Agglomeration and granulation are used to achieve a wide range of objectives in solids-handling processes, including to ensure a desired particle-size distribution, minimize segregation, and improve solids flow, as well as to control de-aeration and compaction behavior and attrition resistance and solid dissolution rates. This one-page refresher describes the two broad categories of agglomeration processes — agitation (wet agglomeration) and compression methods.
Wet agglomeration
Agitation-based processes include fluidized-bed, disc, drum and mixer granulators, as well as hybrid designs (Figure 1). A particulate feed is introduced to a process vessel and is agglomerated (batch or continuous) to form a granulated product. The feed typically consists of a mixture of active products, binders, diluents, flow aids, surfactants, wetting agents, lubricants, fillers and end-use aids (sintering aids, colors and taste modifiers).
Agglomeration can be induced by a solvent or slurry atomized onto the bed of particles, or by the controlled sintering or partial melting of a binder component of the feed. Wetting of the initial feed promotes nucleation of fine powders, or a coating for particle sizes in excess of drop size. In the coalescence (growth) stage, partially wetted primary particles and previously formed nuclei coalesce to form granules composed of several particles. As granules grow, they are compacted by the forces of bed agitation.
Granulation processes vary from low to medium levels of applied shear and stress, producing granules of low to medium and (in some cases) high density. Ranked from lowest to highest levels of shear, these processes include fluidized-bed, tumbling and mixer granulators.
Fluidized-bed granulators. In fluidized-bed granulators, particles are supported, mixed and dried by a heated gas. Proper gas-distributor design is required to maintain solids mixing, and heat and mass transfer. Liquid binder (aqueous or solvent) is sprayed through an atomizing, two-fluid nozzle located above, in or below the bed. Spray distribution, atomizer design and humidity control are crucial to proper operation.
Tumbling granulators. In tumbling granulators, particles are set in motion by the tumbling action caused by the balance between gravity and centrifugal forces. Common designs include continuous, inclined disc and drum granulators with throughput ranges of 1–100 ton/h and 1–5-min residence times. Disc granulators consist of a rotating pan with a rim, typically tilted at horizontal angles of 50–60 deg. Drums are cylindrical, inclined at a horizontal angle of 3–10 deg, and may be either open-ended or fitted with annular retaining rings.
Mixer granulators. Mixer granulators induce granulation through mechanical agitation. A wide selection of mixing-tool designs is available. Differences in equipment, impeller and chopper geometry result in wide variations in shear rate and powder-flow patterns among manufacturers. Controlling the amount of liquid phase, wet mass rheology, and the intensity and duration of mixing determines agglomerate size and density.
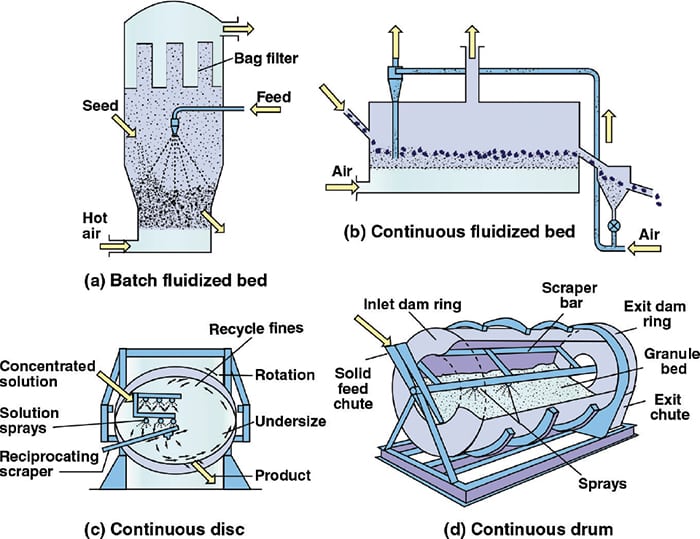
Figure 1. In wet agglomeration processes, a particulate feed is introduced to a process vessel along with additives
Compaction processes
In agglomeration by compression (compaction), a powder blend is fed to a device that promotes agglomeration due to large, applied compaction pressures. Continuous sheets of solid material are produced, as in roll pressing, or some solid form is made, such as a briquette or tablet. Continuous sheets or strands may either break down in subsequent handling to form a granulated material, or the material may be further processed through a variety of chopping, spheronization or forced screening methods.
Tablet presses. Tablet presses produce shapes of superior appearance with strict specifications in weight, geometry, hardness and dissolution behavior. Good flow properties are required for rapid, consistent die filling as well as proper die lubrication (low die friction) to prevent capping and delamination.
Roll presses. Roll presses force material into gaps between two rotating rolls and amplify the incoming feed pressure to a maximum value that occurs at the minimum gap. This pressure and roll dwell time controls agglomerate quality for given feed properties. Smooth or corrugated rolls produce solid sheets, which are subsequently broken down and classified to a desired agglomerate size.
Extrusion. In extrusion, powder in a plastic state is forced through a die, perforated plate or screen. These processes can operate wet or dry to produce narrowly sized, dense pellets. Extruder types include screw extruders (such as axial end plate, radial screen and basket designs), and pelletization equipment (such as rotary cylinder and ram extruders). The equipment imparts shear to the material and product attributes are strongly influenced by friction between the powder and wall. Extrusion processes can exert the highest applied force of any size-enlargement device to give the highest-density product.
Editor’s note: This edition of Facts at your Fingertips was adapted from the following articles: Ennis, B.J., Agglomeration Technology: Mechanisms, Chem. Eng., March 2010, pp. 34–39; and Ennis, B.J., Agglomeration Technology: Equipment Selection, Chem. Eng., May 2010, pp. 50–54.