Wearable technologies help chemical processors improve productivity and safety of workers
Wearable technologies — cameras, tablets and other devices loaded with applications (apps) and software that can be attached to the body or personal protective equipment (PPE) — are catching on in the chemical process industries (CPI) because they provide an efficient way to increase productivity and enhance safety for maintenance technicians and field operators.
Technology drives trends
While the concept is not new, as wearables have been available for years, the technology has dramatically improved, making them more user-friendly, feature-rich and suitable for hazardous environments than previous iterations, opening avenues for use in a variety of industrial applications. Wearables are being applied to enhance maintenance and operator activities by providing digital libraries of necessary documents and over-the-shoulder coaching, and are improving worker safety by supplying location, health and other information about the wearer in an effort to assist with emergency response, mustering and access control.
“Three factors are making wearable technologies more prevalent today: improved devices, the ability to design end-to-end, integrated solutions and better connectivity options,” explains Tracey Countryman, managing director and global lead for Industry X.0 Digital Manufacturing and Operations at Accenture (London, U.K.). “In the past, the devices were clunky, not suitable for industrial or hazardous environments and were often carried in a heavy metal container that had to be strapped on. However, they’ve come a long way toward reconciling themselves for the industrial environment. Today’s versions are lightweight, durable and have better enclosures, so they can be certified for use in hazardous environments and are available at a better price point.”
She adds that by leveraging the newest technologies to build more customized, end-to-end integrated software solutions, facilities are able to digitize the entire work process and load it into a device where workers can access documents, instructions, training videos, work orders and the like via apps and voice commands. The third component is connectivity. “Three to four years ago, only a few plants had WiFi, but now more facilities are employing WiFi for pervasive connectivity. Bluetooth is also widely used and 4G and 5G technologies are available at lower costs, making connectivity a much less expensive, more viable and easier-accessed prospect in industry than ever before,” notes Countryman. “These three factors are driving the adoption of wearable technologies for industrial use.”
And, statistics demonstrate the anticipated growth. “The Industry 4.0 market opportunity is currently worth $110 billion by total economic value, with Accenture estimating that the industrial internet of things (IIoT) could impact 46% of the global economy, estimated at $14 trillion, by 2030. In the connected worker space, wearable technology and wearable sensor devices alone is growing at a predicted 13.1% compound annual growth rate and is estimated to reach $4.3 billion in the next 20 years,” says Mark Bernstein, CEO of Wearable Technologies, Ltd. (Leicestershire, UK), quoting from an Accenture Industrial Internet of Things Positioning Paper Report.
More specifically, Accenture’s Countryman, quoting Accenture’s Digital State of the Industry Report, adds that when chemical companies were asked how much they’d invest in mobility/wearables in the next 12 months (from 2018), 77% said they’d invest nothing; however, 16% said they’d invest between 21% and 40%. When asked where digital investment for product and operations will be in the next three years, 24% of the top three chemical companies cited mobility/wearables.
“The internet of things is affecting all our lives — small sensors sending data via the internet to and from connected homes, connected cars and connected factories. It is inevitable that most industrial workers in the developed world will, in years to come, wear sensor devices to monitor their health, safety and efficiency,” says Bernstein.
But how do wearables help increase productivity and enhance safety? “First and foremost, wearable devices are productivity boosters because most of them can be loaded with digital versions of work procedures and other documents that maintenance technicians and field operators need to do their jobs and these documents and information can be accessed by voice. So instead of carrying binders or a tablet which they have to keep picking up to search for the necessary information and then put down to complete the task, they can quickly locate the information, view the instructions and work on the equipment all at the same time because their hands are free,” explains Sanjay Jhawar, co-founder and president of RealWear, Inc. (Vancouver, Wash.) “And because you can operate these devices hands-free, they can be used in locations where handheld devices would be inconvenient or impossible to operate due to protective gloves or other PPE or while climbing into a confined space such as a distillation column or vessel, and this is a safety enhancement.”
In addition, several available devices include location and other sensors to detect falls, unresponsiveness and dangerous health conditions and assist with mustering, access control and emergency response.
Boosting productivity
One of the biggest productivity benefits associated with wearables is the ability to not only store, but also to easily access, necessary documents and videos, on demand, in the field.
