A common adage says “if you can’t measure it, you can’t control it.” Now, advances in flow-measurement technologies are increasing the breadth of what it is possible to measure
As process demands evolve and organizations increasingly focus on sustainability in their operations, chemical processors must stay abreast of what these changes mean for their instrumentation devices, especially those that measure, monitor and control flow. Beyond measuring flowrate, modern flowmeters increasingly must adapt to rapidly changing conditions, measure many parameters beyond flowrate and continuously communicate with other systems in a plant.
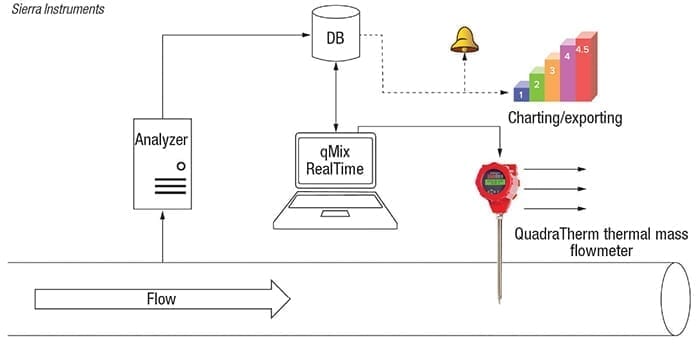
FIGURE 1. The qMix tool integrates with a gas chromatograph to provide realtime measurement of varying gas compositions
Environmental management
“Customers want more than just a flowmeter, they want solutions. This may be additional hardware or software that allows the flowmeter to interface with another control system in the plant,” says Scott Rouse, director of product management for Sierra Instruments, Inc. (Monterey, Calif.; www.sierrainstruments.com). Combining adaptability with connectivity, Sierra has developed a mass flowmeter that can be updated with changing gas compositions in real time, integrating with a gas chromatograph to obtain gas composition (Figure 1), explains Rouse. Using Sierra’s qMix gas-mixing application (app), users can create unlimited custom gases or gas mixtures to compensate for gas compositional changes in the field. Measurement of combustion, flaring and waste-gas processes are often regulatory requirements, and Sierra has now developed an advanced qMix functionality, qMix RealTime, for realtime monitoring of flare and stack gases, says Rouse, thus helping users meet the environmental requirements of organizations like the U.S. Environmental Protection Agency (EPA) and Bureau of Land Management (BLM).
Changing gas compositions can certainly wreak havoc on flow-measurement accuracy in a wide range of industrial applications, including those processing biogas and natural gas. “In biogas and natural gas applications, gas composition can change and look very different from week to week,” explains Ria Edens, industrial marketing communications manager at Fox Thermal Inc. (Marina, Calif.; www.foxthermal.com). Fox Thermal offers the Gas-SelectX tool on several of its thermal mass flowmeters, which allows users to quickly re-program the meter to begin measuring new gas compositions identified by gas sampling. This tool utilizes a library of common pure gases or can be programmed for the users’ own custom gas mixtures. In shale-gas applications, accurate flow measurement of changing gas mixtures is critical for allocation and royalty purposes among the many stakeholders.
Compressed air is another area where accurate flow measurement can reduce wasted energy, thus greatly contributing to efficiency, as problems with leakage are nearly universal to these types of systems. Thermal mass flowmeters provide accuracy benefits with their simplicity — unlike other flow-measurement techniques, they do not require accompanying pressure or temperature calculations to read flowrate. “What ends up happening is that you have three or more different instruments taking these separate measurements, and each one has its own accuracy, so that compounds the measurement uncertainty you’re dealing with,” explains Edens.
In compressed-air systems, many interconnected sub-meters may be involved, so minimizing uncertainty is key. “You have to figure out where the leaks are happening, so installing a flowmeter to measure primary airflow from the compressor, along with sub-meters at each end-use facility, can give data to compare to the estimated demand. If there is variance, you can start to identify leaks,” she adds.
