Moving 3-D printing beyond prototyping toward production of finished parts has driven innovation and spurred investment, but has also forced the industry to address a host of challenges
Industrial use of 3-D printing (3DP; also known industrially as additive manufacturing; AM) for research and development (R&D) projects and prototyping is widespread, but the focus of this potentially disruptive technology has shifted toward utilizing 3DP as a manufacturing platform to produce finished parts. Fully realizing the benefits of 3DP in the manufacturing space requires the industry to address a number of challenging questions about equipment capabilities, material properties and about the integration of 3DP into wider industrial processes.
“3-D printing is already a key R&D and prototyping tool, but a fundamental shift is ongoing right now to use it for the production of final parts,” explains Terry Wohlers, a 3DP industry analyst and consultant with Wohlers and Associates (Fort Collins, Colo.; wohlersassociates.com). “This is where the most significant financial benefits are found.
3DP technology continues to advance in terms of printing equipment, availability of engineered raw materials, and software for designing and building 3D-printed components. Along with these advancements has come investment from companies seeking to position themselves to either supply the 3-D printing industry or to take advantage of the benefits offered by this manufacturing approach, which include design freedom, mass customization and the ability to reduce or eliminate assembly. Although the 3DP industry remains relatively small (estimated $5.2 billion in 2015, according to the Wohlers Report 2016), it is growing rapidly (26% compound average growth rate in 2015; anticipated growth to $26 billion by 2021, according to the report), and a number of indicators are signaling that 3DP is entering mainstream industry, including investment from both the public and private sectors.
Reality replaces hype
As AM’s objective crystallizes around production of final parts, the frothy hype surrounding industry a few years ago has given way to an optimistic, but sober reckoning of key real-world issues: chief among them are how to ensure the safety, quality and consistency of 3D-printed components and how to integrate AM equipment and digital attributes into broader manufacturing processes.
“For many industries, AM offers huge potential benefits, but as you move from prototyping to production, there are many questions that need to be considered carefully in order for these potential benefits to be made real,” explains Chris Chung, head of strategic development and external affairs at Lloyd’s Register (LR; Singapore; www.lr.org). “We need to get a good handle on all essential variables for AM processes, and develop standards for systems and personnel, so that there is a methodology to producing a series of AM-printed products, and the effectiveness of the printed parts can be demonstrated,” says Andy Imrie, LR business development and global product launch manager. “We want to make sure that AM enters the mainstream in a safe way.”
In addition to ensuring the quality and consistency of final parts from 3PD, the industry must also address questions of reliability and repeatability of the process itself. “When you are talking about mass production of finished parts, machine uptime is a critical aspect,” says analyst Wohlers, as are the supporting processes, equipment and systems upstream and downstream of the printer. “The overall process steps need to be streamlined and automated for 3DP manufacturing processes,” including powder handling before, for example, and surface finishing after. “Companies are still figuring out how to do this,” he says.
In October 2016, the LR Foundation (www.lrfoundation.org.uk) released a “Roadmap for Additive Manufacturing,” a consultation document that outlines the work needed to safely implement AM technologies for commercial production of final parts, especially in safety-critical areas. Because the roadmap was created under the purview of the not-for-profit LR Foundation, it is in a position to examine longer-term, industry-wide concerns that individual companies might not consider, Chung and Imrie explain. The roadmapping process identified four principal challenges that the AM industry must resolve, including qualification of AM technology, supply-chain standards, workforce development and realizing safety benefits.
Designed for 3DP
A significant portion of 3DP technology is subject to patent protection, so in some cases, raw material costs are high where equipment vendors produce proprietary materials for use with specific printers. But the industry is gradually moving toward a freer model, where printer consumables can be made by third-party producers. The chemical process industries (CPI) have become involved in developing and supplying raw materials specifically for use in 3-D printers.
Polymers designed for use in 3DP require different properties than those for injection molding, because engineers need to consider the nature of the process, in terms of rheology, and the stability of the polymer at high temperatures. Temperature history is more important in 3DP due to the significantly longer cycle times, and while the pressure is generally ambient in 3DP, injection molding occurs at high pressures, controlling the packing and dimensional stability of the final part.
“To engineer a polymer specifically for use in 3DP applications, you have to think in parallel about the polymer chemistry and the equipment in which it will be used. For the material, you need to focus on the thermal management of the process system (that is, how heating and cooling are accomplished),” says Dominique Giannotta, Solvay’s manager of Sinterline nylon products for Solvay S.A. (Brussels, Belgium; www.solvay.com). Three general approaches exist for developing a polymer for 3DP, Giannotta explains: modify the material to work with existing equipment; start with the material and design equipment that works for that material, or a blend of the two. Solvay is working mainly on the latter two approaches, he says.