“During the digital transformation, we aim to provide customers with digital solutions and opportunities using software, hardware and services that improve safety, productivity and collaboration,” says Veronica Turner, business development leader with Honeywell Process Solutions (Houston). “So when we think of field personnel, our Intelligent Wearables — android devices that can be hooked through clips to an industrial hard hat — are an ideal solution. These devices are loaded with software that provides field personnel with the necessary tools, such as forms, P&IDs [piping and instrumentation diagrams] drawings, manuals and libraries of procedures in PDF format, as well as photos and videos, so they can complete tasks more efficiently” (Figure 1; Courtesy of Honeywell).
Accenture’s Countryman agrees: “If you go to a chemical plant or [petroleum] refinery today, it is highly paper-driven. There are binders for work orders and work procedures. It is not an efficient process. However, we are seeing a major trend around digitizing work processes, which allows workers to access the needed information and pull up different drawings and instructions in the field to work on a particular asset.
“Wearables allow them to scan barcodes for a particular asset and quickly access operating procedures and real-time information related to that asset, so they can do the work efficiently and properly the first time without going back for tools or information. Today, there’s a lot of time spent not having the right information at the right time to do the right work, but people are beginning to look at mobility and wearables to address that issue.”
Taking it a step further are applications, such as Video Assist from Honeywell, which allow users to make their own video library of work procedures and break the procedures down into rational steps. “The entire video can be viewed, if needed. However, workers who don’t need to watch an entire five minute video, but may need to review just one step in a process, can access only the part they need using voice commands, making it easy to navigate among the steps. Search engine optimization allows procedures to be tagged with key words, so workers can access the information they need,” explains Turner.
While it does take effort to add data and work instructions to the software in the devices, it is often worth the effort in increased productivity, according to the experts. RealWear’s Jhawar says customers who have done ROI studies often see task time reduced by 40% and error rates reduced by 80%. Likewise, Accenture’s Countryman cites their most recent digitalization project, in which the customer sought to improve productivity and maintenance planning. “They had 10,000 pieces of equipment that were barcoded and an integrated, realtime information system between document management systems, SAP, work orders and all the associated things that needed to come together to do the work,” she says. “After the project, they had 100% compliance with time reporting and they were expecting a 2 to 5% production increase and a 15 to 20% productivity increase. This is in line with what we anticipate for customers who are using wearables for over-the-shoulder coaching and digitizing procedures and other documents.”
Live experts on demand
Many of the wearable devices contain a camera along with software that allows field personnel to place a call and connect in real time with an expert selected by the user. Experts are typically control-room personnel, maintenance professionals, vendors or call centers, depending upon who is chosen by facility management. The subject matter expert can guide the field worker by “tele-stration,” meaning they can not only see what the field technician is looking at via the camera, but also use the camera to verbally and visually assist the technician by adding drawings, arrows or writing on the image.
“We offer the Onsight Cube EX [Figure 2], which is a wearable camera certified for hazardous areas that, along with the Remote Field Expert software feature enabled, allows a person in the field to initiate a video call so they can communicate directly with tech support on the spot,” explains Justin Olivier, product manager for mobility for the Americas with ecom Instruments, a Pepperl+Fuchs brand (Twinsburg, Ohio).
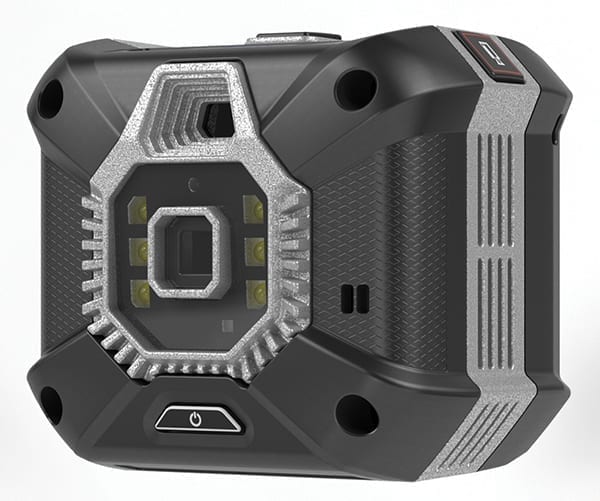
Figure 2. Pepperl+Fuchs’s Onsight Cube EX is a wearable camera certified for hazardous areas that, along with the Remote Field Expert software feature enabled, allows a person in the field to initiate a video call so they can communicate directly with technical support. Pepperl+Fuchs
Olivier provides an example of how a customer with downed equipment on an oil rig used this technology to their advantage. “The technicians on site couldn’t find the root cause of the problem causing downtime. The company was contemplating flying an expert out, which was an expensive prospect,” he says. “Not only were there associated travel costs, but the rig was losing big money each day the equipment was down. However, they were able to use the Cube and software so the expert could physically see the asset. He was able to provide instructions on the spot. That one application saved the customer hundreds of thousands of dollars from a productivity standpoint because they didn’t experience additional downtime while waiting for an expert to be flown to the rig,” he says.