Wastewater treatment is an essential part of environmental management, and flow measurement is a central activity in ensuring that these processes are operating as intended. Although most users might envision a flowmeter being installed on a closed pipeline or tube, the open channels encountered in the water-treatment sector also require accurate and precise flow measurements, particularly at the water inlet (Figure 2). For these special tasks, devices typically used for level measurement can be adapted. “You can find open channels in all kinds of wastewater treatment systems. The flow is measured in open channels using an ultrasonic sensor for height measurement and related linearization,” explains Jürgen Skowaisa, product manager Radar, VEGA Grieshaber KG (Schiltach, Germany; www.vega.com). For this type of application, radar technology provides reliability because it is unaffected by temperature changes, says Skowaisa. VEGA’s radar devices are now offered with a new 80-GHz radar chip that is optimized for measurement tasks in the water and wastewater industries.
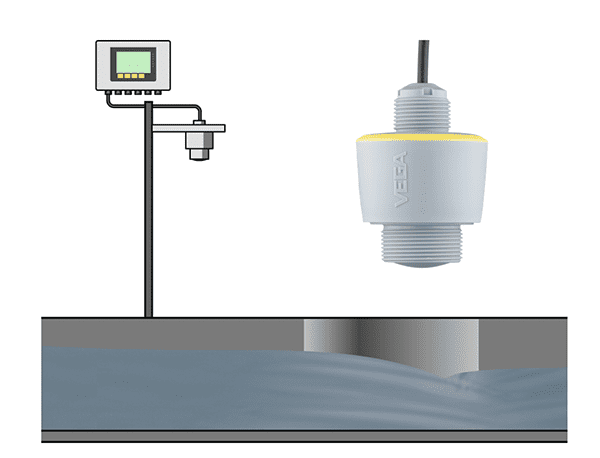
FIGURE 2. A level-measurement device can be adapted to provide open-channel flow-measurement readings in water-treatment applications. VEGA
Less process disruption
Flowmeters are also adapting to processing demands by offering simpler installation and maintenance for their devices. “Customers are tending to shy away from devices with many moving parts that could cause downtime,” says Dave Vollaire, instrumentation product manager at GF Piping Systems (GF; Irvine, Calif.; www.gfps.com). GF has launched the Signet 2580 FlowtraMag magnetic flowmeter (Figure 3), which features a full-bore, all-plastic design with no moving parts that is lighter weight than conventional full-bore magnetic flowmeters.
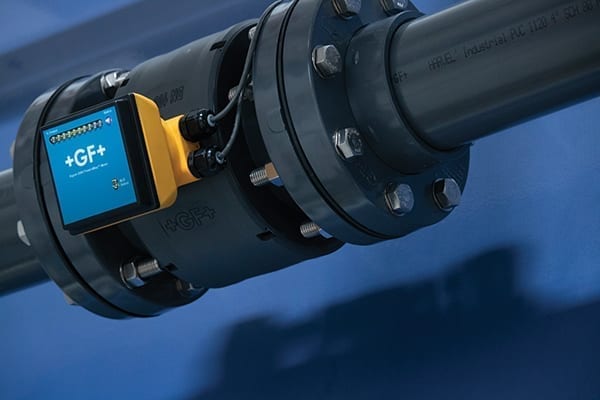
FIGURE 3. With no moving parts and less restrictive installation requirements, the Signet 2580 FlowtraMag is suitable for tight spaces and short pipe runs. GF Piping
According to Vollaire, plastic construction provides environmental benefits in that there are no coated metal parts that could chip and cause corrosion or damage within a process. Streamlined installation is also beneficial. “The shorter run requirements after flow disturbances, such as elbows, valves or pumps, enable users to fit these flowmeters into tighter spaces that otherwise would not be possible with other flow technologies,” according to Vollaire. Furthermore, adaptive flow measurement in both the forward and reverse direction is possible when Signet meters are used alongside the company’s S3L sensors.
