Advanced equipment, new chemistries and digital technologies help manage water use to provide efficiency, sustainability and savings
Water, the “common currency” across all chemical process industries (CPI) sectors, is an integral part of every process — from upstream, where it is treated and used for utility and process purposes, to downstream, where it must again be treated to meet environmental regulations before discharge. However, as demand for water increases, water stress and scarcity are creating a situation where water is a costly and valuable resource. “Chemical processors have transitioned from considering water to be secondary to their production to realizing that water management and treatment is an integral part of the process, which means they are more focused on improving the efficiency and sustainability of this critical fluid,” says Subir Bhattacharjee, founder and CEO of IntelliFlux Controls (Irvine, Calif.; www.ifctrl.com).
This new focus has led to the use of more sustainable water practices, and these practices do not stop at treating wastewater to comply with environmental regulations, says Charlotte Fischer, customer success manager with TrendMiner (Houston; www.trendminer.com). “Processors are focused on minimizing the amount of water used and the amount of wastewater produced, as well as changing the entire production process to include recycling or reusing water in a circular economy.”
Today’s version of a circular economy involves a regenerative system in which resource usage, waste production, emissions and energy waste are reduced by slowing, reducing and closing material and energy cycles. “In this circular economy, water, energy consumption and carbon footprint are often harnessed together, since water reuse and treatment are intrinsically energy intensive due to the need to move large streams of water,” notes Fischer (Figure 1).
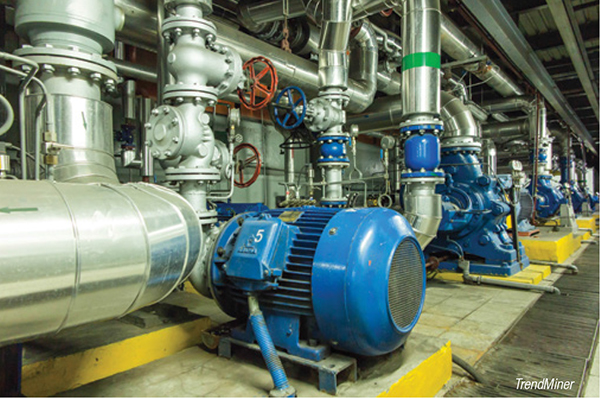
FIGURE 1. Water reuse and treatment are intrinsically energy-intensive due to the need to move large streams of water
While mechanical and other treatment methods are improving radically to meet today’s water challenges, digitalization and data analytics are also being employed to intensify the efficiency of water management technologies (Figure 2). “A digital and software-based upgrade often shows processors how to enhance the process intensity or process efficiency to achieve savings in operating expenses while still improving the sustainability of the current process,” says Bhattacharjee.
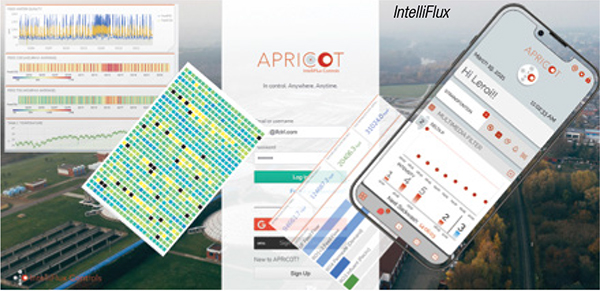
FIGURE 2. A digital and software-based upgrade often shows processors how to enhance the process intensity or process efficiency to achieve savings in operating expenses while still improving sustainability of the current process
Peter Macios, executive product manager with SUEZ Water Technologies & Solutions (Trevose, Pa.; www.suezwatertechnologies.com) agrees: “Sustainability and operations don’t have to be exclusive. As operations evolve and chemical processors are reusing more water, it is a mix of equipment, new treatments and digital solutions that can help them achieve both sustainability and operational goals.”
Equipment advances
Because sustainability includes reduced resource and energy consumption, along with increased efficiency, in a way that complies with regulatory frameworks, there are a myriad of technologies available to meet the needs of many situations, says Fischer. These can include zero liquid discharge (ZLD) technologies, advanced biological processes that use microorganisms to degrade organic matter, advanced oxidation processes (AOP) that use oxidation to remove pollutants and membrane technologies, such as reverse osmosis (RO) and ultrafiltration. “As these technologies become more developed and optimized, they are becoming very helpful,” she says.
For example, in years past, equipment for water reuse and recycling did not have the capability to achieve the quality of water that is needed for reuse in the process or other areas of the facility in a cost-effective way or within necessary operational parameters, says Joe Tirreno, executive vice president strategic corporate business, with Kurita America (Minneapolis, Minn.; www.kurita.com). “However, in recent years, technologies have advanced enough that wastewater that is discharging can be recycled back into use at the beginning of the plant in a cost-effective manner, especially since the cost of water today is considerably more expensive than the cost of recycling.”