For example, Solvay was a pioneer in developing the high mechanical- and thermal-performing range of polyamide-6 (PA6) powders, known as Sinterline, which are specially engineered for selective laser sintering (SLS), a prominent 3DP technology class (for more on 3DP techniques, see Chem. Eng. February 2015, pp. 20–23).
Solvay is joined by BASF, Eastman, Evonik and others in developing raw materials specifically for 3DP.
3D-print simulation
Solvay’s Sinterline PA6 is involved in a project that is an example of how 3D-printed finished parts could be developed. Specifically, the project, known as Polimotor 2, aims to demonstrate operation of a fully plastic internal combustion engine for a racecar. Solvay’s Sinterline material was used to 3D-print an air-intake plenum for the engine. For Solvay, the inclusion of a 3D-printed part is helping to change the prevailing mindset about the performance possibilities for such components, Giannotta says.
The Polimotor project is also illustrating the importance of simulation software in understanding the performance and properties of a plastic component before it is made. “Simulation in 3DP is improving in its ability and increasing in its importance, as companies are adapting simulation techniques currently used for injection-molded parts to model 3D-printed parts,” Giannotta says. “We are now assembling a raw-material database to allow designing a finished part from the beginning that will be able to withstand the demands of the application,” he remarks.
The Polimotor project represents the first time that Solvay’s new simulation tool (known as MMI Technyl) was used along with the Sinterline PA6 material to produce a 3D-printed final part. “In this case, experimental testing of the plenum confirmed what was indicated in the simulation work,” Solvay’s Giannotta explains, and the simulation helped to answer questions about how the part met engine specifications. “Simulations offer the ability to save time and money for experimental testing, and also allow the ability to modify the design prior to the start of production,” he says.
Metals and quality
Alongside engineered plastics, “the use of 3DP for manufacturing finished metal components is a super-hot area right now,” says Wohlers, and improved materials are becoming available. For example, Alcoa (Pittsburgh, Pa.; www.alcoa.com) recently opened a state-of-the-art facility for manufacturing metal powders specifically engineered for 3DP. Located at Alcoa’s Technology Center near Pittsburgh, the facility will produce proprietary titanium, nickel and aluminum powders optimized for 3D-printed aerospace parts. Alcoa also has invested in a range of technologies to further develop AM processes, product design and qualification, the company says.
Because product quality and consistency are critical in metal part production, the atmosphere inside the build chamber becomes very important. Many 3DP processes use high-purity inert gases, such as argon or N 2, to control the influence of oxygen and water during the fabrication of the part. However, the presence of traces of O 2 and humidity, due to incomplete purging, machine leakages, or from the metal powder itself, can negatively affect mechanical properties or chemical composition of the end product — for example, leading to oxidation of the metal, decreased fatigue resistance and sub-optimal performance. Industrial gas companies are recognizing this need and getting involved to support 3DP processes.
At European tradeshows last Fall, Linde Gases (Munich, Germany; www.linde.com) launched ADDvance O2 precision, a first-of-its-kind measuring and analysis unit that enables metal additive manufacturers to analyze and control more precisely the level of O2 and humidity within the printer chamber, the company says.
The new technology — developed in response to a need identified by aerospace company Airbus Group Innovations — can detect O2 levels up to 10 parts per million (ppm) within the printer chamber and then modify the gas atmosphere by adjusting the level of argon or nitrogen. ADDvance O2 allows for more accurate detection of oxygen and humidity without cross-sensitivity to other species in the complex mixture of impurities.
“Handling powders can also introduce some humidity, and this is known to increase porosity in the final part,” explains Pierre Foret, of Linde Gas. “ADDvance O 2 allows manufacturers to accurately and reliably measure oxygen in the build chamber and lower the levels by adjusting inert gas flow,” he notes. Currently with the instrument, a small pipe is installed on the printer and sucks a sample of gases from the build chamber and analyzes it externally for O2 and H2O content, Pierre explains, but in the future, the sensor should be integrated into the print chamber.
The ADDvance O2 launch comes on the heels of Linde’s recent opening of a dedicated industrial gases laboratory specifically for AM in Unterschleissheim, Germany. The focus of the facility is to study the effects of various atmospheric gases and gas mixtures on the different metal powders used in AM to optimize the various layering processes, Linde says.
