Altilium Metals Ltd. (Plymouth, U.K.) announced that construction has begun on the U.K.’s first at-scale EV battery recycling facility with integrated chemical refining capabilities, located in Plymouth, Devon.
The groundbreaking ACT 3 scale-up plant will place the UK at the forefront of sustainable battery materials production and underscores Altilium’s commitment to building a national battery recycling ecosystem, supporting industrial resilience, energy security and economic growth.
The state-of-the art facility will have capacity to recover critical battery minerals, including lithium, nickel and graphite, from 24,000 EVs per year. Using Altilium’s proprietary EcoCathode process, battery scrap will be recycled into Nickel Mixed Hydroxide Precipitate (MHP) and Lithium Sulfate — critical intermediate materials for domestic production of battery cathodes.
Construction work at the 4-acre site has already begun, with engineering design work being completed by Hatch, a leading global engineering consultancy. The plant will provide important learnings around materials handling, scalability and process optimization, as well as sustainability and environmental compliance, as part of a clear scale-up pathway for construction of Altilium’s planned ACT 4 mega-scale refinery later this decade.
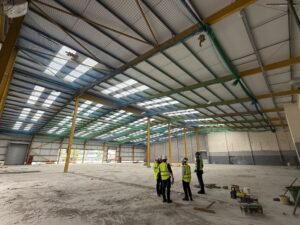
Altilium commences construction of UK’s first at-scale EV battery recycling and refining plant in Plymouth (Source: Altilium)
Currently the U.K. is dependent on the international market for supply of critical battery materials, which are essential for decarbonization and the energy transition. With growing demand from the battery production sector, the U.K. is expected to need up to 40% of current global lithium production and up 30% of current global graphite production by 2030, according to research by the U.K. Critical Minerals Intelligence Centre (CMIC).
By developing a circular economy for EV batteries, Altiliium is ensuring the U.K. has a secure and sustainable domestic supply chain for these materials, while reducing our reliance on imported resources and cutting carbon emissions. ABB is among Altilium’s partners for scaleup.
Dr Christian Marston, Altilium COO, commented: “Our ACT 3 site marks the next phase in Altilium’s mission to close the loop on battery materials here in Britain. We are proud to be building this scale-up facility here in Plymouth, which will be a cornerstone of the UK’s EV battery supply chain. This is about taking a strategic and incremental approach to scaling a vital new industry, one that ensures value stays in the country and creates long-term skilled green jobs.”
While battery recycling in the U.K. has to date focused primarily on shredding batteries and black mass production, Altilium is pioneering the next step: keeping valuable battery metals like lithium and nickel in the U.K. through advanced hydrometallurgical refining. This approach ensures local job creation and a resilient supply of battery-grade materials for the U.K.’s growing EV and gigafactory sectors.
Altilium’s growth strategy provides a structured, risk-managed scale-up pathway to commercialization, culminating in construction of one of the largest planned recycling facilities in Europe:
- ACT 1: Altilium’s Technology Centre in Devon is the company’s innovation hub, where its proprietary EcoCathode™ process was developed.
- ACT 2: A pilot line that processes one EV battery per day, validating the process and materials with automotive OEMs.
- ACT 3: Scale-up plant in Plymouth, now under construction, producing intermediate battery materials.
- ACT 4: A planned mega-scale refinery delivering battery metal salts, P-CAM and CAM (cathode active material) to UK gigafactories.