He points to technologies such as ZLD as being improved enough to become a major trend. “We have built several ZLD facilities for the ethanol industry. These plants are often in the middle of a cornfield and do not have access to water or a location to dispose of water, so ZLD is commonly used there. In other industries, ZLD and other technologies are being used for sustainability efforts and for the limited accessibility to raw water.”
Often, according to Ravi Chidambaran, chief operating officer with Aquatech International (Canonsburg, Pa.; www.aquatech.com), there are integrated ZLD plants that employ multiple technologies to achieve even higher levels of sustainability. The company recently developed a high-recovery RO technology, Advanced Recovery Reverse Osmosis (ARRO), that overcomes the challenges of conventional RO technologies to achieve recovery rates up to 95% without extended downtime for cleaning and maintenance, which limited previous RO technologies to a 75% recovery rate.
Integrated plants are being built around the world, he notes. For example, in India, Aquatech supplied an integrated ZLD plant that converts waste into pure sodium chloride, which is used as a feedstock in their caustic manufacturing. “Not only do they not incur costs for disposing of the waste, but it’s being converted into a raw material with its own value.”
The company also developed a technology known as BioMOD AnMBR, which is an anaerobic membrane bioreactor that is an energy-neutral or energy-positive technology, says Chidambaran. “This means it doesn’t consume any energy or it can deliver energy that can be used as a heat source. We’re able to achieve more than 95% COD [chemical oxygen demand] reduction and generate methane as a by-product, which can be used as a heat source. This also reduces the quantity of extra sludge, so sludge disposal is reduced by almost half.”
Alternative treatments
While mechanical equipment options are advancing, there is still a need for additional treatment methods and chemistries, such as environmentally friendly disinfectants, corrosion inhibitors, scale removers or other chemicals, as well as alternative treatment options, such as ultraviolet (UV) light and membrane technologies. So, treatment providers are working to improve these offerings to meet sustainability goals.
One of the simplest options is the use of filtration before mechanical equipment like RO, says Dan Flanick, company manager for Tekleen Automatic Filters (Los Angeles, Calif.; www.tekleen.com). “We offer self-cleaning screen filters with capabilities down to 2 microns,” he says. “We’ve seen a lot of growth for these filters in RO pre-filtration because the membranes for RO are very expensive, so protecting them with a self-cleaning filter saves a lot of downtime and a lot of money on membrane replacement, while helping extend the life of the RO equipment.” Prior to the use of self-cleaning screen filters, processors used multi-media filters as a pre-filter, which required a lot of floor space. Tekleen’s self-cleaning filters can reduce that footprint by 70%, giving processors additional space to add more equipment at a lower cost, Flanick says.
Resins are another method employed to solve pre-treatment challenges, says Noel Carr, EMEA life sciences and specialties marketing manager with DuPont Water Solutions (Wilmington, Del.; www.dupontwatersolutions.com). “Contaminants are elements, complexes and compounds that are human-made and naturally occurring in water that must be selectively removed so they don’t interfere with chemical processing,” says Carr. Boron is one of the most troublesome compounds for processors, especially in the microelectronics industry where even a small concentration of boron can create issues for ultrapure water (UPW) systems and product yield. While DuPont has been providing Boron Selective Resins (BSR), most are not applicable for the polishing loop at the UPW system due to the requirements on total organic carbon (TOC) leachables and resistivity. To meet the increasing demand for semiconductor-grade BSR products, DuPont developed the AmberTec UP7530 Semiconductor Grade Boron Selective Ion Exchange Resin, which can be used to remove boron to trace levels with acceptable delta TOC and resistivity. It is ready to use without further post treatment with chemicals at the site, making it an environmentally friendly choice.
And, to protect heat exchange surfaces without harsh chemicals, polymers are being developed for scale prevention. “One of the biggest challenges for chemical processors is the criticality of the heat exchange equipment. It must operate, at the minimum, at design parameters because for every percentage point below design, the impact on productivity and profitability of the facility can be substantial,” says Kurita’s Tirreno. “This also impacts sustainability because it increases the use of power as the equipment has to work harder, so it’s critical to keep this equipment free of scale, but at the same time, environmentally friendly options are needed.”
In response, Kurita offers a polymer designed to keep heat exchange surfaces clean and remove existing deposition. Kurita’s DReeM Polymer, also referred to as Dispersion and Removal effect Management technology, is a unique chemistry developed to maximize heat-transfer-surface cleanliness and efficiency (Figure 3).
