From initial conceptualization to final calculation, designing compressors requires not only engineering intuition and robust simulation tools, but also a bit of creativity
As technology has evolved, so has the refrigeration industry. What were once holes in the ground filled with ice and snow have transformed into the modern high-efficiency compression machinery we have become so familiar with today. However, as common as these devices have become, the design process remains a challenge. This is where a combination of scientific knowledge, experience and creative initiative comes into play. While there are, of course, several variations in terms of the application of each design step, the guidelines presented here could be applied not only to refrigeration compressors, but also to compressors used in many other processes and industries.
There are a number of steps to consider throughout the compressor design process, and each step has to relate back to the original design concept. Experience has shown that having a starting concept and an end goal in mind is imperative. Namely, before you can begin the process, you need to know where you are starting and where you want to end up. With this in mind, before we can even get started with preliminary design, blade profiling and analysis of computational fluid dynamics (CFD), it is important to take out a piece of paper and start brainstorming. Consideration of the different refrigeration technologies (cycles), is always a great place to start, so we can ensure we will design the best compressor for the application. The cycle will directly impact the rest of the compressor design decisions, so this is not a step that can be bypassed. This article’s discussion begins with cyclic compression.
Cycle design and optimization
Cyclic refrigeration units are used for reducing and maintaining the temperature of a body below the general temperature of its surroundings. In a refrigerator, heat is pumped from a low-temperature heat source to high-temperature surroundings. According to the second law of thermodynamics, this process can only be performed with some aid of external work. The vapor-compression refrigeration cycle (which is a type of cyclic refrigeration) is used in most household refrigerators, as well as in many large industrial systems. The advantages of choosing this route are that the technology is mature, the costs are relatively low and the process has the capacity to be driven directly with electrical or mechanical energy.
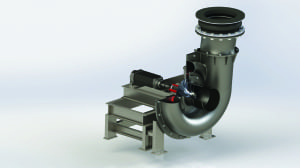
FIGURE 1. While there are numerous compressor types frequently used in the process industries, centrifugal compressors are among the most ubiquitous
For initial consideration of the compressor, we must perform calculations to determine the operating conditions and system function, the type of working fluids and the system size and requirements, as well as the economic analysis of the whole cycle. By completing these steps prior to beginning the preliminary design, we are establishing boundary conditions, performance requirements and geometric constraints for the compressor before committing to a design that may or may not be realistic.
Next, we must determine the type of compressor we want to use for the refrigeration cycle. For the purposes of this article, we will focus on the centrifugal configuration (Figure 1). However, many other options exist, including reciprocating, scroll, helical and rotary compressors.
To elaborate on the output from cycle calculations, we also need to know several specific data points for the proposed compressor, including the required pressure ratio, discharge pressure, volumetric flowrate of the refrigerant, application requirements and the assumed required economics. At this stage, the procedure feels much more like science than art.
Next, the designers need to decide whether they want to design a compressor using an existing similar design (requiring them to scale up or down and optimize the design) or to start from scratch with something completely new. For the purposes of this article, let’s focus on a new design. Now that these decisions have been made, let’s revisit that piece of paper from the brainstorming session and launch into the design process to make the project a reality.
Preliminary design
Once brainstorming is complete and the technical specifications have been defined, preliminary designs and feasibility studies can begin. First, it is recommended that the engineer start by listing all of the constraints determined in the brainstorming step. From there, a novel approach to preliminary design is to use an inverse-design method of problem solving. Specifically, what this means is that we want to consider the specific performance of a compressor and then determine the best geometry to achieve this performance by using software and solver tools. Here, it is important to begin considering the internal components of the compressor (Figure 2). The primary components of a centrifugal compressor stage are the impeller, inducer, diffuser (vane or vaneless) and volute (Figure 3). The impeller functions to increase the fluid pressure, and the diffuser further increases the fluid pressure by utilizing the kinetic energy of the flow, which is available downstream of the impeller. The volute is used for flow collection and for directing the fluid to the pipe. The inlet guide vane (IGV) provides mass flowrate control. Fundamentally, since the total enthalpy and pressure rise of the compressor stage occurs at the impeller, the impeller’s performance and loss prediction are among the most important aspects of centrifugal compressor design and analysis.
