Primetals Technologies Ltd. (London, U.K.), together with its strategic partner Mitsubishi Corp. (Tokyo), Rio Tinto plc (London) and steel and technology group voestalpine (Linz, Austria) signed a cooperation agreement to fast-track the development of fluidized-bed and smelter technologies. The participants will implement and operate an industrial-scale prototype plant featuring a new process for potential net-zero CO2 emissions ironmaking at the voestalpine site in Linz, Austria. Startup of the hydrogen-based direct-reduction and smelting plant is scheduled for mid-2027.
Hydrogen-Based Direct Reduction and Smelting
The new ironmaking process with a projected capacity of three tons of hot metal per hour is based on the HYFOR and Smelter solutions from Primetals Technologies. HYFOR is the world’s first direct reduction technology for iron ore fines that does not require any agglomeration steps. Since 2021, Primetals Technologies has operated a pilot plant on voestalpine’s premises in Donawitz, Austria, and has run numerous successful test campaigns. The Smelter is a furnace powered by renewable energy used for melting and final reduction of direct reduced iron (DRI). It produces potential net-zero CO2 emissions hot metal for the steelmaking plant.
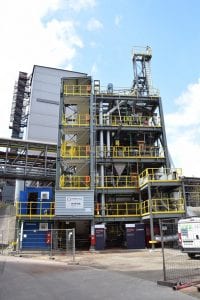
The pilot plant in Austria has been operating since 2021 (Source: Primetals Technologies)
“This project represents a significant advancement in future-proof ironmaking – for the first time, we will implement a continuous production process with hydrogen-based direct reduction,” said Alexander Fleischanderl, Chief Technology Officer and Head of Green Steel at Primetals Technologies. “The combination of HYFOR and Smelter is a highly innovative development with the potential to transform the industry, similar to the impact the LD converter (BOF) had on steel production. We are extremely proud to have the support of strong partners in voestalpine, Rio Tinto and Mitsubishi Corporation, and together, we are poised to make a big difference to the future of net-zero CO2 emissions ironmaking.”
“Mining and trading of ferrous raw materials has been one of our core businesses for many decades and we envision to develop a new supply of low emission metallics to support steel decarbonisation. HYFOR and Smelter are new promising technologies to accelerate the decarbonisation of the steel industry and Mitsubishi Corporation, as a strategic partner of Primetals Technologies, is excited to participate in the development of these groundbreaking technologies together with leading partners in the steel supply chain,” said Kenichiro Tauchi, COO, Ferrous Raw Materials Division of Mitsubishi Corporation.
“With greentec steel, voestalpine has a clear phased plan for steel production with net zero CO2 emissions. In a first step, one green-powered electric arc furnace will be put into operation at each of our sites in Linz and Donawitz starting in 2027. By 2029, we will have reduced our CO2 emissions by up to 30 percent compared to 2019. That is equivalent to almost 5 percent of Austria’s entire annual CO2 emissions, making greentec steel the largest climate protection program in Austria. Our long-term strategy is to use green hydrogen to achieve carbon-neutral steel production. Together with Primetals Technologies and Rio Tinto, we are taking an entirely new and promising approach to research into hydrogen-based pig iron production,” said Herbert Eibensteiner, CEO of voestalpine AG.
Rio Tinto, one of the world’s largest iron ore producers, will draw on its extensive expertise in iron ore quality and preparation to provide technical input to the project. Additionally, Rio Tinto will supply 70 percent of the iron ore for the new plant from across its global operations. It will also support Primetals Technologies to accelerate the commercialisation of the technology.
Rio Tinto General Manager, Steel Decarbonisation Thomas Apffel said, “We are delighted to join a consortium that encompasses the entire iron and steelmaking value chain. By contributing our ironmaking expertise and iron ores from our Pilbara, Iron Ore Company of Canada, and future Simandou operations, we aim to advance the development and adoption of fluidised bed technology. This fines-based ironmaking solution presents a compelling alternative to shaft furnace technology by eliminating the need for pelletisation, potentially offering substantial benefits to both steelmakers and miners. Rio Tinto welcomes additional participants to the consortium and looks forward to supporting the widespread implementation of this innovative technology.”
Funding for the investment and operation of this prototype plant has been provided by the Austrian federal government through its “Transformation of Industry” program managed by Kommunalkredit Public Consulting (KPC) and the “Twin Transition” initiative managed by Austria Wirtschaftsservice (aws). In addition, the European Union supports the venture through the European Union Research Fund for Coal and Steel within the Clean Steel Partnership (CSP) and the European Union Clean Hydrogen Partnership within the Hydrogen Valleys, i.e. areas where hydrogen serves more than one end sector or application in the mobility, industry, and energy sectors.