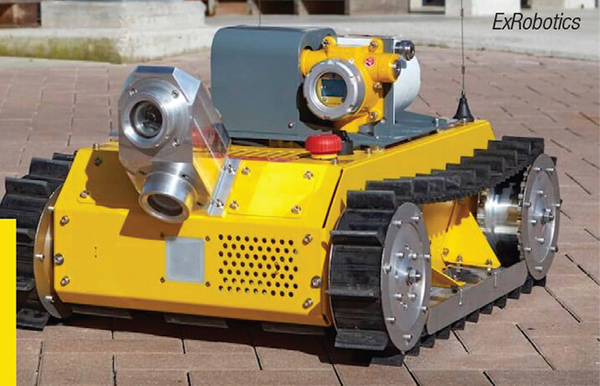
Figure 3. The robot shown here, from ExRobotics, can operate in potentially explosive or hazardous environments to assess incidents
ExRobotics was established in 2017 to commercialize robotics technology for use in potentially explosive atmospheres found at oil-and-gas production and processing facilities, which are often in remote locations with harsh environments. Equipment operating in these hazardous environments must adhere to IECEx Zone 1 requirements. The ExR-1 can be equipped with a range of sensors and cameras, has 4G LTE wireless network capabilities, and can be monitored and operated from a laptop, tablet or smartphone by an operator located in a safe control room anywhere in the world.
Users can realize safety improvements by having fewer people in hazardous locations, more cost-effective, frequent and reliable inspections of facilities; and reliable execution of repeatable work processes, the company says.
Mitsubishi Heavy Industries, Ltd. (MHI; Tokyo, Japan; www.mhi.com) has also been pursuing an explosion-proof plant-inspection robot. MHI recently concluded an agreement with Eneos Corp. on joint development of a second-generation EX ROVR, a plant inspection robot with explosion-proof features to limit the danger of the robot igniting an explosion or fire from electric sparks or heat, even in areas with flammable gas. The agreement targets early realization of a practically viable model (Figure 4).
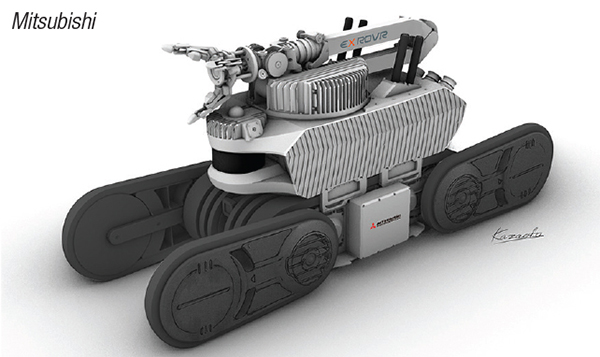
Figure 4. A prototype similar to the robot shown here can move autonomously through a refinery
Last year, a prototype EX ROVR moved autonomously through several floors of an oil refinery and collected data through its various sensors, demonstrating its feasibility in the field. Under the newly agreed joint-development program, the companies will pursue greater volumes of high-quality onsite data through software improvements and the incorporation of a manipulator for photographing instrumentation from a directly facing position. Targets will also include enhancing usability.
Asset inspections
Another area where robotics is catching on is in the inspection of plant assets. An example comes from HEBI Robotics (Pittsburgh, Pa.; www.hebirobotics.com), a spin-off of Carnegie Mellon University’s (CMU) Robotics Institute (www.ri.cmu.edu). The company recently announced that it is taking pre-orders for its MAPS (Modular Absolute Positioning System), part of a suite of robotic tools based on the articulated locomoting “snake robot” technology developed at CMU.
The MAPS system is designed for non-destructive testing (NDT) inspections of complex surfaces. It is a lightweight, portable, passive arm that continuously measures the full absolute position and orientation of a probe as it is moved along any surface. Thickness data from the probe is combined with positional data from MAPS to create fully-encoded scans of complex surfaces.
Manual fitness-for-service inspections can be used for many assets, but this approach lacks verifiability, HEBI says, because there is no practical way of measuring and encoding the inspection. Automated ultrasonic testing (AUT) systems enable the collection of encoded data, but are limited to simple surfaces, such as straight runs of piping, tank walls and plates. HEBI’s MAPS system combines the flexibility of manual inspection with the robust data collection of AUT.
“The MAPS system can improve personnel safety by reducing the time spent by technicians in dangerous or confined areas because they can obtain NDT inspection data faster,” says Bob Raida, COO of HEBI Robotics. Other advantages come in the realm of improving data quality, Raida says.
“Because scans are anchored to an absolute position in the world, it allows a confident alignment and comparison of multiple inspections over time. It removes the variability among different inspectors,” he adds. The first deliveries of the system will occur in Q4 2020.
HEBI’s long-term vision is to accelerate the incorporation of robots into industrial settings by developing robotics tools that can be used to solve problems by engineers who are not robotics experts. “We want to bring the power of robotics and automation development to the subject-matter experts at the plant sites,” Raida says. Right now, robots are difficult to build because doing so involves a synergy of many engineering disciplines. If robots can become part of a ‘toolbox’ that is accessible to plant engineers, then they can build the robots to do what they need,” he adds.
Quality control inspections
Robots can assist in applications where quality control is critical, such as in the manufacture of single-use medical devices, such as syringes, vials and catheters. All units must be visually inspected before being released for shipping, a function that has been done manually. Manual inspection poses several problems, because it can be difficult to find qualified employees, and worker can fatigue during a shift can alter decision making in inspections. This can negatively impact quality control.