Similarly, RealWear had a customer who experienced an explosion that damaged several distillation columns. A complete plant shut down was needed to repair the columns, resulting in very expensive downtime, so there was an urgent need to complete the repair in a short amount of time.
“They purchased a dozen devices and sent subcontractors into the distillation columns to perform the repairs. The contractors wore the devices on their heads and took photos and videos of the work being done so that at the end of the shift, they could transfer the photos and videos to a laptop and have plant personnel audit the work based on the images,” says Jhawar. “It streamlined their inspection and approval process, shortening the job by several days and providing payback for the technology in under 72 hours.”
This can also provide savings when “witnessing,” which is the act of verifying that newly delivered equipment is in working order after installation. “We have customers who use wearables to perform witnessing activities in distant refineries and oil rigs remotely over video call to avoid physical travel,” says Jhawar.
Enhancing safety
Wearable technologies also improve safety functions in chemical facilities. “In the industrial markets, there is a growing request for safety products in the wearables realm and for smart PPE, such as technologies for location and access control. In the past, most solutions were extremely expensive to install,” says Amanda Alexander, global product manager with Emerson Automation Solutions (Shakopee, Minn.). “So we created a product for location technology using the WirelessHART infrastructure and it has removed a lot of the cost, while providing necessary safety benefits.”
Emerson offers its Location Tag (Figure 3) for use in geofencing and mustering applications.
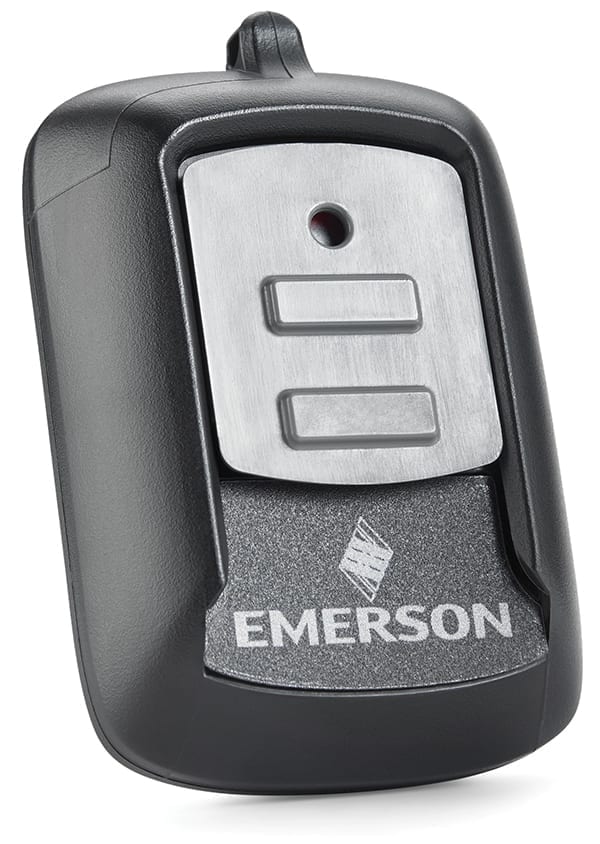
Figure 3. Emerson’s Location Tag can be used to create a virtual fence for access control and mustering purposes. Emerson
Many chemical facilities need to maintain fences for access control around hazardous areas and would prefer to have a virtual fence rather than a physical fence. Using Location Tag, they can create a virtual fence and apply certain rules to it. “For instance, if someone is wearing a tag and they do not have permission to enter a particular zone within a facility, an alert will be sent to the appropriate personnel if that person enters that area,” explains Alexander. “This also works within the efficiency realm regarding contractors, as it enables facilities to create zones for the contractors by providing them with tags that allow them entrance into only the accessible areas of the facility.”