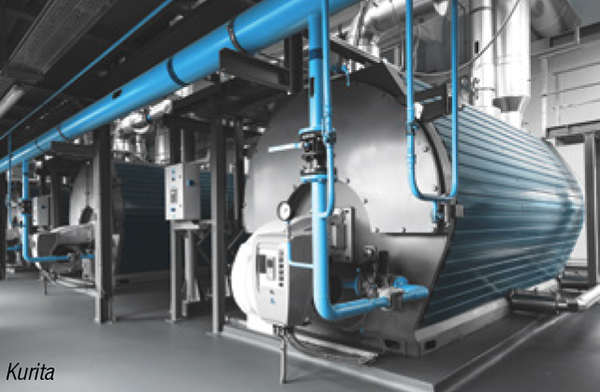
FIGURE 3. Kurita’s DReeM Polymer is a unique chemistry developed to maximize heat-transfersurface cleanliness and efficiency.
Film-forming chemistry is also being developed to replace chemicals that contain phosphates, such as those used for cooling and boiler water treatments. “Historically, utility chemicals have included some phosphorus component, but we are now seeing bans around phosphors, which create many problems in receiving streams,” says SUEZ’s Macios. “So, processors are seeking alternative solutions for cooling and boiler water treatment.” As a result, SUEZ developed E.C.O.Film for cooling water treatment, which doesn’t contain any priority pollutants and is based on simple carbon-, hydrogen- and oxygen-containing molecules that use the natural properties of the water being treated to create an engineered film on the surface of the metallurgy (Figure 4). Specialty chemicals are used to promote the formation of these films on metal surfaces. “We are also using very advanced surface analysis techniques to help ensure that we are creating these films and getting to levels of protection that exceed prior performance of phosphorus materials,” says Macios.
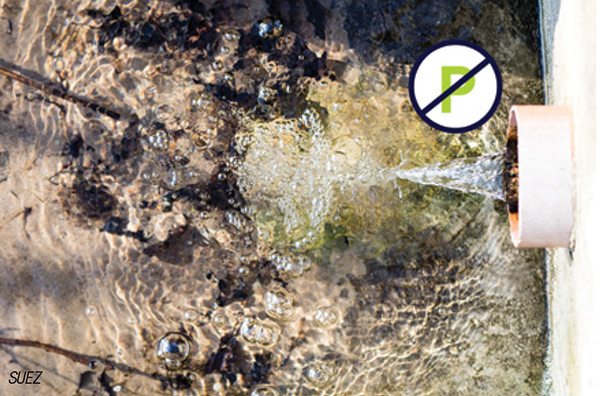
FIGURE 4. Film-forming chemistry, such as SUEZ’s E.C.O.Film, is being developed to replace chemicals that contain phosphates, such as those used for cooling water treatment
Along with kinder chemistries, automation technologies for control and dosing of liquid-solid separation chemicals in wastewater applications are available. Kurita’s S.sensing CS system was developed to manage the chemical feed, so the system proactively reacts and adjusts to variations in influent wastewater quality, enabling higher productivity, lower environmental impact and optimized wastewater treatment results. “Typically, in a water treatment facility, you monitor the cleanliness of the water in the effluent and then make adjustments based on that cleanliness, but the time span to see the results between adjustments can be hours,” says Tirreno. “This system uses laser technology to measure the influent water to detect production changes, unexpected spills and operational upsets within minutes. S.sensing CS has the capability to make immediate chemical adjustments to changing conditions within the facility, ensuring that chemical costs are lower and water quality needs are met in real time.”
Aquatech’s Chidambaran agrees: “In general, we see a desire to reduce and optimize chemical consumption and minimize the use of some chemicals that generate potentially hazardous byproducts,” he says. “Sometimes, excess chemicals are used continuously based on a programmed worst-case scenario. However, these conditions may only exist for a few days in a year. With real-time sensing, chemical dosing can be drastically reduced or eliminated, based on actual conditions, reducing the chemical cost and also any impact due to unintended byproducts.”
Aquatech recently developed BioFilmPro (Figure 5), a technology solution using real-time monitoring to address such problems. The technology uses an electrochemical method to control biofouling and dose chemicals only when necessary.
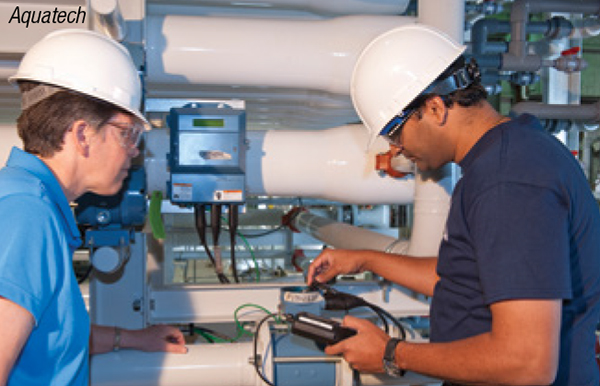
FIGURE 5. Aquatech’s BioFilmPro is a sustainable data-driven solution that effectively controls
biofouling by integrating real-time sensing and monitoring of biofilm formation with continuous
electrochemical deactivation of bacteria and controlled biocide dosing
Digitalization and analytics
In addition to the available technologies and eco-friendly chemistries offered by water treatment professionals, processors are requesting an enabling technology wrapper surrounding water treatment. “We are not only bringing mechanical equipment, membranes, molecules, chemistries and filters to processors, but we’re also bringing sensors, automation and analytics that help them solve problems by having data available around assets so that under any kind of operating conditions, operators can detect, predict and assure performance,” explains SUEZ’s Macios.