Speed and post-processing
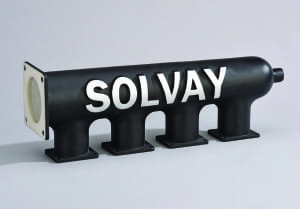
Figure 4. This 3D-printed air-intake plenum was made as a finished part for a project aimed at operating an all-plastic internal combustion engine
Two significant obstacles to widespread adoption of 3DP for manufacturing finished parts have to do with its speed, and the fact that 3D-printed parts often have to undergo post-production finishing steps in order to be suitable for use. If these steps are not integrated well or are costly, it may make the particular part uneconomical for certain applications. A number of approaches and technologies are aimed at improving speed and streamlining the downstream processing of 3D-printed parts.
In some laser-based 3DP technologies, for example, unfused material may have to be cleaned off in a post-production process. Linde Gas has developed a post-production cleaning technology that claims to be faster, more cost effective and more environmentally friendly than existing alternatives, such as power-washing and sand-blasting. Tradenamed CryoClean Snow, the method uses small particles of dry ice (solid CO2) for cleaning. The particles are formed on-demand by feeding liquid CO2 into a specially designed snow chamber to form very hard dry-ice particles. The particles are then propelled against the component surface using compressed air. Uses for CryoClean Snow in the context of 3D-printed parts include removal of unfused powder from laser-fused AM parts and removal of surface oxides from steel, aluminum and other metals.
Printing technologies are also evolving to reduce post-processing. Rize Inc. (Woburn, Mass.; www.rize3d.com) has developed a printing technology, known as augmented polymer deposition (APD), that the company says achieves zero post-processing (such as filing or sanding) of parts and generates no toxic fumes. APD allows the extrusion of Rize’s proprietary engineering-grade thermoplastic simultaneously with the jetting of functional inks that can change the properties of the thermoplastic. The printer is capable of jetting these functional inks with each voxel (3DP version of a pixel) of material, so parts can be stronger, and downstream processing steps can be eliminated, the company says.
Another factor limiting the use of 3DP technologies for finished parts is their relatively slow speed. “Current technologies require many hours to days to generate parts, which is acceptable for prototyping applications, but not for manufacturing of finished parts,” says Jason Rolland, vice president of material for Carbon (Redwood City, Calif.; www.carbon3D.com), a company that recently introduced a printer designed to address both speed and finishing issues in 3DP.
When selecting materials and printing technologies, there are often tradeoffs between mechanical properties and surface finish. “Light-based technologies (such as stereolithography) offer the best choice for surface finish and resolution, but the parts have poor mechanical properties, especially when compared to injection-molded thermoplastics, explains Rolland. “Heat-based technologies [like fused deposition modeling and selective laser sintering] offer better mechanical properties, but are limited with respect to surface finish and resolution,” he says.
Carbon recently introduced a unique technology, known as continuous liquid interface production (CLIP; Figure 1) that the company says addresses significant current gaps. CLIP is a photochemical-based process in which ultraviolet (UV) light is projected through an oxygen-permeable window into a reservoir of liquid UV-curable resin. The resin solidifies in a specific shape according to a series of UV images projected through the window. The built part rises out of the reservoir as the UV images induce resin hardening.
The company has also developed resins with both UV- and thermal-cure components, which allow improved strength after triggering secondary heat-activated reactions after printing. Carbon’s printer, known as the M1, can make parts with high resolution, engineering-grade mechanical properties and surface-finish properties like those of injection-molded parts, the company says. CLIP is faster than current stereolithography technology, Rolland says, and it does not involve layering of material, which, when coupled with digital optics to define part geometry, results in a clean surface finish.
“By expanding the available formulation space to include thermally curable materials, we open up a much broader range of chemistries and mechanical properties than ever before,” Rolland says.
3D Printing 2.0
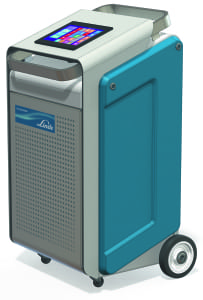
Figure 2. The ADDvance O2 instrument from Linde Gas samples oxygen and humidity in build chambers of 3D metal printers, allowing better part integrity
While companies work to adapt 3DP technologies to commercial manufacturing, researchers are already exploring the next generation of 3DP capabilities and identifying ways to address the limitations of current 3DP. University-industry partnerships in this area provide insights about where the 3DP industry is heading. One example is the New York State Center for Advanced Technology in Additive Manufacturing and Functional Printing at the Rochester Institute of Technology (RIT; Rochester, N.Y.; www.rit.edu/amprint). Operational since Spring of 2016, the center is focused on addressing some of the limitations of current 3D printing. The RIT AMPrint Center brings in R&D contracts from other companies and government agencies.
