Establishing novel materials and systems is challenging for new companies. However, startup companies can streamline their research and drastically accelerate product development with effective tools and strategies
While long-standing organizations are often challenged with digitizing large volumes of unstructured historical research data, new companies begin with very little data and usually must rely on trial and error to build up their experimental knowledge base. The pressure to move quickly is intensified by a limited capital runway, making a working prototype’s rapid development essential to maintaining momentum. This is particularly true in companies that are developing advanced materials systems.
The product-development process for materials, in general, is characterized by the difficulty of carefully coordinating each stage of development, from material selection to performance testing, while evaluating thousands of raw-material options along the way. In additive manufacturing (AM), beyond identifying suitable materials, scientists must also design and refine novel printing processes to enable the smooth integration of their developed materials into existing or new printing systems. Furthermore, developing a multi-material system in polymer AM processes presents its own distinct challenge. Engineers must optimize the ink formulation and printing process while complying with multiple performance requirements.
Innovation and precision are crucial to success in such a high-stakes environment, where time and resources are limited.
Multi-material printing challenges
In 2021, Polyfos 3D Ltd. (Yokne’am Illit, Israel; www.polyfos.com), a startup company with a new approach to multi-material polymer printing, began developing a process for selective polymerization of desired materials out of a mix, dependent on final model design. Polyfos’ technology offers the unique ability to print parts simultaneously using two distinct polymers — one polymer is durable for the parts themselves and the other is a soft, water-soluble material for the supports. This method opens up new possibilities in material properties and applications (Figure 1).
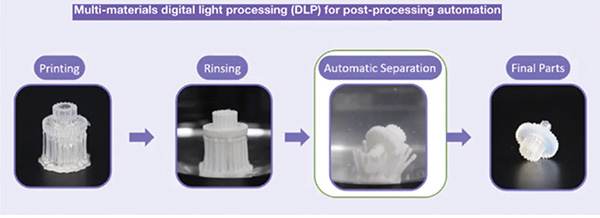
FIGURE 1. Parts are printed with Polyfos’s dual-material printing process, allowing for simplified postprocessing removal of supports
Unlike the challenges faced by established companies with vast amounts of unorganized experimental data, Polyfos’ hurdle was the lack of historical data. The team’s task was complex — they needed to develop a dual-material formulation with specific properties for two interdependent materials. As a startup starting from scratch, the company needed to quickly and efficiently collect experimental data to narrow down the vast combinations of materials and processes. In addition to selecting from thousands of potential raw materials, they had to design, stabilize and optimize a novel printing process to meet demanding requirements. This high-pressure environment necessitated innovation, particularly in how the team approached materials research and process optimization.
Four pillars for precision
From the outset, Polyfos worked with MaterialsZone’s (Tel Aviv, Israel; www.materials.zone) Lean research and development platform to document and optimize research. This partnership has significantly accelerated the development timeline and enhanced product performance.
With MaterialsZone, Polyfos has been empowered to standardize and document their experiments from day one, creating a comprehensive data catalog as they progress. Using MaterialsZone’s four-pillar platform, Polyfos has leveraged advanced tools, including a technical datasheet (TDS) importer and advanced data-visualization tools, which enabled Polyfos to compare raw materials and effectively track experimental results in real-time. This systematic documentation created a single source of truth for research, interlinking experiment data, formulation compositions and material properties.
The system’s first pillar, the Materials Knowledge Center, consolidates internal and external data sources into one coherent structure, utilizing materials and process-specialized data architecture with persona-driven access for tailored user experiences. As Polyfos grew, new team members were quickly integrated into the platform, ensuring all experiments continued to be documented effectively.
Next, through the Visual Analyzer pillar, Polyfos gained insights by performing multi-dimensional analyses, detecting patterns within their R&D processes to facilitate cross-organizational understanding and make data-driven decisions. Additionally, Polyfos has leveraged artificial intelligence (AI) modeling to predict experimental results with the Predictive Co-Pilot pillar, which helps predict experimental outcomes, reducing the need for numerous iterations and enabling quicker, more informed decision-making.