SUEZ’s InSight, a cloud-based asset-performance-management tool, uses data analytics to help ensure that water treatment assets operate at optimal performance by connecting key assets, such as boilers, cooling towers, condensers, RO membranes and tanks, into a single platform, which provides real-time visibility at an asset, plant or enterprise-wide level. “This allows users to predict what may be trending in the wrong direction and take action before it becomes a real problem,” says Macios.
Kurita’s Tirreno agrees that this is of growing importance: “If you have the ability to cognize via sensors and then add the ability to understand the impact via analytics, this results in a step change toward improving water management. Adding the ability to control and make changes remotely, on the fly, such as with our Lumyn technology, allows processors to identify and address potential issues before they happen. Having this interconnection of devices and understanding of how this influences water processes in the plant goes a long way toward improving sustainability.”
IntelliFlux’s Bhattacharjee adds that managing the data and complexity of water management systems and tying it into the overall health monitoring of the plant helps to make these assets an integral part of the overall process and sustainability effort. “We offer digitalization of the plant through a combination of software technologies and digital twins of the plant, including the water management operations, so that processors can enhance their process intensity or efficiency to achieve savings in operating expenses, enhancements in reliability of equipment, better product quality and improvements in sustainability,” he says. “Regarding water treatment, this may include a membrane separation technology with modules that are expensive to replace. Our technology helps reduce the frequency of replacement of those modules, because we can see when they will need to be replaced versus replacing them on a planned maintenance schedule, which provides a cost reduction. Another example might be using the technology to properly monitor chemical dosing of cooling tower water, which reduces chemical usage, thus reducing the cost of chemical management, as well as the waste that is produced as sludge or solids that processors typically have to pay to dispose of.”
TrendMiner offers software based on a high-performance analytics engine for data capture in time series, which allows process engineers and operators to search for trends and question process data, enabling them to make data-driven decisions that affect overall plant optimization, including water management, water treatment and sustainability decisions (Figure 6). “We have many different cases where it has been applied to water decisions,” says Fischer. “For example, a customer had issues with fouling of the nozzles that pump air through the water to begin a biological treatment process. As soon as the nozzles started fouling, the efficiency of the biological process was reduced. However, when they employed sensors and our analytics, operators no longer had to wait for bubbles in the water to detect fouling. Instead, the sensors detected issues and analytics examined the patterns and amount of airflow to determine when cleaning was needed before fouling occurred, so the process was optimized.
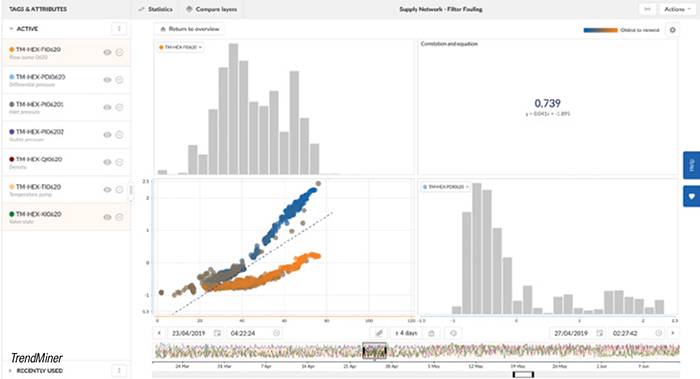
FIGURE 6. TrendMiner offers software based on a high-performance analytics engine, which allows processors to search for trends and question process data, enabling them to make data-driven decisions that affect overall plant optimization
“This ties into energy consumption and sustainability because the nozzles were used to transfer and mix oxygen into the process, but when fouling of the nozzles was prevented via the sensors and analytics, there was a more efficient oxygen supply and mixing operation in the bioreactors, which required less energy consumption,” explains Fischer.
Examples such as these demonstrate how digitalization and analytics can improve water treatment and drive sustainability. “As water treatment options continue to advance and improve, it just makes sense to combine them with industrial analytics and IoT [internet of things] to intensify and enhance the efficiency and sustainability of these processes,” says Fischer.