Another trend in flowmeter design aims to minimize process disruptions during installation. “We are increasingly observing a trend towards non-invasive and clamp-on instrumentation, both with respect to ultrasonic flow measurement and other analytical applications,” says Jörg Wylamrzy, director of sales at Flexim GmbH (Berlin, Germany; www.flexim.com). Last year, Flexim released the world’s first non-invasive technology for steam measurement, the Fluxus G601 ST (Figure 4).
Measuring and monitoring steam flow is an essential task to ensure energy-efficient operations and reduce waste. “In particular, non-invasive flow measurement in steam-distribution networks can often reveal a huge energy-efficiency potential for plants,” adds Wylamrzy.
Another common application for clamp-on ultrasonic measurement technology is controlling the efficiency of heat exchangers for predictive maintenance tasks. “In general, non-invasive measurement of volume and mass flow, as well as concentration and density, allows for increases in energy efficiency without affecting plant availability,” continues Wylamrzy. Later this year, Flexim plans to release a new high-temperature steam flowmeter that overcomes challenges associated with high-temperature steam operations.
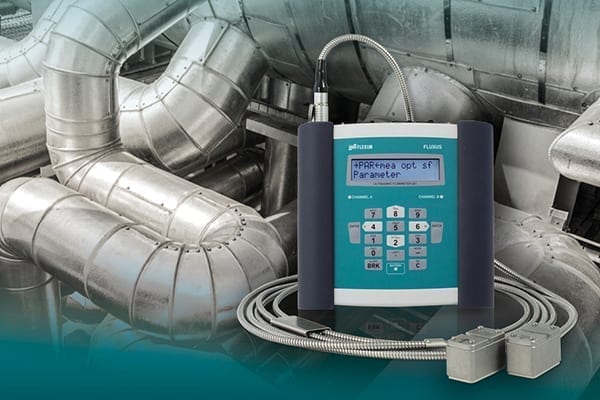
FIGURE 4. The Fluxus G601 ST is said to be the first non-invasive flow-measurement technology for steam systems. Flexim
Multifaceted flow devices
As flowmeters evolve to handle a wider range of processing demands, users increasingly need multifunctional instruments. “Most flowmeters are starting to be recognized as multivariable devices, providing flow information, but also other process variables, such as density, temperature and viscosity,” says Howard Siew, chemical industry manager at Endress+Hauser (Greenwood, Ind.; www.us.endress.com). “Users are continuing to look for qualitative measurements, not just quantitative ones. They typically use laboratory measurements to verify product quality, but this decreases efficiency and throughput. Through the use multivariable flowmeters, users can monitor live product quality and adjust their process on the fly, if necessary,” adds Siew “Rather than thinking of these devices as flowmeters, it’s a change to thinking of them as process analyzers,” emphasizes Nathan Hedrick, Endress+Hauser’s national flow product manager.
As an example, Adam Booth, flow product marketing manager at Endress+Hauser, highlights the company’s recently launched Prosonic Flow G 300/500 inline ultrasonic flowmeter: “This device is available with optional integrated pressure and temperature measurement, which provides an accurate measurement, even with changing process conditions. It also features the Advanced Gas Analysis application package, which enables the device to compensate for varying gas compositions and provides more process variables, such as energy values, molar mass and density.”
To illustrate the importance of compensating for varying process compositions and measuring values beyond flow, Hedrick cites the example of a boiler. “You have some energy stream in (typically natural gas) that is converted to a different energy stream out (steam). With devices like we’ve mentioned here, you can immediately see the efficiency of the boiler in converting from one energy stream to another by monitoring the associated energy values.” One particularly valuable parameter to measure is steam quality — Endress+Hauser’s Prowirl 200 vortex flowmeter (Figure 5) can provide a steam quality measurement down to a dryness fraction of 80%. Hedrick explains: “Saturated steam that is 100% dry is essentially a theoretical fluid. As soon as you have any inefficiency in your steam system from the boiler, you start to get condensation. Most flow-measurement devices assume 100% dry saturated steam in any energy calculations they provide. As a result, unless you are using a device with wet-steam measurement, or a separate steam-quality-measuring device, you are getting an overinflated energy value from the device,” he says.