As Polyfos grows, it can further benefit from the Collaboration Hub pillar, which enables secure cross-departmental collaboration in a cloud-based, real-time environment. The hub provides an organizational memory of data, processes and insights, ensuring that knowledge is preserved, accessible and shared across teams, supporting scalability and enhancing innovation.
MaterialsZone has enabled Polyfos to confidently identify trends, conduct root-cause analysis, make data-driven decisions and optimize its research and development processes. This comprehensive approach is also adaptable to Polyfos’ future growth.
Rapid progress
The partnership with MaterialsZone has driven considerable progress. Over the past year, Polyfos has achieved a fivefold increase in the hardness of their insoluble printing material, a key performance metric in their development. The team optimized their complex dual-material printing process using AI-guided experimentation in just 12 experiments, significantly reducing time and resources (Figure 2). With over 250 formulations tested — using more than 100 different raw materials — Polyfos has been able to refine its process at an impressive pace, thanks to the robust data-driven insights provided by the MaterialsZone platform.
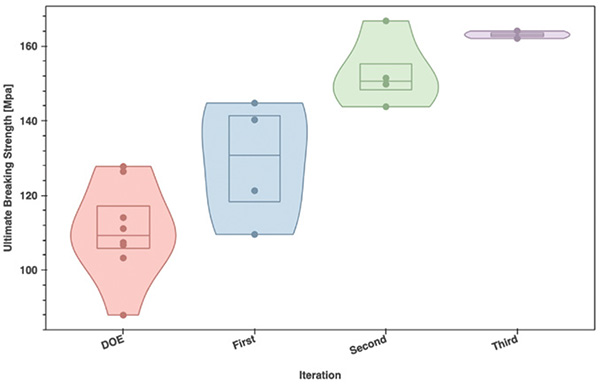
FIGURE 2. A plot in MaterialZone’s platform visualizes how a project focusing on a specific material property (ultimate breaking strength in this case) significantly narrows down its target in just a few iterations starting from the design of experiments (DOE) phase using AI-guided experimentation capabilities
“We initially implemented the MaterialsZone system as a database, but it has proven to be so much more. It enables us to accelerate our development by intelligently selecting experiments, leveraging machine learning capabilities to guide our decisions,” said Keren Regev, co-founder and chief technology officer of Polyfos. “This technology has significantly increased the confidence in our results, allowing us to achieve faster and more accurate outcomes. Ultimately, it has made us better researchers, enhancing both the speed and precision of our work.”
Looking ahead: AI and innovation
As Polyfos continues to push the boundaries of additive manufacturing, its reliance on AI-guided experimentation will deepen. Plans include refining their predictive models to forecast experimental outcomes for untested formulations, reducing trial-and-error processes, and driving efficiency. Additionally, Polyfos intends to implement platform-generated QR codes to streamline sample tracking for external testing, ensuring traceability and data integrity. By continuing to leverage MaterialsZone’s capabilities, Polyfos aims to maintain its rapid innovation and growth trajectory while exploring new opportunities for its dual-material printing technology.
Polyfos’ journey underscores the potential of combining advanced materials informatics with cutting-edge AM technology. As they pioneer the future of multi-material printing, their success is a testament to the power of data-driven research and experimentation.
Edited by Mary Page Bailey
Acknowledgement
Images provided by authors
Authors
Delina Damatov is the head of solutions at MaterialsZone ([email protected]). Prior to joining MaterialsZone, she served as the director of process & materials at Nano Dimension. She holds a B.S. degree in medicinal chemistry from Bar-Ilan University and a Ph.D. in chemistry from the Weizmann Institute of Science. She also conducted postdoctoral research at Yale University.
Omri Schulman is the AI/ML product manager at MaterialsZone ([email protected]). Prior to joining MaterialsZone, he was an R&D process researcher at Nano Dimension. He holds a B.S.Ch.E. from the Technion Israel Institute of Technology and a M.S. in materials engineering from Tel Aviv University.