Smart devices are the foundation of a connected chemical plant, producing the data that can help you drive better decision-making across your operations. But having access to data is only the beginning — you also need to collect, orchestrate and contextualize it in order to truly realize value from it.
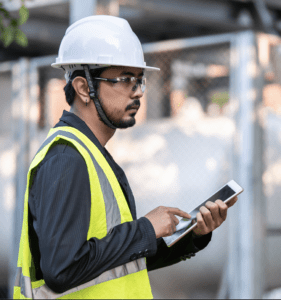
While smart devices provide the data-supported foundation for a connected plant, strategies must be in place to properly utilize all of the collected data to help improve operational performance
A recent poll of chemical industry leaders found that this process of turning raw data into actionable insights comes with some challenges. About 6 in 10 respondents reported difficulties integrating data across multiple systems, and 1 in 3 reported challenges converting data into actionable information.
Because every digital journey is different, there’s no set formula for harnessing data in your operations. But by using some well-established concepts — an intentional approach, an open architecture and layered cybersecurity — you can reduce risk in your projects and help make sure they not only deliver results today but also can be scaled across the rest of your operations at a later point.
An intentional approach
Large, enterprise-wide digitalization projects aren’t for everyone. In fact, large-scale implementations can sour your company’s leadership on digitalization because these projects can come with a big price tag and take years to deliver value.
Often, a better approach is to think big but start small. First, define your vision for how digital technologies and data-based insights can transform how you operate. Can it accelerate your design and development processes? Improve your production performance? Reduce your environmental footprint?
Then, after you’ve defined your vision, narrow your focus. Identify a small number of digitalization projects that both align with your vision and address your organization’s top challenges.
A common focus of many initial projects is improved production performance, and some key technologies can help you achieve this goal.
For example, you can model and ultimately optimize your production process using a digital twin, which is a living virtual replica of a physical system or entity across its entire lifecycle. A digital twin can also help you optimize plant operations in other ways — from improving operator readiness through virtual training, to speeding up maintenance by delivering digitally overlayed insights on a physical system in an augmented reality (AR) environment.
An asset performance management (APM) tool can also help you optimize your performance. By monitoring critical assets to detect anomalies or declines in their performance, you can maximize asset utilization and reduce unplanned downtime.
Another goal that is increasingly the focus of digital initiatives is improved sustainability. Using tools like energy-monitoring solutions, you can track energy consumption and intensity information to identify areas for improvement and optimization.
An open architecture
Starting small not only helps to limit the size of your project, but it also allows you to build your architecture in a scalable fashion, rather than building it all at once. Furthermore, it helps mitigate risk and accelerate value by “starting small” with pilots at select points in your plant.
Your architecture starts with the device layer. This includes all the data-producing devices in your chemical plant, from sensors, valves and flowmeters to process control systems and motor control centers. Data can be readily captured with wired or wireless plant data collectors and smart gateways.
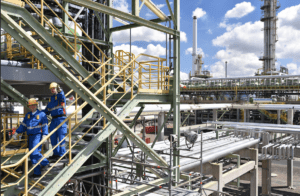
A chemical process plant contains multitudes of data-collecting devices that should be considered the first level of the digitalized architecture
You can build out or use existing process operations databases and historians around a specific area of focus such as a process unit or product line. After a successful implementation, consider expanding the database to scale up across multiple process units, sites or even the enterprise.
The middle layer is where raw device data is transformed into powerful insights. A key component of this layer is your scalable industrial internet of things (IIoT) platform. It should be able to collect, aggregate and access operations data from disparate sources in your plant. And it should connect to the tools that deliver insights to employees, like your analytics software and manufacturing execution system (MES) platform.
When building your architecture, consider your long-term needs. For example, by selecting technologies that use open communication standards such as MQTT or database connectors (open APIs) over EtherNet/IP, you can build your architecture for interoperability and scalability. This can help you reduce costly integration challenges and achieve a seamless flow of data across your plant and enterprise systems. And it can help you more easily expand your digital technologies to more use cases in the future.
What’s more, a seamless data flow allows you to create a digital thread, which is a continuous data trail that spans and connects every point in your value chain. And when you can capture insights anywhere and share them everywhere, you can break down barriers between your business functions and reimagine how you design, create, make and sell products.
Layered cybersecurity
Securing your increasingly connected chemical plant is about more than protecting data. Cyberattacks in the oil-and-gas, food-and-beverage and water and wastewater industries have impacted operations and even threatened to put people in harm’s way. Such incidents are a very real threat for chemical operations, as well.
What can you do to help protect not only your data but also your people, processes and overall business? The best practice is to use a layered and comprehensive security approach that adheres to the defense-in-depth concept, which assumes that any one security measure can and likely will be defeated.
Elements of your architecture can support a layered security approach. Modern distributed control systems, for example, are now built to align with international security standards like IEC 62443, which defines procedures for implementing an electronically secure industrial automation and control system. But you also need a mix of other security measures, like network segmentation, strong password policies and physical access restrictions, to help combat today’s diverse and ever-changing threat landscape.
If you’re light on resources, it may make sense to bring on a partner to help address your security needs. A partner can help with a one-time need, whether it’s performing a security assessment, providing training, or helping develop response and recovery plans. They can also help manage ongoing security efforts, such as by doing continuous monitoring to help detect anomalous and potentially malicious activity on your networks.
A just-right approach
The data you need to drive better decision-making may already exist within the installed base in your chemical plants. Tapping into it doesn’t need to be a monumental effort. With a planned and purposeful approach, you can securely access data and turn it into actionable information that empowers employees, all with minimal cost, effort and risk. ♦
Edited by Mary Page Bailey
Author
Rick Ng is the strategic marketing manager at Rockwell Automation (Email: [email protected]). He has more than 25 years of experience as a global market development manager, technical advisor and project manager in the oil-and-gas and chemical industries with Sasol, Chevron, and ExxonMobil before joining Rockwell Automation in 2021. Currently, he is the global market development manager responsible for industry strategy and marketing in the chemicals and oil-and-gas sectors. His role includes developing market strategy to capture market share and business growth in these industries. His educational background is focused on chemical engineering. He has a PhD and a master’s degree from the California Institute of Technology and a bachelor’s degree from the University of Houston.