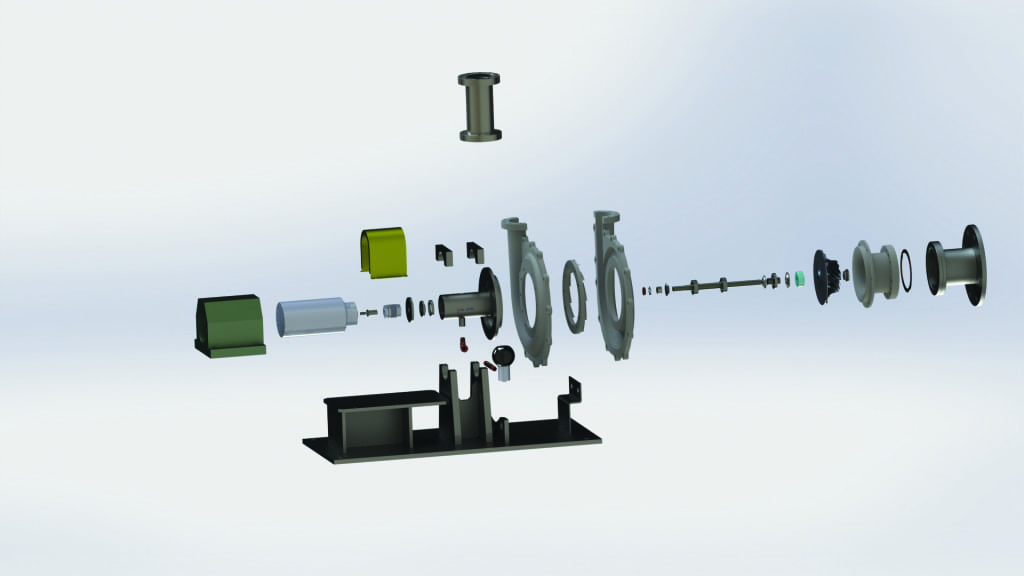
FIGURE 2. Centrifugal compressors include several critical internal components that cannot be ignored during the preliminary design phase
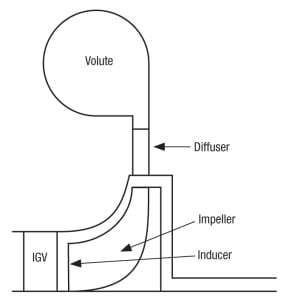
FIGURE 3. The many internal components of compressors, including the diffuser, impeller and inlet guide vane (IGV) must be considered in order to ensure a robust design
To run an inverse-task exploratory approach of preliminary design, and further explore the design space, we must consider different types of impellers and which to use. Some of the options to consider include whether the impeller is shrouded or unshrouded, whether or not an inducer is present on the impeller and whether a forward or backswept impeller blade is used at the outlet. Other options include splitter blades, types of diffusers, IGV exit and so on. To arrive at the appropriate decision about which configuration to use, we must consider various losses that can exist during different modes of operation and applications, including friction, windage, leakage, recirculation and passage blockage. Once we are settled on the specific type of configuration we want to study, the simulations can begin.
Meanline and streamline design
After we have picked one or several potential geometries and designs, the next phase is to perform meanline and streamline (also sometimes called through-flow) calculations. To better explain this, if the cycle is zero dimensional (0-D) and the inverse task/preliminary design is one dimensional (1-D), then this is considered a two-dimensional (2-D) design. The meanline approach is a 1-D calculation at the pitch (mean) line with extrapolation of the flow properties at the hub and shroud. The streamline approach is a 2-D calculation accounting for real blade angles at each spanwise location, and is especially useful for longer blades. Here, we are considering the actual geometries (profiles) we evaluated previously and performing more precise calculations to see the real performance of these compressors, as well as what that performance will be at different operating conditions. Although turbomachinery is typically designed for a set of specific operating conditions, it is also a good idea to consider the performance characteristics in “off-design” conditions. Just like the prior ones, this step is quite important, because these simulation calculations are significantly faster to run now, as opposed to doing so in the later CFD step. By generating a full performance map with a 1-D tool, it is possible to estimate working range and choke or surge margin early on with acceptable accuracy.