“Currently, 3D printing is slow, so we are looking for ways to apply and adapt high-speed document printing technologies to 3DP. We want to be able to print hundreds of layers per minute with multiple materials,” says Denis Cormier, RIT engineering professor and the center’s director.
“We are looking at blending materials in 3-D printing applications so that the products can serve other functions beyond just the component,” Cormier explains. Some examples include 3D-printed heaters, printed circuits, and materials that serve thermal, optical, energy storage or other functions. “There is a huge focus on chemistry and chemical engineering in how you engineer the 3-D print ‘inks,’” he says. This can include synthesizing nanoparticles that can impart functionality and figuring out the chemistry of how to turn these molecules into 3D-print inks.
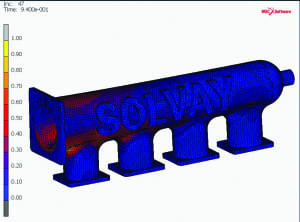
Figure 3. Simulations helped Solvay ensure that a 3D-printed part met specifications for an engine project
There are 12 active research projects ongoing at the Center, which has been operational since Spring of 2016. Some of the projects include the 3DP of low-cost, disposable medical devices, 3DP of carbon-fiber composite materials, and 3D printing of ceramic materials combined with other materials, such as metals and polymers. “We are figuring out how to use metals and plastics along with ceramics, which typically require high-temperature firing steps that are not compatible with plastics,” Cormier says, “and we are looking at photonic curing processes that do not require high temperatures.”
Multi-material printing
Finished products often are composed of more than one material, and a number of startup companies are seeking to advance multi-material 3-D printing. Voxel8 (Somerville, Mass; www.voxel8.com) was spun out of a research laboratory at Harvard University and has developed methods for making 3D-printed electronics (wires and components printed together). The Voxel8 technology can lay out precise circuits in three dimensions, allowing electronics without flat-printed circuitboards.
Markforged (Cambridge, Mass.; www.markforged.com) has developed 3D printing hardware and materials to combine the design flexibility of 3D printing with high-strength engineered materials, such as carbon-fiber-reinforced plastics, fiberglass, Kevlar and others.
Xjet (Rehovot, Israel; www.xjet3d.com) is working on technology to use metal nanoparticles to create specially designed liquid metal “inks” that aim to provide faster speeds and better surface finish.
In the next generation of 3D printers, the term “4D printing” will become more familiar. 4D printing describes 3D-printed components that are able to change their shape or other physical function based upon the addition of an external stimulus, such as heat, pressure or chemical interaction. For example, piping systems that operate without the need for pumps, valves or pipes designed for different pressures. This means less physical parts or control systems to maintain or fail so safety can be improved.
CPI applications
Much potential exists for the use of 3D-printed parts in the CPI. Among them are the following:
Reducing part numbers in equipment. “With traditional manufacturing, many parts must be assembled from smaller pieces, because of the limits on what shapes can be cast, milled or molded,” Wohlers explains. “The technique of building in layers allows for parts to be combined digitally that could include 20, 50 or 100 parts into one, two or three parts,” he says. Fewer parts means big savings in expensive manufacturing processes, assembly, labor, inventory and maintenance, he says. For example, a joint venture from GE Aviation and Safran Aircraft known as CFM International recently unveiled a 3D-printed component called the LEAP jet fuel injection nozzle. With 3DP, the part count for the assembly of the nozzle was reduced from from 18 to one, GE Aviation says. 3DP could also allows the use of cheaper and simpler designs that eliminate joints and welds.
Spare parts. 3DP could be used to make spare parts for older equipment, and could allow quick turnarounds for replacement parts. By replacing the conventional manufacturing technique of punching, rolling and seam-welding, improvements could be made in filter support geometries that have resulted in optimized fluid flow in certain applications. 3DP allows design flexibility that could result in conical, inline filter supports for existing filtration and pumping systems with efficiency gains and a reduction of raw materials used in the manufacturing process.
Engineered lattice structures. Although the engineering advantages of lightweight cellular materials are significant, limitations of conventional manufacturing processes have made it difficult or impossible to fabricate many types of cellular materials. 3DP technology allows engineered lattice structures with “engineered” geometries. This has been a major focus of research by RIT’s Denis Cormier.