In one example, robots from Stäubli International AG (Pfäffikon, Switzerland; www.staubli.com) were employed to support automated inspection of medical catheters. In this application, molded catheters are dispensed into a vibratory feeder system, where they are oriented correctly and delivered into a servo escapement. The escapement separates eight catheters at a time for pickup by a servo transfer robotic arm. Two Stäubli TX2-60L six-axis robots handle the catheters after inspection, with high precision and while maintaining hygienic standards. The robot controller is integrated seamlessly into one programming platform.
After catheters are inspected for defects and noncompliance, the Stäubli robot picks the catheters off the transfer arm and separates those that failed inspection. The end-of-arm tooling on the robot features an eight-position gripper assembly that can individually select and release the catheter, as required. Control of the eight grippers is accomplished using a pneumatic manifold mounted directly on the arm of the robot. Each cell can inspect, sort and package over 50 catheters a minute.
Plant surveillance and security
Plant security and surveillance is another area in which autonomous robots have seen traction. For example, SMP Robotics Systems Corp. (Sausalito, Calif., www.smprobotics.com), offers fully autonomous, self-driving surveillance robots that are designed to navigate in a wide variety of weather conditions on any terrain in daylight or night. SMP Robotics service robots monitor security and safety of designated perimeters in fully autonomous mode. They conduct an inspection for gas leaks, air quality issues, and equipment malfunctions, monitor and observe designated areas with 360-deg views using the advanced video monitoring system (VMS), infrared cameras and onboard sensors SMP Robotics says. The latest generation of outdoor robots are powered by artificial intelligence, deep learning, swarm intelligence technology, obstacle, behavior, and intruder recognition, as well as the state-of-the-art video surveillance system, allowing robots to step to service the open-air space at plant facilities, the company says.
Robots work as a team (Figure 5), covering large common areas simultaneously, redistributing routes (swarm intelligence) while always been connected with the dispatch center (ONVIF; a communications standard between a physical dispatch center and an autonomous device or system (camera, robot or sensor). Swarm intelligence is the collective behavior of decentralized, self-organized artificial systems, and arises out of a combination of technologies (including AI/deep learning and VMS) that work cohesively among more than one robot.

Figure 5. Working together, groups of autonomous robots, can provide plant security
For example, after the robots are programmed to follow certain protocols and navigate the assigned route, swarm intelligence would help the robots rebalance the assigned route among themselves once a robot needs to recharge its battery, the company says. They would notify each other of any out-of-the-pattern behavior (including equipment failures, gas or oil leaks, electrical failures, air-quality issues and so on) as well as any obstacle occurrences (a fallen tree branch, garbage can, gate, and moving objects, including humans).
SMP Robotics robots are already deployed at user sites in more than 15 different countries around the globe. Clients include Eni Sp.A., Saudi Electric and Ejadah, in Dubai, among others.
Supply chain
Another application area for robotics in the CPI is in optimizing supply-chain efficiency. Inpro/Seal, a leading manufacturer of bearing isolators, recently announced the activation of robotic tuggers to improve product flow and advance lean manufacturing at its manufacturing facility in Rock Island, Ill. The Inpro/Seal facility will be using the robotic tuggers to move raw materials, in-progress parts and completed products around the facility, mitigating potential safety risks inherent in manual material handling, the company says (Figure 6). The system will also help reduce work-in-progress (WIP) and achieve lead-time reductions.
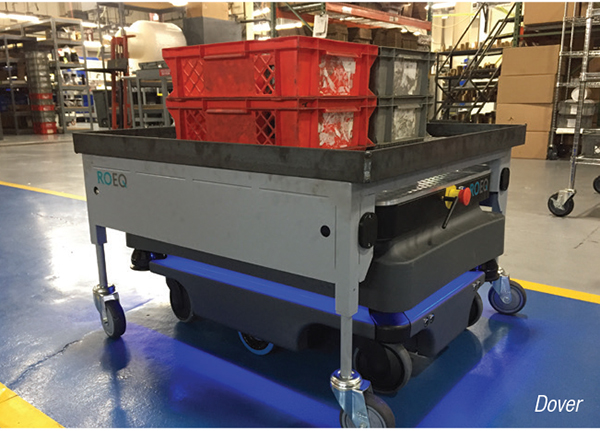
Figure 6. Robotic tuggers can move raw materials and completed parts around a facility, reducing potential safety risks
The adoption of the autonomous tuggers is part of a long-term manufacturing strategy at Inpro/Seal and its parent company, Dover Precision Components (Houston, Tex.; www.doverprecision.com), aiming to further improve safety, ensure quality, optimize productivity and quickly scale manufacturing volume in response to customer demand. From a safety perspective, the adoption of the tuggers reduces heavy lifting, pushing and tugging necessitated by human operation. From a lean-manufacturing perspective, the robotic tuggers eliminate waste associated with moving materials and parts, improve workflow and optimize lead time, the company says.
Cobots
Mitsubishi Electric Automation, Inc. (Vernon Hills, Ill.; us.mitsubishielectric.com) has announced the launch of its ASSISTA collaborative robot in the Americas. As a collaborative robot, or ‘cobot’, ASSISTA is designed to share its workplace with humans in a safe and efficient manner. ASSISTA is designed for original equipment manufacturers and end users with a focus on easy implementation, as its high-quality internal wiring and piping reduces the risk of cables being caught or snagged, increasing uptime and decreasing the risk of needing repair. Safety considerations include the elimination of hand and pinch points to protect hands and fingers of operators, and the robot reacts to its environment by going into a collaborative mode when operators approach it.