Acrylic acid is a moderately strong carboxylic acid primarily used as an intermediate in the production of acrylate esters. These acrylate esters are then mainly used to manufacture adhesives, plastics additives, coatings, paints and textiles.
The process
Figure 1 depicts a propylene oxidation process similar to technology for the production of ester-grade acrylic acid (EAA) that was developed by Lurgi GmbH (Frankfurt, Germany; part of Air Liquide; Paris; www.airliquide.com) and Nippon Kayaku (Tokyo; www.nipponkayaku.co.jp). This process is described in the next paragraphs.
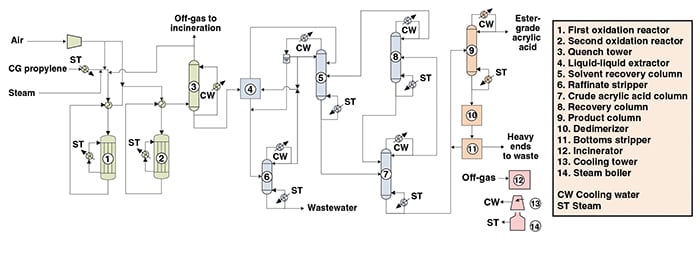
Figure 1. The diagram shows a process similar to the Lurgi/Nippon Kayaku technology for ester-grade acrylic acid production
Reaction and quench. Chemical-grade (CG) propylene is mixed with steam and air and fed to a two-step oxidation reaction system. In the first step, the propylene is oxidized to acrolein and, in the second step, the acrolein is oxidized to acrylic acid. Both steps are carried out in tubular, fixed-bed reactors. The heat generated by the exothermic reactions is used to generate steam. The effluent from the reaction system is sent to a quench tower, where the acrylic acid formed is absorbed in water. Part of the residual gas obtained by the top of the quench tower is incinerated, with the balance being recycled to the first-step reactor. The aqueous solution is sent to downstream units for product recovery.
Product recovery. The aqueous solution from the quench step is fed to an extractor, where the acrylic acid is separated by liquid-liquid extraction with a solvent. The top portion of the extractor, containing the acrylic acid, is sent to a solvent-recovery column to recover a two-phase overheads stream. This two-phase stream is separated and the organic phase, containing the solvent, is recycled to the extractor. The aqueous phase is mixed with the raffinate from the extraction step and sent to a raffinate stripper to minimize the solvent losses. The bottom stream from the solvent-recovery column is then fed to the crude acrylic-acid column, where a concentrated acrylic acid stream is obtained as the bottom product. The column overhead stream, mainly comprised of acetic acid and light impurities, is sent to a recovery column. The bottom stream from the recovery column is sent to the crude acrylic acid column and the overhead stream is recycled to the solvent recovery column.
Purification. In the purification area, the concentrated acrylic acid stream from the crude acrylic acid column is fed to the product column. In this column, ester-grade acrylic acid is obtained as the overhead product. The column bottoms are sent to a dedimerizer to convert the dimer impurity, formed in the process, back to acrylic acid. Finally, the product from the dedimerizer is sent to the bottoms stripper column, where the heavy ends are separated and sent to waste.
Economic performance
The total fixed capital estimated to construct such a plant producing 150,000 metric tons per year of EAA in the second quarter of 2015 in the U.S. is about $350 million. The total fixed capital estimated includes the inside- and outside-battery limit units (production units, storage installations, utilities facilities and auxiliary buildings).
Acrylic acid pathways
Processes based on propylene oxidation are traditionally most employed in the production of acrylic acid. Figure 2 illustrates other alternative pathways for the production of acrylic acid, starting from different feedstocks.
Edited by Scott Jenkins
Editor’s Note: The content for this column is supplied by Intratec Solutions LLC (Houston; www.intratec.us) and edited by Chemical Engineering. The analyses and models presented are prepared on the basis of publicly available and non-confidential information. The content represents the opinions of Intratec only. More information about the methodology for preparing analysis can be found, along with terms of use, at www.intratec.us/che.