Heat exchangers. A project led by the University of Maryland (College Park, Md.; www.umd.edu) involving Oak Ridge National Laboratory (Oak Ridge, Tenn.; www.ornl.gov) and several companies is developing a miniaturized air-to-refrigerant heat exchanger that is more compact and more energy efficient than current market designs. The heat exchanger will have at least 20% less volume, 20% less material volume, and 20% lower approach temperature compared to current multiport flat-tube designs, and it will be in production within five years. The heat exchanger, which acts as both an evaporator and a condenser, can be applied to commercial and residential air-conditioning or heat-pump systems with various capacity scales. Prototype 1- and 10-kW designs will be tested and then improved as necessary for final tests and demonstration in a three-ton heat pump.
New component designs. 3DP allows the design of new components for equipment like pumps, compressors, impellers and others.
Lloyd’s Register Roadmap for Additive Manufacturing
The four main challenges for the use of 3DP for finished parts, as identified in the LR Roadmap (released 2016), are the following:
Qualification of AM technology. Pointing out that a fundamental understanding of material properties and performance (in addition to how to reliably measure them) is key to designing and building safe products, the roadmap calls for increased research attention on how to “measure appropriate properties and performance under operating conditions, in order to generate relevant and repeatable information.” The roadmap also calls for the establishment of an international, publically available database with contributions from academia and industry to populate it with safety-relevant and validated data on testing in this area. In the rapid growth of AM, this type of information generated by companies is often not made available for commercial reasons. Also, the roadmap says that qualification programs for AM need to be established that are similar to those used in traditional manufacturing approaches.
Confidence in the supply chain. For this challenge, the roadmap calls for standards surrounding how to define raw materials for AM, as well as systems to allow traceability of components back to their suppliers and sub-suppliers. And while the LR document acknowledges that standardization during periods of rapid technology evolution carries the risk of perpetually outdated standards, it suggests a “rapid method of qualifying processes based upon control and monitoring of critical fundamentals, rather than just being machine-specific.”
Establishment of a competent and qualified workforce. The uptake of any technology, no matter how beneficial or disruptive, depends on a workforce with essential skills and knowledge, the roadmap points out, so it calls for a knowledge framework for additive manufacturing technology. “The opportunity exists to develop a framework of what good additive manufacturing education and knowledge should look like to enable development of essential skills training across the globe,” the report says. “It is important to establish a qualified and competent workforce to operate machines and support installations in a manner that not only results in components of the correct quality, but also keeps the working environment safe.”
Enabling safety enhancements with AM. AM techniques offer opportunities to enhance safety, the roadmap points out, through design optimization, embedding sensors for self-aware “smart” materials, and devising 3D-printed parts that change in shape or other function in response to external stimulus.
3-D Printing Moves Toward the mainstream
“The 3DP industry is finally receiving well-deserved attention and respect,” says 3DP industry analyst Terry Wohlers, and that attention is backed up by substantial investment from several sources, including state and federal governments, large chemical companies and equipment makers.” The leading industry sectors for 3D-printed finished parts are aerospace, medical devices and the dental industry. Others sectors, such as automotive, oil and gas, and others, will likely follow as technology further improves.
General Electric (GE; Fairfield, Conn.; www.ge.com) recently announced plans to spend $1.4 billion to acquire two leading suppliers of metal-based 3DP equipment, and Siemens AG (Munich, Germany; www.siemens.com) recently acquired a majority stake in U.K.-based 3DP company Materials Solutions (Worcester, U.K.; www.materialssolutions.co.uk). Further, information technology and printer giant Hewlett Packard Inc. (HP; Palo Alto, Calif.; www.hp.com) is introducing two 3-D printers aimed at manufacturing customers.
Meanwhile, companies in the chemical process industries (CPI) are also positioning themselves to support the 3DP industry by supplying analytical instruments and raw materials designed specifically for 3-D printers. Solvay S.A., BASF SE (Ludwigshafen, Germany; www.basf.com), and Eastman Chemical Co. (Kingsport, Tenn.; www.eastman.com) are among the prominent chemical manufacturers that have introduced plastics specially designed for 3DP machines. Wacker Chemie AG (Munich, Germany; www.wacker.com) has developed technology for 3D printing with silicones. Indmatec GmbH (Karlsruhe, Germany) have developed 3DP technology for polyether ether ketone (PEEK) plastics. Alcoa is among those producing metal powders designed for metal-based 3DP machines. And industrial gas companies, such as Linde Gases and Air Products Inc. (Allentown, Pa.; www.airproducts.com), are becoming involved by supplying high-purity gases and related instruments, which are critical in manufacturing metal parts with high quality and consistency. BASF recently launched its Ultrasint PA6 X028, a polyamide-6 polymer that the company says provides excellent mechanical stability and higher heat resistance compared to component parts fabricated with other polyamides. currently used in the 3DP industry.
Scott Jenkins