The tag can also be used for safety mustering. “Typically the muster zone is a designated area and when there is an emergency or drill, employees report to the zone, find a supervisor or sign into a sheet that is uploaded and recorded later to determine how long it took employees to reach safety. Simplifying the process, Location Tag creates a muster zone with a virtual fence and when tagged employees arrive, they are automatically counted. On the flip side, if someone does not arrive, an alert is sent and the person can be located by emergency responders using the sensor on the tag. In addition, there is a button on each tag that can be pressed in the event of emergency or injury to send an alert over the user interface.”
Wearable Technologies, too, is using wearables to keep industrial workers safer by delivering data-led, actionable insights in real time to site managers and health and safety managers. “We are delivering big data relating to workers, to the data lakes already holding other types of data such as plant and weather data to facilitate the application of artificial intelligence across the large enterprise,” says Bernstein. The company’s Eleksen Connected Worker Solution (Figure 4) provides the ability to monitor industrial workforces to improve safety and increase productivity by linking smart garments to a choice of personal sensor devices, such as for gas, noise and physiology, to a reporting dashboard that enables managers to monitor the conditions of their workforce in the field and onsite in real time, helping mitigate risk, reduce costs and improve performance.
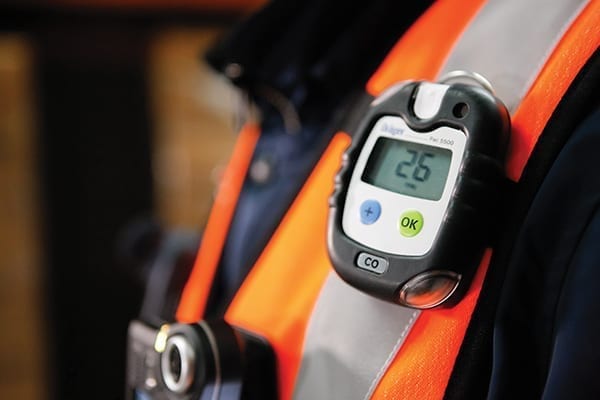
Figure 4. Wearable Technologies’ Eleksen Connected Worker Solution monitors industrial workforces to improve safety and increase productivity by linking smart garments to a choice of personal sensor devices, such as gas, noise and physiological, to a reporting dashboard that enables managers to monitor the conditions of their workforce in the field and onsite in real time. Wearable Technologies
As wearable technologies continue to improve, they will become an extension of Industry 4.0, connecting not just plant data and analytics, but that of worker productivity and safety, as well. “If you think of sensors as instrumenting the plant itself, it’s not a great leap to think of them as instrumenting the humans operating the plant. And, if you can combine IoT from humans and IoT from the plant, then you will have a complete picture of your operations,” says RealWear’s Jhawar (Figure 5). “This is important because the maintenance and reliability performance of the manufacturing operation depends upon how well the field technicians maintain the assets, as well as their safety. At the end of the day, it’s all about the effectiveness and efficiency of how the people in the field interact with the assets that gets processors to best-in-class operating performance. Wearables are all about helping individuals be the best version they can be because they have access to best-in-class knowledge at all times.”
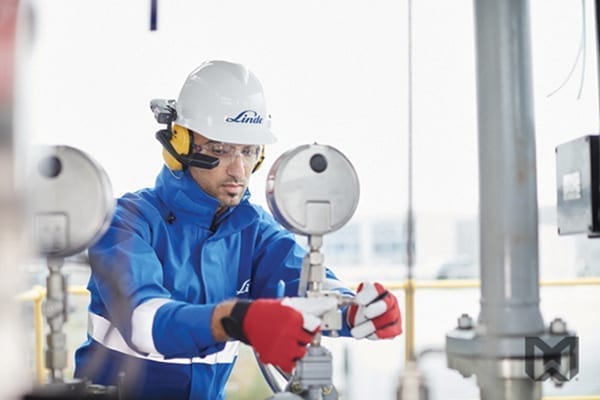
Figure 5. Wearable devices, such as those provided by RealWear, are productivity boosters because most of them can be loaded with digital versions of work procedures and other documents that maintenance technicians and field operators need to do their jobs — these documents and information can be accessed by voice. RealWear