In hygienic or sanitary processes, advanced multiparameter meters provide many benefits — not only for producing high-quality products, but also for controlling the frequent rinsing and cleaning activities that are required to ensure process integrity. “Many modern flow-measurement devices are multiparameter sensors. Besides the flowrate, they are able to measure other process-relevant parameters in a single device,” says Hendrik Faustmann, product manager, FLOWave at Bürkert Fluid Control Systems (Ingelfingen, Germany; www.burkert.com).
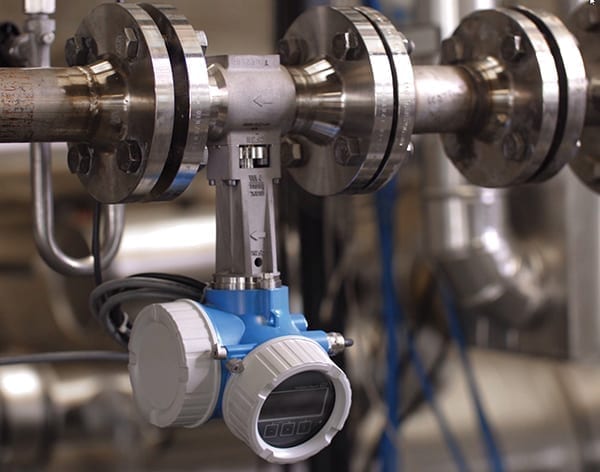
FIGURE 5. The Prowirl 200 vortex flowmeter provides information on steam quality alongside conventional flowrate measurements
In the case of Bürkert’s FLOWave flowmeter (Figure 6), surface acoustic wave (SAW) technology is employed to obtain a direct measurement of flow, combined with temperature readings, interpretations for density and an acoustic transmission factor. This factor provides an indication of viscosity, as well as the presence of solids or bubbles in the measured fluid. “Together, these parameters can be analyzed to provide real-time analysis of the contents of a pipeline, for instance to detect media changeover in rinsing or clean-in-place processes,” explains Faustmann. This enables the flowmeter to rapidly adapt to changeovers between different liquid types during production. “Particularly in cleaning processes, rapid differentiation between product and rinsing water or cleaning reagents ensures efficient process control. Compared to conventional time-controlled processes, product waste can be minimized,” adds Faustmann. These meters do not require that sensors come into contact with process media, and the measurements are taken independently of conductivity, making them suitable for hygienic processes, such as those in pharmaceutical manufacturing.
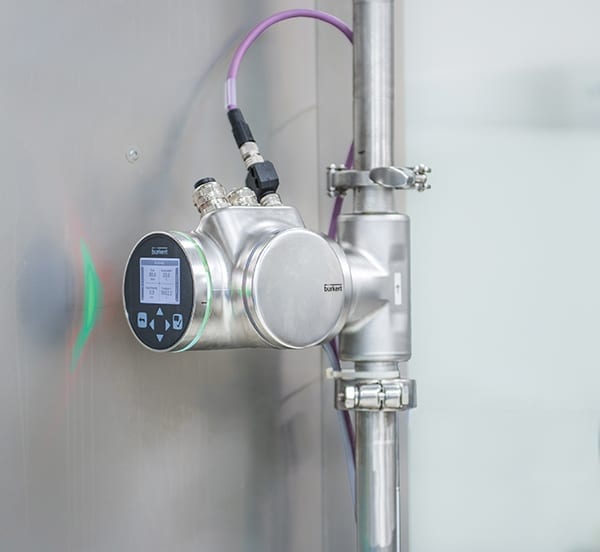
FIGURE 6. The multiparamter readings provided by FLOWave devices give many valuable parameters for controlling clean-in-place operations in addition to regular production processes. Bürkert Fluid Control Systems
With the many available flowmeter technologies, it can be difficult for users to select just one device to best suit their processing needs. Fluid Components International LLC (FCI; San Marcos, Calif.; www.fluidcomponents.com) has launched the Adaptive Sensing Technology (AST) for its ST80 flowmeters (Figure 7), which brings together the two major modes of operation for thermal-mass gas-flow measurement — constant power (CP) and constant temperature (CT) — said to be an industry-first achievement.