Software best practice. Designing a compressor is certainly not a simple task. While it can be appealing to have a range of different software tools each specialized for a different function, this is typically not the best course of action. Going through each of these steps can be extremely tricky when you use a number of different software design tools, since, not only is there the time commitment of figuring out how each works, there is also the potential for error associated with reentering data at each design step, as well as the struggle of ensuring that each platform integrates with one another. For this reason, it is typically best to stick with one or two integrated platforms that can accomplish what is needed to complete the given design project.
Blade design and profiling
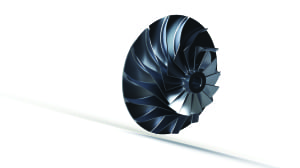
FIGURE 4. Blade profiling is an essential design step in confirming the operability of a proposed compressor geometry. This image shows a completed compressor blade for radial machinery after streamline analysis and CFD analysis has occurred
Now that we have a geometry and are comfortable with its assumed performance characteristics from the previous steps, the next activities will be profiling and blade optimization. During the profiling of the plain sections, we need to control the quality of the flow in the channel to achieve results with minimal profile losses and reasonable distribution of thermodynamic (pressure) and kinematic (velocity) parameters along the channel.
The typical and most applicable mechanism of blade-shape definition for radial machines is the angle distribution along the meridianal length of the blade channel (Figure 4). Here, the major objective is to determine which blade shape is optimal, and whether we obtain it with our geometry. The answer lies more in creativity than science. The understanding of the flow particularities, and even an imagination of the fluid behavior, should be called into play. This can even be called an engineering art. Further, we validate our blade-building skill with the 2-D/3-D calculating methods — full streamline analysis and 2-D/3-D CFD. Usually, this is an iterative process.
Volute design

FIGURE 5. Considerations related to friction, flow velocity and circumferential variation are important when evaluating the design of a compressor’s volute
A volute, in this case, is a casing that receives the working fluid coming out of the impeller. The volute typically looks like a curved funnel, as seen in Figure 5. The main objective of volute design is to define the circumferential variation of the mean radius and cross-sectional area. The different types of volutes are as follows:
- External, with an outer diameter higher than the diffuser discharge diameter
- Internal, with the volute outer diameter equal to the diffuser outlet diameter and the inner diameter lower than the diffuser exit
- Intermediate (somewhere in the middle of option 1 and 2)
Volutes may also be classified by the shape change across the circumference (constant external diameter, constant internal diameter and constant mean diameter).
Once we have considered the type of volute, the next main objective becomes to define the circumferential variation of the mean ratios and the cross-sectional area. There are two main methods of doing this, described below.
Simple area schedule (SAS). A desired flow velocity at the scroll discharge is used to set the area at the full-collection plane. Then the volute area is allowed to vary linearly with the polar angle, 0 deg.
Area distribution. Establish an area distribution from the principles of conservation of mass and angular momentum.
When considering volute designs, we must also consider losses, which include incidence losses and losses related to flow turn in the volute, such as friction, mixing losses and so on.
Computational fluid dynamics
CFD calculations are an integral part of centrifugal compressor design and are an important final step for broad modeling and simulation of flow, heat transfer and turbulence. The main objectives of 3-D CFD calculations are to evaluate the quality of the flow path, compare the results of 3-D CFD calculations and the meanline and streamline calculations’ experimental data, and check for the presence of flow separation, supersonic shocks and the effects of 3-D blade design.