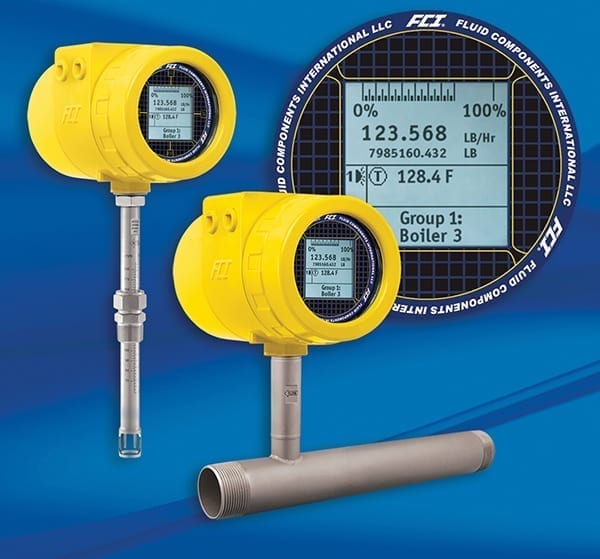
FIGURE 7. The new AST sensor head enables hybrid operation for thermal mass flowmeters, enabling measurement accuracy across a wider flow range. FCI
“CT-type devices historically give a faster response but have less range, and use more power” explains Randy Brown, executive director of marketing and industrial sales & service for FCI. “On the other hand, CP devices can have slower response, but provide more range and consume less power,” he continues. FCI developed and patented the AST sensor drive technology, which enables its flowmeters to adaptively shift between the two modes, depending on the measured value. “The instrument starts out in CT mode, and as the flowrate increases, it will switch automatically over to CP,” says Brown. This adaptability provides users with the fast response of CT meters combined with the wider flow range and lower power needs of CP meters.
Further, since standard CT devices react more erratically when there is moisture or humidity in the pipe, the ST80 can be fixed to operate only in the CP mode to deliver a stable reading. This type of adaptability is particularly beneficial in new process applications, where users may not always know the specific conditions inside of a pipe, says Brown. “In the field, users can switch the unit’s operating mode from AST to CP or CP to AST, to provide the optimum performance in an installation’s actual conditions as opposed to replacing it with a different device.”
While flow measurement is the paramount function, many other variables beyond a process’ flowrate must be considered to ensure flowmeters’ adaptability and reliability. Emerson Automation Solutions (Austin, Tex.; www.emerson.com) has developed several new tools aimed at providing more insight into the flow-measurement process to support improved data use and instrument diagnostics.
For instance, the Smart Meter Verification diagnostic suite allows users to run a health check for an in-service device, looking at many factors that can help streamline troubleshooting and maintenance. “There is a version designed for both magnetic and Coriolis flowmeters that helps extend operating intervals by detecting things like non-uniform coating, erosion and corrosion,” explains Tonya Wyatt, product line manager at Emerson Automation Solutions. Another tool, Zero Verification, helps users with flowmeter calibration. “This tool is especially helpful where the mass flowrate is on the low end of the meter range in applications such as low-pressure gases, high-viscosity fluids and other applications with a large turndown ratio,” mentions Wyatt.
Emerson also offers Advanced Phase Measurement, a patented set of algorithms used on Coriolis meters to improve the accuracy of flow measurement in multiphase flow conditions, including liquids with entrained gas and wet gases. It can also be used in concentration measurements when gas is present, including in oil, water or gaseous mixtures. With so much data available, it is important that users not be overwhelmed. Emerson’s ProcessViz visualization software, says Wyatt, helps people get a quick view of all the data being created by the instrumentation without having to spend hours manipulating data in large spreadsheets.