In most CFD codes, the main aspects include a preprocessor, which is used for mesh construction, definition of fluid properties of the appropriate boundary conditions, a solver and a postprocessor for analysis and display of results. Typically, the process starts with loading the data into the CFD software, with given boundary conditions, geometry shape and so on. Next, the engineer needs to create and define the mesh. Mesh generation involves the computational domain where the engineer solves a set of equations (specifically Navier-Stokes equations) to obtain an appropriate mesh (grid). Finally, it is time to set up the solver and monitor for completion. Once the solutions are presented, the engineer must review the results, and adjust the models to make sure that everything is reasonable, and of course, if issues arise, revisit the geometry in the profiling tool to make the appropriate changes.
Finite element analysis
Finite element analysis (FEA) is another important step of centrifugal compressor design — especially so for refrigeration compressor applications, as those may involve working with challenging fluids. The objective of this type of analysis is to explore how the compressor (or anything for that matter) would perform under “stress” operation. Engineers typically want to perform static, modal and harmonic analysis. When undesired stresses are discovered in the compressor (usually on the impeller), the engineer goes back to the profiling step and iterates the design to minimize these performance characteristics. Although seemingly straightforward, this step can result in serious time and monetary losses if not carried out correctly.
Rotor dynamics
Rotors and bearings are the most critical components of any rotating machinery, including centrifugal compressors. Rotor lifetime and reliability depend, first of all, on the level of rotor vibrations. In order to meet the highest requirements of reliability, each step of rotor design for a centrifugal compressor should be based on accurate rotor-dynamics predictions.
Recognizing all these points, we cannot forget to perform rotor dynamics analysis during the process of compressor development. Using a given design software, we can perform the full-scope rotor dynamics analyses required by widely used standards. To guarantee safe centrifugal compressor dynamic operation, we want to perform static deflection analysis, critical speed and map analysis, stability analysis, unbalancing response, model torsional analysis and time-transient torsional analysis. Another useful tool here is a Campbell diagram, which shows the frequency versus the rotation speed of a shaft, allowing for analysis of these two factors to determine the functionality of a given design.
Coupled to this process is the estimation of bearing workability. Often, using a software module (Figure 6) packed with mechanical and hydrodynamic characteristics for various types of journal bearings (including oil, gas-foil and ball-bearings), stiffness and damping characteristics is best, because you can also simulate the thrust.
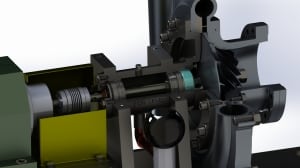
FIGURE 6. A robust compressor-design software can evaluate the performance of different types of bearings
Closing thoughts
Using refrigeration compression as an example, it is clear that quite a lot of thought goes into compressor design before any engineering work can take place. After you have brainstormed and decided on the type of compressor you wish to design and what you need it to do (where you are and where you’re going), the work really kicks into full gear. Preliminary design must be conducted, followed by meanline and streamline analysis, volute design, CFD, FEA and finally rotor dynamics. While this can all appear overwhelming at first, compressor design is a skill that can be perfected through the means of science, art and practice. Rome certainly wasn’t built in a day, and neither is your compressor. So once you have the logistics figured out, patience is key. Combining your own knowledge with the steps presented in this article, along with an integrated software platform and a team of enthusiastic colleagues, will put you well on your way to a successful compressor design.
Edited by Mary Page Bailey
Valentine Moroz is the chief operating officer (COO) of SoftInWay Inc. (1500 District Avenue, Burlington, MA 01803; Phone: 1-781- 685-4942; Email: valentine@ softinway.com; Website: www. softinway.com). Moroz has been involved in turbomachinery for over 15 years, and has supported SoftInWay in the capacity of COO since 2009. In this role, he has been instrumental in growing the turbomachinery development and services business from his involvement in moderately sized design projects to engaging in complete turnkey product development, ranging from green-energy turbines to refrigeration compressors. His specialties include turbomachinery technologies, such as turbines, pumps and compressors. Additionally, his responsibilities include sales, marketing and finance for the SoftInWay Group of companies, as well as opening and staffing global offices in Switzerland, India and the U.S.